(Image source: Allegro Microsystems official website)
According to foreign media reports, Allegro Microsystems has launched the A8060x series of LED backlight drivers, which use innovative PEB patented control technology (pre-emptive boost) to successfully eliminate the annoying noise generated by the PWM modulation circuit in the LED driver. Allegro is a supplier of power and sensor solutions for motion control and energy-saving systems.
The A8060x series uses PEB control technology to greatly reduce output voltage ripple and eliminate the common problem of audible noise generated by ceramic output capacitors during PWM dimming, while requiring less output capacitance overall. The system uses 200 Hz PWM dimming to achieve an LED brightness contrast ratio of 15000:1. If PWM and analog dimming are combined, the contrast ratio is even higher, reaching 150000:1.
ALT80600 and A80603 combine a switching converter, a metal oxide semiconductor field effect transistor (MOSFET) and four current receivers. A80601 and A80602 drive external boost field effect transistors to achieve higher output power. All parts can be configured in boost or single-ended main inductor converter (SEPIC) topology to meet different needs. The switching converter is designed for low electromagnetic interference, including programmable switching frequency, controllable switching rate and programmable high-frequency jitter noise processing. In addition, the clock pin allows other switching converters to synchronize to the switching frequency of A8060x to enhance the anti-electromagnetic interference performance of the entire system.
The A8060x series of parts are suitable for all types of automotive backlighting devices, such as audio and video systems, instrument panels, and head-up displays (HUDs). These parts use a single 4.5 to 40 V supply and can continue to operate at a low voltage of 3.9 V once started. Therefore, they can withstand stop/start, cold start, dual battery, and load dump in automotive systems. The A8060x has the safety and protection features required for automotive applications. The ALT80600 and A80603 have four LED strings, each capable of up to 120 mA, with a total current of up to 480 mA. The A80601 and A80602 provide up to 840 mA of LED current through 4 or 6 strings, respectively.
Previous article:Preh's automotive temperature sensor is equipped with a CAN interface and can be installed anywhere in the vehicle
Next article:Fraunhofer Institute successfully integrates multiple components on GaN chip
Recommended ReadingLatest update time:2024-11-16 13:45
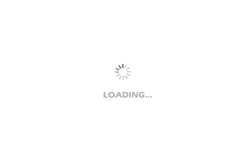
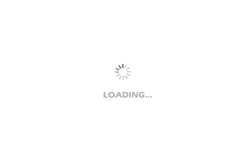
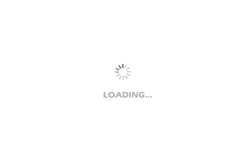
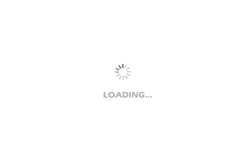
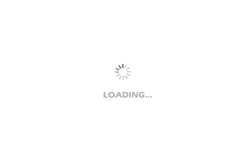
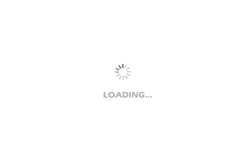
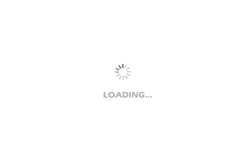
- Popular Resources
- Popular amplifiers
-
西门子S7-12001500 PLC SCL语言编程从入门到精通 (北岛李工)
-
Small AC Servo Motor Control Circuit Design (by Masaru Ishijima; translated by Xue Liang and Zhu Jianjun, by Masaru Ishijima, Xue Liang, and Zhu Jianjun)
-
Intelligent Control Technology of Permanent Magnet Synchronous Motor (Written by Wang Jun)
-
100 Examples of Microcontroller C Language Applications (with CD-ROM, 3rd Edition) (Wang Huiliang, Wang Dongfeng, Dong Guanqiang)
- Car key in the left hand, liveness detection radar in the right hand, UWB is imperative for cars!
- After a decade of rapid development, domestic CIS has entered the market
- Aegis Dagger Battery + Thor EM-i Super Hybrid, Geely New Energy has thrown out two "king bombs"
- A brief discussion on functional safety - fault, error, and failure
- In the smart car 2.0 cycle, these core industry chains are facing major opportunities!
- The United States and Japan are developing new batteries. CATL faces challenges? How should China's new energy battery industry respond?
- Murata launches high-precision 6-axis inertial sensor for automobiles
- Ford patents pre-charge alarm to help save costs and respond to emergencies
- New real-time microcontroller system from Texas Instruments enables smarter processing in automotive and industrial applications
- Innolux's intelligent steer-by-wire solution makes cars smarter and safer
- 8051 MCU - Parity Check
- How to efficiently balance the sensitivity of tactile sensing interfaces
- What should I do if the servo motor shakes? What causes the servo motor to shake quickly?
- 【Brushless Motor】Analysis of three-phase BLDC motor and sharing of two popular development boards
- Midea Industrial Technology's subsidiaries Clou Electronics and Hekang New Energy jointly appeared at the Munich Battery Energy Storage Exhibition and Solar Energy Exhibition
- Guoxin Sichen | Application of ferroelectric memory PB85RS2MC in power battery management, with a capacity of 2M
- Analysis of common faults of frequency converter
- In a head-on competition with Qualcomm, what kind of cockpit products has Intel come up with?
- Dalian Rongke's all-vanadium liquid flow battery energy storage equipment industrialization project has entered the sprint stage before production
- Allegro MicroSystems Introduces Advanced Magnetic and Inductive Position Sensing Solutions at Electronica 2024
- Car key in the left hand, liveness detection radar in the right hand, UWB is imperative for cars!
- After a decade of rapid development, domestic CIS has entered the market
- Aegis Dagger Battery + Thor EM-i Super Hybrid, Geely New Energy has thrown out two "king bombs"
- A brief discussion on functional safety - fault, error, and failure
- In the smart car 2.0 cycle, these core industry chains are facing major opportunities!
- The United States and Japan are developing new batteries. CATL faces challenges? How should China's new energy battery industry respond?
- Murata launches high-precision 6-axis inertial sensor for automobiles
- Ford patents pre-charge alarm to help save costs and respond to emergencies
- New real-time microcontroller system from Texas Instruments enables smarter processing in automotive and industrial applications
- Transfer-【TWS headphones】Some you really don’t know
- Need help 24V 100mA working current sensorless built-in MOS three-phase brushless motor driver chip
- (A-Current Signal Detection Device) First Prize of Zhejiang Province_Hangzhou Dianzi University
- Is this what the 0 detection is like?
- IAR FOR 430 Failed to re-intialize A possible solution
- Design information for temperature monitoring system
- Speed, frequency, chip instruction set
- The MPU9250 magnetometer ID reading does not get the correct value for the following reasons:
- CircuitPython 6.0.0 Beta 1 released
- Controlling LED brightness under ZSTACK