With the rise of smart grid research and the continuous improvement of urban and rural power grid structures, higher requirements are put forward for distribution network automation. Feeder Terminal Unit (FTU) with selectivity, rapid fault removal and fault self-healing ability has become a research hotspot. In the reference, based on the digital processor DSP, the reference used ARM and DSP to develop and design feeder automation terminal devices.
The above references use different processors and different technologies to design distribution network feeder terminals, but the designed devices have problems such as high cost, low configuration flexibility and difficulty in installation and wiring. ARM microprocessors have strong processing capabilities, fast computing speed, high performance, low power consumption, low cost and small size, and are the first choice for core control devices of feeder terminals. Internet of Things technology is an important part of the new generation of information technology and has broad application prospects. It can realize wireless communication of feeder terminal data. Solar energy, a new energy source, is pollution-free, renewable and low-cost. The use of solar energy is an inevitable trend.
1 FTU overall design scheme
The feeder automation system is an integrated system for remote real-time monitoring, coordination and control of equipment on distribution lines. It consists of three parts: feeder terminal (FTU), monitoring substation and monitoring center. Its basic structure is shown in Figure 1.
The FTU on the monitoring line is responsible for collecting power information of the distribution line, monitoring and controlling the pole-mounted switches, and aggregating the information of the distribution line and the pole-mounted switches to the monitoring substation through the radio frequency network. The monitoring substation plays the role of data forwarding and uses the DTU function of the 3G router to achieve remote transmission.
The power distribution master station receives the information data packets collected by the FTU terminal in real time, and unpacks, verifies, dynamically displays, stores, and determines faults of the real-time data packets, and realizes control functions such as the closing of switches on the remote control column of the monitoring center.
2 Feeder terminal structure design
The main tasks of the feeder terminal FTU are to collect power information of the distribution line, monitor the status of the switch on the control pole, send real-time information to the monitoring substation through the radio frequency network, and receive and process the control commands sent by the host computer. In view of the above requirements, this terminal should have the following functions: real-time power information collection and monitoring function, pole switch control and status monitoring, data processing and storage function, wireless communication function. According to the above functional analysis, combined with the reliability and scalability requirements of the device itself, the hardware design adopts a configurable modular design, in which the hardware structure includes CPU control module, power collection module, switch input/output module, wireless communication module, data storage module and power supply module, etc. Its structure is shown in Figure 2.
2.1 Dual power switchable power module
FTU adopts dual power supply mode. When the system is operating normally, it obtains AC220 V through PT to provide 24 V and 5 V power for the system; when the system fails, it automatically switches to the backup power supply mode.
The backup power supply of the FTU terminal uses a solar-charged lithium battery. By connecting two 12 V batteries in series to obtain a 24 V DC working power supply (the operating voltage of the pole switch), when the power system fails, it can provide power for the FTU terminal and ensure the energy for at least three opening and closing operations of the pole switch, thereby ensuring the reliability of the power supply of the power system. The power supply voltage of the feeder terminal is DC5 V. The DC24 V voltage is converted to ±5 V by the DC/DC modules of WD15-24D05C1 and WD15-24S05C1 to power the CPU control module and other modules. The power conversion circuit is shown in Figure 3.
2.2 Real-time power and switch status acquisition module
The power acquisition module uses the three-phase power metering chip ATT7022B from Actions. ATT7022B integrates 6-way second-order sigma delta, ADC, reference voltage circuit, all power, energy, effective value, power factor and frequency measurement digital signal processing circuits, etc. It can measure the active, reactive and apparent power of each phase and the combined phase, and can also measure the effective value of each phase current, voltage, power factor, phase angle, frequency and other parameters. ATT7022B provides an SPI interface to facilitate the transmission of metering parameters and calibration parameters with the CPU control module. All metering parameters can be read out through the SPI interface.
In fact, the FTU power collection is completed through ATT7022B, and the ARM chip is responsible for various peripheral tasks such as communication interface, human-machine interface and I/O control, which can reduce the complexity of software design and effectively shorten the calculation time of digital filtering and Fourier transform. In addition, S3C2440A can support the embedded operating system Linux, converting various communication functions, human-machine interface functions and I/O control functions into multiple tasks running concurrently in real time, and Linux performs task management and state switching, which not only improves the real-time performance of the software system, but also can effectively manage various information collected by ARM, meeting the distribution system's demand for the diversification and intelligence of FTU functions.
The function of the pole switch status signal acquisition module is to send various pole switch status signals to the CPU module through the photoelectric isolation circuit and the parallel interface circuit. The status information of the power distribution network mainly covers the protection signal, the action status of the automatic device, the position status of the isolation switch, and the operation status of the system and equipment. The above status information can be converted into the contact position signal of the auxiliary contact or relay. Therefore, as long as the contact switch position information is collected, the acquisition of the pole switch status signal can be realized.
The pole switch status signal acquisition module and the control signal output module are designed separately, and each module has an independent circuit. In order to ensure the accuracy and reliability of the collected pole switch status information, photoelectric isolation elements are added to the circuit to take necessary isolation measures and prevent interference signals from entering the monitoring terminal through the acquisition module. The pole switch status acquisition circuit is shown in Figure 4.
2.3 Auxiliary Hardware Components
The remote signal input and remote control output circuits of the feeder automation system mainly complete the input/output of status signals, including the opening and closing of the pole switch, remote/local conditions, whether the communication is normal, the battery input status, the external power failure, and the completion of energy storage, etc. The main control chip S3C2440 has a large number of interface resources. After photoelectric isolation measures, it can realize 16-channel digital input and 16-channel digital output to meet the needs of remote signal and remote control.
The storage part mainly records the current, voltage and the opening and closing status of the pole switch when a fault occurs in the distribution line.
3 Feeder Monitoring Terminal Software Design
According to the functions that FTU needs to realize, combined with the hardware circuit, the lower computer program is written, and the flow of the lower computer program is shown in Figure 5. Two interrupts are set in the program, one is the serial port receiving interrupt, which is used to receive the command word from the control center, and the other is the timer interrupt, which is used to query the status information of the switch at a fixed time.
The FTU system collects power through ATT7022B, and ATT7022B needs to be calibrated. The calibration process is shown in Figure 6.
In order to ensure the accuracy of the A/B/C three-phase current vector and effective value parameters, when correcting the current effective value, the current effective value of ATT7022B is corrected to about N×Ib. After the external MCU reads the current effective value from ATT7022B, it only needs to divide it by N. The method to determine the true value N is to make N×Ib as close to 60 A as possible.
4 Monitoring center system management software
The monitoring center system management software is developed in C# based on the .NET framework, following modular standards, based on the realization of functions, supplemented by principles such as easy upgrade and maintenance, operation, and a simple and elegant interface. The main functions of the monitoring center system management software are as follows:
◆TCP protocol remote communication;
◆FTU interface design and configuration;
◆Real-time data reception and processing;
◆Remote control function;
◆FTU fault handling;
◆Other parameter settings and storage.
The system adopts C/S structure and is based on Internet of Things technology. The feeder monitoring terminal in a region is used as the client, and the monitoring center is used as the server. Two-way communication is achieved through sockets. The distribution of FTUs is simulated, and the GDI+ drawing tool is used to implement the interface design and configuration of FTUs. The monitoring center dynamically displays the acquired power and switch status information and stores it in real time. For abnormal power information, the system determines the fault type and issues an alarm.
In addition, the system management software also realizes functions such as automatic time calibration, configuration of FTU parameters, query of historical data, drawing of curve graphs and printing of reports.
5 System Testing and Application Effects
Data collection and communication tests were performed on the feeder terminal to ensure the reliability of the hardware and software design of the product. With the help of engineers from Suzhou xxxx Electric Company, a 10 kV high voltage was generated through a 10 kV inverter and connected to the power collection port through a 10:0.1 PT; since this device has no load, the current test in the experiment uses a current trolley to implement a simulation test. Two FTU terminals were installed on site, and the test results showed that the device has fast data collection speed and high accuracy, and its collected data is basically consistent with the actual measurement results.
The normal monitoring interface of the system management software is shown in Figure 7. Since only two-phase voltage is connected during the test, the monitoring interface alarms, which is in line with expectations.
Conclusion
The feeder terminal based on ARM processor developed in this paper has the functions of real-time power collection, processing, storage, switch status monitoring and control, power supply voltage monitoring, wireless communication, etc. The wireless network data transmission technology is adopted to get rid of the wired trouble, save the cost of data transmission, and improve the flexibility and anti-interference of the equipment; solar power is used to avoid the FTU monitoring terminal from being unable to work due to line faults; and the improved fault location algorithm is discussed. The ARM-based FTU can well meet the real-time, reliable and intelligent requirements of distribution network automation.
Previous article:STM32 startup process startup file analysis
Next article:Design of automatic measurement circuit for microwave frequency controlled by stepping motor
Recommended ReadingLatest update time:2024-11-16 16:31
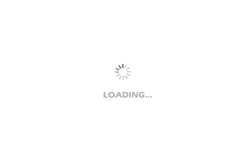
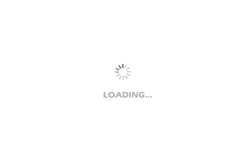
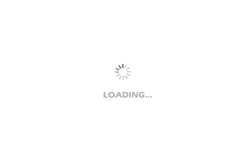
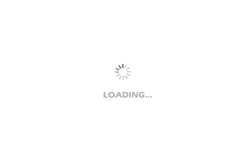
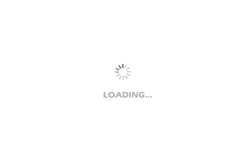
- Popular Resources
- Popular amplifiers
-
Practical Deep Neural Networks on Mobile Platforms: Principles, Architecture, and Optimization
-
ARM Embedded System Principles and Applications (Wang Xiaofeng)
-
ARM Cortex-M4+Wi-Fi MCU Application Guide (Embedded Technology and Application Series) (Guo Shujun)
-
CVPR 2023 Paper Summary: Vision Applications and Systems
Professor at Beihang University, dedicated to promoting microcontrollers and embedded systems for over 20 years.
- Innolux's intelligent steer-by-wire solution makes cars smarter and safer
- 8051 MCU - Parity Check
- How to efficiently balance the sensitivity of tactile sensing interfaces
- What should I do if the servo motor shakes? What causes the servo motor to shake quickly?
- 【Brushless Motor】Analysis of three-phase BLDC motor and sharing of two popular development boards
- Midea Industrial Technology's subsidiaries Clou Electronics and Hekang New Energy jointly appeared at the Munich Battery Energy Storage Exhibition and Solar Energy Exhibition
- Guoxin Sichen | Application of ferroelectric memory PB85RS2MC in power battery management, with a capacity of 2M
- Analysis of common faults of frequency converter
- In a head-on competition with Qualcomm, what kind of cockpit products has Intel come up with?
- Dalian Rongke's all-vanadium liquid flow battery energy storage equipment industrialization project has entered the sprint stage before production
- Allegro MicroSystems Introduces Advanced Magnetic and Inductive Position Sensing Solutions at Electronica 2024
- Car key in the left hand, liveness detection radar in the right hand, UWB is imperative for cars!
- After a decade of rapid development, domestic CIS has entered the market
- Aegis Dagger Battery + Thor EM-i Super Hybrid, Geely New Energy has thrown out two "king bombs"
- A brief discussion on functional safety - fault, error, and failure
- In the smart car 2.0 cycle, these core industry chains are facing major opportunities!
- The United States and Japan are developing new batteries. CATL faces challenges? How should China's new energy battery industry respond?
- Murata launches high-precision 6-axis inertial sensor for automobiles
- Ford patents pre-charge alarm to help save costs and respond to emergencies
- New real-time microcontroller system from Texas Instruments enables smarter processing in automotive and industrial applications
- Google Protobuf 库
- EEWORLD University ---- Wildfire LwIP Application Development Practical Guide
- Compile QT5.6.0
- How to consider and design ESD of RF modules?
- There seems to be something wrong with microPython's regular expression library ure. The matching result of the "*" wildcard is incorrect.
- Regarding IIC communication PCB routing, do I need differential routing? I am currently routing in a dispersed manner? Maximum frequency of 400K
- Decoupling Basics
- Communicate with device over wifi (Android)
- 【RPi Pico】Install MicroPython
- Can anyone recommend the DATASHEE for ATMLU308? I have searched on Baidu but couldn't find it. Thank you.