The rising penetration of electric vehicles (EVs) has stimulated market demand for optimized design, reduced costs, and improved vehicle operating efficiency, and has raised new challenges for product testing. Various power converters and traction inverters form the core of the electric vehicle powertrain subsystem and must be tested to achieve optimal efficiency levels. While wide-bandgap semiconductor devices such as SiC/GaN can actively support this, we still have other test challenges to contend with.
The introduction of 800V powertrain architecture is a milestone leap. Let's take a look at the current design and testing challenges related to the 800V electric vehicle powertrain architecture.
Unlock application potential with 800V systems
800V powertrain architecture refers to the electrical systems on electric vehicles with a nominal operating voltage of 800 volts. This architecture represents a significant performance improvement over the 400V powertrain architecture commonly used in current battery electric vehicles (BEVs). When using an electric vehicle with a 400V powertrain architecture, users must charge the vehicle on a public DC fast charger (DCFC) for 40 to 120 minutes. Specific charging times will be limited by the size of the actual cables responsible for delivering the required current to the battery pack. The 800V battery electric vehicle can reach an ultra-high charging rate of 350 or 400 kilowatts, which is a promising technology development route.
Transitioning to battery electric vehicles using an 800-volt architecture can alleviate or even eliminate users' "range anxiety" to a large extent. Doubling the voltage while keeping the current constant will result in a doubling of the vehicle's energy input. Increasing the charging speed of the vehicle by 50% (that is, reducing the charging time by 50%) can greatly alleviate users' concerns about running out of battery power during long journeys.
Bar chart of 800V system production share growth from 2020 to 2030. Data source: market research results of yole company
Increasing the range of battery electric vehicles
It only takes less than 23 minutes for a vehicle using an 800V system to increase the charge from 5% to 80%, adding an additional cruising range of approximately 200 miles. This is in sharp contrast to the 40 to 120 minute charging times of today's mainstream 400V battery powertrain systems.
In addition, the increased voltage can deliver the same amount of electricity at a smaller current, thereby effectively reducing the diameter of cables and connectors in the powertrain, reducing the weight of electric vehicles, and ultimately extending the driving range of battery packs of the same class.
Not only that, transitioning the operating voltage from 400 volts to 800 volts will also help improve the overall operating efficiency of the powertrain subsystem and simplify the vehicle's thermal management process.
According to market research firm Yole, it is expected that by 2023, 800V systems will begin to become the mainstream solution for the entire automotive industry. The many advantages mentioned above will become an important driving force in this transformation process and effectively promote the automotive industry, especially the high-end vehicle field, to move to 800V systems; among them, automobile manufacturers such as Audi, Porsche, Hyundai and Kia have already started Early related commercialization layout. Although only a few public DCFC charging stations are currently fully capable of supporting 800V architecture, the numbers are growing day by day, and it is likely that within the next 5 years, most public DCFC charging stations will begin to support charging powers of 150 kW or higher. .
Temperature Advantages of Wide Bandgap Semiconductor Devices
An important point when choosing a hardware approach is to use wide bandgap (WBG) semiconductor devices such as SIC and GAN switches. These devices are chosen for their high switching speed and large temperature tolerance. These devices operate efficiently at high temperatures, improving efficiency while reducing total harmonic distortion (THD). The wide operating temperature range of wide-bandgap semiconductor devices also helps simplify inverter design while minimizing the device's need for thermal management systems. In cooperation with standardization organizations such as JEDEC and IEC, we focus on establishing relevant standards for switching analysis and diode reverse recovery measurements, thereby playing a vital role in characterizing the performance of wide bandgap semiconductor devices.
The importance of oscilloscopes to the verification process
Oscilloscopes can play a vital role in validating and diagnosing design issues in electric vehicle traction motors and inverters. It helps designers meet stringent productivity requirements. But we must realize that an oscilloscope alone may not meet all measurement needs. This is where detection solutions and analysis software come in handy. Optically isolated voltage probes help designers perform measurements on high-voltage gate drivers.
With its 4 Series B MSO, 5 Series B MSO and 6 Series B MSO oscilloscopes, Tektronix can provide engineers with wide bandgap double pulse test (DPT, referred to as double pulse test) solutions to help them design the most advanced power converters. Solution for accurate and repeatable measurements. To complement this, engineers can leverage specially tailored software such as Tektronix's IMDA (Inverter Motor Driver Analysis) that supports three-phase measurements of PWM and mechanical data, increasing the overall usefulness of the solution.
To be able to make measurements at the right amplitude and frequency at critical moments, dedicated current and voltage probes are necessary. The 5 and 6 Series MSO oscilloscopes support high channel counts, inverter analysis software, and versatile probing options, making them an excellent solution for engineers designing electric vehicle powertrains.
Tektronix engineers are using a 5 Series B oscilloscope to test electric vehicle powertrains.
Previous article:Automobile hybrid technology basics and typical products
Next article:Who can win the "Holy Grail" of next-generation power battery technology in developing eVTOL?
Recommended ReadingLatest update time:2024-11-16 13:33
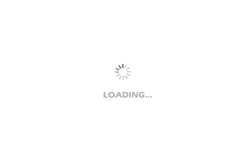
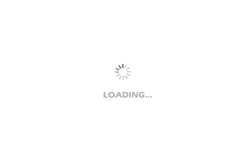
- Popular Resources
- Popular amplifiers
- Car key in the left hand, liveness detection radar in the right hand, UWB is imperative for cars!
- After a decade of rapid development, domestic CIS has entered the market
- Aegis Dagger Battery + Thor EM-i Super Hybrid, Geely New Energy has thrown out two "king bombs"
- A brief discussion on functional safety - fault, error, and failure
- In the smart car 2.0 cycle, these core industry chains are facing major opportunities!
- The United States and Japan are developing new batteries. CATL faces challenges? How should China's new energy battery industry respond?
- Murata launches high-precision 6-axis inertial sensor for automobiles
- Ford patents pre-charge alarm to help save costs and respond to emergencies
- New real-time microcontroller system from Texas Instruments enables smarter processing in automotive and industrial applications
- Innolux's intelligent steer-by-wire solution makes cars smarter and safer
- 8051 MCU - Parity Check
- How to efficiently balance the sensitivity of tactile sensing interfaces
- What should I do if the servo motor shakes? What causes the servo motor to shake quickly?
- 【Brushless Motor】Analysis of three-phase BLDC motor and sharing of two popular development boards
- Midea Industrial Technology's subsidiaries Clou Electronics and Hekang New Energy jointly appeared at the Munich Battery Energy Storage Exhibition and Solar Energy Exhibition
- Guoxin Sichen | Application of ferroelectric memory PB85RS2MC in power battery management, with a capacity of 2M
- Analysis of common faults of frequency converter
- In a head-on competition with Qualcomm, what kind of cockpit products has Intel come up with?
- Dalian Rongke's all-vanadium liquid flow battery energy storage equipment industrialization project has entered the sprint stage before production
- Allegro MicroSystems Introduces Advanced Magnetic and Inductive Position Sensing Solutions at Electronica 2024
- Car key in the left hand, liveness detection radar in the right hand, UWB is imperative for cars!
- After a decade of rapid development, domestic CIS has entered the market
- Aegis Dagger Battery + Thor EM-i Super Hybrid, Geely New Energy has thrown out two "king bombs"
- A brief discussion on functional safety - fault, error, and failure
- In the smart car 2.0 cycle, these core industry chains are facing major opportunities!
- The United States and Japan are developing new batteries. CATL faces challenges? How should China's new energy battery industry respond?
- Murata launches high-precision 6-axis inertial sensor for automobiles
- Ford patents pre-charge alarm to help save costs and respond to emergencies
- New real-time microcontroller system from Texas Instruments enables smarter processing in automotive and industrial applications
- Use stm32l452 to drive hts221 and stts751 routine
- [National Technology N32WB452 Review] + Basic Function Usage
- Will demand for SiC FETs increase in the future?
- Problems with pressure maintenance of testing machine
- Testing a battery-powered product with a 26K resistor between the battery pads (no battery is soldered at this time!),...
- When TMS320F28377D runs CLA, it shows that Cla1Task2 does not contain frame information
- Application and precautions of Hall elements
- Which one is better to use, the Type-C interface or the MicroUSB interface for mobile phone data cables?
- Showing goods + development board and multimeter
- Why is the GaN device [G-level is negative voltage powered]