As a test of whether electric vehicles (EVs) can be popularized, Nissan launched the LEAF (Chinese name: 葉风) (Figure 1). This vehicle is designed and developed as a dedicated EV vehicle with the premise of mass production and sales worldwide. It is also a compact model designed based on the popular 5-door (hatchback) "family car". It can be fully charged in about 8 hours with a 200V power supply, and the sustainable driving distance on a single charge is 200km in JC08 mode (160km in USLA4 mode)* 1. As for the life of the lithium (Li) ion rechargeable battery, "it does not need to be replaced if it can travel 100,000km in 10 years" (Nissan technicians). Although this is the first commercial EV launched by Nissan under the conditions of many competitors, it aims to be a hot seller as soon as it is launched (table). The vehicle will first be launched in Japan and the United States in December 2010, and will be sold in parts of Europe in early 2011. Sales will begin in the global market, including other countries and regions, in 2012* 2 .
* 1 The JC08 mode is a driving mode for automobile fuel consumption tests specified by the Ministry of Land, Infrastructure, Transport and Tourism of Japan. The US LA4 mode is an urban driving mode for automobile fuel consumption tests in the United States, established by the US Environmental Protection Agency (EPA).
* 2 In line with this sales plan, Nissan is also building a mass production system for vehicles and lithium-ion rechargeable batteries. For vehicles, Nissan has established a production capacity of 50,000 units per year at the Oppama Plant, and started assembling the LEAF in October 2010. Nissan also plans to start production of the LEAF at the Smyrna Plant in the United States in the second half of 2012 and at the Sunderland Plant in the United Kingdom in 2013. The production capacities of the two plants are 150,000 units per year and 50,000 units per year, respectively. As a result, Nissan will have a global EV production capacity of 250,000 units per year in 2013. This is Nissan's total EV production capacity, including the LEAF. For lithium-ion rechargeable batteries, Nissan plans to implement mass production at the Zama Plant, the United Kingdom, Portugal, France, and the United States, and plans to establish a production system of 500,000 units per year by 2015, including the needs of Renault in France, in which it has a capital partnership.
Figure 1: Appearance of Nissan EV "LEAF". The charging port is designed at the front of the vehicle body.
Figure 2: Nissan EV "LEAF" dedicated chassis. The large and heavy battery pack is placed under the floor in the center of the vehicle body, creating a low center of gravity and bringing the center of gravity close to the center of the vehicle, improving handling safety. The FF method, which places the motor and inverter as the driving source in the "engine room", expands the interior space. Since there is no engine, a smooth floor shape and no exhaust tail pipe design are achieved.
Table 1: EVs that are currently in production or are scheduled to be launched
Focus on EV special vehicles
The LEAF is priced at 3,764,250 yen (tax included) in Japan. With the Japanese government subsidy, it is priced at a "cheaper price" of 2,984,250 yen (tax included) (Nissan CEO Toshiyuki Shiga). Sales have been very good since the start. A total of 26,000 orders have been received in the Japanese and American markets alone.
Nissan developed a special EV chassis for LEAF. The heavy and large lithium-ion rechargeable battery is installed under the floor in the center of the vehicle body, which is equivalent to the position between the front seat and the rear seat (in the length direction). It is particularly worth mentioning that Nissan has placed more battery modules (composed of 4 battery cells) directly under the front and rear seats, and less under the feet of the rear passengers, so as not to cause inconvenience to the passengers.
In addition, Nissan has added a battery bracket and an inverter bracket to the body frame. This not only fixes the respective components, but also has the effect of improving the rigidity of the body. The drive motor (hereinafter referred to as the motor) is located below the inverter bracket and is fixed to the subframe in the "engine room" of the engine vehicle (Figure 3). This is what is commonly known as a front engine (motor) front wheel drive (FF) vehicle.
Figure 3: The location of the inverter and motor. In a FF vehicle, the inverter and motor are installed in the "engine room".
The inverter is installed on the inverter fixing bracket that connects the left and right sides of the vehicle body. The vehicle body rigidity is also improved through this bracket.
In addition to the inverter and motor, many other components such as the DC-DC converter, charger, and heater are also located in the "engine room." This approach aims to expand the interior space and trunk capacity by adding components as much as possible outside the vehicle.
[page]
Performance that cannot be experienced by engine cars
One of the characteristics of LEAF is its high driving performance that exceeds that of engines in the same class. When the driver steps on the accelerator, it accelerates strongly. The motor is used as the driving source, and the maximum torque (280N•m) can be generated from almost zero speed, so the acceleration at the start is excellent. Although it is a compact model, it can achieve the same acceleration performance as a 3L engine vehicle.
However, the maximum speed of the motor is 9800rpm and the maximum speed is 145km/h, which is not suitable for high-speed driving on unlimited speed roads such as the German Autobahn.
In addition, LEAF also uses the characteristics of lithium-ion batteries with low internal resistance and high input and output current to control motor torque at high speed "in units of 1ms" (Nissan technicians). This is fully utilized for anti-vibration control. Specifically, the amplitude is suppressed by precisely controlling the torque near the torsional vibration resonance point of the drive system, achieving smooth acceleration without stiffness.
LEAF also has excellent handling stability. The large and heavy battery pack is installed under the floor in the center of the vehicle body, so the center of gravity is lower than that of FF-type engine vehicles, and because it is installed near the center of the vehicle, the inertia moment of rotation around the yaw axis is smaller. In addition, the aforementioned high-speed control of motor torque in units of 1ms improves handling stability when turning. Nissan LEAF development director Hidetoshi Kadota confidently stated, "You can turn smoothly just by turning the steering wheel. There is also less sense of separation from the rear end, making it a car with gentle movements."
Of course, the interior of the car is also very quiet. This is because there is no engine sound, vibration, or exhaust pipe sound, and the body rigidity is higher than that of an engine car. In addition, the vibration of the body is also suppressed.
Thorough quality inspection
In addition, LEAF also pays great attention to safety performance. The battery pack is stored under the floor in the center of the car body to strengthen the protection against external mechanical, thermal and electrical intrusions and minimize damage. In the collision test conducted, the frontal collision hit the car body at a speed of 56km/h and the rear collision hit the car body at a speed of 80km/h, and "it was confirmed that the battery pack did not suffer any damage" (Kadota).
To prevent electric shock, high-voltage components are enclosed in protective shells and insulated. In addition, a design is adopted to cut off high voltage in the event of a collision (Figure 4). In addition, these protective shells are connected to the vehicle body with wires to form an equal potential. In this way, even if these protective shells lose their insulation and passengers happen to touch the protective shells and the vehicle body at this time, there will be no potential difference and the current will not flow through the human body.
Figure 4: Improved safety against high voltage. The lithium-ion rechargeable battery is protected by the vehicle body structure, and the high-voltage components including the battery are insulated. In addition, the high voltage is cut off in the event of a collision.
We also conducted driving tests on flooded roads. For example, when the engine car "TIIDA" was driven on a flooded road with a depth of 700mm, the engine would shut down when water entered the intake pipe, but the LEAF had no problem driving on such a road. The reason is that the battery pack and other parts are tightly sealed.
Remote operation via smartphone
One of the features of LEAF is that it uses more IT technology than existing EVs. LEAF has introduced a dedicated information and communication system "EV-IT", which can access the data center of Nissan's in-vehicle information service "CARWINGS" to obtain vehicle information and operate the vehicle. This improves the convenience unique to EVs and eliminates users' concerns about battery exhaustion, etc.*3.
*3 To use CARWINGS, you need to join the "Nissan Zero Emission Support Program" or sign a "CARWINGS for EV" contract.
For example, it is equipped with a function that can display how far the current battery power can be used to travel while driving (displaying a map of the area that can be reached), or introduce nearby charging locations and facility information when the battery power is low (Figure 5). Among them, the problem of running out of battery is a particular concern for drivers, so in addition to saving charging point information based on past charging history, it will also automatically update through CARWINGS to keep the charging point information around the user's home always up to date.
Figure 5: EV-IT functions
(a) shows an EV-related function called "Zero Emission Menu" called up on the navigation screen. This function allows users to search for charging stations or check a map of their estimated destination (b).
CARWINGS service also allows you to check the battery status through your PC, smartphone or mobile phone, and start or stop charging at home or in the office. You can also remotely control the air conditioner, and adjust the temperature in the car to the optimal level before setting off when charging. This can reduce the load of the air conditioner after starting to drive, thereby extending the driving distance. In addition, it is equipped with a timer charging function that can charge at any time, and can use cheap late-night electricity to charge.
Previous article:Continental is committed to developing new intelligent charging technology
Next article:A new generation of EV that goes beyond engine cars: Nissan LEAF technology explained (Part 2)
Recommended ReadingLatest update time:2024-11-16 20:24
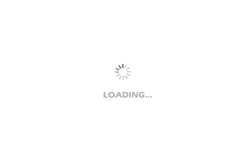
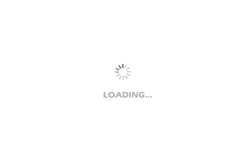
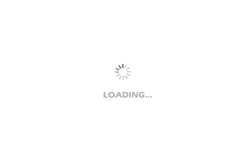
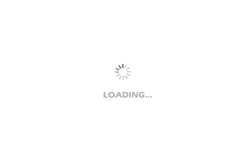
- Car key in the left hand, liveness detection radar in the right hand, UWB is imperative for cars!
- After a decade of rapid development, domestic CIS has entered the market
- Aegis Dagger Battery + Thor EM-i Super Hybrid, Geely New Energy has thrown out two "king bombs"
- A brief discussion on functional safety - fault, error, and failure
- In the smart car 2.0 cycle, these core industry chains are facing major opportunities!
- The United States and Japan are developing new batteries. CATL faces challenges? How should China's new energy battery industry respond?
- Murata launches high-precision 6-axis inertial sensor for automobiles
- Ford patents pre-charge alarm to help save costs and respond to emergencies
- New real-time microcontroller system from Texas Instruments enables smarter processing in automotive and industrial applications
- Innolux's intelligent steer-by-wire solution makes cars smarter and safer
- 8051 MCU - Parity Check
- How to efficiently balance the sensitivity of tactile sensing interfaces
- What should I do if the servo motor shakes? What causes the servo motor to shake quickly?
- 【Brushless Motor】Analysis of three-phase BLDC motor and sharing of two popular development boards
- Midea Industrial Technology's subsidiaries Clou Electronics and Hekang New Energy jointly appeared at the Munich Battery Energy Storage Exhibition and Solar Energy Exhibition
- Guoxin Sichen | Application of ferroelectric memory PB85RS2MC in power battery management, with a capacity of 2M
- Analysis of common faults of frequency converter
- In a head-on competition with Qualcomm, what kind of cockpit products has Intel come up with?
- Dalian Rongke's all-vanadium liquid flow battery energy storage equipment industrialization project has entered the sprint stage before production
- Allegro MicroSystems Introduces Advanced Magnetic and Inductive Position Sensing Solutions at Electronica 2024
- Car key in the left hand, liveness detection radar in the right hand, UWB is imperative for cars!
- After a decade of rapid development, domestic CIS has entered the market
- Aegis Dagger Battery + Thor EM-i Super Hybrid, Geely New Energy has thrown out two "king bombs"
- A brief discussion on functional safety - fault, error, and failure
- In the smart car 2.0 cycle, these core industry chains are facing major opportunities!
- The United States and Japan are developing new batteries. CATL faces challenges? How should China's new energy battery industry respond?
- Murata launches high-precision 6-axis inertial sensor for automobiles
- Ford patents pre-charge alarm to help save costs and respond to emergencies
- New real-time microcontroller system from Texas Instruments enables smarter processing in automotive and industrial applications
- High-paying job openings: A well-known American fashion brand of headphones is looking for electronic engineers, quality engineers, and firmware engineers who are fluent in English
- [National Technology N32G457 Review] OLED screen display driver and RTC electronic clock
- Things to note when writing programs based on TMS320 series DSP using C/C++
- "STM32 Library Development Practical Guide", a must-have for STM32 development!
- C language version of the time library function file or timestamp conversion algorithm
- To ensure the stability of electronic equipment, what tests need to be done on the hardware?
- Evaluation Weekly Report 20220801: Canaan K510 AI Development Kit is launched, and a domestic FPGA is expected to be launched this week~
- Why is the safety spacing of the board edge set in Altium Designer 18 invalid?
- Series and parallel circuits of common resistors
- Will the tuition be higher if I pursue graduate studies after I start working?