This section introduces several commonly used PLC control circuits and compares them with relay contactor control circuits, so that readers can fully understand the control principles and application technologies of PLC based on their mastery of relay control systems.
Start and stop control of electric motor
Figure 5-50 Composition of PLC control system
The PLC control system consists of two parts: hardware and software, as shown in Figure 5-50. Hardware part: Connect the input element to the PLC through the input point, and connect the output element to the PLC through the output point, forming the hardware part of the PLC control system. Software part: Use PLC instructions to transform the control idea into a program that the PLC can accept.
Start control: usually implemented by using a button, connecting its moving contact to the input point of the PLC, and the corresponding bit in the PLC input image register forms a mapping relationship with the contact, using digital quantities "1" and "0" to reflect the on and off states of the contact, as shown in Figure 5-51. The motor is first connected to the contactor, and the main contact of the contactor is connected to the output point of the PLC. There is an output image register in the PLC that forms a one-to-one mapping relationship with each output point.
Figure 5-51 Mapping of buttons and input image registers
For the usual start control, it is only necessary to connect the start button to the input point of the PLC and the motor to the output point of the PLC. The ladder diagram of Figure 5-53 has a single circuit function and cannot be self-locking. It can only realize a simple inching function. It has the same function as the relay control Figure 5-52 (b). The ladder diagram of Figure 5-54 uses the auxiliary contact (soft contact) of the output coil in parallel with the button mapping contact (soft contact), which is called self-locking. The simple start circuit is added with a self-locking function, so that the motor can continue to run after the hand leaves the button. It has the same function as the relay control Figure 5-52 (c). The ladder diagram of Figure 5-55 uses the break contact of the button to connect to the input point of the PLC. In the ladder diagram, it plays the role of cutting off the control signal of the main channel. Therefore, the break contact of the button is connected in series to the main channel of the controlled coil. A stop button is added to the figure to enable it to have the function of starting and holding the stop. It has the same function as the relay control Figure 5-52 (d). By comparing the two control devices, readers can understand PLC hardware and software and how to use ladder diagrams to achieve control functions.
Figure 5-52 Start-stop circuit of motor relay control
(a) Main circuit; (b) Inching control; (c) Inching control with self-locking; (d) Typical start-stop control
The circuit in Figure 5-55 includes start, hold and stop control, which is the most typical start-stop-protection control circuit. When reading the diagram, analyze the three ladder diagrams accordingly. In the actual circuit, some protection measures need to be added, such as interlock protection, overload protection, etc., and the ladder diagram is relatively complicated. The motor start-stop control implemented by the ladder diagram has the same function as the relay contactor control system, and the ladder diagram is more concise and intuitive.
Figure 5-53 The simplest motor starting procedure
Figure 5-54 Starting procedure with self-locking contacts
Motor forward and reverse control
Figure 5-55 Motor starting procedure with stop button
The previous section has introduced the use of relay control systems to achieve forward and reverse control of motors. To achieve forward and reverse rotation of a three-phase motor, it is only necessary to swap any two of the three phases connected to the motor, as shown in Figure 5-56. Based on the start-stop circuit, the ladder diagram adds interlock protection to prevent the motor coil from being burned by simultaneous forward and reverse rotation of the motor, thus forming a simple forward and reverse control program, as shown in Figure 5-57. In actual circuits, control signals from buttons, travel switches, and sensors are usually used as input signals for forward and reverse switching.
Figure 5-56 Forward/reverse control circuit
Figure 5-57 Input/output configuration and external wiring diagram
Realize the forward and reverse start control of the motor. Press SB1 to start the motor in the forward direction (keep running); press SB2 to start the motor in the reverse direction; press SB3 to stop the motor.
(1) To achieve forward and reverse rotation, two contactors KM1 and KM2 are required. The corresponding PLC input points can be Q0.1 and Q0.2.
(2) Because in the forward and reverse circuits, if they are turned on at the same time, a short circuit will occur, so only one can be turned on at a time. One method is to use a button with an interlock, and the other method is to connect the auxiliary contact of the contactor to the other circuit. In this example, double interlocking is used, and self-locking contacts should be used to maintain the operating state in a certain direction.
(3) It is impossible to let the motor run endlessly, so the break contacts of the stop button are connected in series in the corresponding circuit.
Assign I/O addresses according to the number of input and output points, see Table 5-8.
Table 5-8 I/O address allocation table
Connect the wires according to the corresponding I/O points on the PLC, and connect the power cord according to the S7-200 manual. The schematic diagram is shown in Figure 5-57. Since the output of the PLC is often strong electricity, you must comply with the safety operating procedures during operation, and only power on and debug after checking that there are no problems.
Enter the Step7 MicroWin32 development environment to design a ladder diagram program, as shown in Figure 5-58. The analysis of its action principle is the same as that of relay control.
Figure 5-58 Ladder diagram for motor forward and reverse control
Y-△ Decompression Start
Star-delta decompression starting can greatly reduce starting current, reduce current shock and extend the service life of the motor. It is widely used in light-load or no-load starting circuits. Figure 5-59 is a Y-△ decompression starting control circuit diagram. The Y-△ starting control circuit diagram has been discussed before. Although the functions are similar, the circuits implemented are different. Readers can compare and analyze.
Figure 5-59 Star-delta decompression starting control system. Control process: Press SB2 to start the motor in star mode, delay 3s to switch to delta operation state, press SB1 to stop the system.
Figure 5-59 Y-△ pressure reducing start control circuit
The control process of the relay control system is as follows.
(1) When the motor is connected in star, one end of the three-phase winding coil is connected together. When it is connected in triangle, the head and tail of the three-phase winding coil are connected separately. To achieve the switching between these two states, three contactors KM1, KM2, and KM3 are required. The connection method is shown in Figure 5-59.
(2) When KM1 and KM3 are energized and KM2 is disconnected, the motor is connected in star.
(3) When KM1 and KM2 are energized and KM3 is disconnected, the motor is connected in a triangle.
To prevent a short circuit due to KM3 not being disconnected in time when switching to a delta connection, an interlocking protection is established between KM2 and KM3.
SB1 is a stop button, which is connected in series where it can cut off the entire control circuit.
According to the working process of the above circuit, according to the required components, set the I/O address, and its assigned I/O address is shown in Table 5-9. Convert its relay control system into a PLC programming control system. Readers can analyze it according to its design ideas and design the PLC ladder diagram based on the analysis of the relay control principle.
Table 5-9 Y-△ decompression start I/O address
According to the traditional relay control circuit diagram, it is converted into a PLC ladder diagram, as shown in Figure 5-60. The reader must first clarify the Y-△ decompression start I/O address and the role of the soft relay used, and the PLC writing rules. When reading the diagram, the method of following the clues is adopted. Along the input and output elements on each branch of the relay control circuit, the corresponding instructions are replaced in the PLC control program ladder diagram, and then the position is analyzed according to the PLC writing rules. In the Y-△ decompression start ladder diagram, a timer is used to replace the time relay in the relay control.
Figure 5-60 Y-△ pressure reduction start ladder diagram
In order to help readers better understand the execution process of the ladder diagram program, the execution process of the ladder diagram program in Figure 5-60 is analyzed as follows:
Press SB2 to close contact I0.2 → coil Q0.1 is energized and self-locked; timer T37 starts → coil Q0.1's make contact closes, coil Q0.3 is energized → star operation; at the same time, Q0.3's break contact opens, achieving interlocking.
While pressing SB2 → timer T37 sets for 3s → when the time is up, the break contact of T37 opens, and coil Q0.3 loses power; the make contact of T37 connects, coil Q0.2 is energized and self-locks → triangle operation. The break contact of Q0.2 opens, and interlocking is achieved. The break contact of Q0.2 opens, and the timer is reset.
Press the SB1 stop button → the entire system stops running.
The operator can make hardware connections according to the corresponding I/O points on the PLC and connect the power cord according to the S7-200 manual. Since the output of the PLC is often strong electricity, the safe operating procedures must be followed during operation, and power-on debugging can only be performed after passing the inspection.
Previous article:Basic wiring method of inverter
Next article:Basic structure of interlocking start-stop control circuit for two three-phase AC motors
Recommended ReadingLatest update time:2024-11-16 13:54
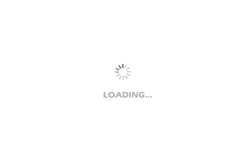
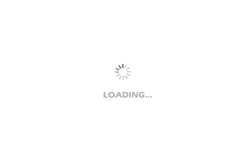
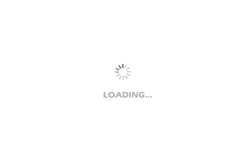
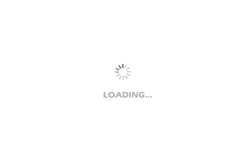
- Popular Resources
- Popular amplifiers
- Huawei's Strategic Department Director Gai Gang: The cumulative installed base of open source Euler operating system exceeds 10 million sets
- Analysis of the application of several common contact parts in high-voltage connectors of new energy vehicles
- Wiring harness durability test and contact voltage drop test method
- Sn-doped CuO nanostructure-based ethanol gas sensor for real-time drunk driving detection in vehicles
- Design considerations for automotive battery wiring harness
- Do you know all the various motors commonly used in automotive electronics?
- What are the functions of the Internet of Vehicles? What are the uses and benefits of the Internet of Vehicles?
- Power Inverter - A critical safety system for electric vehicles
- Analysis of the information security mechanism of AUTOSAR, the automotive embedded software framework
Professor at Beihang University, dedicated to promoting microcontrollers and embedded systems for over 20 years.
- Innolux's intelligent steer-by-wire solution makes cars smarter and safer
- 8051 MCU - Parity Check
- How to efficiently balance the sensitivity of tactile sensing interfaces
- What should I do if the servo motor shakes? What causes the servo motor to shake quickly?
- 【Brushless Motor】Analysis of three-phase BLDC motor and sharing of two popular development boards
- Midea Industrial Technology's subsidiaries Clou Electronics and Hekang New Energy jointly appeared at the Munich Battery Energy Storage Exhibition and Solar Energy Exhibition
- Guoxin Sichen | Application of ferroelectric memory PB85RS2MC in power battery management, with a capacity of 2M
- Analysis of common faults of frequency converter
- In a head-on competition with Qualcomm, what kind of cockpit products has Intel come up with?
- Dalian Rongke's all-vanadium liquid flow battery energy storage equipment industrialization project has entered the sprint stage before production
- Allegro MicroSystems Introduces Advanced Magnetic and Inductive Position Sensing Solutions at Electronica 2024
- Car key in the left hand, liveness detection radar in the right hand, UWB is imperative for cars!
- After a decade of rapid development, domestic CIS has entered the market
- Aegis Dagger Battery + Thor EM-i Super Hybrid, Geely New Energy has thrown out two "king bombs"
- A brief discussion on functional safety - fault, error, and failure
- In the smart car 2.0 cycle, these core industry chains are facing major opportunities!
- The United States and Japan are developing new batteries. CATL faces challenges? How should China's new energy battery industry respond?
- Murata launches high-precision 6-axis inertial sensor for automobiles
- Ford patents pre-charge alarm to help save costs and respond to emergencies
- New real-time microcontroller system from Texas Instruments enables smarter processing in automotive and industrial applications
- (Bonus 5) GD32L233 Review - CRC (with the clearest article explaining CRC in history)
- Recruiting MCU development engineers (workplace: Beijing, Wuhan)
- ST FOC electrical angle problem
- Altium Designer software is abnormal, please solve it! ! !
- Car-to-everything design
- Unboxing
- Programming Techniques in FPGA Design
- 5G frequency band division among the three major operators
- TMS320F28335 and its minimum system design
- 2022 Digi-Key Innovation Design Competition + ESP32-S2-KALUGA1 Unboxing