The automobile tire pressure monitoring system (TPMS) is mainly used to automatically monitor the tire pressure in real time while the car is driving, and to provide alarms for tire leakage and low air pressure to ensure driving safety and the life safety of drivers and passengers. Early warning system. This article details the components of a TPMS system as well as design considerations such as device selection, energy saving, and installation.
When a car is driving at high speed, tire failure is what all drivers worry about most and is the most difficult to prevent. It is also an important reason for sudden traffic accidents. According to statistics, 70%-80% of traffic accidents on highways are caused by tire blowouts. How to prevent tire blowouts has become an important issue in safe driving. According to the analysis of relevant experts, maintaining standard tire pressure while driving and detecting tire leaks in time are the keys to preventing tire blowouts, and TPMS will undoubtedly be the ideal tool.
Figure 1: PSB TPMS system structure diagram.
At present, TPMS is mainly divided into two types: one is TPMS based on wheel speed (WSB TPMS, indirect TPMS). This system uses the wheel speed sensor of the automobile ABS system to compare the speed difference between tires to achieve For the purpose of monitoring tire pressure, the main disadvantage of this type of system is that it cannot judge the situation of two or more tires being deflated at the same time and the speed exceeding 100 km/h; the other is TPMS based on pressure sensors (PSB TPMS, which directly (Type TPMS), this system uses a pressure sensor installed in each tire to directly measure the tire pressure, and displays and monitors the tire pressure. When the tire pressure is too low or there is leakage, the system will automatically alarm . PSB TPMS is superior to WSB TPMS in terms of functionality and performance. Many European automobile manufacturers have equipped PSB TPMS in their own models, including Germany's BMW Z8, France's Citroën C5, Lincoln Continental, Chrysler and Dodge minivans, as well as Chrysler 300M and Concorde Limited passenger cars, Ponti Gram's flagship Bonneville SE and more. Most domestic automobile manufacturers have not yet conducted research in this area. With the requirements of internationalization and the export of domestically produced automobiles, I believe that domestic manufacturers will keep up with this pace.
TPMS system composition
PSB TPMS mainly consists of a TPMS transmitting module consisting of pressure and temperature sensors and signal processing units and RF transmitters installed in the car's tires, as well as an RF receiver and liquid crystal display (LCD) installed on the car's driving console including a digital signal processing unit. composition. The system is depicted in Figure 1.
1.TPMS sensor
The TPMS sensor is a system-on-chip module that integrates a semiconductor pressure sensor, a semiconductor temperature sensor, a digital signal processing unit and a power manager. In order to enhance the tire pressure detection function, many TPMS sensor modules also add acceleration sensors, voltage detection, internal clocks, watchdogs, and 12-bit ADC, 4kB Flash, 2kB ROM, 128B RAM, 128B
Figure 2: TPMS module installed in the tire.
ASIC digital signal processing unit for EEPROM and other functions. These functional chips enable the TPMS sensor to not only detect changes in tire pressure and tire temperature in real time while the car is moving, but also to realize functions such as instant startup of the car, automatic wake-up, and power saving when the car is moving. The power manager ensures that the system achieves low power consumption so that one lithium battery can be used for 3-5 years.
TPMS pressure sensors are designed and produced based on MEMS technology. They mainly include silicon integrated capacitive pressure sensors, such as Freescale's MPXY8020, MPXY8040; silicon piezoresistive pressure sensors, such as GE NovaSensor's NPX1, NPXC01746, Infineon SensoNor's SP12, SP12T, SP30. The silicon piezoresistive pressure sensor uses a high-precision semiconductor resistance strain gauge to form a Wheatstone bridge as a force-to-electric conversion measurement circuit, and its measurement accuracy can reach 0.01-0.03% FS.
The TPMS pressure sensor is an on-chip system module. Its internal typical architecture includes an integrated silicon micromachined pressure sensor, temperature sensor, accelerometer, battery voltage detection, internal clock, and an analog-to-digital converter (ADC), sampling /Hold (S/H), SPI port, calibration, data management, digital signal processing unit for ID code. The module has mask programmability, that is, it can be configured using customer-specific software. The piezoresistive sensor is made of a MEMS pressure sensor and a semiconductor SoC circuit in a package using integrated circuit technology. There is a pressure/temperature introduction hole on the top of the package to directly introduce the pressure onto the stress film of the pressure sensor. The inner wall of the circular stress film fixed on the periphery is composed of semiconductor strain gauges to form a Wheatstone measurement bridge. At the same time, this hole will also The ambient temperature is directed to the semiconductor temperature sensor.
To facilitate identification by the TPMS receiver, each pressure sensor has a unique 6-8 digit ID code.
2. Pressure/temperature signal processing and emission
The pressure/temperature signal is processed by the ASIC/SoC circuit in the TPMS sensor module and transmitted to the signal processing unit installed in the transmitting module through its SPI port. It is synthesized into a data stream and then enters the RF transmitting IC in the same package. According to the set Ultra-high frequency (UHF) modulated transmission to a receiver installed in the bridge. as shown in picture 2.
In order to reduce the area occupied by the measurement and signal processing IC and the volume of the transmission module in the car tire, combined SoCs are also used for pressure/temperature signal processing and transmission, such as ATMEL's ATAR862 and Freescale's MC68HC908RF2, which combine a single MCU. , an ultra-high frequency (UHF) RF transmitter integrated in the same package.
MCU is generally a 4-bit or 8-bit CPU core, including clock management, EEPROM, RAM, multiple timers, multiple I/O ports, internal crystal oscillator, etc. The UHF RF transmitter takes ATAR862 as an example. T5754 UHF ASK/FSK is embedded inside.
Figure 3: T5754 UHF ASK/FSK RF transmitter.
RF transmitter, T5754 is internally composed of PLL, VCO, power amplifier, etc. (see Figure 3). The external crystal oscillator source supplies the VCO through the serial port resonator. The PLL provides the clock to the MCU. The MCU modulates the encoded data through the power amplifier in UHF Specify the frequency and transmit it to the antenna. The antenna uses a loop antenna printed on the PCB board, and the transmit power requires the PA to output 7-10dBm at 9.5mA.
ASK is amplitude conversion modulation, and FSK is frequency conversion modulation. The North American standard for RF transmission frequency is 315MHz, the European standard is 433.92MHz, and South Korea is 448MHz. Some people have suggested that the new standard be 868MHz.
3.Installation of TPMS transmitting module
Since most of today’s cars have eliminated inner tubes, it has brought great convenience to the installation of TPMS transmitting modules. Currently, there are two ways to install TPMS transmitting modules in car tires: installation using valve nozzles and installation using tightening buckles. on the wheel hub. No matter which method is used, the tire must be re-balanced after the TPMS transmitting module is installed.
4.TPMS receiver and display
The TPMS receiver consists of UHF ASK/FSK RF receiving IC, signal processing MCU, keyboard, and LCD display. The RF receiving IC and signal processing MCU are installed in a box and can be installed in the car instrument box. The LCD display with control keyboard can be installed on the driver's console. The LCD display can display the pressure, temperature and temperature of each tire in real time. ID identification code, and sound and light alarm. UHF ASK/FSK RF receiver takes T5743 as an example. The chip consists of low noise amplifier (LAN), low pass filter (LPF), intermediate frequency power amplifier, ASK/FSK demodulator, data interface, as well as PLL, XTO, VCO , mixer composition (Figure 4). The signal received by the antenna is amplified by LAN at the RF analog front-end, filtered by LPF, and demodulated by ASK/FSK. The extracted data is communicated to the MCU of the TPMS receiver. After software processing, the tire pressure, temperature, and ID code are restored and displayed on the LCD. Intelligently identify whether the system is safe and provide sound and light alarms.
The receiver's MCU needs to have 8K Flash and 32-bit I/O ports to meet the needs of system functions.
TPMS system solution
Figure 4: T5743 UHF ASK/FSK RF receiver.
The SP12 sensor module, ATAR862, T5743, and AVR MCU main chips can form a complete TPMS system (Figure 2). A car requires 4 TPMS transmitting modules (one more for the spare tire) and 1 TPMS receiver. A truck requires 6-12 TPMS transmitting modules. In order to improve the system's receiving capability and anti-interference ability, a receiving antenna needs to be installed on the car chassis during system installation, as shown in Figure 5.
1. Device selection
Since the TPMS transmitting module works under conditions of severe vibration, large changes in ambient temperature, and inconvenience for maintenance at any time, all devices are required to have good reliability and stability and be able to adapt to working temperatures from -40°C to +125°C. scope. In order to reduce the size of the TPMS transmitting module, save power consumption and enhance functions, it is necessary to use on-chip composite chips as much as possible, such as composite chips including pressure, temperature, acceleration and ASIC, including MCU and Tx (RF) or Rx (RF) Composite chip.
TPMS is a product designed, produced and inspected according to industrial standards and sold at the price of consumer electronics products, so the production cost of the product is crucial. The ESD protection of the product must comply with the MIL-STD.833 standard, that is, the human body model (HBM) is greater than 4KV.
2. Power saving and wake-up
In order for the TPMS transmitter module to work for 3-5 years on a lithium battery, system power saving is a very important issue. Therefore, only by letting the system enter sleep mode most of the time can power be saved and battery life extended. There are generally two ways to wake up the TPMS system when the car starts and when the car enters high-speed driving. One is to perform a self-test of the TPMS when the car starts and when the car enters high-speed driving, use a pre-set software program to perform regular patrol inspections. To this end, the TPMS receiver needs to send out a calling signal, and a wake-up chip, such as ATA5283, must be installed on the TPMS transmitting module. Since the wake-up frequency is 125kHz low frequency, the TPMS receiver needs to send out a calling signal with a certain power. Add a first-level antenna driver to the TPMS receiver, such as ATA5275; the second is to add an acceleration sensor to the sensor module and use the sensitivity of its mass block to motion to realize automatic startup of the car, enter the system self-check, and press the motion button when the car is driving at high speed. The speed automatically and intelligently determines the detection time period, and uses software to set the safe period, sensitive period and dangerous period to gradually shorten the patrol inspection period and improve early warning capabilities.
3. Tire pressure and temperature
Figure 5: TPMS installation in cars and trucks.
The pressure and temperature of car tires are closely related, and they are also the life safety of car drivers and passengers. When the car tire pressure is lower than the standard value, the deformation increases and the force changes, which can easily cause the wheel wall ply to break in an annular shape, cause uneven tread wear, and sharply increase tire shoulder wear; at the same time, each component is glued to the ply. The shear force between the layers and cord layers increases, and the heat generation intensifies, which reduces the physical properties of the rubber layer and cords and shortens the service life of the tire. If the tire pressure is lower than 80% of the normal pressure for a long time, the tire will heat up rapidly and delaminate when driving at high speed, eventually leading to a puncture.
When the tire pressure is higher than the standard value, the contact area between the tire and the ground is reduced and the unit pressure increases, causing increased wear in the middle of the tire tread. Indoor tests have proven that: It is generally believed that if the air pressure is increased by 25%, the tire life will be reduced by 15-20%; if the air pressure is reduced by 25%, the tire life will be reduced by about 30%. (Note: The normal tire pressure of a general car is around 210kpa (1kgf/cm=98kpa), and the appropriate pressure for a multi-seat commercial vehicle (7-9 seats) is around 240kpa.) The higher the tire temperature, the lower the tire strength. The greater the deformation (generally the temperature cannot exceed 80 degrees, when the temperature reaches 95 degrees, the condition of the tire is very dangerous), the tire wear will increase by 2% for every 1 degree increase; every time the driving speed doubles, the tire mileage will be reduced by 50 %. Therefore, overtemperature and speeding are not allowed.
Previous article:Designing LIDAR Systems for Automotive Using High-Speed ADCs
Next article:Design and application of Flash file system in vehicle MP3 player
Recommended ReadingLatest update time:2024-11-16 16:33
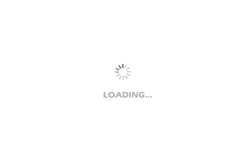
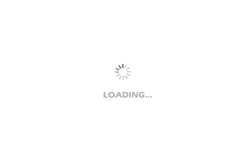
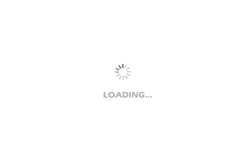
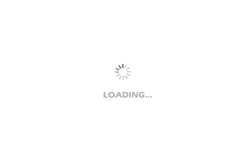
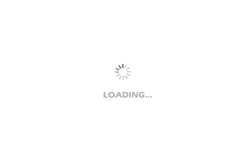
- Popular Resources
- Popular amplifiers
-
Wireless Sensor Network Technology and Applications (Edited by Mou Si, Yin Hong, and Su Xing)
-
Modern Electronic Technology Training Course (Edited by Yao Youfeng)
-
Modern arc welding power supply and its control
-
Small AC Servo Motor Control Circuit Design (by Masaru Ishijima; translated by Xue Liang and Zhu Jianjun, by Masaru Ishijima, Xue Liang, and Zhu Jianjun)
- Car key in the left hand, liveness detection radar in the right hand, UWB is imperative for cars!
- After a decade of rapid development, domestic CIS has entered the market
- Aegis Dagger Battery + Thor EM-i Super Hybrid, Geely New Energy has thrown out two "king bombs"
- A brief discussion on functional safety - fault, error, and failure
- In the smart car 2.0 cycle, these core industry chains are facing major opportunities!
- The United States and Japan are developing new batteries. CATL faces challenges? How should China's new energy battery industry respond?
- Murata launches high-precision 6-axis inertial sensor for automobiles
- Ford patents pre-charge alarm to help save costs and respond to emergencies
- New real-time microcontroller system from Texas Instruments enables smarter processing in automotive and industrial applications
- Innolux's intelligent steer-by-wire solution makes cars smarter and safer
- 8051 MCU - Parity Check
- How to efficiently balance the sensitivity of tactile sensing interfaces
- What should I do if the servo motor shakes? What causes the servo motor to shake quickly?
- 【Brushless Motor】Analysis of three-phase BLDC motor and sharing of two popular development boards
- Midea Industrial Technology's subsidiaries Clou Electronics and Hekang New Energy jointly appeared at the Munich Battery Energy Storage Exhibition and Solar Energy Exhibition
- Guoxin Sichen | Application of ferroelectric memory PB85RS2MC in power battery management, with a capacity of 2M
- Analysis of common faults of frequency converter
- In a head-on competition with Qualcomm, what kind of cockpit products has Intel come up with?
- Dalian Rongke's all-vanadium liquid flow battery energy storage equipment industrialization project has entered the sprint stage before production
- Allegro MicroSystems Introduces Advanced Magnetic and Inductive Position Sensing Solutions at Electronica 2024
- Car key in the left hand, liveness detection radar in the right hand, UWB is imperative for cars!
- After a decade of rapid development, domestic CIS has entered the market
- Aegis Dagger Battery + Thor EM-i Super Hybrid, Geely New Energy has thrown out two "king bombs"
- A brief discussion on functional safety - fault, error, and failure
- In the smart car 2.0 cycle, these core industry chains are facing major opportunities!
- The United States and Japan are developing new batteries. CATL faces challenges? How should China's new energy battery industry respond?
- Murata launches high-precision 6-axis inertial sensor for automobiles
- Ford patents pre-charge alarm to help save costs and respond to emergencies
- New real-time microcontroller system from Texas Instruments enables smarter processing in automotive and industrial applications
- Download the information and watch the video to win a prize | Tektronix HDMI 2.1 test solution is now available for download, and you can also watch the supporting video
- Things to note when using C/C++ to write programs based on TMS320 series DSP
- Generate sine wave data using microcontroller DAC and C language
- RISC-V RVB2601 First Experience--Section 4--Sensor Module Interface
- Based on micropython-1.9.4 ESP8266 motor control firmware
- MATLAB reads txt file data and processes it
- Easy to use, LiChuang EDA. Haha!
- [Start at 10:30] Interpretation of TI's latest smart lock, visual doorbell, and network camera solutions, and recommendations for its core components
- C6678 multi-core DSP development - connected domain marking of vlib application
- Nanjing MIIT certified enterprise [urgently hiring IC engineers with high salary]