As global warming continues, the automotive industry needs to produce more environmentally friendly and fuel-efficient cars. Demand for luxury cars with improved safety and comfort is increasing in developed countries, while there is also a strong demand for compact cars in rapidly developing countries such as China, India and Brazil.
In response to these demands, many automakers are promoting platform design for body control applications. Accordingly, microcontrollers (MCUs) that are easily integrated into these platforms are also needed. To meet these demands, Fujitsu Semiconductor has introduced the MB91520 series, enriching its 32-bit microcontroller FR81S family. The new series offers a variety of pin configurations and memory capacities, provides many peripheral functions for body control applications, and built-in cost reduction functions as standard features, thereby providing a most suitable platform solution. Dedicated timers for brushless DC motors and safety functions can also support AUTOSAR.
Fujitsu Semiconductor has launched the MB91520 series of the FR81S family lineup for body control with 60 new device models. This new automotive 32-bit microcontroller product line provides an optimally suited body control platform.
Extensive body control functions
The product lineup of this series is very rich. In order to meet the various needs of the automotive industry, Fujitsu Semiconductor's 60 models include a package range from 64 to 176 pins, flash memory from 320 to 1,088KB, and support for sub-clock (subcLOCk). Various peripheral functions help load body control functions mainly for body control modules (BCM). This lineup is more powerful than the FR60 family MB91460 series for body control. Compared with the conventional FR60 family, the CPU performance of the new products has increased by more than 30% due to improved pipeline processing and internal bus operation.
In addition, the new MCU can access flash memory without waiting time, even when running at 80MHz. Other high-performance functions, such as a dedicated floating-point operation (FPU) embedded unit, support automatic code creation in the model library design phase. The complete product lineup supports a variety of application development.
The new products support a range of peripheral functions suitable for body control applications, such as a multi-function serial interface that allows flexible connection to a variety of external devices, a 12-bit A/D converter that enables advanced sensor input, and a controller area network (CAN) that supports up to 128 messages.
The device's multifunctional serial interface can flexibly connect various external devices to achieve a wide range of body control communication methods. In order to flexibly support these communication systems, the product provides a multifunctional serial interface, as shown in Figure 1. UART , SPI, LIN and I2C are software selectable for each channel. Up to 12 channels can be loaded in the industry, which is the highest level in the industry.
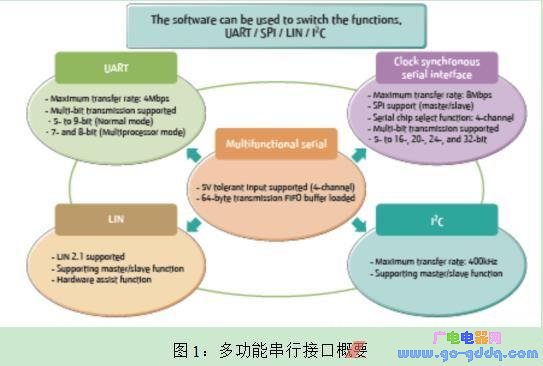
A/D converter supports advanced sensor input
The high-resolution 12-bit A/D converter loaded on the product can support sensors and peripheral components, providing improved technical advantages. Since two A/D converter units are loaded, simultaneous conversion can be achieved. As shown in Figure 2(a), the range comparison function can detect a given range level integrated as a hardware function. The highest and lowest thresholds compared with the A/D conversion value can be set in advance. When the level is within or outside the predetermined range, the function automatically detects, thereby reducing the software load. Moreover, as shown in Figure 2(b), continuous comparison can be achieved.
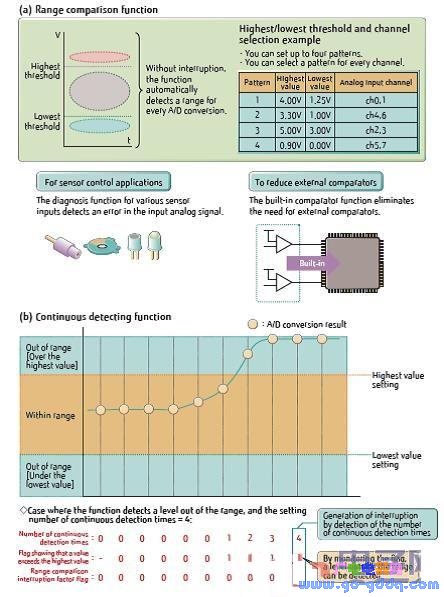
Figure 2: Overview of the A/D converter range comparison function
Other advanced features
Many new cars are equipped with electronic control units (ECUs) connected via CAN. Networks are becoming larger due to the increase in the number of nodes and other factors. Fujitsu Semiconductor's previous 32-bit microcontrollers typically had a cache of 32 messages. The new product's cache can hold up to 128 messages, making it possible to support systems with more nodes. The supported CAN protocol is Version 2.0A/B.
In addition, the built-in E2PROM, watchdog timer IC and reset IC and other external components can reduce the number of components and board mounting space, reducing the total system cost. Since the product has 64KB data flash (working flash) in addition to the program flash, no external E2PROM is required. Moreover, the data flash embedded in the microcontroller prevents information leaks. The built-in CR oscillation circuit system operates the hardware watchdog timer independently of the main clock. No external watchdog timer IC is required.
Since this product has a low voltage function that monitors the external power supply, there is no need to load an external reset IC on the board. 11 voltage levels can be selected by software. The waveform generator can be used as a dedicated timer to support brushless DC motors, and it can output a three-phase waveform. In order to support brushless motor operation, a dead time setting function and an emergency stop function are required.
Figure 3 describes the diagnostic functions of the product, such as the CPU self-diagnostic program, bus error detection function, RAM self-diagnostic function, memory error detection and correction (ECC), and I/O port protection function.
Functional Safety for Microcontrollers
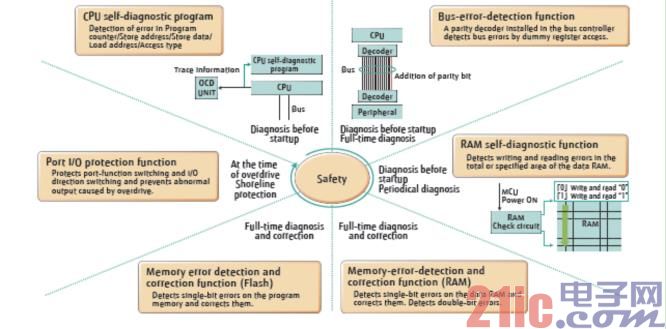
Figure 3: MB91520 Series Diagnostic Functions
Applications
Based on the switches and sensors installed in the vehicle and the information obtained from other ECUs, BCM controls the interior lighting, turn signals, wipers, door locks, side mirrors and other items. The product has up to 12 channels of multi-function serial interface and three-channel CAN, which can flexibly connect multiple devices and ECUs. The A/D converter provides up to 48 channels to support various input processing from sensors. Figure 4 describes the application example of BCM.
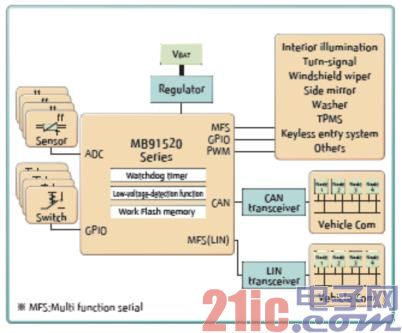
Figure 4: Application example of BCM
As an example of BCM application, electric compressors have recently been used in car air conditioners. To maintain comfort inside the car, the temperature must be accurately controlled. Control is achieved using a waveform generator to control the brushless DC motor, which in turn operates the air conditioner's electric compressor. Figure 5 describes an example of an electric compressor application.
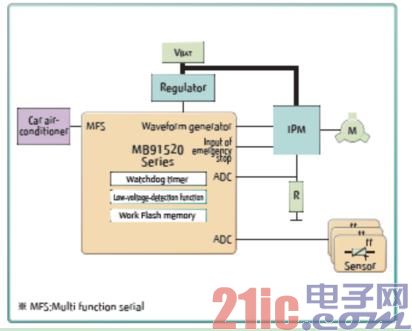
Figure 5: Application example of electric compressor
In summary, the MB91520 series is compatible with AUTOSAR R3.1/4.0, and can use a seamless integrated development environment for 16-bit and 32-bit microcontrollers, as well as an emulator (MB2100-01-E) that supports single-line on-chip debugging. All chips in the new product line are equipped with program flash and separate data storage flash. This reduces the need for external E2PROM and simplifies system development, making it suitable for peripheral functions in automotive ECU systems.
Previous article:Universal programmer design for Freescale HCS12 series MCU
Next article:Design of window opener controller based on single chip microcomputer STC15F104E
Professor at Beihang University, dedicated to promoting microcontrollers and embedded systems for over 20 years.
- Innolux's intelligent steer-by-wire solution makes cars smarter and safer
- 8051 MCU - Parity Check
- How to efficiently balance the sensitivity of tactile sensing interfaces
- What should I do if the servo motor shakes? What causes the servo motor to shake quickly?
- 【Brushless Motor】Analysis of three-phase BLDC motor and sharing of two popular development boards
- Midea Industrial Technology's subsidiaries Clou Electronics and Hekang New Energy jointly appeared at the Munich Battery Energy Storage Exhibition and Solar Energy Exhibition
- Guoxin Sichen | Application of ferroelectric memory PB85RS2MC in power battery management, with a capacity of 2M
- Analysis of common faults of frequency converter
- In a head-on competition with Qualcomm, what kind of cockpit products has Intel come up with?
- Dalian Rongke's all-vanadium liquid flow battery energy storage equipment industrialization project has entered the sprint stage before production
- Allegro MicroSystems Introduces Advanced Magnetic and Inductive Position Sensing Solutions at Electronica 2024
- Car key in the left hand, liveness detection radar in the right hand, UWB is imperative for cars!
- After a decade of rapid development, domestic CIS has entered the market
- Aegis Dagger Battery + Thor EM-i Super Hybrid, Geely New Energy has thrown out two "king bombs"
- A brief discussion on functional safety - fault, error, and failure
- In the smart car 2.0 cycle, these core industry chains are facing major opportunities!
- The United States and Japan are developing new batteries. CATL faces challenges? How should China's new energy battery industry respond?
- Murata launches high-precision 6-axis inertial sensor for automobiles
- Ford patents pre-charge alarm to help save costs and respond to emergencies
- New real-time microcontroller system from Texas Instruments enables smarter processing in automotive and industrial applications
- LIS2MDL array magnet displacement data acquisition for magnetic nail navigation AGV
- Domestic Bluetooth BLE chip
- EEWORLD University Hall----Digital Image Processing (MATLAB) Shandong University (Jiang Mingyan)
- [RT-Thread reading notes] First acquaintance
- Support jesd204b protocol high-speed DAC chip AD9144-FMC-EBZ configuration notes
- Analog Dialogue Collection
- How to concatenate 8 sbits of data into one? Bitwise operation? How to implement it?
- Ask a question about bit fields
- There is a circuit for fast shut-off of MOS tube. Does anyone know the specific working principle? How to shut down quickly?
- What is the difference between using * and ? in the day of the week in cron expressions? I checked some information but it's not clear.