By Tim Bresien, Microchip
From humble beginnings in the early 1990s, the CAN bus (Controller Area Network) has expanded from its base in automotive and industrial applications to connect and interconnect control systems in numerous other industries.
In traditional cars, the wiring system is quite daunting, with wires, data cables and criss-crossing control harnesses, making the vehicle difficult to repair. However, despite so many harnesses, the electronic functions of old cars are very few.
At the time, the first car to feature in-car connectivity via the CAN network was about to roll off the production line. This unique event would simplify automotive wiring and pave the way for incredibly advanced vehicle communications. It would kick off a series of networking milestones that would quickly culminate among automakers. Long before the commercial Internet, smartphones, or digital media, the introduction of the CAN bus redefined the possibilities of in-car communication and connectivity and sparked a growing technology landscape whose impact has transcended the automobile. The 1991 Mercedes S-Class model W140 was a trendsetter, featuring five CAN-connected electronic control units (ECUs).
Today's cars include as many as 60 to 100 ECUs and a wide variety of CAN networks and subnetworks connecting a dizzying array of electronic systems. On-board diagnostics (OBD) systems also utilize the information streams supported by CAN to provide real-time system performance data to drivers, mechanics, and regulators who monitor vehicle emissions.
The CAN protocol was originally developed by Robert Bosch for automotive applications in the mid-1980s and has become a trusted high-speed standard for applications that require reliable communication and high bandwidth utilization. The classic CAN protocol (ISO 11898) has also evolved into a development called CAN FD (ISO 11898-1) with faster rates to support the growing amount of data in smart cars. Advances in automotive design require sensor-driven capabilities to improve driver safety and optimize engine performance with little human intervention. Engine control units, automatic transmissions, active safety systems, seat control units, door modules, trailer interfaces, parking assist controls and collision avoidance systems continuously utilize CAN bus and CAN controller technology during vehicle operation. Data transmission speed and reliability are critical because systems can share network capacity in an instant while performing starts, stops and priority access.
Over the years, numerous standards bodies have redesigned the CAN-based standard for use in non-automotive industries, taking advantage of its short messaging capabilities and high transmission speeds through market-specific customizations of the upper layers of the protocol stack. You’ll find CAN-based networks in agricultural equipment, avionics, industrial and factory automation systems, smart buildings, medical systems, and many areas that would probably surprise the original inventors.
In fact, Microchip recently introduced a radiation-hardened microcontroller for space applications that includes a dual CAN controller in addition to Ethernet capabilities. CAN is also considered a reliable alternative for spacecraft control systems.
Microchip leverages our rich heritage in the automotive industry and our commitment to supporting our customers throughout their design process. Incorporating the CAN protocol into designs is a cost-effective communication option that provides a high degree of real-time capabilities for all electrical environments, from simple to complex. Microchip offers a complete range of products to meet the needs of high-performance embedded applications using the CAN protocol, including 8-bit, 16-bit and 32-bit microcontrollers, 32-bit microprocessors and digital signal controllers (DSCs) as well as integrated CAN, external CAN controllers and CAN transceivers. With easy-to-use development systems, code examples, drivers and application notes, Microchip offers a comprehensive CAN bus solution that enables low-risk product development, lower total system cost and faster time to market for high-performance embedded devices.
Previous article:As automotive electronic architecture continues to evolve, what will be the most expensive automotive semiconductor in the future?
Next article:Three automotive camera module power supply strategies, how to choose the right one?
Recommended ReadingLatest update time:2024-11-16 10:39
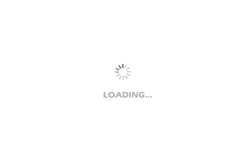
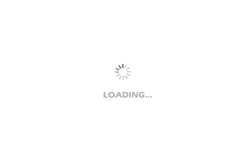
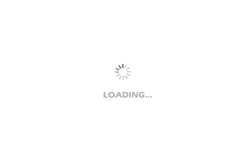
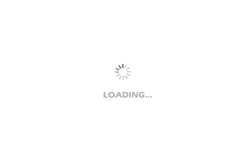
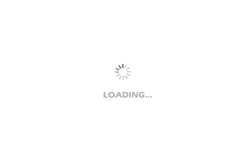
- Popular Resources
- Popular amplifiers
-
New Energy Vehicle Control System Inspection and Maintenance (Edited by Bao Pili)
-
Detailed explanation of big data technology system: principles, architecture and practice (Dong Xicheng)
-
Automotive CAN embedded intrusion detection system based on deep learning
-
Lightweight FPGA-based IDS-ECU architecture for automotive CAN networks
- Car key in the left hand, liveness detection radar in the right hand, UWB is imperative for cars!
- After a decade of rapid development, domestic CIS has entered the market
- Aegis Dagger Battery + Thor EM-i Super Hybrid, Geely New Energy has thrown out two "king bombs"
- A brief discussion on functional safety - fault, error, and failure
- In the smart car 2.0 cycle, these core industry chains are facing major opportunities!
- The United States and Japan are developing new batteries. CATL faces challenges? How should China's new energy battery industry respond?
- Murata launches high-precision 6-axis inertial sensor for automobiles
- Ford patents pre-charge alarm to help save costs and respond to emergencies
- New real-time microcontroller system from Texas Instruments enables smarter processing in automotive and industrial applications
- Innolux's intelligent steer-by-wire solution makes cars smarter and safer
- 8051 MCU - Parity Check
- How to efficiently balance the sensitivity of tactile sensing interfaces
- What should I do if the servo motor shakes? What causes the servo motor to shake quickly?
- 【Brushless Motor】Analysis of three-phase BLDC motor and sharing of two popular development boards
- Midea Industrial Technology's subsidiaries Clou Electronics and Hekang New Energy jointly appeared at the Munich Battery Energy Storage Exhibition and Solar Energy Exhibition
- Guoxin Sichen | Application of ferroelectric memory PB85RS2MC in power battery management, with a capacity of 2M
- Analysis of common faults of frequency converter
- In a head-on competition with Qualcomm, what kind of cockpit products has Intel come up with?
- Dalian Rongke's all-vanadium liquid flow battery energy storage equipment industrialization project has entered the sprint stage before production
- Allegro MicroSystems Introduces Advanced Magnetic and Inductive Position Sensing Solutions at Electronica 2024
- Car key in the left hand, liveness detection radar in the right hand, UWB is imperative for cars!
- After a decade of rapid development, domestic CIS has entered the market
- Aegis Dagger Battery + Thor EM-i Super Hybrid, Geely New Energy has thrown out two "king bombs"
- A brief discussion on functional safety - fault, error, and failure
- In the smart car 2.0 cycle, these core industry chains are facing major opportunities!
- The United States and Japan are developing new batteries. CATL faces challenges? How should China's new energy battery industry respond?
- Murata launches high-precision 6-axis inertial sensor for automobiles
- Ford patents pre-charge alarm to help save costs and respond to emergencies
- New real-time microcontroller system from Texas Instruments enables smarter processing in automotive and industrial applications
- Application solutions and optimization suggestions for low-power Bluetooth ranging technology
- Art on Silicon (1)
- What happened to the stm32f407 font update failure? It has been stuck at 99%
- Based on the automatic generation of IoT mini-programs by Gizwits, you can quickly create your own IoT mini-applications
- Can you unlock your phone with a photo? I feel relieved after knowing the truth!
- Where is today's sign-in?
- The power ripple is too large when Nor Flash is working
- Draw an LCD expansion board for the HPM6750EVKMINI
- Disassemble the Geiger counter, a glass tube can detect radiation dose, the principle is clear at a glance
- Dynamic Power Path Management for Battery Charging ICs