The application conditions at sea are harsh and the use requirements are complex. The transponder often needs to have a long standby waiting time in addition to meeting the specified response working time. For this reason, in addition to the selection of devices and the low-power design of circuits, practical transponders often use two states, namely, the value change and the working state, to further reduce power consumption; in the working state, the DSP operation circuit is turned on to achieve reliable and high-precision response ranging; in the value change state, all unnecessary circuits are turned off, and only the control instructions of the water system are detected and responded.
Since the transponder works in the value change state for a long time, the power consumption of the value change circuit has become the primary problem. The use of the low-power single-chip microcomputer MSP430F5438 effectively solves the system's power consumption requirements.
1 Hardware Design of Response Releaser Value Changing Circuit
1.1 Performance Characteristics of MSP430F5438 MCU
MSP430F5438 is a powerful MCU with ultra-low power consumption characteristics from TI, with the following characteristics:
1) Ultra-low power consumption
MSP430F5438 runs under 1 M clock and 2.2 V power supply conditions, with an operating current of 165μA, and ultra-low power consumption.
2) Powerful processing capability
MSP430F5438 has 18 M system clock; has rich addressing modes, but only needs 27 concise instructions, has a large number of on-chip registers, and the memory can realize multiple operations; has an efficient table lookup processing method; has many internal interrupt sources, and can be arbitrarily nested, which is flexible and convenient to use.
3) Rich on-chip peripheral modules
Peripheral modules include: 12-bit A/D, precision analog comparator, hardware multiplier, two groups of clock modules with a frequency of up to 8 M, two 16-bit timers with a large number of capture/comparators, watchdog, two serial communication interfaces that can realize asynchronous, synchronous and multiple access, dozens of parallel input and output ports that can realize direction setting and interrupt functions, etc.
4) Large storage space
MSP430F5438 is a FLASH type microcontroller with up to 256 kB FLASH ROM and 16KB RAM.
The powerful functions and ultra-low power consumption of the MSP430F5438 microcontroller provide the basis for realizing the various functions of the response releaser.
1.2 Hardware block diagram of the value change circuit
The function of the value change circuit is to receive remote control commands and respond accordingly. The main surface remote control commands are: power on, standby, release, self-test, etc. Among them, power on is to power on the DSP circuit of the transponder releaser and prepare for high-precision transponder ranging; standby is to shut down the DSP circuit of the transponder releaser and return to the low-power value change state; the release command opens the release hook, releases the sinker, and makes the transceiver float up for recovery; the self-test command makes the transceiver perform pressure (depth) detection and power supply detection, and uploads through underwater acoustic communication. Therefore, in addition to external signal input, command transmission control and JTAG debugging port, the MSP430F5438 microcontroller also needs to realize the monitoring and management of various power supplies, pressure data collection, release mechanism control, etc. In addition, the RS232 port is used for communication with the PC during laboratory and surface debugging, and I2C realizes data communication with the DSP working circuit. The hardware block diagram of the value change circuit is shown in Figure 1.
1.3 Data Input Port Allocation
External signal acquisition, power monitoring and pressure sensor data are all converted into digital signals by ADC and then sent to MCU for processing. Considering the power consumption and complexity of the system, the ADC uses the 12-bit ADC integrated in the MCU. The electrical connection relationship is shown in Table 1.
The signal is connected by external broadband, enters the microcontroller after passing through the on-chip ADC, and is filtered in two narrowband channels, respectively targeting the two remote control command frequencies of the RZ-BFSK digital communication method. The power supply voltage is sent to the MCU after passing through a voltage divider network, and an insufficient power alarm signal is given when the power supply voltage drops to the threshold. [page]
to achieve low power consumption of the underwater acoustic response releaser. The power supply of the working module, the release mechanism, the pressure sensor and the power amplifier are strictly managed. The system will only turn on the power supply of the corresponding module after receiving the command. The power control adopts the level trigger mode, and its electrical connection relationship is shown in Table 2.
1.5 Others
To improve the reliability of the system, a low-power hardware watchdog based on MAX6369 is added, and the supply current is 8μA at 3.3 V power supply; to improve the efficiency of the transmitter, the power amplifier works in Class D mode, using symmetrical square wave drive, which is directly generated by the MCU, reducing the complexity of the system; in order to debug and set parameters of the underwater acoustic transponder releaser under laboratory conditions, an RS232 data transmission interface is designed.
2 Software Design of the Value Change Circuit of the Underwater Acoustic Transponder Releaser
2.1 Software Flow of the Value Change Circuit
The value change management functions of the transponder releaser include: underwater acoustic communication command code group detection, underwater acoustic communication command interpretation, underwater acoustic communication coding transmission, power management, release mechanism management and setting DSP parameters. The software flow is shown in Figure 2.
The following is part of the initialization code for the main program
[page]
2.2 Underwater Acoustic Command DetectionFor the value change circuit of the responder releaser, the biggest challenge lies in the reliable detection of underwater acoustic commands and the confirmation of underwater acoustic communication pulses. In MSP430F5438, the signal detection adopts the Notch filter energy detection method. Its algorithm is:

Since the core clock frequency of MSP430F5438 is 18 MkHz, the processing performance is much worse than that of the DSP dedicated digital processing chip. The following measures are taken to implement two-way Notch filter detection:
1) The absolute value method is used to replace the envelope output, while avoiding calculation overflow;
2) The filter smoothing algorithm is used instead of the mean smoothing algorithm;
3) One of the signals is sampled 4 times.
2.3 Underwater Acoustic Command Pulse Selection
Due to the influence of underwater acoustic multipath, the command signal containing the specified code element often has more than the specified pulse when it reaches the underwater acoustic transceiver after passing through the underwater acoustic channel, and even inter-code interference may occur in severe cases. Therefore, it is necessary to select the collected pulse information and then determine which command it belongs to.
Suppose the obtained pulse sequence is represented by p(0), p(1), p(2), ..., p(N). If it is a correct command, then the starting points of each pulse and the starting point of the first pulse have the following relationship:
p(k)=p(0)+k*100
Considering the influence of the propagation path on the signal, the above formula becomes:
p(0)+k*100-ξ≤p(k) That is:
k*100-2*ξ≤p(k)-p(0)-ξ
3 Conclusion
The design of the transponder releaser value change circuit based on the MSP430F5438 microprocessor achieves low power consumption and high reliability value change function through scientific and reasonable power management, concise and efficient underwater acoustic signal processing and command detection software. The standby time is more than 30 days after use. At the same time, its launch control and release recovery functions have also been fully verified in the actual use of the transponder releaser.
Previous article:Six source codes for basic C language programming of microcontrollers
Next article:Monolithic integrated variable gain visible light receiver
Recommended ReadingLatest update time:2024-11-16 14:32
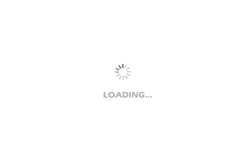
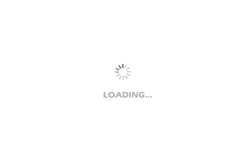
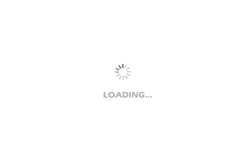
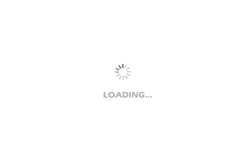
- Popular Resources
- Popular amplifiers
-
MSP430 series single chip microcomputer system engineering design and practice
-
oled multi-chip calling program
-
Microcontroller Principles and Applications Tutorial (2nd Edition) (Zhang Yuanliang)
-
Getting Started and Improving MSP430 Microcontrollers - National Undergraduate Electronic Design Competition Training Course
Professor at Beihang University, dedicated to promoting microcontrollers and embedded systems for over 20 years.
- Innolux's intelligent steer-by-wire solution makes cars smarter and safer
- 8051 MCU - Parity Check
- How to efficiently balance the sensitivity of tactile sensing interfaces
- What should I do if the servo motor shakes? What causes the servo motor to shake quickly?
- 【Brushless Motor】Analysis of three-phase BLDC motor and sharing of two popular development boards
- Midea Industrial Technology's subsidiaries Clou Electronics and Hekang New Energy jointly appeared at the Munich Battery Energy Storage Exhibition and Solar Energy Exhibition
- Guoxin Sichen | Application of ferroelectric memory PB85RS2MC in power battery management, with a capacity of 2M
- Analysis of common faults of frequency converter
- In a head-on competition with Qualcomm, what kind of cockpit products has Intel come up with?
- Dalian Rongke's all-vanadium liquid flow battery energy storage equipment industrialization project has entered the sprint stage before production
- Allegro MicroSystems Introduces Advanced Magnetic and Inductive Position Sensing Solutions at Electronica 2024
- Car key in the left hand, liveness detection radar in the right hand, UWB is imperative for cars!
- After a decade of rapid development, domestic CIS has entered the market
- Aegis Dagger Battery + Thor EM-i Super Hybrid, Geely New Energy has thrown out two "king bombs"
- A brief discussion on functional safety - fault, error, and failure
- In the smart car 2.0 cycle, these core industry chains are facing major opportunities!
- The United States and Japan are developing new batteries. CATL faces challenges? How should China's new energy battery industry respond?
- Murata launches high-precision 6-axis inertial sensor for automobiles
- Ford patents pre-charge alarm to help save costs and respond to emergencies
- New real-time microcontroller system from Texas Instruments enables smarter processing in automotive and industrial applications
- FAQ_How to calculate the response time from shutdown state to READY state
- [NXP Rapid IoT Review] Low Power Consumption Experiment & Summary
- There is something wrong with the program, please solve it
- What does the data check code mean? Can someone explain it to me?
- Supercapacitor constant power charging and voltage regulation
- EEWORLD University ---- Big Data Machine Learning (Yuan Chun)
- Boss, what's your home WIFI password? ——Qorvo~Wi-Fi 6
- When BLE meets MEMS——attitude calculation
- Lazy voice-controlled lamp based on Gizwits Cloud
- 【NXP Rapid IoT Review】+ Review Summary