Today’s cars have multiplied in complexity, with many new features added to enhance passenger comfort and infotainment systems, as well as advanced driver assistance systems (ADAS) and autonomous driving technologies to ensure driving safety. Many of these new features require increased communication with other vehicles and the surrounding environment, essentially turning the vehicle into an onboard data center.
These new functions are provided by modules such as lidar or cameras, each of which is controlled by an electronic control unit (ECU). Vehicles require a large number of ECUs, each of which requires dedicated wiring to connect it to the rest of the vehicle. Due to space constraints, managing an ever-expanding system of ECUs becomes a challenge, adding additional time and cost to vehicle production.
Increasing complexity can also lead to more potential points of failure. Therefore, high reliability becomes a key goal in wiring harness manufacturing, including connectors that connect cables to sensors and ECUs. A recent Molex survey found that more than half of respondents consider reliability as the main driver of brand loyalty, highlighting the importance of high reliability.
The automotive industry has been at the forefront of innovation in the use of industrial automation and robotics, thereby replacing manual assembly with machine technology, improving quality while reducing costs.
The complexity of wiring harnesses prevents them from benefiting from robotic assembly. Due to their lack of rigidity, wiring harnesses are easily bent and twisted, making them difficult for robots to handle. Manual assembly has always been the most viable option, but with kilometers of wires and hundreds of connectors on each vehicle, this approach is prone to systemic defects caused by human error. These failures can have significant consequences for manufacturers, including material costs and reputational damage.
Evolving Cabling Solutions
The traditional wiring method is to simply add connections between devices and ECUs based on their location in the vehicle, an approach known as flat architecture. In addition to being difficult, time-consuming, and error-prone to assemble, flat architecture is difficult to flexibly adapt to the addition of new systems. It also makes it difficult to diagnose faults and repairs, making it difficult to meet changing needs and standards.
To overcome these drawbacks, many manufacturers are adopting a zoned design that groups the vehicle architecture by function to provide control over the entire vehicle. Each domain has its own controller dedicated to the powertrain, infotainment, or safety systems, and communicates with other controllers through a gateway to create a complete vehicle control system.
Since each domain will have a series of devices distributed throughout the vehicle, each device requires a unique connection to the controller, the domain structure still cannot solve the wiring problem.
Although the domain approach is more adaptable than the traditional flat architecture, it is not the final answer to the vehicle wiring challenge. If we look at vehicle wiring from an evolutionary perspective, manufacturers will increasingly adopt the domain architecture in the coming years, but it is clear that this architecture is still just a stepping stone on the road to a better wiring approach.
The emergence of partitioned architecture
Zonal architecture is an advanced design that divides the functions within the vehicle into several zones according to their location. Each zone has its own regional gateway, which is responsible for controlling specific functions and subsystems in the zone, such as engine management, lighting, suspension or safety sensors. Since each gateway is close to the device it controls, the cable length required to connect them is relatively short.
The gateways communicate with each other and with the central computer via a high-speed network such as Ethernet, enabling the exchange of data and response to changing conditions. As a result, communication between the gateway and the central computer has more in common with computer networks than with traditional vehicle wiring harness solutions.
This revolutionary solution will change the way vehicles work and how they are manufactured, updated and maintained.
Compared with traditional methods, partitioned architecture has many advantages.
The most prominent of these is the reduction in the amount and complexity of cabling. With devices connected locally to the zone gateway, cable lengths can be kept to a minimum. This applies to both data and power cables, as the zone gateway can act as both a power distribution module and a data processing hub.
In addition, the communication links between the partitioned gateways and the central computing cluster only require a small number of high-speed network connections (such as a few twisted pairs), thus reducing the length of cables. Although redundancy of safety-critical systems is a necessary constant within the vehicle, the partitioned architecture can still significantly reduce the volume and weight of copper cables.
The reduction in wiring size will greatly simplify the installation of cable harnesses. Each area is installed in a modular manner instead of using a harness that spans the entire length of the vehicle. In addition, the weight reduction can also improve vehicle operating efficiency. For example, electric vehicles (EVs) can achieve longer charging intervals and higher power performance.
Another major advantage of the partition structure is flexibility, which can divide the vehicle's electronic equipment into smaller areas, so that new functions or subsystems can be added or modified without affecting the entire system, making it easier to adapt to changing needs. During the life cycle of the vehicle, updates can be made more convenient and cost-effective, while simplifying maintenance work (such as replacing motors and sensors). This will enable the dealer network to perform most of the vehicle maintenance updates and repairs on its own, without having to send the vehicle to a more advanced and complex repair workshop.
Software-driven functionality also allows the zoning gateway to be adapted and updated to accommodate new functionality as it is required.
With multiple zoned gateways distributed throughout the vehicle, redundancy and fault tolerance are enhanced. If one gateway fails, the others can continue to function, reducing the risk of a serious (potentially catastrophic) failure.
Because the vehicle electronics are divided into different zones, diagnostics are also made easier. Technicians no longer have to search for the source of a problem in a single complex system. Instead, they can evaluate a single zone to quickly isolate and repair the problem in that area.
In terms of overall system performance, the partitioned architecture distributes processing power among different partitioned gateways, thereby increasing communication speed, improving response time and improving resource utilization efficiency.
One of these key resources is the vehicle's electrical power. The partitioned architecture requires more distributed power sources to connect to the partitioned controllers distributed throughout the vehicle. In addition, each device such as ECU, motor and sensor requires power. Many automakers are looking beyond the existing 12V automotive power architecture to higher voltages (up to 48V). The higher the voltage, the lower the current, and smaller wires can be used to deliver the same power, reducing weight and increasing the efficiency of the vehicle.
Molex's MX150 medium voltage connector provides a 48V power architecture solution. The MX150 medium voltage connector enables automakers to upgrade to a 48V wiring architecture with minimal design engineering effort by adopting the proven MX150 form factor. This 48V upgrade capability saves significant cost and weight by reducing wiring size in a variety of in-vehicle applications.
▲MX150 medium voltage connector
Establishing a connection
Zoning architectures offer clear advantages, but they also present significant challenges. One such challenge is the connectors used between devices and zone controllers. Harsh environmental conditions coupled with high circuit count requirements for each connection will require new, complementary connectors to support zoning systems in today’s vehicles.
The industry will need a new generation of hybrid connectors to connect devices to partitions and work.
Connectors for central computing clusters will also need to be more resilient than traditional board-to-board connection solutions; they will need to provide higher pin counts and power connections. Standardized designs will enable interchangeable modules, simplifying the manufacturing process and facilitating upgrades.
Connectors that can accommodate automated assembly processes are an important factor in the successful adoption of partitioned architectures. Until manufacturers can reliably adapt cables and connectors for automated assembly processes, the installation of cables and connectors will likely remain a manual process.
As an experienced automotive connector supplier, Molex has developed a series of connection solutions designed based on automatic installation. With innovative connection solutions designed to improve both flexibility and ease of assembly, automotive OEMs can confidently adopt the advantages of partition architecture.
Previous article:Detailed explanation of FlexRay in-vehicle bus
Next article:Interpretation of A-PHY, the new generation of automotive high-speed connection standard
Recommended ReadingLatest update time:2024-11-16 10:33
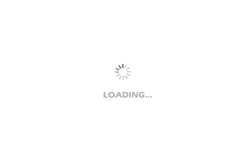
- Popular Resources
- Popular amplifiers
- Car key in the left hand, liveness detection radar in the right hand, UWB is imperative for cars!
- After a decade of rapid development, domestic CIS has entered the market
- Aegis Dagger Battery + Thor EM-i Super Hybrid, Geely New Energy has thrown out two "king bombs"
- A brief discussion on functional safety - fault, error, and failure
- In the smart car 2.0 cycle, these core industry chains are facing major opportunities!
- The United States and Japan are developing new batteries. CATL faces challenges? How should China's new energy battery industry respond?
- Murata launches high-precision 6-axis inertial sensor for automobiles
- Ford patents pre-charge alarm to help save costs and respond to emergencies
- New real-time microcontroller system from Texas Instruments enables smarter processing in automotive and industrial applications
- Innolux's intelligent steer-by-wire solution makes cars smarter and safer
- 8051 MCU - Parity Check
- How to efficiently balance the sensitivity of tactile sensing interfaces
- What should I do if the servo motor shakes? What causes the servo motor to shake quickly?
- 【Brushless Motor】Analysis of three-phase BLDC motor and sharing of two popular development boards
- Midea Industrial Technology's subsidiaries Clou Electronics and Hekang New Energy jointly appeared at the Munich Battery Energy Storage Exhibition and Solar Energy Exhibition
- Guoxin Sichen | Application of ferroelectric memory PB85RS2MC in power battery management, with a capacity of 2M
- Analysis of common faults of frequency converter
- In a head-on competition with Qualcomm, what kind of cockpit products has Intel come up with?
- Dalian Rongke's all-vanadium liquid flow battery energy storage equipment industrialization project has entered the sprint stage before production
- Allegro MicroSystems Introduces Advanced Magnetic and Inductive Position Sensing Solutions at Electronica 2024
- Car key in the left hand, liveness detection radar in the right hand, UWB is imperative for cars!
- After a decade of rapid development, domestic CIS has entered the market
- Aegis Dagger Battery + Thor EM-i Super Hybrid, Geely New Energy has thrown out two "king bombs"
- A brief discussion on functional safety - fault, error, and failure
- In the smart car 2.0 cycle, these core industry chains are facing major opportunities!
- The United States and Japan are developing new batteries. CATL faces challenges? How should China's new energy battery industry respond?
- Murata launches high-precision 6-axis inertial sensor for automobiles
- Ford patents pre-charge alarm to help save costs and respond to emergencies
- New real-time microcontroller system from Texas Instruments enables smarter processing in automotive and industrial applications
- Chinese Academy of Sciences releases domestic open source RISC-V processor "Xiangshan": the first version is scheduled to be taped out in July
- Trump administration "blacklists" Xiaomi, Xiaomi using Qualcomm chips is a "military-related company"???
- 『Anxinke Bluetooth Development Board PB-02-Kit』-3: Start Docker
- lan8720A strange reset problem?
- FAQ_How to calculate the response time from shutdown state to READY state
- The single-chip microcomputer has a built-in LCD driving function, and an external resistor drives the LCD screen. Please tell me the impact of external resistors and capacitors on the display
- Zigbee-IO port configuration
- There is something wrong with the program, please solve it
- What does the data check code mean? Can someone explain it to me?
- Python Raspberry Pi Programming