introduction
The quality of a car's braking performance is mainly evaluated from the following three aspects: 1) Braking efficiency, i.e. braking distance and braking deceleration; 2) Constancy of braking efficiency, i.e. resistance to heat or water decay; 3) Directional stability of the car during braking, i.e. the ability of the car to avoid running off the track, skidding or losing steering ability during braking.
Usually, there are two forces in the braking process of a car: one is the friction resistance generated between the brake friction pad and the brake drum or brake disc, which is called the resistance of the brake system. Since it provides the braking force during braking, it is also called the braking force of the brake system; the other force is the friction resistance generated between the tire and the road surface, also known as the tire-road adhesion. If the braking force of the brake system is less than the tire-road adhesion, the car will remain stable during braking; on the contrary, if the braking force of the brake system is greater than the tire-road adhesion, the wheels will lock during braking. If the front wheel is locked, the car basically moves forward in a straight line and is in a stable state, but the car loses the ability to control steering, so the driver cannot avoid obstacles, pedestrians, and take necessary steering control on curves during braking. If the rear wheel is locked, the braking direction stability of the car becomes worse, and under very small lateral interference force, the car will have dangerous phenomena such as tailspin or even U-turn. Especially in some bad road conditions, such as slippery roads or ice and snow, wheel locking will make it difficult to ensure the driving safety of the car. In addition, the wheel locks during braking, causing local sharp friction, which will greatly reduce the service life of the tire.
1 ABS working principle
The Anti-lock Braking System (ABS) is an electronic device that automatically adjusts the wheel braking force to prevent the wheels from locking in order to achieve the best braking performance by controlling the brake line pressure acting on the wheel brake cylinder during the braking process. ABS is currently one of the effective measures to improve automobile braking safety that is generally recognized in the world.
2 Hydraulic ABS system based on MC9S12DP256 chip
Hydraulic ABS systems are mainly used in the braking systems of cars, mini cars and light vehicles. Unlike pneumatic ABS systems, the controller and regulator of most hydraulic ABS systems are an integrated system. Although it is difficult to manufacture, due to the development of the domestic car market in recent years and the improvement of traffic safety requirements, hydraulic ABS systems have attracted more and more attention from manufacturers, and many manufacturers have begun to develop hydraulic ABS systems.
The MC9S12DP256 chip of Freescale Semiconductor (formerly Motorola Semiconductor Division) is a single-chip microcomputer with a high-speed CPU12 core (Star Core) as the core, and a bus speed of 25MHz. The MC9S12DP256 single-chip microcomputer consists of standard on-chip peripherals, including a 16-bit central processor (HCS12CPU), 256K bytes of Flash, 4K EEPROM, and 12K bytes of RAM. It has a 5-way CAN bus, a temperature range of -40 to 125°C, and uses a 5 V power supply. It is mainly used for industrial control, especially for automobiles. The configuration block diagram of the hydraulic ABS system based on MC9S12DP256 control is shown in Figure 1.
Since the bus of MC9S12DP256 chip is built-in, it has strong anti-interference ability. The automatic programming/erasing algorithm improves performance, and the extended instruction set and addressing mode improve coding efficiency. The background debugging mode module (BDM) allows full-speed online simulation. In addition, using CodeWarrior Integrated Development Environment (IDE), through the background debugging mode (BDM), download the control program and modify the relevant parameters, without interfering with the operation of the target program, real-time monitoring of each register and memory, and realizing the on-board online debugging of the control program, thereby improving the development efficiency of the integrated system and the convenience of the test, which can greatly shorten the test cycle.
3 Hydraulic control principle
The hydraulic ABS system adopts an integrated structure, that is, the controller and the regulator are integrated into one, which can make the system structure simple and save wiring harnesses. At the same time, due to the use of MC9S12DP256 chip, it is sufficient to meet the requirements of ABS calculation, real-time control and diagnosis. The hydraulic control part mainly utilizes the characteristics of the three-position three-way solenoid valve. Its pressure regulation method and working principle are as follows:
(1) Normal braking (ABS not working)
During normal braking, the braking force is small, the wheels have not locked and slipped, the ABS does not work, and the three-position solenoid control valve is in the first state, that is, the left position of the three-position solenoid valve. The brake fluid from the brake master cylinder directly enters the four wheel cylinders through the three solenoid control valves to produce a braking effect. When the brake pedal is released to release the brake, the oil in the wheel cylinder still flows back to the master cylinder through the solenoid control valve. At this time, since the ECU (ABS electronic control unit) has not issued any instructions, the electric oil pump is in an inoperative state.
(2) Depressurization state When the vehicle brakes and the wheels are about to lock, the ECU issues a command based on the sensor signal to pass a large current through the coil of the three-position solenoid valve, putting the three-position solenoid valve in the third state, that is, the three-position solenoid valve is in the right position in the figure. The oil circuit leading to the master cylinder is closed, and the four wheel cylinders are connected to the accumulator. The high-pressure oil in the wheel cylinder flows into the accumulator through the solenoid valve, reducing the braking pressure and preventing the wheels from locking. At the same time, under the command of the ECU, the electric oil pump works to pressurize the oil flowing into the accumulator and transport it back to the master cylinder, preparing for the next braking action.
(3) Pressure-maintaining state When the brake cylinder reduces pressure (or increases pressure) to the optimal braking state, the ECU issues a corresponding command based on the signal from the wheel speed sensor to pass a small current through the coil. At this time, the three-position solenoid valve is in the second state, that is, the three-position solenoid valve in the figure is in the middle position, and all valve ports are closed to maintain the oil pressure in the wheel cylinder in the optimal braking state.
(4) Boost state: When the braking force is insufficient, the wheel speed sensor sends a signal, the ECU stops supplying power to the coil, and the three-position solenoid valve returns to the first state. The master cylinder and the wheel cylinder are connected again, and the high-pressure brake fluid in the master cylinder enters the wheel cylinder through the three-position solenoid valve, causing the braking force to increase rapidly.
[page]
ABS controls the above-mentioned pressure reduction, pressure maintenance and pressure increase states so that they are performed alternately, thereby ensuring that the vehicle obtains the best braking effect. The ABS system hydraulic circuit is shown in Figure 2.
4 Simulation test results
SIMUL INK is a software package for modeling, simulation and analysis of dynamic systems. It supports linear and nonlinear systems, continuous and discrete time models, or a mixture of the two. SIMUL INK has been widely used in industrial control and other fields. The actual braking process of a car is a very complex process, so it is almost impossible to describe the braking process completely and accurately. Before simulation, the braking process of the car can be appropriately simplified and assumed. After simplification and assumption, the car actually becomes a two-degree-of-freedom model for linear motion.
The equation of motion of the vehicle body during braking is:
In this paper, MATLAB /SIMUL INK software is used for simulation research. The simulation is carried out using the fifth-order variable step size Runge-Kutta method. The minimum simulation step size is 0.001 s and the maximum simulation step size is 0.01 s. A certain type of car is used as the simulation test object. The main parameters of the car are: full load mass 1 795 kg; wheelbase 2 800 mm; center of gravity height from the ground 655 mm; center of gravity distance from the front axle 1 430 mm; center of gravity distance from the rear axle 1370 mm; drag coefficient 0.4; center of drag height 965mm; frontal area 1 736 × 1 490 mm2; initial braking speed 80 km/h; road surface is ordinary cement road surface. The simulation results are shown in Figures 3 and 4.
5 Conclusion
(1) It can be seen from the simulation results that the hydraulic ABS system based on Freescale chips can keep the slip rate between 0.1 and 0.3 during braking, effectively preventing the wheels from locking and ensuring that the car has good braking performance.
(2) When ordinary industrial-grade chips are usually used as ABS control chips, they are not satisfactory in terms of temperature adaptability and system stability. This system uses Motorola's special automotive chip MC9S12DP256, which makes the system more reliable and stable, providing a new option for the development of hydraulic ABS systems.
Previous article:Design of TPMS system based on intelligent sensor MPXY8320A
Next article:Research on the parameter test circuit of vehicle cooling system based on C8051F020
Recommended ReadingLatest update time:2024-11-16 20:30
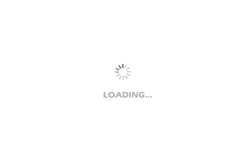
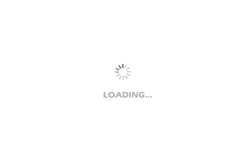
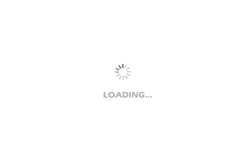
- Popular Resources
- Popular amplifiers
-
A review of learning-based camera and lidar simulation methods for autonomous driving systems
-
Practical Development of Automotive FlexRay Bus System (Written by Wu Baoxin, Guo Yonghong, Cao Yi, Zhao Dongyang, etc.)
-
Automotive Electronics Technology (Edited by Han Jinyu and Zhang Yong)
-
Driver Assistance Systems Brochure: Basic information, components and systems for active safety and comfort
- Car key in the left hand, liveness detection radar in the right hand, UWB is imperative for cars!
- After a decade of rapid development, domestic CIS has entered the market
- Aegis Dagger Battery + Thor EM-i Super Hybrid, Geely New Energy has thrown out two "king bombs"
- A brief discussion on functional safety - fault, error, and failure
- In the smart car 2.0 cycle, these core industry chains are facing major opportunities!
- The United States and Japan are developing new batteries. CATL faces challenges? How should China's new energy battery industry respond?
- Murata launches high-precision 6-axis inertial sensor for automobiles
- Ford patents pre-charge alarm to help save costs and respond to emergencies
- New real-time microcontroller system from Texas Instruments enables smarter processing in automotive and industrial applications
- Innolux's intelligent steer-by-wire solution makes cars smarter and safer
- 8051 MCU - Parity Check
- How to efficiently balance the sensitivity of tactile sensing interfaces
- What should I do if the servo motor shakes? What causes the servo motor to shake quickly?
- 【Brushless Motor】Analysis of three-phase BLDC motor and sharing of two popular development boards
- Midea Industrial Technology's subsidiaries Clou Electronics and Hekang New Energy jointly appeared at the Munich Battery Energy Storage Exhibition and Solar Energy Exhibition
- Guoxin Sichen | Application of ferroelectric memory PB85RS2MC in power battery management, with a capacity of 2M
- Analysis of common faults of frequency converter
- In a head-on competition with Qualcomm, what kind of cockpit products has Intel come up with?
- Dalian Rongke's all-vanadium liquid flow battery energy storage equipment industrialization project has entered the sprint stage before production
- Allegro MicroSystems Introduces Advanced Magnetic and Inductive Position Sensing Solutions at Electronica 2024
- Car key in the left hand, liveness detection radar in the right hand, UWB is imperative for cars!
- After a decade of rapid development, domestic CIS has entered the market
- Aegis Dagger Battery + Thor EM-i Super Hybrid, Geely New Energy has thrown out two "king bombs"
- A brief discussion on functional safety - fault, error, and failure
- In the smart car 2.0 cycle, these core industry chains are facing major opportunities!
- The United States and Japan are developing new batteries. CATL faces challenges? How should China's new energy battery industry respond?
- Murata launches high-precision 6-axis inertial sensor for automobiles
- Ford patents pre-charge alarm to help save costs and respond to emergencies
- New real-time microcontroller system from Texas Instruments enables smarter processing in automotive and industrial applications
- After the power supply common mode surge protection, the power supply output voltage rises instead of falling
- Disturbance-free continuous power supply solution (disturbance-free quick switching with anti-sway module)
- Power supply obstacle" + electromagnetic interference and inductive howling
- Install an N102 on STM32F103 and experience NB-IoT development at home
- Switching Power Supply
- TMS320C6748 DSP Development Kit (LCDK)
- Selecting a buck-boost solution
- MSP430F5529 library functions
- Recruitment for part-time MBSE technical or consulting services
- EEWORLD University - 10 hours to learn image processing opencv introductory tutorial