The signal processing of modern sonar is basically undertaken by the signal processor. Since the signal processor has perfect self-test and fault isolation capabilities, the bottleneck of rapid testing of sonar equipment lies mainly in the test of the receiver. The actual sonar receiver generally has several receiving channels. For a single receiving channel, it is necessary to have a flat amplitude-frequency characteristic and a linear phase characteristic within the working frequency band, otherwise the signal cannot be transmitted without distortion; for all channels, their amplitude and phase characteristics should be consistent, otherwise the subsequent signal processing will be difficult to achieve the ideal effect. Testing the sonar receiver can not only understand its working status, but also compensate for deviations in some receiving channels, thereby improving the detection performance of the sonar equipment. Therefore, it is necessary to develop a dedicated sonar receiver test equipment. The design of the signal source is an indispensable link in the development process. According to the characteristics of sonar receiver testing, this paper designs a dedicated signal source for sonar receiver testing.
1 System Design
The system block diagram of the designed signal source for sonar receiver testing is shown in Figure 1. It is divided into the frequency synthesis part controlled by the single-chip microcomputer AD9850; the bandpass filter part composed of MAX275; the signal amplitude adjustment part and the host computer part controlled by the single-chip microcomputer AD7111. Among them, the function of the host computer is mainly to set and display the frequency, initial phase and amplitude of the test signal.

2 Hardware Design
2.1 Frequency Synthesis Module
The circuit of the frequency synthesis module is shown in Figure 2. Among them, AD9850 is a high-stability direct digital frequency synthesis device, which integrates the input control word register, binary full adder, phase register, sine lookup table, 10-bit high-speed DAC and high-speed comparator. Every time a reference clock comes, the phase register increases with a step size of M (the size of M is determined by the frequency control word). After its output is added to the phase control word, the corresponding digital amplitude information is obtained by querying the sine table, and then output through the DAC to obtain the sine signal of the required frequency. Since the 430 microcontroller has rich digital I/O, a parallel interface is used. When the microcontroller programs AD9850, the FQ_UD signal is first turned low, and then the 8-bit control word is written into the input register of AD9850 at the rising edge of W_CLK. After 5 clock cycles, a total of 40-bit control words are written. Finally, the FQ_UD signal is turned high, and the 40-bit control word is loaded into the function register at the same time, and AD9850 can output a sinusoidal signal. This design uses a 12 MHz crystal oscillator, and the frequency control word of AD9850 is 32 bits, so the frequency resolution (unit: Hz) is:

Let W be the frequency control word of AD9850, and from fo=W△f=W×12×106/232, we get:

According to the test needs, the microcontroller writes the frequency control word to AD9850 according to formula (2) to generate a sinusoidal signal of the required frequency.
2.2 Bandpass filter module
Due to phase accumulation rounding, amplitude quantization and DAC non-ideal characteristics, the noise of the direct output signal of the DDS chip is relatively large, and the sonar receiver test (such as frequency characteristic test, etc.) requires a sine signal with a pure spectrum, so the signal output by the DDS chip must be filtered. According to the operating frequency range of the receiver to be tested, the filter can be designed as a low-pass or band-pass form. The signal source designed in this paper is used to test a certain type of synthetic aperture sonar receiver. The operating frequency of the receiver is 100-200 kHz, so the filter is designed as a band-pass form, and the chip selected is MAX275. MAX275 is a continuous-time active filter chip launched by MAXIM. It contains two independent cascaded 2nd-order filter units, which can achieve low-pass or band-pass output of 100 Hz to 300 kHz. The filter designed with MAX275 has the characteristics of simple circuit (only external resistors are required, no external capacitors are required) and convenient design (MAXIM provides free design software, no complex calculations are required). The 12th-order Chebyshev bandpass filter designed in this paper is shown in Figure 3. The center frequency is 150 kHz, the bandwidth is 240 kHz, the transition band is 25 kHz, the maximum attenuation in the passband is 1 dB, and the minimum attenuation in the stopband is 20 dB. The resistance values in Figure 3 are generated by the design software provided by MAXIM. After the designer inputs the function and performance indicators of the filter, the software can automatically calculate the resistance value of the external resistor after a series of optimizations, and can observe and print the frequency characteristics of the filter. It is actually observed that the attenuation of the filter is -50 dB within 5 kHz and beyond 300 kHz.

2.3 Amplitude adjustment module
Since the echo of the short-range target is strong and the echo of the long-range target is weak when the sonar is working, in order to compensate for the propagation loss and obtain a uniform sonar image in the near and far fields, TVG (Time Variable Gain) control is generally adopted. A larger TVG control voltage is applied to the echo of the farther target, and the gain of the receiver becomes larger, which makes the dynamic range of the receiver gain very large. The signal source designed in this paper is used to test a certain type of synthetic aperture sonar receiver. The gain of the receiver is 0 to 120 dB, so the amplitude of the signal source applied to its test should also vary within the range of 120 dB, otherwise the output of the receiver will be saturated. [page]
This article uses AD7111 to adjust the signal amplitude. AD7111 is a logarithmic D/A converter (LOGDAC) launched by AD. It controls the attenuation of the input signal Vi through 8-bit input data, and the attenuation range is 0 to -88.5 dB. The transfer function of the circuit is: the

signal amplitude VoAD9850 output from AD9850 = Io × Ro = 10.24 × 100 = 1.024 V, the attenuation of the bandpass filter in the passband is less than 1 dB, and when the maximum gain of the sonar receiver to be tested is 120 dB, the sine output of the bandpass filter needs to be attenuated by 120 dB, so that after the test signal is added to the receiver, the signal output by the receiver is still around 1 V and will not be saturated. The single-chip AD7111 can attenuate the input signal by 88.5 dB at most, but as the attenuation increases, the error also increases. Therefore, this paper uses two AD7111s, each of which can attenuate the signal by 60 dB at most. Both AD7111s work in the linear attenuation area, thus ensuring that the entire amplitude adjustment circuit has a small error. The specific circuit is shown

in Figure 4. R1 and R3 in Figure 4 are used to adjust the precise 0 dB, that is, when the single-chip microcomputer controls D7~D0 to be low, adjust R1 and R3 to make the input and output signal amplitudes of the amplitude adjustment circuit equal. The two-stage attenuation circuit should be adjusted separately to reduce the error; the AD711 in Figure 4 is an op amp with an input bias current of less than 10 nA, which can be replaced by other similar op amps with excellent performance; in addition, since the attenuation resolution of less than 1.5 dB is not required, D3~D0 of the AD7111 in Figure 4 are grounded. Since the attenuated signal may be very weak, optical coupling is adopted for the control signal of AD7111, and shielding measures are taken for the entire amplitude adjustment circuit.
3 Software Design
The software is mainly used to control the DDS chip to generate a signal of a certain frequency and control the AD7111 to adjust the signal amplitude. The program flow is shown in Figure 5.

The working process of the lower computer is: after the initialization is completed, it waits for the interrupt of the upper computer. After the interrupt occurs, it receives the signal frequency and amplitude control word, and writes the control word to AD9850 and AD7111 respectively, and then continues to wait for the interrupt of the upper computer.
4 Test method The
designed signal source is connected to the AWA5810A measurement amplifier produced by Hangzhou Aihua Instrument Co., Ltd., and the signal source is controlled to output a 30 kHz sine wave. Then the signal amplitude of the signal source output is gradually attenuated, and then the measurement amplifier is used to measure its amplitude. The experiment shows that when the signal output by the signal source is attenuated by 90 dB and the gain of the measurement amplifier is adjusted to 90 dB, the measurement amplifier still indicates 1.0 V, which shows that the signal source can output at least 32.4 μV of sinusoidal signal.
5 Conclusion
A design method of a signal source for sonar receiver testing is introduced in detail and tested. The experiment shows that the signal source can accurately control the frequency and amplitude of the output signal and can make the amplitude of the output signal reach 10μV level. The designed signal source can be extended to a universal signal source for sonar receiver testing, so it has a wide range of applications.
Previous article:LCD1602 clock experimental routine based on 51 single chip microcomputer
Next article:Modular independent photovoltaic power generation control system based on controller
Recommended ReadingLatest update time:2024-11-16 22:01
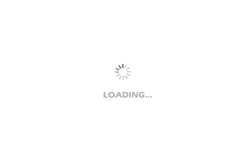
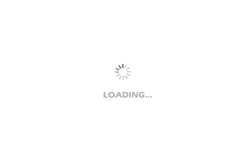
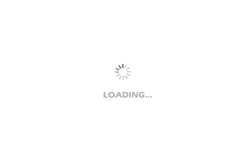
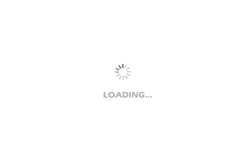
Professor at Beihang University, dedicated to promoting microcontrollers and embedded systems for over 20 years.
- Innolux's intelligent steer-by-wire solution makes cars smarter and safer
- 8051 MCU - Parity Check
- How to efficiently balance the sensitivity of tactile sensing interfaces
- What should I do if the servo motor shakes? What causes the servo motor to shake quickly?
- 【Brushless Motor】Analysis of three-phase BLDC motor and sharing of two popular development boards
- Midea Industrial Technology's subsidiaries Clou Electronics and Hekang New Energy jointly appeared at the Munich Battery Energy Storage Exhibition and Solar Energy Exhibition
- Guoxin Sichen | Application of ferroelectric memory PB85RS2MC in power battery management, with a capacity of 2M
- Analysis of common faults of frequency converter
- In a head-on competition with Qualcomm, what kind of cockpit products has Intel come up with?
- Dalian Rongke's all-vanadium liquid flow battery energy storage equipment industrialization project has entered the sprint stage before production
- Allegro MicroSystems Introduces Advanced Magnetic and Inductive Position Sensing Solutions at Electronica 2024
- Car key in the left hand, liveness detection radar in the right hand, UWB is imperative for cars!
- After a decade of rapid development, domestic CIS has entered the market
- Aegis Dagger Battery + Thor EM-i Super Hybrid, Geely New Energy has thrown out two "king bombs"
- A brief discussion on functional safety - fault, error, and failure
- In the smart car 2.0 cycle, these core industry chains are facing major opportunities!
- The United States and Japan are developing new batteries. CATL faces challenges? How should China's new energy battery industry respond?
- Murata launches high-precision 6-axis inertial sensor for automobiles
- Ford patents pre-charge alarm to help save costs and respond to emergencies
- New real-time microcontroller system from Texas Instruments enables smarter processing in automotive and industrial applications
- Application of Hall sensor and current ripple technology in electric window anti-pinch
- There is no one to teach me how to learn FPGA. Can I learn it just by watching tutorials?
- Brushed DC and brushless DC driver chips
- Analysis of the application of NTC thermistor in power circuit
- Use LabVIEW to remotely control the Raspberry Pi via WiFi~
- DC-DC boost to 5V abnormal
- Analysis of the working principles of seven triode collector DC circuits 6
- TI's C6000 series DSP, implementation of flashboot
- What is PENA in the technical manual spnu515c.pdf of TMS570LS1227? ? ?
- Maximizing Thermistor Accuracy Using Common Microcontroller Design Techniques