0 Introduction
With the increasing requirements of automation control and reliability of induction heating power supply, induction heating power supply is developing towards intelligent and digital control. DSP has high-speed digital processing capability and rich peripheral functions, which enables some advanced control strategies to be applied in practice. Research on digital control induction heating power supply based on DSP can make the product have better stability and real-time control, and has the characteristics of simplicity and flexibility. This paper takes TMS320F2812 as the core and designs a digital control system of super-frequency series resonant induction heating power supply, including digital phase-locked loop (DPLL), phase-shifted PWM generation and system closed-loop control.
1 System Structure
The main circuit of the series resonant induction heating power supply is shown in Figure 1. It adopts an uncontrolled rectifier plus a controllable inverter power supply structure, and the load is an induction coil (equivalent to an inductor) connected in series with a compensation capacitor. The inverter part adopts a phase-shifted PWM control with a phase-locked loop. The system control block diagram based on TMS320F2812 is shown in Figure 2. The DC side voltage detection circuit and current detection circuit are used for closed-loop control of the system; the output current detection circuit is to obtain the load current frequency pulse signal, which is used as a synchronization signal for frequency tracking.
2 Phase-Shift PWM Power Regulation Principle
In Figure 1, the arms of VT1 and VT2 are used as reference arms, and the arms of VT3 and VT4 are used as phase shift arms, and the control pulses are shown in Figure 3. As can be seen from the figure, the control signals of VT1 and VT2, VT3 and VT4 still maintain a complementary phase relationship, but the control signals of VT3 and VT4 lag VT1 and VT2 by an angle β, respectively, which is continuously adjustable within the range of 0 to π. Changing the phase angle β of the phase shift arm can change the output voltage waveform, thereby changing the voltage fundamental effective value and achieving the purpose of voltage regulation in the bridge.
Assume that the input DC voltage is Ud, and the VT4 control signal lags the VT1 control signal by an angle of β. Then the circuit output power can be expressed by the fundamental wave active power:
3 Implementation of DSP-based control system
1) Generation of digital phase-locked loop and phase-shifted PWM signal
The EV unit using TMS320F2812, combined with the basic formula of digital phase-locked loop, can effectively realize the frequency tracking of induction heating power supply. The basic formula of digital phase-locked loop is as follows:
Where, T0(n) is the synchronization signal period, T1(n) is the result after second-order filtering, and T(n) is the result after frequency and phase correction. A is the frequency correction coefficient, and B is the phase correction coefficient.
The basic principle of implementing a digital phase-locked loop (DPLL) based on TMS320F2812 is shown in Figure 4. The algorithm process is as follows:
(1) Set the capture unit to rising edge capture. When the rising edge of the synchronization signal pulse arrives, counter 2 starts counting from zero. When the next pulse rising edge arrives, the value of counter 2 is captured to obtain the period value T0(n) of the synchronization signal.
(2) Open the underflow interrupt of timer 1. When counter l reaches zero, it enters the underflow interrupt. Immediately read and record the value of counter 2 at this moment, as shown in point M in Figure 4. This value is the phase difference θ(n). Store it in the corresponding register and wait for the program to call.
(3) Call related variables and calculate the new period value T(n) based on the basic formula of the phase-locked loop.
(4) Determine whether T(n) is within the frequency limit range. After the amplitude limiting process, use T(n) as the period value of the next cycle of counter 1. In this way, the purpose of phase locking can be achieved by adjusting it in each cycle.
Considering the occurrence of phase-shifted PWM signal, the counter l needs to be set to continuous up and down counting mode, so the value actually loaded into the period register needs to be divided by 2.
The principle of the generation of phase-shifted PWM signal is shown in Figure 5. Set the timer/counter 1 (GP1) to the continuous increase and decrease counting mode, set A and A' to correspond to the comparison unit 1 (CMP1), and B and B' to correspond to the comparison unit 2 (CMP2). Comparison unit 1 and comparison unit 2 output two complementary pulse signals respectively. By timely changing the value of the timer comparison register during the underflow interrupt and cycle match interrupt of GPl, the required phase-shifted PWM signal can be generated.
The algorithm for comparing register values is as follows:
Where TPR(n) is the period value of timer 1, date1 and date2 are two variable values. By changing the difference between date1 and date2, a PWM output with controllable phase shift angle can be obtained.
Assuming the lag angle of the phase shift arm is β, then
From formula (3), we can see that when datel=0, date2=TPR(n), the phase shift angle β is the largest, and the phase shift range is 0~π. However, in the DSP program design, datel (point A) cannot be zero. Therefore, under this algorithm, the range of the phase shift angle is related to the minimum value of datel.
Combining the generation principle of digital phase-locked loop and phase-shift PWM, an algorithm combining the two can be designed. The algorithm flow chart in DSP is shown in Figure 6.
2) Closed-loop control
This paper adopts a closed-loop control structure as shown in Figure 7. The output voltage and current changes are detected, and the feedback signal is input to the ADC sampling port of the DSP for analog-to-digital conversion to obtain the feedback values of the voltage and current. The two are then multiplied by a multiplier and compared with the given value. The output of the power regulator controls the phase shift angle of the inverter to keep the output power constant.
Because the inertia of the induction heating power system load is relatively large, that is, the parameters change slowly, therefore, the PID differential link can be ignored and PI regulation can be used to meet the control requirements of the system.
3) Phase compensation and startup issues
Due to the influence of hardware lag or program execution efficiency in the actual operation of the system, when phase compensation is not performed, the control signal must lag behind the feedback signal by a certain angle. In practical applications, an external phase compensation circuit is often used to achieve phase synchronization between output and feedback, which can also be compensated in the program. This paper adds a phase compensation link to the algorithm program of the phase-locked loop. In the calculation of the phase difference, the error angle θerr is introduced, and
Where θ′(n) is the recalculated phase difference, which can be used as the phase difference in the DPLL algorithm to achieve phase compensation of the output pulse. According to the experimental test and calculation, the accurate θerr can be obtained, which can eventually keep the input pulse and the output signal with zero phase difference, which is very necessary for the actual operation of the system.
When the induction heating power supply is started, since the load has no current, the frequency cannot be tracked, so the power supply must first rely on the external excitation signal to start normally, and then convert to the self-excitation state when the feedback current reaches a certain amplitude. When the system starts, this paper first generates a 50kHz to 20kHz sweep PWM signal through the DSP, and then the ADC sampling unit continuously detects the load current effective value feedback and sets the threshold. When the effective value of the feedback current is higher than the threshold, the sweep program jumps out and enters the digital phase-locked loop program, so that the system works in the self-excitation state. The algorithm flow chart is shown in Figure 8.
4 Experimental results and conclusions
The control system program was written based on TMS320F2812, connected to the induction heating power supply prototype, and experiments and debugging were carried out to obtain the following experimental results.
Figure 9 shows the working waveforms of the output voltage and output current of the induction heating power supply under the frequency tracking and phase-shift closed-loop control. At this time, the load inductance L≈105μH, and the compensation capacitor C=0.4μF. It can be seen from the figure that the output voltage and current always maintain a fixed phase relationship, indicating that the digital phase-locked loop works normally.
During the experiment, the given constant is changed, and the size of the load series resistance is changed. As shown in Figure 9 (a), (b), and (c), the load series resistance is Chi = 6Ω, R = 5Ω, and R = 4Ω respectively. It can be seen that under the action of closed-loop control, when the resistance value of the load series connection becomes larger, the duty cycle of the output voltage will decrease accordingly. Figure 9 (d), (e), and (f) are the output voltage and output current waveforms when the input voltage on the DC side of the inverter is Ud = 27V, Ud = 30V, and Ud = 34V respectively. It can be seen from the figure that under different input voltage conditions, the duty cycle of the output voltage will change accordingly.
The experiment shows that the algorithm designed in this paper is stable and effective, and the experimental results are consistent with the theoretical analysis. The phase-shifted closed-loop control system of the induction heating power supply based on TMS320F2812 can complete the frequency tracking and continuous adjustment of the output power of the series resonant induction heating power supply, and has good closed-loop control characteristics.
Previous article:Typical design of TMS320F206 peripheral circuit
Next article:Design of an AGWN Signal Generator Based on FPGA
Recommended ReadingLatest update time:2024-11-16 19:31
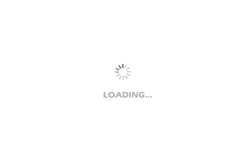
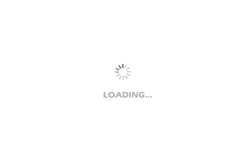
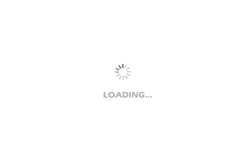
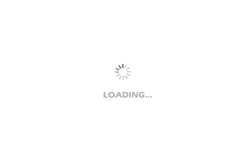
- Popular Resources
- Popular amplifiers
- Huawei's Strategic Department Director Gai Gang: The cumulative installed base of open source Euler operating system exceeds 10 million sets
- Analysis of the application of several common contact parts in high-voltage connectors of new energy vehicles
- Wiring harness durability test and contact voltage drop test method
- Sn-doped CuO nanostructure-based ethanol gas sensor for real-time drunk driving detection in vehicles
- Design considerations for automotive battery wiring harness
- Do you know all the various motors commonly used in automotive electronics?
- What are the functions of the Internet of Vehicles? What are the uses and benefits of the Internet of Vehicles?
- Power Inverter - A critical safety system for electric vehicles
- Analysis of the information security mechanism of AUTOSAR, the automotive embedded software framework
Professor at Beihang University, dedicated to promoting microcontrollers and embedded systems for over 20 years.
- Innolux's intelligent steer-by-wire solution makes cars smarter and safer
- 8051 MCU - Parity Check
- How to efficiently balance the sensitivity of tactile sensing interfaces
- What should I do if the servo motor shakes? What causes the servo motor to shake quickly?
- 【Brushless Motor】Analysis of three-phase BLDC motor and sharing of two popular development boards
- Midea Industrial Technology's subsidiaries Clou Electronics and Hekang New Energy jointly appeared at the Munich Battery Energy Storage Exhibition and Solar Energy Exhibition
- Guoxin Sichen | Application of ferroelectric memory PB85RS2MC in power battery management, with a capacity of 2M
- Analysis of common faults of frequency converter
- In a head-on competition with Qualcomm, what kind of cockpit products has Intel come up with?
- Dalian Rongke's all-vanadium liquid flow battery energy storage equipment industrialization project has entered the sprint stage before production
- Allegro MicroSystems Introduces Advanced Magnetic and Inductive Position Sensing Solutions at Electronica 2024
- Car key in the left hand, liveness detection radar in the right hand, UWB is imperative for cars!
- After a decade of rapid development, domestic CIS has entered the market
- Aegis Dagger Battery + Thor EM-i Super Hybrid, Geely New Energy has thrown out two "king bombs"
- A brief discussion on functional safety - fault, error, and failure
- In the smart car 2.0 cycle, these core industry chains are facing major opportunities!
- The United States and Japan are developing new batteries. CATL faces challenges? How should China's new energy battery industry respond?
- Murata launches high-precision 6-axis inertial sensor for automobiles
- Ford patents pre-charge alarm to help save costs and respond to emergencies
- New real-time microcontroller system from Texas Instruments enables smarter processing in automotive and industrial applications
- Please recommend, is there any domestic dual-channel H-bridge that can drive motors with an operating voltage of 12V or above?
- How to install and use pressure transmitter
- The flashing prompt cannot recognize the device. What's going on?
- Model-Based Design and Its Embedded Implementation
- Q&A on Connectivity: Why Wi-Fi 6 Could Be Your Competitive Advantage
- Why do we need to learn transistor circuits when we already have integrated circuits?
- 2. Hardware Introduction and Development Environment Installation
- 【New Year's Festival Competition】+ Watching Lanterns on the Lantern Festival (multiple photos)
- 5G small base stations are under the spotlight: now is the eve of the outbreak
- 【CH579M-R1】+ PWM breathing light