introduction
The safety support of the roadway plays an important role in the safe production of coal mines, and it is also a difficult point in the safe production of coal mines. The key to the safe support of the roadway is to grasp the crushing state of the loose zone of the rock in real time.
After the tunnel is excavated, the stress equilibrium state of the original rock is destroyed, resulting in: first, the radial stress around the tunnel drops to zero, and the strength of the surrounding rock decreases significantly; second, stress concentration occurs in the surrounding rock. When this stress exceeds the strength of the surrounding rock, the fracture zone formed in the surrounding rock around the tunnel is the surrounding rock loosening zone. Its physical state is manifested as an increase in cracks and a decrease in the stress level of the rock mass. The loosening zone test is to test the new destructive cracks and their distribution range after the tunnel is opened. The interface position between new cracks and no cracks in the surrounding rock is the boundary of the loosening zone. The reference introduces the corresponding test methods based on the detection principle of the loosening zone test, including ultrasonic detection method, multi-point displacement measurement method and geological radar detection method. The reference proposes a surrounding rock loosening zone test method based on seismic waves based on the principle that the propagation speed of seismic waves in rock layers of different states is different.
In view of the simplicity, ease of operation and non-destructiveness of ultrasonic testing, this paper proposes a surrounding rock crack monitoring system based on ultrasonic waves. This system, combined with the mature dry hole test method, can conveniently detect the information of the surrounding rock loosening zone in real time, provide information in time for the safe support of the tunnel, and ensure the safety of mine production.
1 Principle of ultrasonic detection of surrounding rock loose zone
1.1 The form of ultrasonic waves in surrounding rocks
When ultrasonic waves enter the rock mass in a vertical direction, longitudinal waves, transverse waves, and surface waves are generated simultaneously. According to acoustic theory, in an infinite medium, the sound speeds of these three waves are:
In the formula, Vl, Vs, Vr are the sound velocities of longitudinal wave, transverse wave and surface wave respectively, E is Young's modulus, ρ is density, and μ is Poisson's ratio. Usually, in solids, Vs is about 1/2 of V1, and Vr is about 0.9 times of Vs. However, since the energy of longitudinal and transverse waves propagating along the surface of the rock mass is very small, while the energy of the surface wave is highly concentrated (the energy of the surface wave is almost entirely concentrated within a wavelength depth of the surface layer of the object), the amplitude of the surface wave reaching the receiving transducer at a close distance is much greater than that of the longitudinal and transverse waves. In this paper, the state of the surrounding rock will be analyzed by collecting the surface wave information of ultrasonic waves propagating in the rock.
In addition, the propagation speed of ultrasound is also related to the structure and stress state of the rock mass. The sound wave velocity decreases with the development of medium cracks, reduced density, and increased acoustic impedance, and increases with increased stress and density. After the tunnel is excavated, the surrounding rock stress will be redistributed in three stress zones: stress concentration zone, original rock stress zone, and stress reduction zone. The characteristics of these three zones are: the stress reduction zone (loosening zone of surrounding rock) has more cracks, reduced stress, and the sound velocity is lower than the normal wave velocity; the stress concentration zone has higher stress, compacted cracks, and higher sound velocity than the normal wave velocity; the stress in the original rock stress zone is close to the original stress state, and the wave velocity is close to the normal wave velocity. This paper uses the change in the propagation velocity of ultrasound within a certain depth range of the tunnel surrounding rock to determine the loosening range of the surrounding rock.
1.2 Ultrasonic wave velocity test scheme
According to the number of ultrasonic transmitting/receiving transducers, the commonly used speed measurement schemes are single-transmitting and single-receiving and single-transmitting and dual-receiving, as shown in Figure 1. These transmitting/receiving transducers are placed in pre-drilled surrounding rock holes at a fixed distance. The single-transmitting and single-receiving scheme calculates the time from the transmitting end to the receiving end, and then determines the propagation speed of the ultrasonic wave in the surrounding rock at the test location based on the distance between the two ends. The single-transmitting and dual-receiving scheme uses the time difference between the first wave of the transmitting end passing through the two receiving ends and the distance between the two receiving ends to determine the propagation speed of the ultrasonic wave.
The propagation speed of ultrasound is:
Both single-shot and single-receive and single-shot and dual-receive require continuous changes in the test depth to complete the test. This paper combines the single-shot and single-receive and single-shot and dual-receive methods and proposes a single-shot and multiple-receive test scheme using equation (4), as shown in Figure 2. This structure does not require multiple moves of the tester and can even be fixed to the rock formation to achieve real-time monitoring.
2 Hardware design of surrounding rock loosening zone monitoring system
The hardware structure block diagram of the surrounding rock loosening zone monitoring system is shown in Figure 3.
The main control chip generates a 40 kHz rectangular wave, which is amplified by the high-voltage circuit and resonates with the ultrasonic transmitter to emit the ultrasonic wave with the maximum power. When the main control chip STM32F103 generates a 40 kHz rectangular wave, the timer starts counting. After the ultrasonic transducer receives the first wave of the ultrasonic wave, the filter circuit determines and filters out the ultrasonic wave that is not 40 kHz, amplifies it through the amplifier circuit, and the signal shaping circuit converts the high and low levels of 40 kHz and sends it to the main control chip. The main control chip records the moment when the ultrasonic wave passes through each receiving sensor, and calculates the speed of the ultrasonic wave in each rock layer based on the propagation time, and then uploads this information to the rear monitoring room through the GPRS module. [page]
2.1 Main control unit and storage module
The main control chip used in this system is the 32-bit microcontroller STM32F103 based on the ARMCortex-M3 core launched by ST. This controller is specially designed for low-power and price-sensitive applications, with outstanding energy efficiency and processing speed. The μC/OS-II operating system is embedded in this design, which can facilitate multi-task control. In addition, the STM32 microcontroller supports NAND Flash memory expansion, which can store the collected data in Flash, and store and extract data faster.
2.2 Ultrasonic transmitting and receiving circuit
2.2.1 Ultrasonic transmitting circuit
The ultrasonic transmitting circuit consists of an ultrasonic generating circuit, an amplifier circuit and an ultrasonic transducer, as shown in Figure 4. The 40kHz rectangular wave is generated by the PWM module of the STM32F103, amplified by the amplifier circuit and sent to the ultrasonic transmitting transducer to transmit a 40 kHz ultrasonic wave.
2.2.2 Ultrasonic receiving circuit
The ultrasonic receiving circuit includes a signal amplification circuit, a bandpass filter circuit and a rectifier circuit, as shown in Figure 5. The ultrasonic probe receives the ultrasonic wave, and then amplifies it in two stages through the LM358. Then the amplified signal is sent to the LM567 to filter the waveform and trigger the CPU pin. The LM567 has the functions of bandpass filtering and triggering. The external resistors and capacitors of pins 5 and 6 determine the center frequency f of the internal voltage-controlled oscillator, f≈1/1.1RC. When the input amplitude of pin 3 of the LM567 is greater than or equal to 25 mV and the frequency is within the bandwidth, the 8th pin changes from high level to low level, triggering the CPU pin and completing the function of receiving ultrasonic waves.
2.3 GPRS module
The GPRS wireless transmission module uses Huawei's GSM900-C module, as shown in Figure 6. GSM receives CPU data through the serial port and sends it to the rear monitoring room in real time. It transmits the command of the rear monitoring room to the CPU through the sending pin, thus realizing the function that the rear monitoring room can request the human-computer interaction between the target board and the target board. The target board can also automatically collect data at a fixed time and transmit it to the rear monitoring room through the GSM module.
3. Software design of surrounding rock loosening zone monitoring system
The software design process of the ultrasonic-based surrounding rock loosening zone monitoring system is shown in Figure 7. The μC/OS-II operating system is embedded in this design, which mainly includes 4 threads:
①Thread 1 is to collect data of surrounding rock cracks at regular intervals. The collection schedule is sent by the rear monitoring room. For example, if data is collected every 10 minutes, the target board will collect data every 10 minutes and transmit the data to the rear server after the collection is completed.
②Thread 2 is the target board that monitors the instructions sent by the server in real time and saves them to the buffer pool.
③Thread 3 is the target board processing buffer pool data. If it detects that the buffer pool is updated, it means that the rear server has a new task issued, and then it will perform corresponding processing according to the task.
④Thread 4 is a counting thread, which accurately calculates the time taken from sending out the ultrasonic wave to receiving the ultrasonic wave.
Conclusion
The surrounding rock loosening circle monitoring system designed in this paper can monitor the change information of the surrounding rock loosening circle in real time, which can provide correct reference information for the safe support of the tunnel in time. In addition, the scheme proposed in this paper can allow testers to conduct tests away from the mine, which is conducive to the safe production of the mine; due to the addition of multi-tasking, it can also handle multiple tasks in real time, which is conducive to future expansion.
Previous article:Embedded applications using integrated DSP and microprocessor cores
Next article:System design of anti-collision wireless communication car black box
Recommended ReadingLatest update time:2024-11-16 23:46
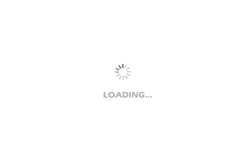
- Popular Resources
- Popular amplifiers
-
Real-time driver monitoring system via modal and viewpoint analysis
-
Computer Vision Applications in Autonomous Vehicles: Methods, Challenges, and Future Directions
-
The STM32 MCU drives the BMP280 absolute pressure sensor program and has been debugged
-
DigiKey \"Smart Manufacturing, Non-stop Happiness\" Creative Competition - Small Weather Station - STM32F103 Sensor Driver Code
Professor at Beihang University, dedicated to promoting microcontrollers and embedded systems for over 20 years.
- Innolux's intelligent steer-by-wire solution makes cars smarter and safer
- 8051 MCU - Parity Check
- How to efficiently balance the sensitivity of tactile sensing interfaces
- What should I do if the servo motor shakes? What causes the servo motor to shake quickly?
- 【Brushless Motor】Analysis of three-phase BLDC motor and sharing of two popular development boards
- Midea Industrial Technology's subsidiaries Clou Electronics and Hekang New Energy jointly appeared at the Munich Battery Energy Storage Exhibition and Solar Energy Exhibition
- Guoxin Sichen | Application of ferroelectric memory PB85RS2MC in power battery management, with a capacity of 2M
- Analysis of common faults of frequency converter
- In a head-on competition with Qualcomm, what kind of cockpit products has Intel come up with?
- Dalian Rongke's all-vanadium liquid flow battery energy storage equipment industrialization project has entered the sprint stage before production
- Allegro MicroSystems Introduces Advanced Magnetic and Inductive Position Sensing Solutions at Electronica 2024
- Car key in the left hand, liveness detection radar in the right hand, UWB is imperative for cars!
- After a decade of rapid development, domestic CIS has entered the market
- Aegis Dagger Battery + Thor EM-i Super Hybrid, Geely New Energy has thrown out two "king bombs"
- A brief discussion on functional safety - fault, error, and failure
- In the smart car 2.0 cycle, these core industry chains are facing major opportunities!
- The United States and Japan are developing new batteries. CATL faces challenges? How should China's new energy battery industry respond?
- Murata launches high-precision 6-axis inertial sensor for automobiles
- Ford patents pre-charge alarm to help save costs and respond to emergencies
- New real-time microcontroller system from Texas Instruments enables smarter processing in automotive and industrial applications
- Python for Data Analysis
- A super electronic capacitor to replace the farad capacitor
- Please help me. How to convert .brd file to Altium file
- DC-DC chips have current control mode and voltage control mode? How to understand?
- The tax control cash register won the "first prize in China"
- The permanent magnet synchronous motor keeps vibrating and turning back and forth
- 09. Anlu SparkRoad domestic FPGA evaluation [practical] key control VGA display
- VS1053 cannot read or write registers
- Several interesting GIF animations
- EEWORLD University Hall----Live Replay: Application of TI Precision ADC in Transmitter