0 Introduction
At present, the output power adjustment of high-frequency induction heating power supply is mainly achieved by changing the output frequency of the inverter or changing the input DC voltage of the inverter. Changing the output frequency of the inverter to adjust the output power is a commonly used power adjustment method. Its disadvantage is that the load of the inverter is inductive, especially when lightly loaded, the output power factor of the inverter is very low and the switching loss is large. This disadvantage can be changed by controlling the inverter to achieve power control. The pulse density modulated (PDM) DC/AC inverter uses the energy storage of the series resonant load and adopts the pulse group control method for the switch of the inverter. In one cycle, the output power is controlled by controlling the ratio (duty cycle) of the continuous on pulse signal and the continuous off pulse signal. The traditional PDM implementation method is to use many counters and some PWM dedicated chips to achieve this. This method is stable and mature, but the control circuit is complex. Here, a method of using CPLD to achieve pulse uniform modulation is proposed. This method is simple and easy, with a short development cycle, simple circuit, small size, wide frequency tracking range, and the switch tube can operate in zero current shutdown (ZCS) and zero voltage switch (ZVS) states.
1 Circuit Structure
FIG1 is a main circuit diagram of a pulse uniformly controlled series resonant inverter power supply, which includes a three-phase uncontrolled rectifier circuit, a filter circuit, an inverter circuit and a series resonant circuit.
In Figure 1: C1 and L1 are filter capacitors and filter inductors; L0 is the load; D1, D2, D3, and D4 are anti-parallel fast diodes; T1 and T2 are current transformers; R2 and R3 are voltage-dividing resistors; VT1, VT2, VT3, and VT4 are switch tubes IGBTs; C2 is a DC blocking capacitor, and T0 is a load matching transformer.
Figure 2 is a block diagram of the entire control system, which uses CPLD as the main control chip, including frequency tracking circuit, drive circuit, detection circuit, and display part.
The three-phase power supply outputs a DC voltage through the rectifier circuit. The DC voltage is filtered and input to the inverter. The inverter realizes DC/AC conversion, and the generated AC power is output to the load through the transformer. The switch tube of the inverter is controlled by the control circuit composed of CPLD. The main control process is as follows: VT1 and VT4 are turned on at the same time, and the current passes through the load in the forward direction; VT2 and VT3 are turned on at the same time, and the current passes through the load in the reverse direction to realize the conversion of DC to AC. In order to make the inverter successful, it must be ensured that the switch tubes of the upper and lower bridge arms cannot be turned on at the same time, otherwise the inverter will fail, so a dead zone must be added when designing the switch control signal. [page]
2 Pulse density control power principle
The basic idea of density regulation power control is to assume that there are N power regulation units in total, in which the inverter outputs power to the load in M power regulation units, and in the remaining (NM) units, the inverter stops working, and the load energy gradually decays in the form of natural oscillation, and the output pulse density is (M/N)%. The output power is regulated by controlling the IG-BT in Figure 3 to make VT1, VT4 and VT2, VT3 work alternately. The principle is as follows:
The control signals of the switch tubes VT1 and VT3 are regarded as the sum of n 1/2i (i=1, 2, ..., n) frequency dividers, that is, there are 2n control pulses in one control cycle. When the switch tube is fully working, that is, the power is 2n/2n when it is at its maximum. When 1 pulse is removed and 2n-1 pulses are left, the power value is (2n-1)/2n; when m (m<2n) pulses are removed and (2n-m) pulses are left, the power value is (2n-m)/2n; when there is no pulse, that is, when m=2n, the switch tube is completely turned off, that is, when the power is at its minimum, it is 0. By controlling the combination of these n frequency dividers, the output power of the inverter can be controlled.
This design uses 4 frequency dividers, that is, n=4. Including 2-frequency divider, 4-frequency divider, 8-frequency divider, 16-frequency divider, through their different combinations to get 16 different power values, as shown in Table 1. Among them, 0 means off, 1 means on. The power value is 0 when it is fully off, and 1 when it is fully on. The power values corresponding to the other combinations are shown in Table 1.
Figure 4 shows the control signal diagram when the power value is 1/16, 2/16, 4/16, and 8/16, and is also the principle diagram of 16-frequency division, 8-frequency division, 4-frequency division, and 2-frequency division. The control signals of VT2 and VT4 are the same at different power values. A brief description of the circuit working state is shown in Figure 4.
When VT1, VT4 are turned on and VT2, VT3 are turned off, the load resonant current is positive, and the load resonant current flows from a to b through VT1, R1, L2, C2, and VT4. The equivalent circuit is shown in Figure 4(a), and is powered by U.
When VT1, VT4 are turned off, VT2, VT3 are turned on, the load resonant current is negative, and the load resonant current flows from b to a through VT2, C2, L2, R1, VT3. The equivalent circuit is shown in Figure 4(b), which is powered by U.
When VT1, VT2, VT3 are turned off and VT4 is turned on, the load resonant current is positive. The load resonant current flows from a to b through R1, L2, C2, and VT4. The equivalent circuit is shown in Figure 4(c), and the current continues through D3.
When VT1, VT3, VT4 are turned off and VT2 is turned on, the load resonant current is negative, and the load resonant current flows from b to a through VT2, C2, L2, and R1. The equivalent circuit is shown in Figure 4(d), and the current is continued through D1. [page]
3 CPLD Implementation of Pulse Density Control Strategy
The Altera MAXⅡ EPM1270 chip is used as the platform, which includes 1 270 LEs, equivalent to 40 000 gates, 8 kB of user-available FLASH, and 116 I/O ports. QuartusⅡ5.1 is used for programming, downloading and simulation.
Figure 5 shows the logic module block diagram of CPLD pulse density control, which mainly includes pulse signal distribution control module, pulse distribution module, pulse width calculation and dead time setting module and PWM pulse width control module.
The pulse distribution module controls the pulse distribution module according to the power given value. The pulse distribution module consists of four frequency dividers: 2, 4, 8, and 16. It combines the frequency dividers according to the signal of the pulse distribution control module. The pulse width calculation and dead time setting module calculates the pulse width according to the input current signal, and controls the PWM output module to control the pulse width and set the dead time.
4 Simulation and Experiment
The following are some simulation and test diagrams of CPLD to realize pulse density power control. In the simulation diagram, the signals from top to bottom are: enable signal, current input signal Iin, power given PWM1, PWM2, PWM3, PWM4 control signals, which control VT1, VT4, VT3, VT2 respectively. Figure 6 shows the simulation diagram when the power value is 8/16 and 16/16 with QuartusⅡ5.1 as the software environment. Figure 7 is the corresponding test waveform diagram downloaded to Altera MAXⅡEPM1270 chip.
[page]
Figure 8 shows some experimental results of input power three-phase 220 V (phase voltage), frequency 50 Hz, output power P = 1 kw, resonant frequency f = 100 kHz, load equivalent inductance L2 = 26 μH, load equivalent resistance R1 = 6.5 Ω. The coordinate values of the two waveforms are the same, the square wave is voltage, and the sine wave is current.
5 Conclusion
The strategy of using CPLD to realize pulse uniform modulation power control inverter is proposed here. CPLD undertakes the tasks of PWM generation, density adjustment and dead time control. Through current feedback, frequency tracking is realized, so that the inverter always works in a resonant state, improves work efficiency and reduces losses. The simulation and test results show the feasibility of this scheme. This scheme has the advantages of high reliability, can effectively reduce the volume of the control board, simple circuit, and easy to achieve high frequency.
Previous article:Implementation of 16th-order FIR filter based on DSP Builder
Next article:Design of Intelligent A/D and D/A Modules Based on CPCI Bus
Recommended ReadingLatest update time:2024-11-17 02:42
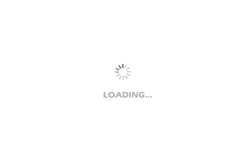
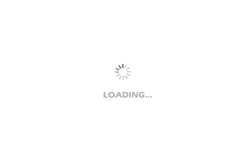
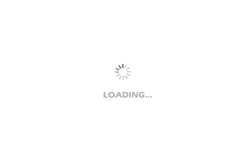
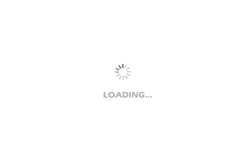
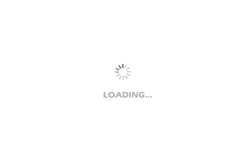
- Popular Resources
- Popular amplifiers
-
Learn CPLD and Verilog HDL programming technology from scratch_Let beginners easily learn CPLD system design technology through practical methods
-
Practical Electronic Components and Circuit Basics (4th Edition)_Explanation of basic circuit principles, introduction to electronic components, design of various circuits and practical circuit analysis
-
FPGA Principle and Structure (Zhao Qian)
-
EDA Technology Practical Tutorial--Verilog HDL Edition (Sixth Edition) (Pan Song, Huang Jiye)
- Huawei's Strategic Department Director Gai Gang: The cumulative installed base of open source Euler operating system exceeds 10 million sets
- Analysis of the application of several common contact parts in high-voltage connectors of new energy vehicles
- Wiring harness durability test and contact voltage drop test method
- Sn-doped CuO nanostructure-based ethanol gas sensor for real-time drunk driving detection in vehicles
- Design considerations for automotive battery wiring harness
- Do you know all the various motors commonly used in automotive electronics?
- What are the functions of the Internet of Vehicles? What are the uses and benefits of the Internet of Vehicles?
- Power Inverter - A critical safety system for electric vehicles
- Analysis of the information security mechanism of AUTOSAR, the automotive embedded software framework
Professor at Beihang University, dedicated to promoting microcontrollers and embedded systems for over 20 years.
- Innolux's intelligent steer-by-wire solution makes cars smarter and safer
- 8051 MCU - Parity Check
- How to efficiently balance the sensitivity of tactile sensing interfaces
- What should I do if the servo motor shakes? What causes the servo motor to shake quickly?
- 【Brushless Motor】Analysis of three-phase BLDC motor and sharing of two popular development boards
- Midea Industrial Technology's subsidiaries Clou Electronics and Hekang New Energy jointly appeared at the Munich Battery Energy Storage Exhibition and Solar Energy Exhibition
- Guoxin Sichen | Application of ferroelectric memory PB85RS2MC in power battery management, with a capacity of 2M
- Analysis of common faults of frequency converter
- In a head-on competition with Qualcomm, what kind of cockpit products has Intel come up with?
- Dalian Rongke's all-vanadium liquid flow battery energy storage equipment industrialization project has entered the sprint stage before production
- Allegro MicroSystems Introduces Advanced Magnetic and Inductive Position Sensing Solutions at Electronica 2024
- Car key in the left hand, liveness detection radar in the right hand, UWB is imperative for cars!
- After a decade of rapid development, domestic CIS has entered the market
- Aegis Dagger Battery + Thor EM-i Super Hybrid, Geely New Energy has thrown out two "king bombs"
- A brief discussion on functional safety - fault, error, and failure
- In the smart car 2.0 cycle, these core industry chains are facing major opportunities!
- Rambus Launches Industry's First HBM 4 Controller IP: What Are the Technical Details Behind It?
- The United States and Japan are developing new batteries. CATL faces challenges? How should China's new energy battery industry respond?
- Murata launches high-precision 6-axis inertial sensor for automobiles
- Ford patents pre-charge alarm to help save costs and respond to emergencies
- Purgatory Legend-Serial Communication War
- A circuit implementation of a precision full-wave rectifier circuit
- Happy Valentine's Day~ May all lovers in the world be happy and contented.
- Should you enter the IT industry? Four factors will tell you at a glance
- What are the commonly used chips that make up DSP systems?
- Analysis of power batteries in the first quarter of 2021
- Using STM32L452 to drive STTS751 through C-Driver-MEMS
- [RTT & Renesas high-performance CPK-RA6M4] 1. Hardware appreciation and RT-Thread development environment construction
- CB140-6G2C core board pin definition solution
- How to achieve PLC remote control through 4G network?