In a narrow sense, DCS is mainly used for process automation, PLC is mainly used for factory automation (production line), and SCADA is mainly for wide-area needs, such as oil fields and pipelines that stretch for thousands of miles. From the perspective of computers and networks, they are unified. The reason for the difference is mainly in the application requirements. DCS often requires advanced control algorithms, such as in the oil refining industry. PLC has high processing speed requirements because it is often used in interlocking and even fail-safe systems. SCADA also has some special requirements, such as vibration monitoring, flow calculation, peak and valley regulation, etc.
SCADA is the dispatching management layer, DCS is the plant management layer, and PLC is the field equipment layer.
PLC system, that is, programmable controller, is suitable for measurement and control in industrial sites. It has strong on-site measurement and control functions, stable performance, high reliability, mature technology, wide application and reasonable price.
DCS system, namely distributed industrial control system, is a large-scale control system with international advanced level in the 1990s. It is suitable for industrial sites with many measurement and control points, high measurement and control accuracy, and fast measurement and control speed. Its characteristics are decentralized control and centralized monitoring, networking communication capability, strong measurement and control function, reliable operation, easy expansion, convenient configuration, simple operation and maintenance, but the system is expensive.
SCADA system, namely distributed data acquisition and monitoring system, is a small-to-medium-scale measurement and control system. It combines the two advantages of strong on-site measurement and control functions of PLC system and networking communication capabilities of DCS system, with high performance-price ratio.
SCADA and DCS are concepts, PLC is a product, and the three are not comparable.
PLC is a product that can constitute SCADA and DCS.
DCS developed from process control, PLC developed from relay-logic control system, PLC is a device, DCS and SCADA are systems.
Key points of difference between DCS and PLC
1. DCS is a "distributed control system", while PLC (programmable logic controller) is just a control "device". The difference between the two is "system" and "device". The system can realize the functions and coordination of any device, while the PLC device only realizes the functions of this unit.
2. In terms of network, the DCS network is the central nervous system of the entire system. It is a safe, reliable, dual-redundant high-speed communication network with better system expandability and openness. Since PLCs basically work for individuals, when communicating with other PLCs or host computers, the network form they use is basically a single network structure, and the network protocol is often inconsistent with international standards. In terms of network security, PLCs do not have good protection measures. We use dual redundancy for power supply, CPU, and network.
3. Considering the overall DCS solution, the operator station has the function of the engineer station. After the operation plan program is downloaded, the stations are closely connected. Any station, any function, and any controlled device are interlocked and coordinated. However, in a system composed of only PLCs connected to each other, the connection between stations (PLC and PLC) is loose, and the coordinated control function cannot be performed.
4. The entire design of DCS leaves a large number of expandable interfaces, which makes it very convenient to connect to external systems or expand systems. After the entire system connected by PLC is completed, it is difficult to increase or reduce operator stations at will.
5. DCS security: To ensure the safety and reliability of DCS-controlled equipment, DCS uses dual redundant control units. When an important control unit fails, the relevant redundant unit will switch to the working unit in real time without interference to ensure the safety and reliability of the entire system. The system connected to PLC basically has no concept of redundancy, let alone redundant control strategy. Especially when a PLC unit fails, the entire system has to be stopped to replace, maintain and reprogram. Therefore, the DCS system is one level higher in safety and reliability.
6. System software. Updating various process control schemes is one of the most basic functions of DCS. When a scheme changes, engineers only need to compile the changed scheme on the engineer station and execute the download command. The download process is automatically completed by the system and does not affect the operation of the original control scheme. Various control software and algorithms of the system can improve the control accuracy of the control object required by the process. For the system composed of PLC, the workload is extremely large. First, it is necessary to determine which PLC to be edited and updated, and then use the corresponding compiler to compile the program. Finally, a dedicated machine (reader) is used to transfer the program to this PLC one-to-one. During the system debugging, the debugging time and debugging cost are greatly increased, and it is extremely unfavorable for future maintenance. There is a big difference in control accuracy. This determines why in large and medium-sized control projects (more than 500 points), the system connected entirely by PLCs is basically not used.
7. Module: All I/O modules of the DCS system are equipped with CPU, which can realize the quality judgment and scalar conversion of the collected and output signals, plug and unplug with power on in case of failure, and replace randomly. However, the PLC module is just a simple electrical conversion unit without intelligent chip, and all corresponding units will be paralyzed after failure.
8. Now the functions of high-end PLC and DCS are almost the same. DCS has strong functions of regular scanning of networks and distributed databases, and is good at processing calculations and analog quantities.
9. PLC is divided into large, medium, small and micro PLC. Micro PLC only costs a few hundred to 2,000 yuan and has few points. Large PLC can have thousands of points and its computing power is similar to DCS, but its multi-machine networking function is weak. Now the two technical platforms are similar, but the focus is different.
Since DCS and SCADA are concepts, they should actually be understood as a system architecture.
PLC and DCS have evolved gradually from different early product forms and application scenarios.
It can be said that PLC evolved from relays in the manufacturing industry.
DCS has evolved from process control instruments.
Each product has its own usage occasions and characteristics. With the advancement of technology, mutual penetration of industries and fierce competition.
Both PLC and DCS products are developing their own advantages while penetrating into each other.
It should be known that the logic control function of PLC is very powerful, while the loop control is not worth mentioning (you can look at the slightly older PLC models), while the DCS system is just the opposite. This is due to the different internal processing mechanisms of the two systems.
Look at it now?
Established PLC manufacturers such as Siemens and Rockwell are all involved in DCS application fields, and their systems are nothing more than PLC plus network plus software plus enhanced controller.
DCS manufacturers such as Honeywell have also integrated PLC into their systems to enhance their logic control functions.
It is important to note that a PLC is a controller;
DCS is a system architecture consisting of controller + IO acquisition + network + software.
SCADA system is another concept, a system presented by another application requirement.
As the name implies, it is a distributed data acquisition monitoring system. Its origin and application are different from the previous two. It is mainly used for data acquisition, such as power monitoring system and oil pipeline monitoring system. Its characteristics are that the control points are dispersed, and one system may cover thousands of functions (such as the oil and gas pipeline monitoring system in North America);
The communication structure is complex and cannot be compared with general control systems (from optical fiber to wireless and even satellite communications). Its basic unit is RTU.
There are two problems here:
1. Define a framework for a system;
2. Explain using the original system definition.
You have to know that products are constantly evolving and there is competition between different products. You have to constantly learn from others' strengths while leveraging your own advantages. This is integration.
The focus of SCADA is on monitoring and control, and it can realize some logical functions and is basically used for upper level;
PLC simply implements logical functions and controls, does not provide a human-machine interface, and requires the use of buttons, indicator lights, HMI, and SCADA systems to implement operations;
DCS has both functions, but is basically used in larger systems and some systems with high control requirements, and is more expensive;
The three systems penetrate each other. In some manufacturing enterprises, all three systems are included: SCADA as the upper-level monitoring of production management, DCS for complex control, and PLC for single machine and simple control.
However, with the development of technology, some manufacturers' PLCs can also achieve very complex and precise control, and gradually occupy the DCS market...
Simply put, PLC+SCADA=DCS. As far as I understand it, they can cross-control each other in terms of control functions, and also develop the advantages of the other for their own use based on the control of this system.
Previous article:What is the difference between a servo motor and a linear motor?
Next article:8 common types of PLC errors that PLC repairers need to know
Recommended ReadingLatest update time:2024-11-16 11:31
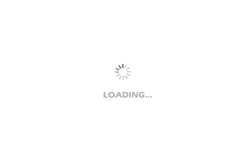
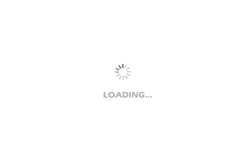
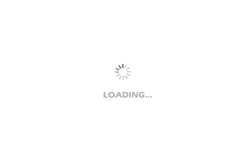
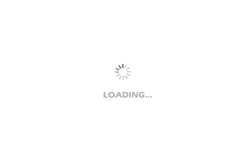
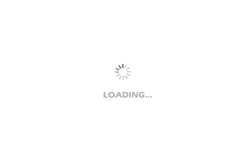
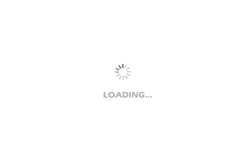
- Popular Resources
- Popular amplifiers
- Huawei's Strategic Department Director Gai Gang: The cumulative installed base of open source Euler operating system exceeds 10 million sets
- Analysis of the application of several common contact parts in high-voltage connectors of new energy vehicles
- Wiring harness durability test and contact voltage drop test method
- Sn-doped CuO nanostructure-based ethanol gas sensor for real-time drunk driving detection in vehicles
- Design considerations for automotive battery wiring harness
- Do you know all the various motors commonly used in automotive electronics?
- What are the functions of the Internet of Vehicles? What are the uses and benefits of the Internet of Vehicles?
- Power Inverter - A critical safety system for electric vehicles
- Analysis of the information security mechanism of AUTOSAR, the automotive embedded software framework
Professor at Beihang University, dedicated to promoting microcontrollers and embedded systems for over 20 years.
- Innolux's intelligent steer-by-wire solution makes cars smarter and safer
- 8051 MCU - Parity Check
- How to efficiently balance the sensitivity of tactile sensing interfaces
- What should I do if the servo motor shakes? What causes the servo motor to shake quickly?
- 【Brushless Motor】Analysis of three-phase BLDC motor and sharing of two popular development boards
- Midea Industrial Technology's subsidiaries Clou Electronics and Hekang New Energy jointly appeared at the Munich Battery Energy Storage Exhibition and Solar Energy Exhibition
- Guoxin Sichen | Application of ferroelectric memory PB85RS2MC in power battery management, with a capacity of 2M
- Analysis of common faults of frequency converter
- In a head-on competition with Qualcomm, what kind of cockpit products has Intel come up with?
- Dalian Rongke's all-vanadium liquid flow battery energy storage equipment industrialization project has entered the sprint stage before production
- Allegro MicroSystems Introduces Advanced Magnetic and Inductive Position Sensing Solutions at Electronica 2024
- Car key in the left hand, liveness detection radar in the right hand, UWB is imperative for cars!
- After a decade of rapid development, domestic CIS has entered the market
- Aegis Dagger Battery + Thor EM-i Super Hybrid, Geely New Energy has thrown out two "king bombs"
- A brief discussion on functional safety - fault, error, and failure
- In the smart car 2.0 cycle, these core industry chains are facing major opportunities!
- The United States and Japan are developing new batteries. CATL faces challenges? How should China's new energy battery industry respond?
- Murata launches high-precision 6-axis inertial sensor for automobiles
- Ford patents pre-charge alarm to help save costs and respond to emergencies
- New real-time microcontroller system from Texas Instruments enables smarter processing in automotive and industrial applications
- CB5654 Development Board Review 4
- One-week evaluation report delivered~~
- Testing methods and diagnostic analysis for DSP-containing circuit boards
- Get the relevant information required by LSM6DSOX+STEVAL-MKI109V3 contestants (including official information and moderator reviews)
- ZigBee terminal (low power device)
- [RVB2601 Creative Application Development] GPIO Simulation SPI Serial Port
- Embedded Qt-Table Usage Test
- I found a very useful Renesas RL78 offline programmer.
- Porting appweb
- Disassembly of the knockoff TWS headset charging box