In electric vehicles, 40% of the cost comes from batteries, which are like the heart that provides "blood pumping function" for electric vehicles. The performance and life of batteries are important indicators for measuring the performance of electric vehicles. How to master these indicators and ensure that the operating status of each battery is optimal?
The battery management system (BMS) is responsible for the battery operation system. It plays the role of a "battery nanny". It processes a wide range of signals, including: battery cells, collisions, CAN, charging, water pumps, high voltage, insulation, etc.
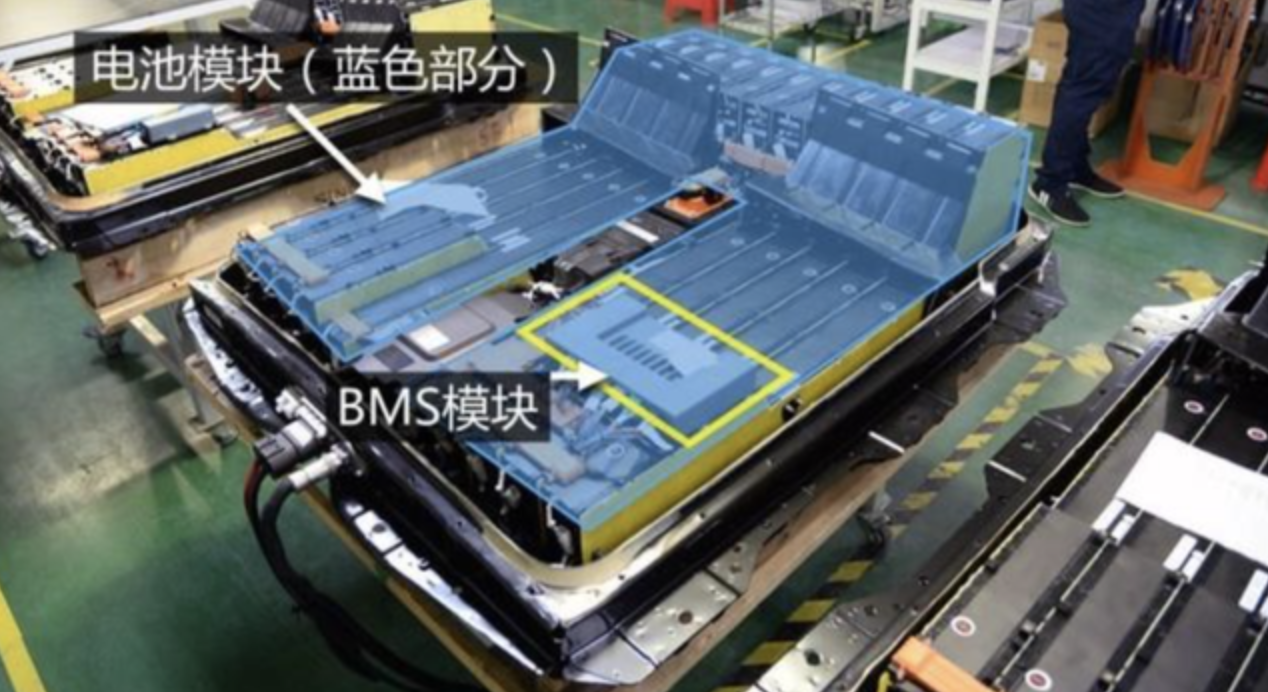
Overdischarge will cause permanent damage to the battery. In extreme cases, overheating or overcharging of lithium batteries will lead to thermal runaway, battery rupture or even explosion. Therefore, BMS can accurately measure the battery pack usage, protect the battery from overcharge and discharge, balance the power of each battery in the battery pack, analyze and calculate the battery pack power and convert it into understandable endurance information to ensure the safe operation of the power battery.What are the main chips in BMS?AFE module: realizes battery information collection, status monitoring and other functionsAFE (Analog Front End) is an integrated component that includes sensor interface, analog signal conditioning (including impedance transformation, programmable gain amplification, filtering and polarity conversion, etc.), analog multiplexer, sample and hold, ADC, data cache and control logic. Some AFEs also come with MCU, DAC and a variety of drive circuits.Battery balancing module: improve battery life and cycle lifeBattery imbalance affects battery life and battery cycle life. Battery imbalance is manifested by unequal voltages of each battery when multiple batteries are connected in series, especially at the end of charging and discharging. When batteries with different full charge capacities are connected in series, the series charging current is the same, but the battery with the smaller full charge capacity will be charged to a higher voltage first, which is manifested as unequal voltages of each battery. Even if the full charge capacity is the same, but the battery with different SOC is connected in series, the voltage of the battery with a higher SOC is higher, which is manifested as unequal voltages of each battery. Even if the full charge capacity and SOC are the same, but the internal resistance R of each battery is different, the IR voltage difference is different during charging and discharging, which will also lead to different battery terminal voltages. In addition, some external factors (such as local temperature of the battery pack or thermal imbalance between individual batteries) will also cause different aging rates of individual batteries, resulting in unbalanced internal resistance. In the end, it may be manifested as unequal voltages of each battery.The balancing circuit mainly includes active balancing and passive balancing. Active balancing is to transfer the excess power of the battery cell with the most power to the battery cell with the least power, or to the entire battery string to achieve energy recovery. Passive balancing is to consume the excess power of the battery cell with the most power through resistance heating.Computing unit (MCU, etc.): realizes control, calculation and other functionsAs a computing platform, MCU needs to meet AEC-Q100, ISO26262 and other certifications. Taking the ADI 48V hybrid BMS system as an example, the MCU plays the role of relay control, SOC/SOH estimation, balancing control, cell voltage, current, temperature data collection, data storage, etc. Compared with consumer-grade and industrial-grade MCUs, automotive-grade MCUs have higher industry barriers. Automotive-grade semiconductors have high requirements for product reliability, consistency, safety, stability and long-term effectiveness, and are difficult to develop: the external temperature difference of automobile driving is large, and there are high requirements for the wide temperature control performance of the chip; in terms of product life, the design life of the whole vehicle is usually 15 years or more, which is much higher than the life requirement of consumer electronic products; in terms of failure rate, the requirements of vehicle manufacturers for automotive-grade semiconductors are usually zero failure; in terms of safety, the high functional safety standards of automotive electronics provide sufficient safety guarantees for the mass production of increasingly complex electronic systems. The supply cycle of automotive-grade semiconductors needs to cover the entire life cycle of the vehicle, and the supply needs to be reliable, consistent and stable, which puts forward high requirements for the configuration and management of the enterprise supply chain.Isolation circuit: realize electrical isolation between high and low voltage modulesIsolation devices realize electrical isolation between high and low voltage modules, and the technical routes include optocoupler isolation and digital isolation. Isolation devices are safety devices that can convert and output input signals to achieve electrical isolation between input and output ends. Electrical isolation can ensure the safety of signal transmission between strong and weak current circuits. If electrical isolation is not performed, once a fault occurs, the current of the strong current circuit will flow directly to the weak current circuit, causing damage to the circuit and equipment. In addition, electrical isolation removes the ground loop between the two circuits, which can block the propagation of interference signals such as common mode and surge, making the electronic system safer and more reliable. Most devices that transmit signals between high voltage (strong current) and low voltage (weak current) need to be electrically isolated and pass safety certification. It is widely used in various fields such as information communication, power meters, industrial control, and electric vehicles.
Major BMS chip manufacturers in Europe and the United StatesThere are not many AFEs to choose from in BMS chips. The internal structures of the AFEs we can access are similar, and the differences lie in the number of sampling channels, the number, type and architecture of internal ADCs.The main suppliers of AFE are ADI, TI, ST, Panasonic, NXP and Renesas. ADI's product line mainly comes from the acquired Linear Technology and Maxim (in 2019, after ADI acquired Linear Technology, it cooperated with General Motors and other vehicle manufacturers to develop wireless BMS and launched a wireless BMS system and platform to detect and analyze battery data throughout the entire cycle from battery production to recycling to maximize the value of power batteries). Renesas' products mainly come from the acquired Intersil. The suppliers of AFE products are mainly foreign companies. At present, no domestic manufacturer has provided AFE chips.AFE major suppliers and product modelsFrom the MCU perspective, the main suppliers are TI, ST, NXP, Infineon, Renesas, etc. At present, many domestic MCU manufacturers are also actively deploying automotive-grade products, such as SinoWise, GigaDevice, Ingenic, Chipsea, National Technology, Unigroup Guoxin, Ninestar, Espressif, Broadcom Integrated, Fudan Microelectronics, Shanghai Belling, Jingfeng Mingyuan, etc.

Main MCU suppliers and product modelsIn terms of ADC, the main suppliers are TI, ADI, ST, Renesas, etc. Most of them are American manufacturers. Although ST has some, its product series are relatively small. The main domestic suppliers are Shanghai Belling, SiRuiPu, Shengbang Shares, and Xinhai Technology.In terms of digital isolation, it is mainly used for digital communication between high and low voltage, such as SPI communication between high voltage sampling and MCU on the BMS main control board, and SPI communication between sampling board AFE and MCU. The main suppliers are ADI, TI, Silicon Labs, etc. Of course, in addition to using digital isolators, optocouplers or transformer isolation solutions can also be used.More representative BMS chipsTI high-precision battery monitoring, balancing, and protectionThe electrification of automobiles is developing rapidly and irreversibly, and the BMS system has become a primary core issue. TI has made great achievements in the field of electric vehicle BMS, and has successively released wired BMS and wireless BMS solutions that meet the ASIL D standard, leading the industry.BQ79614-Q1 circuit topology source: TIBQ79614-Q1 is a high-precision battery monitor, balancer and protector that can be applied to hybrid and pure electric vehicle BMS modules. It can monitor the battery temperature in real time and can automatically pause and start operations to avoid overheating. The chip operates at 12V and can quickly perform high-precision voltage monitoring for 14 batteries within 128μS.The BQ79614-Q1 chip integrates a front-end filter and a post-ADC low-pass filter. The front-end filter is designed to reduce costs and enable the use of a simple, low-voltage differential RC filter on the battery input circuit. The ADC low-pass filter is designed to monitor the filtered DC voltage to facilitate the calculation of the battery charge state. This chip can be used to measure external thermistors. In terms of communication, the BQ79614-Q1 can be connected to the BQ7600 device or communicate directly with the MCU through the UART interface. In the event of an abnormality in the communication line, the MCU can communicate directly with the battery pack through an isolated differential daisy chain.
ST L9963E battery monitoring and protection chipSTMicroelectronics (ST) has been leading the semiconductor market for many years, with its chips applied in many fields, and has become a major supplier of automotive chips. In the automotive field, in order to meet market and design needs, it launched the L9963E battery monitoring and protection chip, which aims to solve the battery management system design problems faced by electric vehicles around the world, including China. The new product adopts a unique architecture that can measure 4 to 14 battery cells in series, and there is no delay in desynchronizing the sample signals. The test results show that although 31 L9963Es can be daisy-chained, the delay of the entire chain is still less than 4 seconds.The L9963E measures voltage with very high accuracy, with a maximum error of ±2 mV, while also measuring current to understand the actual capacity of each battery cell. In addition, the product's architecture ensures that each battery cell has dedicated resources to process the electrical data monitored by the chip, while similar products on the market usually share data processing resources between battery cells. By providing dedicated processing resources for each cell, we can provide synchronized readings and avoid delays caused by desynchronization. Within a daisy-chain network structure, the L9963E can also communicate via a serial bus with a bandwidth of 2.66 Mbps, while most bandwidths in the industry hover around 1 Mbps. Therefore, it takes 4 milliseconds to 16 milliseconds to read and process 434 battery cells.
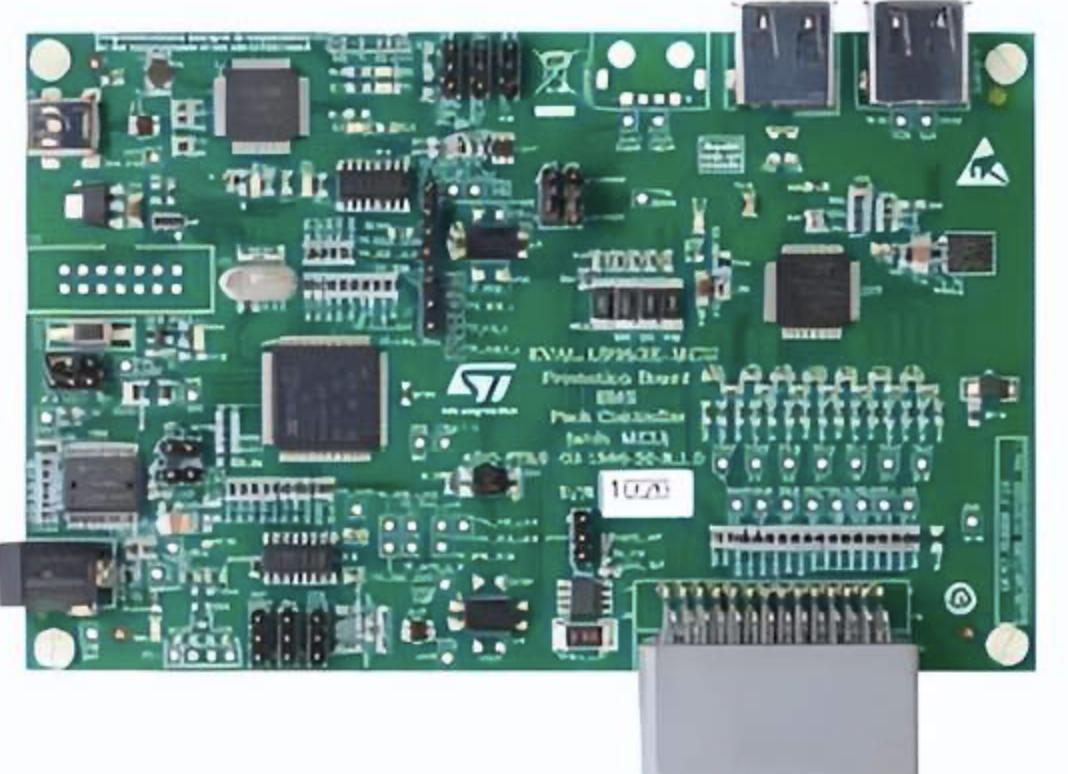