Electric vehicles are becoming more and more complex, with the number of electronic control units (ECUs) in vehicles already reaching around 150, distributed across various vehicle components, controlling key functions such as steering, braking, chassis and powertrain, as well as comfort functions such as infotainment and air conditioning. These ECUs communicate with each other through the in-vehicle network (IVN) to ensure that the vehicle can work together.
Today, the traditional automotive bus can no longer meet the needs of ECU. At the same time, as the automotive E/E architecture moves towards regionalization, a new bus is also needed to match it.
This year, ADI and BMW Group announced that they will be the first to adopt ADI's 10BASE-T1S E²B (Ethernet-Edge Bus) technology in the automotive industry. In-vehicle Ethernet connectivity is a key factor in driving the adoption of new partitioned architectures in automotive design, supporting major trends such as software-defined cars. BMW Group will be one of the first original equipment manufacturers (OEMs) to use this technology, using ADI's E²B technology in future smart cockpit ambient lighting systems.
This year, ON Semiconductor also exhibited the function of using 10BASE-T1S to achieve precise control of car headlights, and realized regional control through the ECU-Light architecture, including that each lighting function can be controlled through a graphical user interface (GUI), providing highly flexible headlight configuration, which means that automakers can design more personalized and diversified headlight systems to meet the needs of different models and driving conditions. At the same time, the diagnostic information of the LED driver can be read regularly to ensure that the system always maintains optimal performance.
IVN Protocol Evolution: Limitations of CAN, LIN and FlexRay
Since the 1990s, the automotive industry has widely adopted a variety of communication protocols, mainly including CAN, CAN FD, LIN and FlexRay. These protocols connect ECUs in a daisy chain, significantly reducing the total cable length and the overall weight of the vehicle. Among these protocols, CAN, CAN FD and FlexRay use unshielded twisted pair cables for communication, while LIN uses a single copper wire, further reducing weight.
However, the transmission rates of these traditional protocols are relatively low, such as LIN supports a maximum of 20 kb/s, CAN supports 1 Mb/s, CAN FD supports 5 Mb/s, and FlexRay supports 10 Mb/s. Although these rates have met the basic communication needs of vehicles in the past, with the continuous deepening of automotive electronics, especially the rapid development of advanced driver assistance systems (ADAS) and autonomous driving technologies, the bandwidth and speed of these protocols can no longer meet new requirements.
More importantly, CAN itself actually has a licensing fee. According to Bosch's official website, the first 10,000 CAN, CAN FD, and TTCAN products need to pay a basic license fee of 2,500 euros, and CAN XL also needs to pay a one-time fee of 2,500 euros; for products exceeding the number, a patent fee of 1% of net sales (with a certain upper limit) is charged. Therefore, free Ethernet has become a good solution in everyone's eyes.
ADAS and the Need for Regionalized Electronic Architecture
The complexity of ADAS functions, such as lane keeping assist, automatic emergency braking, and adaptive cruise control, requires the system to process a large amount of sensor data and perform real-time analysis. In order to support these high-bandwidth requirements, automotive Ethernet has gradually become the first choice. P2P (point-to-point) single-pair Ethernet (SPE) technology can achieve high-speed communication between ECUs through transmission rates of up to gigabits, and simplify the network structure inside the vehicle through regionalized electronic architecture.
In this regionalized architecture, the vehicle is divided into several functional areas, such as front-left, front-right, rear-left, rear-right and central areas. The ECUs in each area can be connected through the backbone of automotive Ethernet. This design greatly reduces the length of cables, improves the transmission efficiency of the network, and enables devices in different areas to work better in coordination, especially when processing high-bandwidth data related to ADAS.
10BASE-T1S: The standard for next-generation automotive networks
In response to these new demands, in 2019 IEEE introduced the 802.3cg specification, which includes two new physical layer standards: 10BASE-T1L (long distance) and 10BASE-T1S (short distance). 10BASE-T1S is particularly suitable for multi-point topology applications in automobiles. It allows multiple nodes (at least 8) to be connected via a single pair of twisted copper wires to achieve a communication rate of 10 Mb/s. This multi-point bus structure can not only significantly reduce the use of cables and connectors, but also reduce the number of physical layer devices (PHY) of the ECU. For example, in an 8-node LAN, traditional Ethernet requires 16 PHYs, while 10BASE-T1S only requires 8 PHYs. This optimization directly reduces the wiring complexity and weight of the vehicle.
Compared with the traditional P2P network topology, the multi-point topology of 10BASE-T1S is a major advantage. It can reduce the connection between nodes and reduce the overall weight of the cable, which is especially important for electric vehicles because the weight of the vehicle directly affects the range. Electric vehicle customers' expectations for vehicle range are constantly increasing, and 10BASE-T1S directly helps alleviate this anxiety by reducing the weight of the cable.
Physical Layer Collision Avoidance (PLCA)
In order to ensure that there is no data conflict in the multi-point topology, 10BASE-T1S introduces the physical layer collision avoidance mechanism (PLCA). PLCA controls the communication of all other nodes through the coordinator node (node 0). Each node gets the communication opportunity according to its physical layer ID sequence. If a node has no data to send, it will give the communication opportunity to the next node. The PLCA mechanism ensures that there will be no conflicts in the network and that the network bandwidth can be used effectively.
The advantage of this mechanism is its determinism. No matter how many nodes there are in the network or how big the data packet is, the system can communicate in a certain order without being affected by random conflicts. Compared with the traditional CSMA/CD (Carrier Sense Multiple Access/Collision Detection) mechanism, PLCA greatly improves the efficiency of the network, reduces communication delays, and ensures that high-bandwidth applications (such as ADAS) can run smoothly.
Power consumption advantage of 10BASE-T1S
Another advantage of 10BASE-T1S is its extremely low power consumption. Compared with the traditional CAN protocol, 10BASE-T1S uses a transmission voltage of 1 VPP and can operate at a 3.3V power supply, while CAN usually requires a 5V power supply. This low-power design is very suitable for ECUs in electric vehicles, especially when the system requires the lowest power consumption. 10BASE-T1S provides developers with a very competitive solution.
Security Advantages of 10BASE-T1S
In addition, 10BASE-T1S relies on mature Ethernet technology, which provides stronger network security for automotive networks. Traditional in-vehicle network protocols such as CAN and FlexRay do not have built-in security mechanisms, while 10BASE-T1S can directly utilize the security features of Ethernet, especially in automotive electronics, where network security is gaining increasing attention, especially in the era of autonomous driving and connected cars.
Full-vehicle Ethernet will be the future
With the development of vehicle electronics and intelligence, the future automotive network architecture will gradually transition to full Ethernet. The emergence of 10BASE-T1S not only fills the connection needs of low-bandwidth devices in automotive IVN, but also enables Ethernet to cover every corner of the vehicle, including sensors and actuators that use low-bandwidth communication.
Through the unified Ethernet standard, seamless data transmission from edge devices to central controllers can be achieved within the vehicle, greatly simplifying the conversion between different network protocols, reducing the use of gateways, and reducing system complexity and cost. In addition, 10BASE-T1S can be closely integrated with ADAS and in-vehicle infotainment systems, providing a reliable communication foundation for these high-bandwidth applications.
Functional Safety and the Deployment Prospects of 10BASE-T1S
The deployment of 10BASE-T1S not only performs well in network communications, it also has advantages in functional safety and redundant design. By using standardized Ethernet technology, developers can more easily integrate functional safety systems that comply with functional safety standards such as ISO 26262 in the automotive industry. This safety is crucial for handling critical tasks involving vehicle safety, especially in autonomous vehicles.
In addition, the low cost and low power consumption of 10BASE-T1S make it an ideal choice in future vehicle architectures. In particular, as vehicle architectures gradually transition to regionalized and service-oriented architectures, 10BASE-T1S can effectively support the development of these new architectures. By connecting sensors, actuators, and control units within the region to an efficient Ethernet network, it not only reduces the number of physical layer components, but also significantly improves the overall response speed and efficiency of the system.
Summarize
The 10BASE-T1S Ethernet standard has brought revolutionary changes to the automotive network architecture. It reduces the weight and cost of cables through a simplified multi-point topology design, and solves the packet collision problem through the PLCA mechanism. At the same time, the low power consumption, low cost and strong network security features of 10BASE-T1S make it an ideal choice for future automotive IVN.
Previous article:High-computing and high-security intelligent connected vehicle terminal | Fu Sai confirms application for the 2024 Golden Edition Award
Next article:Lightweight design of wiring harness for automobile economy: (voltage platform improvement, electrical architecture optimization, new materials)
Recommended ReadingLatest update time:2024-11-23 10:37
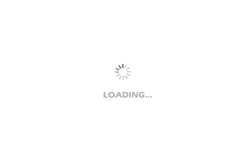
- 2024 China Automotive Charging and Battery Swapping Ecosystem Conference held in Taiyuan
- State-owned enterprises team up to invest in solid-state battery giant
- The evolution of electronic and electrical architecture is accelerating
- The first! National Automotive Chip Quality Inspection Center established
- BYD releases self-developed automotive chip using 4nm process, with a running score of up to 1.15 million
- GEODNET launches GEO-PULSE, a car GPS navigation device
- Should Chinese car companies develop their own high-computing chips?
- Infineon and Siemens combine embedded automotive software platform with microcontrollers to provide the necessary functions for next-generation SDVs
- Continental launches invisible biometric sensor display to monitor passengers' vital signs
- Intel promotes AI with multi-dimensional efforts in technology, application, and ecology
- ChinaJoy Qualcomm Snapdragon Theme Pavilion takes you to experience the new changes in digital entertainment in the 5G era
- Infineon's latest generation IGBT technology platform enables precise control of speed and position
- Two test methods for LED lighting life
- Don't Let Lightning Induced Surges Scare You
- Application of brushless motor controller ML4425/4426
- Easy identification of LED power supply quality
- World's first integrated photovoltaic solar system completed in Israel
- Sliding window mean filter for avr microcontroller AD conversion
- What does call mean in the detailed explanation of ABB robot programming instructions?
- STMicroelectronics discloses its 2027-2028 financial model and path to achieve its 2030 goals
- 2024 China Automotive Charging and Battery Swapping Ecosystem Conference held in Taiyuan
- State-owned enterprises team up to invest in solid-state battery giant
- The evolution of electronic and electrical architecture is accelerating
- The first! National Automotive Chip Quality Inspection Center established
- BYD releases self-developed automotive chip using 4nm process, with a running score of up to 1.15 million
- GEODNET launches GEO-PULSE, a car GPS navigation device
- Should Chinese car companies develop their own high-computing chips?
- Infineon and Siemens combine embedded automotive software platform with microcontrollers to provide the necessary functions for next-generation SDVs
- Continental launches invisible biometric sensor display to monitor passengers' vital signs
- Protecting Your IP Cores - Part 1 Soft IP, Section 1: Encryption of HDL Code
- EEWorld 2020 annual summary: useful articles, popular reviews, download top list, and well-received courses, all here!
- CC4085------Dual 2-2 input AND-OR gate
- Hey guys, this is my first time using Cadence's Pspice simulation and I encountered this problem
- Industrial Control Electronics Popular Data Download Collection
- How to use Bluetooth 4.2 to implement the Internet of Things
- What is the difference between silicon carbide, MOSFET and IGBT?
- [AT-START-F403A Review] + Zero-distance contact
- The power supply cannot be turned on when the USB flash drive is plugged in. What is the reason?
- Understanding of a curve graph in Chapter 4 of "High Frequency Electronic Circuits. Zeng Xingwen Edition"