PLCs come in different sizes, so their control range can be large or small. Small ones can only control one device, or even one component or one site; large ones can control multiple devices, a production line, or even the entire factory. It can be said that industrial control cannot be separated from PLCs in any occasion.
Initially, PLC was mainly used for the logical control of switching quantities. With the advancement of technology, the application field of PLC has been continuously expanded. Nowadays, it is not only used for switching quantity control, but also for analog and digital quantity control. It can collect and store data, monitor the control system, and can also be connected to the Internet and communicate to achieve large-scale cross-regional control and management.
PLC has increasingly become an important role in the family of industrial control devices.
01For switch quantity control
PLC has a strong ability to control switch quantities. The number of input and output points it controls can be as few as a dozen or dozens, or as many as hundreds, thousands, or even tens of thousands. Since it can be networked, the number of points is almost unlimited, and no matter how many points, it can control a variety of logical problems: combined, sequential, immediate, delayed, no need to count, need to count, fixed order, random work, etc.
The hardware structure of PLC is changeable, and the software program is programmable, which makes it very flexible when used for control. If necessary, multiple sets or groups of programs can be written and called as needed. It is very suitable for the needs of multiple working conditions and multiple state changes in industrial sites.
There are many examples of using PLC for switch quantity control, such as metallurgy, machinery, light industry, chemical industry, textile, etc. Almost all industrial sectors need to use it. At present, the primary purpose of PLC, which is also unmatched by other controllers, is that it can be used for switch quantity control conveniently and reliably.
02For analog control
Analog quantities, such as current, voltage, temperature, pressure, etc., vary continuously. Industrial production, especially continuous production processes, often require the control of these physical quantities.
As an industrial control electronic device, if PLC cannot control these quantities, it is a major shortcoming. For this reason, all PLC manufacturers have carried out a lot of development in this regard. At present, not only large and medium-sized machines can perform analog quantity control, but also small machines can perform such control. For PLC to perform analog quantity control, it must be equipped with A/D and D/A units that convert analog quantities into digital quantities. It is also an I/O unit, but it is a special I/O unit.
The A/D unit converts the analog quantity of the external circuit into digital quantity and then sends it to the PLC; the D/A unit converts the digital quantity of the PLC into analog quantity and then sends it to the external circuit. As a special I/O unit, it still has the characteristics of I/O circuit anti-interference, internal and external circuit isolation, and information exchange with input and output relays (or internal relays, which is also an area of the PLC working memory and can be read and written).
The A in A/D here is mostly current, voltage, or temperature. The A in D/A is mostly voltage or current. The voltage and current ranges are mostly 0~5V, 0~10V, 4~20mA, and some can also handle positive and negative values. The D here is mostly 8-bit binary numbers for small computers, and 12-bit binary numbers for medium and large computers. A/D and D/A have single channels and multiple channels. Multiple channels occupy more input and output relays. With A/D and D/A units, the rest of the processing is digital, which is not difficult for PLCs with information processing capabilities. Medium and large PLCs have stronger processing capabilities. They can not only perform digital addition, subtraction, multiplication, and division, but also square root, interpolation, and floating-point operations. Some also have PID instructions, which can perform proportional, differential, and integral operations on the deviation quantity, and then generate corresponding outputs. It can calculate almost everything that a computer can calculate.
In this way, it is entirely possible to realize analog control using PLC.
PLC performs analog control, and there are also units that combine A/D and D/A. It can also use PID or fuzzy control algorithms to achieve control, which can achieve very high control quality. The advantage of using PLC for analog control is that while performing analog control, the switch quantity can also be controlled. This advantage is not available in other controllers, or the control is not as convenient as PLC. Of course, if it is a purely analog system, using PLC may not be as good as using a regulator in terms of performance-price ratio.
03For motion control
Actual physical quantities include not only switch quantities and analog quantities, but also motion control. For example, the displacement of machine tool parts is often expressed in digital quantities. An effective method for motion control is NC, or digital control technology. This is a computer-based control technology that was born in the United States in the 1950s. Today, it is very popular and well-developed.
At present, the CNC rate of metal cutting machine tools in advanced countries has exceeded 40% to 80%, and some are even higher. PLC is also based on computer technology and is becoming more and more perfect. PLC can receive counting pulses with a frequency of up to several k to tens of k Hz. It can receive these pulses in a variety of ways and can also receive them in multiple channels. Some PLCs also have pulse output functions, and the pulse frequency can reach tens of k. With these two functions, plus the data processing and computing capabilities of PLC, if equipped with corresponding sensors (such as rotary encoders) or pulse servo devices, it is completely possible to achieve various controls based on the principles of NC. High- and mid-range PLCs also have NC units or motion units that can achieve point control. Motion units can also achieve curve interpolation and control curve motion.
Therefore, if the PLC is equipped with this unit, it is completely possible to use NC methods to control digital quantities. The newly developed motion unit even has a programming language for NC technology, which provides convenience for better digital control with PLC.
04For data collection
With the development of PLC technology, its data storage area is getting larger and larger. For example, the data storage area (DM area) of Dewesen's PLC can reach 9999 words. Such a large data storage area can store a large amount of data. Data collection can use a counter to accumulate and record the number of pulses collected, and transfer them to the DM area regularly. Data collection can also use A/D units. When the analog quantity is converted into digital quantity, it is transferred to the DM area regularly. PLC can also be equipped with a small printer to print out the data in the DM area regularly.
PLC can also communicate with computer, and the computer can read the data in DM area and process the data. At this time, PLC becomes the data terminal of computer.
Electricity users used PLC to record their electricity usage in real time, so as to implement different charging methods for different electricity usage times, encourage users to use more electricity during low electricity consumption periods, and achieve the goal of rational and economical electricity use.
05For signal monitoring
PLC has many self-check signals and many internal devices, but most users do not fully utilize them. In fact, it can be used to monitor the PLC's own work or to monitor the controlled object. For a complex control system, especially an automatic control system, monitoring and further self-diagnosis are very necessary. It can reduce system failures, make it easier to find failures, increase the cumulative average trouble-free operation time, reduce fault repair time, and improve system reliability.
06Used for networking and communication
PLC has strong networking and communication capabilities, and new networking structures are constantly being introduced.
PLC can be connected to a personal computer for communication, and the computer can be used to participate in programming and control management of the PLC, making PLC more convenient to use.
In order to give full play to the role of computers, one computer can control and manage multiple PLCs, up to 32. One PLC can also communicate with two or more computers to exchange information to achieve multiple monitoring of the PLC control system.
PLCs can also communicate with each other, one-to-one, several PLCs, or even dozens or hundreds of PLCs.
PLC and intelligent instruments, intelligent actuators (such as inverters) can also communicate through the network, exchange data, and operate each other. They can be connected to form a remote control system, and the system range can be as large as 10 kilometers or more. A local network can be formed, and not only PLCs, but also high-end computers and various intelligent devices can be connected to the network. Bus networks and ring networks can be used. Networks can also be nested. Networks can also be bridged. Networking can organize thousands of PLCs, computers, and intelligent devices into one network. Nodes between networks can communicate and exchange information directly or indirectly.
Networking and communication are meeting the needs of the development of today's computer integrated manufacturing systems (CIMS) and intelligent factories. It can enable industrial control to move from point to line and then to aero, connecting equipment-level control, production line control, and factory management level control into a whole, thereby creating higher benefits. This infinitely bright prospect has been increasingly clearly presented to our generation.
Previous article:Three ways to connect the spindle bearing and the motor
Next article:Application of frequency converter in slitting machine control
Recommended ReadingLatest update time:2024-11-16 11:37
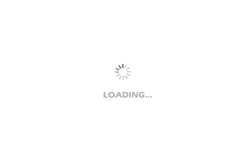
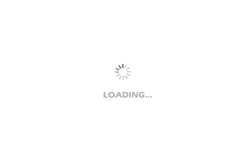
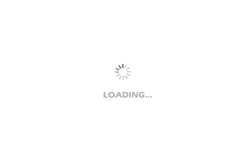
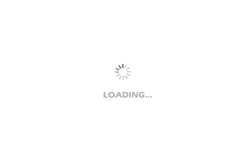
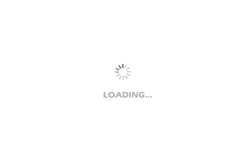
- Popular Resources
- Popular amplifiers
- Huawei's Strategic Department Director Gai Gang: The cumulative installed base of open source Euler operating system exceeds 10 million sets
- Analysis of the application of several common contact parts in high-voltage connectors of new energy vehicles
- Wiring harness durability test and contact voltage drop test method
- Sn-doped CuO nanostructure-based ethanol gas sensor for real-time drunk driving detection in vehicles
- Design considerations for automotive battery wiring harness
- Do you know all the various motors commonly used in automotive electronics?
- What are the functions of the Internet of Vehicles? What are the uses and benefits of the Internet of Vehicles?
- Power Inverter - A critical safety system for electric vehicles
- Analysis of the information security mechanism of AUTOSAR, the automotive embedded software framework
Professor at Beihang University, dedicated to promoting microcontrollers and embedded systems for over 20 years.
- Innolux's intelligent steer-by-wire solution makes cars smarter and safer
- 8051 MCU - Parity Check
- How to efficiently balance the sensitivity of tactile sensing interfaces
- What should I do if the servo motor shakes? What causes the servo motor to shake quickly?
- 【Brushless Motor】Analysis of three-phase BLDC motor and sharing of two popular development boards
- Midea Industrial Technology's subsidiaries Clou Electronics and Hekang New Energy jointly appeared at the Munich Battery Energy Storage Exhibition and Solar Energy Exhibition
- Guoxin Sichen | Application of ferroelectric memory PB85RS2MC in power battery management, with a capacity of 2M
- Analysis of common faults of frequency converter
- In a head-on competition with Qualcomm, what kind of cockpit products has Intel come up with?
- Dalian Rongke's all-vanadium liquid flow battery energy storage equipment industrialization project has entered the sprint stage before production
- Allegro MicroSystems Introduces Advanced Magnetic and Inductive Position Sensing Solutions at Electronica 2024
- Car key in the left hand, liveness detection radar in the right hand, UWB is imperative for cars!
- After a decade of rapid development, domestic CIS has entered the market
- Aegis Dagger Battery + Thor EM-i Super Hybrid, Geely New Energy has thrown out two "king bombs"
- A brief discussion on functional safety - fault, error, and failure
- In the smart car 2.0 cycle, these core industry chains are facing major opportunities!
- The United States and Japan are developing new batteries. CATL faces challenges? How should China's new energy battery industry respond?
- Murata launches high-precision 6-axis inertial sensor for automobiles
- Ford patents pre-charge alarm to help save costs and respond to emergencies
- New real-time microcontroller system from Texas Instruments enables smarter processing in automotive and industrial applications
- [Telink's new generation of low-power, high-performance, multi-protocol wireless kit B91 review] Zigbee program generation and compilation configuration
- Chatting about Saifang: Linux mainline officially supports Saifang JH7100 chip, how did you do it?
- [STM32F769Discovery development board trial] Build development environment & drive LCD screen to display dot matrix characters & touch screen driver
- For a three-pin package like this, if the components are not removed from the board, will the energy come out to be a diode or a transistor?
- Chuanglong TMS320C6748 development board——UART register introduction and program
- What is the use of C language? Is it easy to learn?
- Rebuild Polygons correct usage
- Design of a certain type of radar video acquisition preprocessing module based on FPGA
- 【GD32L233C-START Review】+Unboxing
- GD32F105RBT6 and STM32F103RBT6 are fully compatible, are the programs also fully compatible?