1. Application of CANFD in the new generation of intelligent connected vehicles
The traditional automotive network architecture is mainly composed of the CAN bus. The distributed electronic control unit (ECU) in the vehicle is divided into bus areas such as powertrain, body control, and assisted driving according to function; windows, lights, sunroofs, etc. are connected to the CAN network through the LIN bus .
In the wave of the new generation of intelligent connected vehicles, with the daily doubling of on-board ECUs and the rapid development of processor computing power and hardware, the network connecting ECUs requires a larger bandwidth, which far exceeds the capacity limit of traditional on-board networks such as CAN .
Therefore, the clear trend is to transition to CAN FD, which provides 64-byte data throughput and a maximum transmission rate of 5Mbps. Due to the high bandwidth, low latency and low cost characteristics of automotive Ethernet , it will replace the CAN bus and become the preferred network architecture in the next-generation vehicle architecture.
As shown in Figure 1, the core domain controllers (powertrain, body, entertainment, and ADAS) are connected together using the in-vehicle Ethernet as the backbone network. Each domain controller not only implements dedicated control functions, but also provides powerful gateway functions. As can be seen from Figure 1, below each domain controller, the communication between components is achieved through CANFD to share data.
Figure 1. The next generation of smart car network architecture
(picture drawn with reference to the Internet)
The introduction of CANFD and in-vehicle Ethernet has led to significant changes in the vehicle architecture of the new generation of intelligent connected vehicles. To achieve the upgrade from traditional vehicles to intelligent connected vehicles, major changes will be made in the design of vehicle production line control, laboratories, and ECU units. The CAN nodes involved are numerous and complex. If all are upgraded to CANFD nodes to implement the design, testing, and production of ECU units, it will be a relatively long process.
2. How to quickly implement CANFD upgrade of equipment?
With the development of a new generation of smart cars, many car manufacturers are considering using CAN FD to replace CAN to speed up data transmission. At present, major car manufacturers have not fully realized vehicle domain control. There is a phenomenon of coexistence of CAN and CANFD in production lines or laboratories. For example, millimeter-wave radar and other equipment in the ADAS system of a new generation of smart cars need to use CANFD to increase the communication rate and ensure safe driving. At the same time, ADAS is also the most important part of smart cars. As shown in Figure 2, the existing vehicle system is mainly based on the CAN network. During the debugging stage, the ADAS system cannot communicate with the power control and body control, so it is extremely important to open up the communication between CAN and CANFD.
Figure 2 CANFD communication status
Since CANFD is backward compatible with CAN, and ordinary CAN nodes cannot parse CANFD messages normally, as shown in Figure 3, the baud rates of CAN nodes and CANFD nodes are obviously mismatched. The maximum baud rate of CANFD is 5Mbps, which leads to communication failures, and errors are reported all the time, resulting in abnormal network communication.
Figure 3 CAN and CANFD waveform comparison
So how to ensure the normal communication test of CAN/CANFD nodes and quickly upgrade to CAN FD?
1. All CAN nodes in the network are upgraded to CANFD
Although this method can ensure that both CAN messages and CANFD messages can exist in the network, since the entire network is replaced by CANFD, it is costly and has a low utilization rate for early car factory testing or production of some units.
2.CAN nodes automatically ignore CANFD messages
This method prevents CAN 2.0 nodes in the network from identifying CANFD messages, which can ensure that there are no error frames in the network. However, the CAN nodes and CANFD nodes cannot communicate, which is a disadvantage and can only be used as a temporary solution.
3. Realize the conversion between CAN and CANFD
For the upgrade of CAN FD, if not all nodes are upgraded, most vehicle manufacturers will upgrade the power domain to CANFD first, and then upgrade each functional domain. Therefore, in order to avoid conflicts with the CAN bus, it is necessary to first open up the communication between the CAN network and the CANFD node to ensure that communication testing can be performed on the production line or in the laboratory. In this case, it is a better method to use a CANFD bridge as a conversion. As shown in Figure 4, engineers do not need to worry about how to complete the conversion between CAN and CAN FD messages. They only need to configure some parameters to achieve mutual conversion between CAN/CANFD and focus on the realization of product functions, reduce the cost of preliminary testing, and increase utilization.
Figure 4 CANFD bridge realizes CAN and CANFD communication
In addition, the testing, debugging, reading and storage of data of CANFD devices are also existing pain points. In the face of such phenomena, ZHIYUAN Electronics has launched a series of CANFD cards and recorders as shown in Figure 5 for commonly used interfaces, such as USB, serial port, network port, WiFi, PCIe, etc., to help engineers complete the design, verification, debugging, troubleshooting and maintenance of CANFD networks and automotive Ethernet.
Figure 5 CANFD series products
3. CANFDBridge helps OEMs quickly upgrade CANFD
CANFDBridge is a high-performance CAN/CANFD intelligent protocol bridge developed by Guangzhou Zhiyuan Electronics Co., Ltd. It integrates 2 CAN/CANFD switchable interfaces and supports ISO standard CANFD and Bosch CANFD standard. Each interface has an independent 2500VDC electrical isolation protection circuit and supports setting the baud rate range of 50K~5Mbps; supports default conversion processing of CAN to CAN, CAN to CANFD, CANFD to CAN, CANFD to CANFD and other messages. In addition, it has the following features:
1. Flexible transformation combination to restore data
The three methods of direct conversion, merging and splitting are used to realize the conversion between the 8-byte length of traditional CAN and the 64-byte length of CANFD, and the original data is restored without loss.
2. Support 64 group ID filtering, effective filtering does not require data
Each CAN channel supports setting 64 sets of standard frame ID/standard frame group ID/extended frame ID/extended frame group ID filtering configurations, effectively filtering unnecessary data and reducing bus load.
3. Support CAN ID and data conversion mapping function
CANFDBridge supports conversion mapping between ID and data, and can convert and output specific ID and data of input messages to achieve network access of the same device.
4. Flexible setting of baud rate sampling point, built-in terminal resistor enabled
CANFDBridge has built-in configurable terminal resistance, which can be enabled or removed by the user through software; it comes with a custom baud rate calculator that can calculate the baud rate registers of TESG1, TESG2, SJW and sampling points of the matching network to improve the adaptability of the device.
5. Bus error feedback function to improve fault warning capability
CANFDBridge has the function of sending error information back, allowing the device on this side to know the bus operation status on the other side and improve the fault warning capability.
6. Configure the interface to read the bus error status
Through the configuration interface of CANFDBridge, it is possible to read the communication error status, which can easily find the general direction of the fault, so as to facilitate the troubleshooting of software and hardware problems.
7. Support ECU flashing and E2E security algorithm, perfectly matching the AUTOSAR standard
ZCANPRO supports ECU refresh and E2E security algorithm, provides UDS protocol service, adds flash files and applies actuators, and can easily complete ECU data safe and fast refresh.
Previous article:A mirror to reveal true and false smart cars! The 2020 version of i-VISTA evaluation regulations is officially released
Next article:OTA empowerment, automotive remote diagnosis enters the era of intelligence
Recommended ReadingLatest update time:2024-11-16 11:28
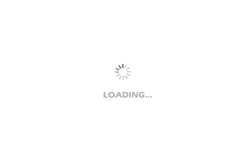
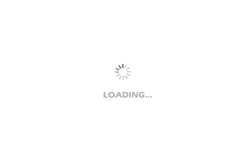
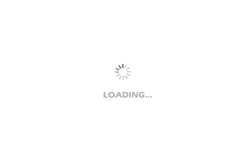
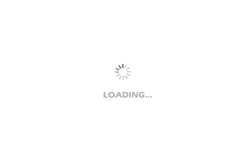
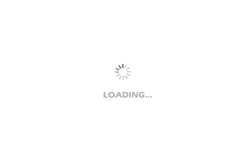
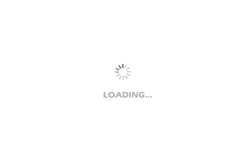
- Popular Resources
- Popular amplifiers
-
New Energy Vehicle Control System Inspection and Maintenance (Edited by Bao Pili)
-
Detailed explanation of big data technology system: principles, architecture and practice (Dong Xicheng)
-
Automotive CAN embedded intrusion detection system based on deep learning
-
Lightweight FPGA-based IDS-ECU architecture for automotive CAN networks
- Car key in the left hand, liveness detection radar in the right hand, UWB is imperative for cars!
- After a decade of rapid development, domestic CIS has entered the market
- Aegis Dagger Battery + Thor EM-i Super Hybrid, Geely New Energy has thrown out two "king bombs"
- A brief discussion on functional safety - fault, error, and failure
- In the smart car 2.0 cycle, these core industry chains are facing major opportunities!
- The United States and Japan are developing new batteries. CATL faces challenges? How should China's new energy battery industry respond?
- Murata launches high-precision 6-axis inertial sensor for automobiles
- Ford patents pre-charge alarm to help save costs and respond to emergencies
- New real-time microcontroller system from Texas Instruments enables smarter processing in automotive and industrial applications
- Innolux's intelligent steer-by-wire solution makes cars smarter and safer
- 8051 MCU - Parity Check
- How to efficiently balance the sensitivity of tactile sensing interfaces
- What should I do if the servo motor shakes? What causes the servo motor to shake quickly?
- 【Brushless Motor】Analysis of three-phase BLDC motor and sharing of two popular development boards
- Midea Industrial Technology's subsidiaries Clou Electronics and Hekang New Energy jointly appeared at the Munich Battery Energy Storage Exhibition and Solar Energy Exhibition
- Guoxin Sichen | Application of ferroelectric memory PB85RS2MC in power battery management, with a capacity of 2M
- Analysis of common faults of frequency converter
- In a head-on competition with Qualcomm, what kind of cockpit products has Intel come up with?
- Dalian Rongke's all-vanadium liquid flow battery energy storage equipment industrialization project has entered the sprint stage before production
- Allegro MicroSystems Introduces Advanced Magnetic and Inductive Position Sensing Solutions at Electronica 2024
- Car key in the left hand, liveness detection radar in the right hand, UWB is imperative for cars!
- After a decade of rapid development, domestic CIS has entered the market
- Aegis Dagger Battery + Thor EM-i Super Hybrid, Geely New Energy has thrown out two "king bombs"
- A brief discussion on functional safety - fault, error, and failure
- In the smart car 2.0 cycle, these core industry chains are facing major opportunities!
- The United States and Japan are developing new batteries. CATL faces challenges? How should China's new energy battery industry respond?
- Murata launches high-precision 6-axis inertial sensor for automobiles
- Ford patents pre-charge alarm to help save costs and respond to emergencies
- New real-time microcontroller system from Texas Instruments enables smarter processing in automotive and industrial applications
- Miniature Alphabet World Clock
- Make a simple lossless music player with STM32F103
- "New Concept Analog Circuit" Series 1, 2
- 51 MCU serial port connected to laser sensor to display distance
- How many types of pads have you seen in PCB design?
- Rowan University RF Fundamentals Lecture Notes
- Tencent employees angrily criticized management for high-intensity overtime work, netizens: role models of our generation
- When using STM32 debugging, a hardware error occurs
- What problems have you encountered recently when using the forum? Feel free to comment!
- Intelligent LED lighting solution based on sensor and MCU