introduction
With the development of science and technology, the printing industry has begun to shift from traditional analog production to digital production. As the core coloring device of the offset printing machine, the control accuracy of the ink fountain plays a very important role in the production quality and automation level of the offset printing machine. The traditional ink fountain is adjusted manually, which makes the production quality of the offset printing machine poor, the production preparation time is long, and the resources are seriously wasted. An ink fountain control system composed of an ink fountain console control system, a motor control system and a host computer system has been widely used in the foreign printing industry. This new ink fountain control system can greatly improve the control accuracy of the ink fountain, shorten the production preparation time and reduce the production cost. The ink fountain console control system described in this article is designed on the basis of tracking international advanced technology and meets the domestic market conditions. It is of great significance to improve the printing quality and automation level of domestic offset printing machines.
1 Introduction to the ink fountain control system
The ink fountain system of an offset printing machine usually consists of 2 to 4 ink fountains (one ink fountain is called a unit), an operating table and a host computer. Each ink fountain has a certain number of ink keys for adjusting the ink volume. In this system, the number of ink keys for each ink fountain is 21. The ink fountain operating table control system is a part of the entire ink fountain control system and is an interface for interaction between people and machines. The operator controls each ink key of the ink fountain through the ink fountain operating table control system. At the same time, the ink fountain operating table displays the position information, communication status information and various fault information of each ink key of the ink fountain. The structure diagram of the ink fountain operating table control system is shown in Figure 1. The display driver and keyboard scanning module consists of a display driver and keyboard scanning circuit and three groups of keys and display units. Each ink key corresponds to a group of keys and display units, as shown in Figure 2. The down-adjustment key is used to adjust the ink key to move in the direction of reducing the ink volume, the up-adjustment key is used to adjust the ink key to move in the direction of increasing the ink volume, the lock key is used to lock the position of the ink key, the lock indicator light is used to indicate the current lock state, and the digital tube and light column are used to indicate the current position of the ink key (the position of the ink key can be 0 to 99).
The digital tube in the system is a 7-segment digital tube, and the light column is composed of 20 LED lights. The entire operating table has 21 groups of buttons and display units, plus some other overall control buttons. This system needs to control 796 LEDs (each digital tube is equivalent to 8 LEDs) and 70 buttons.
2 When the buttons and display unit ink fountain console control system is working, it needs to cooperate with the motor drive system and the host computer system to adjust the position of each ink key. The ink fountain console control system communicates with other systems through the CAN bus.
2 Hardware structure of ink fountain control system
2.1 Main control chip
The control system of the ink fountain operation table uses the PIC18F8680 microcontroller produced by Microchip as the main control chip. The PIC microcontroller adopts the Harvard bus structure and the reduced instruction set (RISC). It has a high code compression rate, fast running speed, and rich varieties. It has up to 2MB of program memory and 4KB of data memory, up to 10MIPS execution speed, priority interrupts and 8×8 single-cycle hardware multipliers. The PIC18F8680 microcontroller has the following characteristics:
1) Highly integrated internal resources. The PIC18F8680 chip integrates many peripheral modules, such as SPI (serial peripheral interface) communication module, I2C (inter-integrated circuit bus interface) module, CAN module that complies with the international standard ISO CAN, etc. These functions greatly simplify the peripheral circuit design and software design of the ink fountain console control system.
2) Strong driving capability. The maximum source current/sink current can reach 25mA.
3) The PIC18F8680 chip has a power-on reset circuit (POR), a power-on delay timer (PWRT) and a watchdog circuit (WDT). These circuits greatly improve the reliability and stability of the ink fountain console control system in complex industrial environments.
4) The PIC18F8680 chip has 80 pins, of which 64 are user I/O ports. Such a large number of user I/O ports makes it easier for the main control module to control a large number of display drivers and keyboard scanning modules, thus facilitating the future upgrade and expansion of the ink fountain console control system.
2.2 CAN bus communication circuit
CAN bus is the abbreviation of controller area network, which is mainly used for process detection and control. It was first proposed in the 1980s. CAN bus is one of the most widely used field buses in the world. It has been widely used in automobiles, aviation, industrial control, measurement and control systems, distributed systems and other fields.
The CAN bus uses a multi-master station working mode and performs bus access arbitration based on priority. The CAN bus signal transmission is broadcast, and all nodes can receive the signal on the bus. The signal contains the transmission address, that is, the identifier. Each node can automatically receive the information of this node with the help of the receiving filter. Error detection and automatic isolation performance ensure the normal operation of the bus. The CAN bus transmission speed is fast and can reach a baud rate of 1M.
The CAN communication circuit of the ink fountain operating table control system is composed of the CAN bus controller integrated in the PIC18F8680 microcontroller, the CAN bus driver PCA82C250 and the high-speed photocoupler 6N137. Adding high-speed photoelectric coupling between the CAN bus controller and the bus driver chip can improve the reliability and anti-interference of the system.
The CAN drive circuit is shown in Figure 3, where the lines labeled CANTX and CANRX are connected to the CANTX pin and CANRX pin of the PIC microcontroller respectively.
2.3 Display driver and keyboard scanning circuit
The control system of the ink fountain operation table uses the BC7281 chip to scan the keyboard and drive the digital tube display. BC7281 is a dedicated control chip for 16-bit LED digital tube display and 64-key keyboard interface. Through the external shift register 74LS164 or 74LS595, BC7281 can control up to 16-bit digital tubes or 128 independent LED displays. Its drive output polarity and output timing are software controllable, and can be used with various external circuits. It is suitable for digital tubes of any size. Each digital tube of BC7281 can also be displayed independently in different decoding or non-decoding modes. Because it has a flashing switch control register and a flashing speed control register inside, the flashing properties and flashing frequency of each digital tube can be independently controlled. BC7281 can connect to a matrix keyboard with up to 64 keys (8x8), has an internal de-jitter function, and has 2 keyboard working modes to choose from. BC7281 uses a high-speed 2-wire interface to communicate with the MCU, which only occupies a small amount of I/O port resources and host time.
In this system, each display driver and keyboard scanning module is composed of a BC7281 chip and two 74LS174 shift registers to control three groups of buttons and display units. A total of 8 display driver and keyboard scanning modules are used in the system. The communication between BC7281 and PIC microcontroller adopts a 2-wire high-speed serial interface. The two lines are the data line DAT and the synchronous clock line CLK. DAT is a bidirectional data transmission line. BC7281 uses this line to receive data from the PIC microcontroller and send data to the PIC microcontroller. The DAT pin of BC7281 is an open-drain output structure. When using it, a pull-up resistor of about 20K? must be added to this line [5]. The CLK pin is the synchronous clock of the serial clock interface, which is controlled by the PIC microcontroller and is valid on the falling edge.
The KEY line of the BC7281 chip is directly connected to the pin of the PIC microcontroller. During normal operation, if a key is pressed, the KEY line outputs a low level. When the PIC microcontroller detects that the KEY line is at a low level, it reads the value from the key value latch in the BC7281 to determine the key press.
3 System Software Design
The serial communication between the PIC microcontroller and the BC7281 chip in the control system of the ink fountain operation table adopts software simulation. The data writing operation of the BC7281 chip is to write 2 bytes at a time. The first byte is the address information and the second byte is the data information. The data reading operation of BC7281 consists of a byte writing operation and a byte data reading operation. The address information is written when the byte is written, and the data in the corresponding address is read when the data is read. The BC7281 chip needs to be initialized before driving the digital tube display and monitoring the key, that is, the working mode control register (address 12H) of the BC7281 chip is set. According to the needs, this system sets the working mode control register of BC7281 to 0X8C during initialization, that is, the shift register mode is set to the normal shift register mode; the keyboard scan mode is set to the KEY level changes with the key situation, when there is a key, the KEY is low level, and when there is no key, the KEY is high level; the flashing mode is set to the extended mode; the display off mode is set to open; the scan enable mode is set to scan enable.
The main program control flow chart of the ink fountain operating table control system is shown in Figure 4:
After the system is powered on, it is first initialized. The system initialization includes initialization of each I/O port, interrupt initialization, CAN bus initialization, BC7281 chip initialization, communication test with other systems, reading the position of each ink key from the motor control system and displaying it, etc. Then the system enters a loop waiting state. If a key is pressed, the PIC microcontroller reads the key information from the key value latch of BC7281, determines the type of key based on the key information and performs corresponding processing, displays the new ink key position information on the console panel, and transmits it to other systems through the CAN bus. The system continues to enter a loop waiting state.
4 Conclusion
The ink fountain control system, which consists of the ink fountain console control system, the host computer system and the motor control system, has been successfully applied to the offset printing press produced by Beiren Group. Practical work shows that the production efficiency and production quality of the offset printing press have been greatly improved, and the ink fountain console control system has shown good performance. The entire system has a low cost and has a good market application prospect.
Previous article:Design of RS-232 to CAN Communication Adapter Card Based on PIC Microcontroller
Next article:How to increase the 8-bit A/D in PIC16C711 to 11-bit
Recommended ReadingLatest update time:2024-11-16 17:46
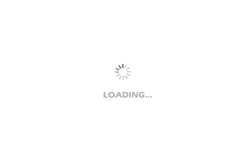
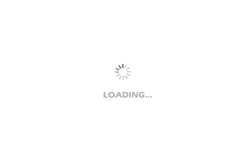
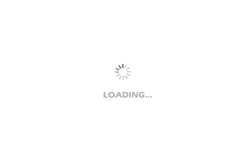
- Popular Resources
- Popular amplifiers
Professor at Beihang University, dedicated to promoting microcontrollers and embedded systems for over 20 years.
- Innolux's intelligent steer-by-wire solution makes cars smarter and safer
- 8051 MCU - Parity Check
- How to efficiently balance the sensitivity of tactile sensing interfaces
- What should I do if the servo motor shakes? What causes the servo motor to shake quickly?
- 【Brushless Motor】Analysis of three-phase BLDC motor and sharing of two popular development boards
- Midea Industrial Technology's subsidiaries Clou Electronics and Hekang New Energy jointly appeared at the Munich Battery Energy Storage Exhibition and Solar Energy Exhibition
- Guoxin Sichen | Application of ferroelectric memory PB85RS2MC in power battery management, with a capacity of 2M
- Analysis of common faults of frequency converter
- In a head-on competition with Qualcomm, what kind of cockpit products has Intel come up with?
- Dalian Rongke's all-vanadium liquid flow battery energy storage equipment industrialization project has entered the sprint stage before production
- Allegro MicroSystems Introduces Advanced Magnetic and Inductive Position Sensing Solutions at Electronica 2024
- Car key in the left hand, liveness detection radar in the right hand, UWB is imperative for cars!
- After a decade of rapid development, domestic CIS has entered the market
- Aegis Dagger Battery + Thor EM-i Super Hybrid, Geely New Energy has thrown out two "king bombs"
- A brief discussion on functional safety - fault, error, and failure
- In the smart car 2.0 cycle, these core industry chains are facing major opportunities!
- The United States and Japan are developing new batteries. CATL faces challenges? How should China's new energy battery industry respond?
- Murata launches high-precision 6-axis inertial sensor for automobiles
- Ford patents pre-charge alarm to help save costs and respond to emergencies
- New real-time microcontroller system from Texas Instruments enables smarter processing in automotive and industrial applications
- What happens if the input voltage of the window comparator is equal to the upper and lower limits?
- Banknote number recognition system based on ARM.pdf
- My knowledge of computers
- Sampling rate of MCU ADC
- [Sipeed LicheeRV 86 Panel Review] 7-Waft Graphical Interface Development Test (Part 2)
- I don't understand the principle of ultrasonic signal processing.
- Let’s talk about the first big event in 2019...
- Wifi controlled LED screen
- IIoT opens up more possibilities beyond the factory floor
- Recommended one: [Lingsheng] MCU code automatic generator (automatic programming tool)