This system mainly consists of three parts, namely the detection part, the control part and the actuator. Since the energy-saving device needs to detect a lot of analog quantities, such as the pressure in the gas tank, the position of the brake pedal, the vehicle speed, the piston running position and the accelerator pedal position, and some of them need to be monitored in real time, such as the pressure in the gas tank, etc., it needs to use multi-task execution to achieve this, and ordinary single-chip microcomputers cannot meet this requirement. Therefore, it is necessary to consider using ARM as the main control chip.
Due to various reasons, buses always repeat the process of acceleration-deceleration or parking-reacceleration. By installing this energy-saving device, when the car needs to brake, under the control of the main control unit, the huge kinetic energy of the car when driving can be converted into the potential energy of high-pressure gas through the air compressor and stored, so as to achieve the deceleration or parking of the car. When the car needs to start or accelerate, the stored high-pressure gas potential energy is used instead of fuel to drive the car, so as to achieve the recycling and reuse of the car energy and achieve the effect of energy saving. At the same time, since the energy consumption of the car is the largest when starting or accelerating, if the car is driven by fuel, the fuel will not burn completely at this time, the combustion effect is the worst, and the noise generated is the greatest.
1) System working principle
This system mainly consists of three parts, namely the detection part, the control part and the actuator. The detection part includes the detection of signals such as the pedal position sensor, the crankshaft position sensor, the compressor piston position sensor, the vehicle running speed sensor, and the gas tank pressure sensor. The actuator mainly includes a two-way controllable solenoid valve and an electromagnetic clutch. The control part is mainly composed of a control system composed of an ARM microprocessor and some peripheral circuits. This article mainly introduces the control part of the system. The function of this device is to change the kinetic energy of the car that should be consumed by friction during braking to the potential energy of the gas. When starting, the high-pressure gas potential energy stored in the gas tank during braking is used to drive the car to move. When the vehicle speed reaches a certain value, such as 20km/h, it switches to the mode driven by the car engine.
2) System hardware design
Since the energy-saving device needs to detect a lot of analog quantities, such as the pressure in the gas tank, the position of the brake pedal, the vehicle speed, the piston running position and the accelerator pedal position, and some of them need to be monitored in real time, such as the pressure in the gas tank, etc., it needs to use multi-task execution to achieve this, and ordinary single-chip microcomputers cannot meet this requirement. Therefore, it is necessary to select a suitable processor chip according to the actual situation, plus various data and program storage chips to form a minimum system. At the same time, add data acquisition, display, communication interface, control execution unit and power management module to form a complete control system. Since the CAN field bus is widely used in automobiles, in order to facilitate the connection with the control system of the car, a CAN bus interface is also added, thus forming the entire hardware system. The overall block diagram of the system is shown in Figure 1.
Figure 1 System Block Diagram
S3C44BOX Introduction
Since the design requires the system to collect signals on the vehicle and conduct real-time monitoring, the requirements for the main control module are relatively high. Therefore, the main control module should be a minimum system composed of a high-performance microprocessor as the core. According to the requirements of specific applications and the reflection of actual applications, Samsung's ARM chip S3C44BOX was selected, and its main performance is as follows:
Samsung's 16/32-bit RISC processor S3C44BOX provides a cost-effective and high-performance microcontroller solution for general-type applications. In order to reduce costs, S3C44BOX provides a wealth of built-in components, including: 8KB Cache, internal SRAM, LCD controller, 2-channel DART with automatic handshake, 4-channel DMA, system manager (chip select logic, FP/EDO/SDRAM controller), 5-channel timer with PWM function, I/O port, RTC, 8-channel 10-bit ADC, IIC-BUS interface, IIS-BUS interface, synchronous SIO interface and PLL multiplier.
The outstanding feature of S3C44BOX is its CPU core, which is a 16/32-bit ARM7TDMI RISC processor (66MHz) designed by ARM. The ARM7TDMI architecture features an integrated Thumb code compressor, ICE (In Circuit Emulator) breakpoint debugging support, and a 32-bit hardware multiplier.
Data acquisition unit
The function of the data acquisition unit is to collect and process the required analog signals and then send them to the processor for processing. In this unit, the core is the conditioning of analog signals. Since the system needs to collect data such as the pressure in the gas tank of the car, the position of the brake pedal, the vehicle speed, the clutch engagement position and the accelerator pedal position, multiple data acquisition channels are required. The data of each channel must be conditioned before it can be sent to the processor for processing. The signal acquisition channel block diagram of the acquisition unit is shown in Figure 2.
Figure 2 Signal acquisition channel
Control execution unit
The function of the control execution unit is mainly to receive the digital quantity sent by the processor, and after isolation and driving, send it to the actuator such as solenoid valve, relay, clutch, etc. to make the corresponding action. The functional block diagram is shown in Figure 3.
Figure 3 Control execution unit
This level is relatively simple, but in order to prevent external interference to the system, isolation must be used. The isolation device can be a common photoelectric device, and TLP521-1 is used in the system.
Data display module
In the design of the system, in order to monitor the collected data and make debugging more convenient and intuitive, a data display module is added. S3C44BOX integrates an LCD (Liquid Cristal Display) controller, which supports monochrome, 4-level, 16-level grayscale, and 256-color display on the LCD, and has strong versatility. The function of the LCD controller of S3C44BOX is to transfer the data in the cache to the external LCD driver and generate the necessary LCD control signals. The LCD controller can be programmed to support LCDs with different horizontal and vertical dot counts (640×480, 320×240, 160×160, etc.), different data line widths, different interface timings and refresh rates, and supports 4-bit dual scan, 4-bit single scan, 8-bit single scan modes, and supports horizontal/vertical scrolling to support larger screen displays (such as 1280×1280).
Since LCDs of different sizes have different numbers of vertical and horizontal pixels, data interfaces, data widths, interface times, and refresh rates, the LCD controller in the S3C44BOX can program the corresponding register values to accommodate different LCD display panels. The LCD controller logic block diagram is shown in Figure 4.
Figure 4 LCD controller logic block diagram
Power Module
In this system design, a single 9V power supply is supplied from the outside to the system, and 5.0V, 3.3V and 2.5V are obtained through three-terminal regulators AS1117-5.0, AS1117-3.3 and AS1117-2.5 respectively. The AS1117 series regulator can provide a maximum current of 800mA. Since the power consumption of this system is low and the maximum required current does not exceed 300mA, AS1117 is sufficient to meet the power supply needs of the system. The other two sets of ±15V power supplies are supplied by DC/DC converters. Considering that there are digital circuits and analog circuits in the system, the current of the digital circuit changes quickly, which is easy to generate pulse interference, thereby affecting the sampling accuracy of the analog signal, so the digital ground and analog ground should be separated.
Debug interface
S3C44BOX has a built-in JTAG test circuit, which makes debugging very convenient. JTAG is an international standard test protocol, mainly used for internal chip testing and system simulation and debugging. JTAG technology is an embedded debugging technology that encapsulates a special test circuit TAP (Test Access Port) inside the chip and tests internal nodes through a dedicated JTAG test tool. JTAG testing allows multiple devices to be connected in series through the JTAG interface to form a JTAG chain, which can test each device separately. The JTAG interface is also commonly used to implement ISP (In System Programmable) functions, such as programming Flash devices.
At present, there are two standards for JTAG interface connection, namely 14-pin interface and 20-pin interface. In this design, the 14-pin interface is used. This interface is mainly connected to the parallel port of the computer through the download circuit. Under the integrated development environment, the corresponding JTAG download agent software can be used for system debugging without a special emulator, which can reduce the development cost.
Communication unit
In the system design, considering the convenience of data transmission, downloading and debugging, a serial communication RS-232C interface is added. In addition, considering the convenience of system upgrade and the convenience of the popular automobile bus interface, a CAN field bus interface is added.
MAX232 is used in this system. MAX232 can realize the conversion between TTL level and RS-232 level. Since the device is very sensitive to power supply noise in practical applications, the VCC pin of MAX232 must be connected to the ground with a 0.1mF decoupling capacitor. In addition, in order to improve the anti-interference ability, four 10mF capacitors are added and connected to the output end of the internal power supply pin. The 7th and 8th pins of the MAX232 chip are connected to the 3rd and 2nd pins of the serial port respectively; the 9th and 10th pins are connected to the RXD and TXD pins of the processor to realize the connection with the processor.
Previous article:Hardware Design of Remote Video Monitoring System for Large Instruments and Equipment
Next article:Design of the test system for leakage protection device
Recommended ReadingLatest update time:2024-11-16 19:52
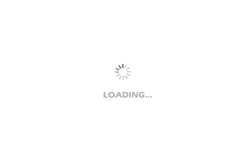
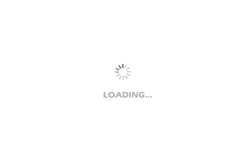
- Popular Resources
- Popular amplifiers
-
Semantic Segmentation for Autonomous Driving: Model Evaluation, Dataset Generation, Viewpoint Comparison, and Real-time Performance
-
Machine Learning and Embedded Computing in Advanced Driver Assistance Systems (ADAS)
-
Principle and maintenance of automobile on-board network system (CAN-BUS)
-
Intelligent program synthesis framework and key scientific problems for embedded software
Professor at Beihang University, dedicated to promoting microcontrollers and embedded systems for over 20 years.
- Innolux's intelligent steer-by-wire solution makes cars smarter and safer
- 8051 MCU - Parity Check
- How to efficiently balance the sensitivity of tactile sensing interfaces
- What should I do if the servo motor shakes? What causes the servo motor to shake quickly?
- 【Brushless Motor】Analysis of three-phase BLDC motor and sharing of two popular development boards
- Midea Industrial Technology's subsidiaries Clou Electronics and Hekang New Energy jointly appeared at the Munich Battery Energy Storage Exhibition and Solar Energy Exhibition
- Guoxin Sichen | Application of ferroelectric memory PB85RS2MC in power battery management, with a capacity of 2M
- Analysis of common faults of frequency converter
- In a head-on competition with Qualcomm, what kind of cockpit products has Intel come up with?
- Dalian Rongke's all-vanadium liquid flow battery energy storage equipment industrialization project has entered the sprint stage before production
- Allegro MicroSystems Introduces Advanced Magnetic and Inductive Position Sensing Solutions at Electronica 2024
- Car key in the left hand, liveness detection radar in the right hand, UWB is imperative for cars!
- After a decade of rapid development, domestic CIS has entered the market
- Aegis Dagger Battery + Thor EM-i Super Hybrid, Geely New Energy has thrown out two "king bombs"
- A brief discussion on functional safety - fault, error, and failure
- In the smart car 2.0 cycle, these core industry chains are facing major opportunities!
- The United States and Japan are developing new batteries. CATL faces challenges? How should China's new energy battery industry respond?
- Murata launches high-precision 6-axis inertial sensor for automobiles
- Ford patents pre-charge alarm to help save costs and respond to emergencies
- New real-time microcontroller system from Texas Instruments enables smarter processing in automotive and industrial applications
- How to choose the appropriate inductor and its parameters? | MPS invites you to learn practical tips and win gifts by commenting!
- I need help with soldering tips. Why does flux often splash out when I add tin to my soldering iron, burning my hands?
- What are the differences between RTU and DTU?
- Three key technologies of mobile robots
- FPGA implementation of terrestrial digital television symbol and carrier synchronization.pdf
- Classic: MSP430 microcontroller enters low power mode program code
- X-NUCLEO-IKS01A3 sensor test based on STM32F401RE development board 3D acceleration LIS2DW12 sensor test...
- ARM Embedded Learning Resource Sharing——"ARM Embedded Architecture and Interface Technology".pdf
- I would like to ask if the 8255A chip can only select one port at a time. After defining the address for the port, such as Q8255A XBYTE...
- Power supplies with digital control