1 Overview
Among the many bus standards, various buses are called standard, but in industries or fields where market competition cannot be divided into different areas, various buses penetrate each other. For example, DeviceNet is widely used in automobiles, material handling and manufacturing industries, but in Europe, Profibus standards are also strong competitors in these fields and occupy an absolute share. In addition, Profibus standards are also widely used in some specific industries, such as the application of Profibus DP in automobile factories. However, there is an interesting phenomenon that the German CANopen bus itself is also used in the automotive industry. However, no matter how you look at it, the entire market can basically be divided into two categories: process industry and manufacturing industry.
As industrial enterprises continue to invest in faster and more efficient production and operation, the number of intelligent devices connected to these different buses is increasing rapidly. The application of the bus can indeed bring vitality and powerful business processing capabilities to end-user enterprises, but it also brings a problem to suppliers of intelligent devices: they must design different bus products according to the numerous buses to meet the needs of various buses; but the data interfaces of the products are all hardware-based, and it is not advisable to design a product with multiple hardware in terms of manufacturing costs. In addition, the control wiring in the fieldbus is a very time-consuming task and is not easy to succeed in the installation project. This complexity of work is obviously contrary to the trend of easier equipment operation today. System integrators expect a plug & produce solution without having to painstakingly read the thick product parameter manuals provided by suppliers. This is actually a demand for flexible and simplified industrial communications. Therefore, ABB designed and produced a product (FieldBusPlug-FBP) that can be easily and quickly connected to any bus system to simplify the entire fieldbus, as shown in Figure 1. In fact, FBP is a bus adapter.
Figure 1 Fieldbus Adapter (FBP)
2. Functions of FBP system
The FBP system can connect switchgear and other similar components, such as motor protection and control equipment to sensors, through a bus adapter of any protocol, with the usual automation system (PLCs) in a simple and effective way. These switchgear are independent of the bus used. Through the selected bus cable (FBP cable), a connection with various bus adapters can be established.
ABB FBP bus adapter can support five types of bus adapters: Profibus-DP, CANopen, Modbus-RTU, DeviceNet and AS-i. The appearance and connection methods of these five bus adapters are the same, which provides convenience for unified use and selection. As shown in Figure 2, the DeviceNet bus adapter is selected for communication.
Figure 2 Connection diagram of multi-substation equipment and PLC system
3. Features of FBP system
Today's automation applications require not only intelligent products, but also the ability to communicate with each other to achieve networking functions, and the bus is undoubtedly the communication method chosen by many current automation equipment. When you walk into any manufacturing plant, process enterprise or energy enterprise, you will easily find that hundreds of actuators and sensors communicate with their controllers through a bus.
3.1 Simple and flexible bus system
One device for all bus types, each device and each functional module in the product line contains a neutral bus adapter interface. With the selected bus adapter and cable connector and pre-connected cables, it is very easy to establish reliable and flexible communication and connection, as shown in Figure 3.
The communication bus can be changed according to the needs of users without changing the communication interface. This is a flexible choice based on ABB's unique FBP bus technology. On the same FBP bus adapter (neutral bus interface), you only need to change the FBP bus adapter of different types of buses (bus types) to change different bus protocols. For example, Profibus or DeviceNet. This change does not require any special settings by the user. You only need to replace it with the corresponding FBP bus adapter and make some simple configurations in the software. The control system automatically recognizes the changes in the communication protocol of the connected electrical equipment. This brings convenience to users in changing between standard field buses. ABB's AC500 series PLC can also run as a slave station of the field bus through the FBP adapter.
Figure 3
3.2 Simplify the entire fieldbus
The FBP bus adapter can simply and quickly connect to any bus system to simplify the entire fieldbus. ABB is now able to provide an interface plug-in with bus independence, which means that suppliers no longer need to redesign products according to different target bus markets in the future. Each automation device can be connected to the bus through the corresponding bus plug-in, and one bus protocol corresponds to one bus plug-in. For example, to connect a motor starter to the DeviceNet bus, you only need to connect the DeviceNet bus plug-in to a general standard motor starter.
This fieldbus plug-in meets all electronic data transmission needs. It converts the data on the connected bus into a neutral data format that can be recognized by standard automation equipment or vice versa.
ABB's motor controllers and motor starters are equipped with a bus-independent FBP interface. All installation engineers need to do is to directly connect the prepared FBP connection cable corresponding to the corresponding bus interface to the fieldbus.
FBP fieldbus plugs can connect some special switches and automation equipment to process controllers. The design of the plug-in is also very simple. One end is a universal interface that has nothing to do with the type of bus, and the other end is an interface that conforms to a specific bus standard. The compact interface has an intelligent electronic conversion device that can convert neutral device data into a language that can be understood by buses such as AS-i or DeviceNet.
4. FBP bus adapter is used in the hardware configuration of the intelligent motor controller (UMC)
In order to better illustrate the flexible application of ABB FBP fieldbus adapter in intelligent motor controller, we use ABB's AC500 series programmable controller and Profibus bus adapter for illustration.
Application of ABB FBP bus adapter in intelligent motor controller:
Figure 4 Application of FBP bus adapter in smart motor
In Figure 4, the automation control management unit (PLCs) uses ABB's AC500 series PM581 as the programmable controller CPU. The CPU has: an LCD display, a set of operation buttons, an SD card expansion port and two integrated serial communication ports. The CPU baseboard integrates an Ethernet interface and retains the CS31 communication interface. It has good compatibility with the AC31 series PLC.
FBP fieldbus adapter: PDP22-FBP.xxx; related cables and accessories: PDA11-FBP.xxx and PDR11-FBP.150 terminal resistor. The PLC communication master station uses the FBP bus adapter to simply and quickly connect to the intelligent motor controller UMC22 with a neutral interface, soft starter and other field devices, thereby achieving seamless connection from the control layer to the field layer. FBP bus adapters are also widely used in occasions where equipment is relatively dispersed. Some sites are far apart, especially some field sites, which are more than 100 meters apart. Therefore, the transmission rate of all networks is set to be consistent to ensure reliable communication. In addition to distributed I/O, circuit breakers, sensors and other sites located at the production site, the bus network system of intelligent motor controllers and inverters is distributed in the motor control center (IMCC) room, which realizes centralized control and unified management of motors.
Experience of using FBP bus adapter in intelligent motor controller:
(1) Fieldbus can save a lot of money
From the installation stage, power supply and communication of famous sites on the entire network can be achieved through only one communication cable. Compared with the point-to-point control method, it saves a lot of cables, bridges, etc., which not only shortens the installation time but also reduces the installation cost.
From the control point of view, the use of network communication and "soft" I/O mode saves I/O modules, especially analog modules. For example, for intelligent motor controller UMC22 or inverter workstations, start/stop, start mode, acceleration/deceleration and other commands; voltage, current, temperature, running time and other parameters can all be realized through bus network communication.
(2) The equipment failure rate is greatly reduced, and diagnosis is convenient and elimination is quick.
The FBP system uses only one communication cable to control the entire equipment network, which greatly reduces the equipment failure rate. The use of data communication to control each station not only greatly reduces the number of cables in the traditional point-to-point method, but also greatly reduces the number of failure links and further improves the system stability.
The FBP system makes the centralized control of motors very effective, greatly facilitating the diagnosis of equipment failures. For example, when a UMC22 intelligent motor controller fails, not only can the alarm information be seen in the central control room, but also from the UMC22 operation panel, which is convenient and quick.
Engineering practice shows that 80% of bus failures occur in the bus cable itself, and the FBP system provides pre-installed cables with metal contacts to minimize the possibility of failures caused by cable problems.
Previous article:Siemens SIMATIC automation products realize the solution of automatic coal blending system
Next article:Application of Profibus-DP, Siemens touch screen and PLC devices in bucket wheel stacker and reclaimer
Recommended ReadingLatest update time:2024-11-16 14:56
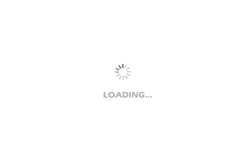
- Popular Resources
- Popular amplifiers
- Huawei's Strategic Department Director Gai Gang: The cumulative installed base of open source Euler operating system exceeds 10 million sets
- Analysis of the application of several common contact parts in high-voltage connectors of new energy vehicles
- Wiring harness durability test and contact voltage drop test method
- Sn-doped CuO nanostructure-based ethanol gas sensor for real-time drunk driving detection in vehicles
- Design considerations for automotive battery wiring harness
- Do you know all the various motors commonly used in automotive electronics?
- What are the functions of the Internet of Vehicles? What are the uses and benefits of the Internet of Vehicles?
- Power Inverter - A critical safety system for electric vehicles
- Analysis of the information security mechanism of AUTOSAR, the automotive embedded software framework
Professor at Beihang University, dedicated to promoting microcontrollers and embedded systems for over 20 years.
- Innolux's intelligent steer-by-wire solution makes cars smarter and safer
- 8051 MCU - Parity Check
- How to efficiently balance the sensitivity of tactile sensing interfaces
- What should I do if the servo motor shakes? What causes the servo motor to shake quickly?
- 【Brushless Motor】Analysis of three-phase BLDC motor and sharing of two popular development boards
- Midea Industrial Technology's subsidiaries Clou Electronics and Hekang New Energy jointly appeared at the Munich Battery Energy Storage Exhibition and Solar Energy Exhibition
- Guoxin Sichen | Application of ferroelectric memory PB85RS2MC in power battery management, with a capacity of 2M
- Analysis of common faults of frequency converter
- In a head-on competition with Qualcomm, what kind of cockpit products has Intel come up with?
- Dalian Rongke's all-vanadium liquid flow battery energy storage equipment industrialization project has entered the sprint stage before production
- Allegro MicroSystems Introduces Advanced Magnetic and Inductive Position Sensing Solutions at Electronica 2024
- Car key in the left hand, liveness detection radar in the right hand, UWB is imperative for cars!
- After a decade of rapid development, domestic CIS has entered the market
- Aegis Dagger Battery + Thor EM-i Super Hybrid, Geely New Energy has thrown out two "king bombs"
- A brief discussion on functional safety - fault, error, and failure
- In the smart car 2.0 cycle, these core industry chains are facing major opportunities!
- The United States and Japan are developing new batteries. CATL faces challenges? How should China's new energy battery industry respond?
- Murata launches high-precision 6-axis inertial sensor for automobiles
- Ford patents pre-charge alarm to help save costs and respond to emergencies
- New real-time microcontroller system from Texas Instruments enables smarter processing in automotive and industrial applications
- Some unclear points about self-oscillation
- Responsibility is heavier than Mount Tai! Talking about the safety requirements of China's high-speed rail signaling
- Write EEPROM, write FLASH experience record
- Commonly used algorithms for drones - Kalman filter (Part 9)
- Reset time problem
- Why does DLL not found error appear when running VB with Ginkgo?
- The problem of STM8L151k4t6 with programmed code being damaged by soldering?
- DSP28335 external interrupt configuration process
- Circuit PCB Design
- What is Wi-Fi 6?