introduction
Today, with the development of electrical intelligence everywhere, countless power consumption occasions cannot do without the Inverted Power Supply System (IPS) to provide stable and high-quality power for field equipment, especially in places such as communication rooms, server workstations, transportation hub dispatching centers, hospitals, power, industrial and mining enterprises, etc., which have strict requirements on power supply guarantee. Many IPS products do not conform to or lag behind the modern power supply concept due to their traditional design. The prominent manifestations are the single complexity of the control module, the backwardness of the controller chip and the heavy control tasks, and the analog closed-loop control without the ideal monitoring and feedback adjustment effect, which brings hidden dangers in the software and hardware design of a single control device, which has an adverse effect on the IPS power output, and even leads to catastrophic consequences for power supply failures to power consumption equipment. Digital control technology is becoming more and more mature, and has been applied in some power supply equipment control applications with leading concepts, highlighting that modularization and digital control have become an inevitable trend.
This paper describes the IPS core control circuit based on the ARM7 Cortex-M3-based single-chip microcomputer STM32F103 and the TI C2000 series DSP chip TMS320F2808, and proposes improvements to the shortcomings of the above products. The designed IPS core control circuit has been proved by test simulation and field test results that this new IPS design improves the IPS structure design, meets the high requirements of IPS operation, and enriches the human-computer interaction interface such as remote monitoring, thereby indirectly saving users' management costs in many aspects.
1. Overall introduction of inverter power supply
In order to meet the requirements of power-sensitive equipment for inverter power supply, the target IPS uses the circuit designed in this paper as the core; the high-speed digital signal microprocessor (DSP TMS320F2808) and peripheral devices are used as signal generation and feedback detection and adjustment modules; the ARM7 single-chip microcomputer ST M32F103 and its peripherals are used as human-computer interaction logic control modules, and the two modules interact and coordinate control. The hardware self-feedback is used to adjust the SPWM waveform output, and the DSP digital algorithm is used to provide high-precision phase-locked technology. The software programming is used for full digital sub-task module control. The DSP module performs the control waveform generation, feedback adjustment, lead-acid battery charging waveform generation and adjustment, self-test and self-detection functions required for IGBT inverter, and performs self-test and fault analysis on all independent circuit connections on the circuit board. The ARM7 module performs tasks such as parameter setting, operation management, environmental parameter monitoring and human-computer interaction processing. The DSP module strives for precision control, and the ARM module has a complete system-level event management function. As shown in Figure 1, the two modules are independent in tasks but closely linked, and they work together to maintain the normal operation of IPS.
Figure 1 IPS inverter principle block diagram
2 Composition of dual-core control system
2.1 DSP control module
This module is an inverter signal generation and feedback detection and adjustment module. The core is a C2000 series high-performance DSP processor TMS320F2808 (hereinafter referred to as F2808). The SPWM signal generated by F2808 is subjected to logic delay and phase shifting by CPLD to form a three-phase inverter IGBT control signal. F2808 is a high-speed DSP chip of Texas Instruments (TI) with a maximum operating speed of 100 MIPS. In order to adapt to the strong interference environment of industrial control, F2808 integrates an enhanced input capture unit (eCAP) and an output comparison PWM generation unit (ePWM) with dead zone control function, and a 12-bit 16-channel fast ADC unit; the kernel supports the IQ conversion function library for fixed-point DSP to realize floating-point operations; there are also rich and common peripheral interfaces such as SCI, SPI, eCAN, etc. As shown in Figure 2, the main task of F2808 in the design is to monitor the switch state and action of the IPS power part, adjust the output of 3-way SPWM waveform according to the feedback of inverter and load state, and control the battery charging pulse. The 3-way SPWM signal output by DSP is directly sent to CPLD, and after the CPLD's equally spaced pulse delay phase shift, it is used as the control waveform of the inverter to generate U, V, W three-phase electricity. [page]
Figure 2 DSP control module block diagram
2.2 Human-computer interaction global control module
The human-machine interaction control module is the most complex digital management module in this IPS design. It not only monitors and manages the operation of the inverter system, but also ensures the communication between the IPS controller and the outside world. The design requires that the human-machine interaction module can handle complex task scheduling and strong burst access (interrupt) processing, which requires a high operating speed; the module must also have a rich expansion interface to provide instant communication between the IPS and the outside world; and have superior bus control and access mechanisms. Taking the above requirements into consideration, the design selected the latest 32-bit microcontroller STM32F103ZET6 (hereinafter referred to as STM32) launched by STMicroelectronics (ST). STM32 is a high-speed, high-performance embedded control chip based on the ARM7 CortexM3 core architecture, with a core operating frequency of 72 MHz and an instruction pipeline processing speed of 1.25 DMIPS/MHz; advanced bus structure and up to 16 levels of preemptive interrupt mechanism (NIVC) with DMA function [10]. As shown in Figure 3, in the design, ST M32 communicates with DSP 2808 through the SCI interface and an interrupt request/receive line; two of the on-chip extended SCI ports are used as RS 232 and RS 485 communication protocol ports respectively; the CAN bus interface and USB bus communicate with the outside world through shared data buffers and interrupt vector entries; the external 256 KB SRAM and 4 MB NOR FLASH are expanded through the 26-bit address bus and 16 data bus of STM32, as well as the LCM module RA8806 with an 8-bit data port and the Ethernet chip W5100 with 16-bit parallel data for SNMP; the SDIO bus of ST M32 is enabled to enable the user to insert the SD card to store and query the IPS status data; the independent clock watchdog circuit and the window watchdog unique to STM32 are enabled in the field environment; the internal chip temperature sensor sampling monitoring, RC clock source and external wake-up function are enabled; the DS18B20 is connected through the general pin The temperature sensor samples the ambient temperature and reserves I2C E2PROM and SPI DA TA FLASH interfaces to prepare for subsequent product upgrades and development.
Figure 3 STM32 module composition block diagram
The communication interface circuit design is shown in Figure 4 and Figure 5.
Figure 4 IPS and external communication interface circuit diagram
Figure 5 STM32 communication interface definition
3. Software Architecture of Control System
The program language in the control module is ANSI standard C language. The program structure, variable naming and comments all follow international standards, which are easy to understand and easy to transplant or expand, as shown in Figures 6 and 7. [page]
Figure 6 DSP program flow chart
Figure 7 ST M32 program flow chart
The code is reasonably written with clear logic, complete functions, compact structure, outstanding robustness and strong maintainability, which meets the requirements of industrial control software writing.
The development and testing documentation compiled during the project is detailed and accurate, and also brings convenience to subsequent research.
4 Prototype Verification
After testing and verification, the target board was successfully applied to a 6KVA industrial frequency double conversion pure online single-phase small power inverter. The load test waveforms of each load are shown in Figure 8. No-load output voltage waveform 1/4 load output voltage waveform Full-load output voltage waveform The measurement results show that the output waveform distortion of the power supply under different load conditions at 220 V AC input is less than 3%, the nonlinear load distortion is less than 5%, and the inverter efficiency is greater than 96%.
Figure 8 Load test waveform output
5 Conclusion
The digitalization of core control is an inevitable trend in the development of industrial control. The IPS based on STM32 and TMS320F2808 control designed in this paper has fast processing speed, high control accuracy, and reasonable modular structure. It can well meet the requirements of modern IPS design, and adds human-computer interaction communication interfaces such as SNMP, USB and SDIO to facilitate local and remote management and maintenance of IPS. The test results prove the feasibility and effectiveness of this design.
Previous article:Dynamic Management of Energy Consumption in Embedded Systems
Next article:A brief discussion on embedded fingerprint recognition solutions
Recommended ReadingLatest update time:2024-11-16 22:31
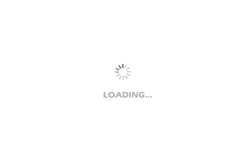
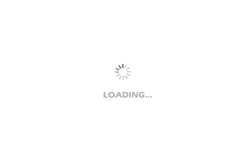
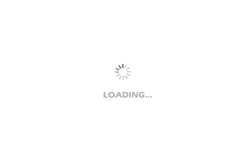
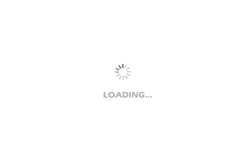
Professor at Beihang University, dedicated to promoting microcontrollers and embedded systems for over 20 years.
- Innolux's intelligent steer-by-wire solution makes cars smarter and safer
- 8051 MCU - Parity Check
- How to efficiently balance the sensitivity of tactile sensing interfaces
- What should I do if the servo motor shakes? What causes the servo motor to shake quickly?
- 【Brushless Motor】Analysis of three-phase BLDC motor and sharing of two popular development boards
- Midea Industrial Technology's subsidiaries Clou Electronics and Hekang New Energy jointly appeared at the Munich Battery Energy Storage Exhibition and Solar Energy Exhibition
- Guoxin Sichen | Application of ferroelectric memory PB85RS2MC in power battery management, with a capacity of 2M
- Analysis of common faults of frequency converter
- In a head-on competition with Qualcomm, what kind of cockpit products has Intel come up with?
- Dalian Rongke's all-vanadium liquid flow battery energy storage equipment industrialization project has entered the sprint stage before production
- Allegro MicroSystems Introduces Advanced Magnetic and Inductive Position Sensing Solutions at Electronica 2024
- Car key in the left hand, liveness detection radar in the right hand, UWB is imperative for cars!
- After a decade of rapid development, domestic CIS has entered the market
- Aegis Dagger Battery + Thor EM-i Super Hybrid, Geely New Energy has thrown out two "king bombs"
- A brief discussion on functional safety - fault, error, and failure
- In the smart car 2.0 cycle, these core industry chains are facing major opportunities!
- The United States and Japan are developing new batteries. CATL faces challenges? How should China's new energy battery industry respond?
- Murata launches high-precision 6-axis inertial sensor for automobiles
- Ford patents pre-charge alarm to help save costs and respond to emergencies
- New real-time microcontroller system from Texas Instruments enables smarter processing in automotive and industrial applications
- ST announces price increase
- [Smart Wardrobe] Material Unboxing ESP32-S3-BOX
- A valve is used in the water supply of the product. The valve is opened when water is used and closed when water is not used. How to measure the force of the opening and closing valve?
- Taiwan Sun Yat-sen University ASIC Laboratory Comprehensive Script Tutorial
- MSP430 Program Library--Digital Tube Display
- How to add hard interrupt to DSP/BIO in DM6437
- Six sharings of power supply design experience
- DSP28335 pwm program dead zone experiment
- Connecting a TVS in parallel to the input of the DCDC chip as protection will limit the power input range. Is there any good solution?
- [Me and Yatli] + From nothing to something, from something to big, I hope to develop better!