With the development of social life, people's requirements for current printing and dyeing products are getting higher and higher, especially for cloth and packaging shells, so the requirements for modern printing and dyeing technology are also getting higher and higher. With the increase of technology, it is a big challenge for printing and dyeing equipment. The most important one is the synchronous control of multiple motors in large printing and dyeing machines.
In printing and dyeing equipment, the synchronous control of motors is mainly determined by three aspects: one is the processing speed of the processor for tension sensor data and the reaction speed of the motor to the tension sensor; the second is the difference in mechanical properties between different motor groups and the real-time simultaneous control problems they produce; the third is the communication problem between the control unit and each motor group, including speed, anti-interference, etc. The traditional printing and dyeing machine adopts a single-chip microcomputer plus AD/DA chip for data processing and execution, and there is also a practice of using DSP plus single-chip microcomputer to improve data processing capabilities. With the development of current technology, the design method of the sub-system of the processor based on the ARM CORTEX-M3 core plus the CAN bus is studied.
The master controller and unit controller use the STM32F103 chip based on the ARM Cortex-M3 core launched by ST to try a new design. This design reduces costs while improving system performance and also achieves docking with existing printing and dyeing equipment.
1 System Design
1.1 System Structure Design
According to the specific situation of the existing printing and dyeing machine in the printing and dyeing industry, the control system is mainly improved.
In the design of large-scale printing and dyeing machines, the main consideration is the synchronous control of multiple motors. It is necessary to ensure that the cloth is stable during the transmission process. The tension should not be too large due to the asynchronous motor, which will cause the cloth to be overstretched, and the cloth should not be wrinkled due to insufficient tension. In large-scale printing and dyeing machines, depending on the complexity and simplicity of the process, the number of motors that need to be synchronized ranges from 8 to more than 40. The use of the CAN bus network ensures that the number of unit controllers can be expanded autonomously according to different processes. The system design block diagram is shown in Figure 1.
1.2 System composition
The system is mainly composed of the main controller, unit controller, CAN bus network, and inverter.
The main controller is the main control unit of the system. Its main function is to display and control the working status of the entire system, as well as to set and adjust the main working parameters of the system, such as fabric speed and tension sensor sensitivity. Coordinate the working status of each unit control.
The function of the unit controller is mainly to fine-tune the sensitivity of the tension sensor, monitor the data of each tension sensor in real time, adjust the output voltage according to the data of each tension sensor, and thus adjust the working status of the corresponding motor. At the same time, it is also necessary to deal with emergencies, such as the handling of tension sensor failure and motor stalling.
1.3 Specific design of the unit controller
In the design, I used the chip based on ARM's CORTEX-M3 core-STM32f103RCT6 as shown in Figure 2. Its features include: The STM32F103 series microprocessor is the first 32-bit standard RISC (reduced instruction set) processor based on the ARMv 7-M architecture, providing high code efficiency; the operating frequency is 72MHz, with built-in FLASH memory up to 256KB and SRAM up to 48KB.
It integrates a 12-bit A/D and a dual-channel 12-bit D/A, as well as a controller area network (CAN) specifically for industrial control. It provides compatibility with specifications 2.0A and 2.0B (active), with a bit rate of up to 1 Mb/s. It can receive and send standard frames with 11-bit identifiers, as well as extended frames with 29-bit identifiers. It has 3 transmit mailboxes and 2 receive FIFOs, and 3 levels of 14 adjustable filters. [page]
Because the logic level of the CAN bus controller of STM32 adopts LVTTL, the CAN bus transceiver SN65HVD230 produced by Texas Instruments is used . SN65HVD230 can be used in high interference environments. It adopts differential reception and has the ability to resist a wide range of common mode interference and electromagnetic interference. The isolation circuit composed of 6N137 can well realize the electrical isolation of each node on the CAN bus. Although the addition of the isolation circuit increases the complexity of the node, it improves the stability and security of the node. In addition, in order to avoid signal reflection, which leads to a decrease in communication reliability and anti-interference ability, or even communication failure, two 120Ω bus impedance matching resistors are required at both ends of the CAN bus. The CAN interface design is shown in Figure 3.
2 System working principle
The system working principle mainly includes four parts: adjustment before the system works, system startup, synchronous adjustment during operation and fault handling.
(1) Before the system works, because the mechanical properties of each motor unit of the printing and dyeing equipment cannot be the same, the operation synchronization coefficient Li of each part should be adjusted before conveying the cloth so that the line speed is the same when there is no load. Here, the first motor unit of the first unit controller is generally set as the master unit, and the others are slave units. The operation speed of the slave motor unit needs to be adjusted to be consistent with the line speed of the master unit. After this coefficient Li is set, it will be fixed in the subsequent operation.
(2) The system starts by the main controller sending a control command to each unit controller, including setting the cloth speed V and the rising time interval to reach the cloth speed v. Then the main controller gives a general startup command. The unit controller sets the corresponding 8-way signal output according to the command of the main controller, thereby controlling each motor unit to run to the set speed according to the preset rising time interval.
(3) Adjustment during system operation. According to the actual operation of the printing and dyeing machine, when the motor speed increases, the measurement data of the tension sensor will change. According to the formula:
Vout=V0Li+KiFi (1)
where: Vout is the output voltage of D/A conversion; Li is the operation synchronization coefficient set before the system starts; V0 is the D/A output voltage of the active motor unit; Fi is the output of the tension sensor; Ki is the sensitivity of VOUT output to the tension sensor output feedback Fi. Through the output feedback Fi, a small closed-loop system is formed at the control end of the motor. The schematic diagram of the tension sensor is shown in Figure 4.
The basic principle of tension sensor feedback regulation synchronization: In the normal state, the sensor contact stops in the middle state, and the output voltage of the sensor is zero. When the motor speed increases, causing the tension of the cloth to increase, the tension sensor contact will move downward, and the output of the sensor will become negative. According to formula (1), the value of Vout will decrease, which will slow down the speed of the corresponding motor. In this way, the purpose of synchronization can be achieved.
(4) Fault handling: In the actual industrial production process, it cannot be absolutely guaranteed that the system will run without any faults. According to the previous production experience of printing and dyeing combined machines, the tension sensor is a part that may fail. Therefore, according to the actual situation, a tension sensor sharing mechanism and a free configuration function of the motor output channel are designed. If the tension sensor Fi cannot work normally, that is, its corresponding output (Vout) has no output regulation function. At this time, the unit controller will output the adjacent motor control voltage (Vout)i-1 to (Vout)i.
3 Software design of the main parts of the system
The software design adopts a modular software design concept, and mainly implements the following modules: host human-machine exchange interface, system operation monitoring module, CAN bus communication module of each unit controller, sensor data acquisition module, unit controller motor control and adjustment module, fault analysis and judgment processing module and operation data storage module. Among them, the CAN bus communication module and the coordination between modules are difficult.
3.1 Design of CAN bus communication module
The main function of the CAN bus communication module is to transmit the control commands issued by the main controller and upload the status data of each unit controller. After receiving the data, the CAN node parses the data and obtains the corresponding commands and data.
The software design of the CAN bus node mainly includes three parts: CAN node initialization, message sending and message receiving. The initialization program design is very important for the normal operation of the CAN bus node. It mainly includes the setting of working mode, clock output register, receiving mask register, receiving code register, bus timer, output control register and interrupt enable register.
3.2 Work coordination between various software modules of the system
(1) The main controller sends the control command to the CAN bus, and the corresponding node receives and extracts the corresponding command and performs the corresponding operation according to the command.
(2) Each unit controller collects data from each tension sensor in a loop and adjusts the working state of the corresponding motor according to the data.
(3) Each unit controller sends the status of its 8 subordinate motors to the main controller through the CAN bus at regular intervals. The main controller extracts the status information, records the status information of each node, and displays it on the human-machine interface.
(4) People can set the working state of each motor according to specific circumstances.
4 Conclusion
From the principle design of the system, it can be seen that this printing and dyeing machine design uses a processor with a main frequency of 72 MHz, which can complete the data processing on each unit controller. The minimum feedback adjustment system composed of tension sensors is adopted to ensure the real-time synchronization of the system. The large-loop feedback method of transmitting the status information to each master controller and then implementing synchronization by the master controller is changed. In addition, this design uses a relatively high-integration MCU with 12-bit A/D and D/A conversion channels, so that the system has no peripheral sampling circuits, avoiding the influence of the complex factory environment on the system.
In short, the design of this printing and dyeing machine realizes the combination of existing high-performance processors and advanced CAN bus control networks, and has simple hardware design, strong anti-interference ability, and modular software design. The system uses a small feedback loop, which reduces the data flow on the bus on the one hand, and avoids the transmission delay on the bus on the other hand, making the motor synchronization more timely and accurate.
Previous article:Study on the performance of μC/OSII based on Cortex-M3 core
Next article:Design of ecological IoT data collection substation based on Cortex-M3
Recommended ReadingLatest update time:2024-11-16 16:21
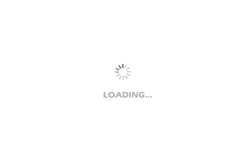
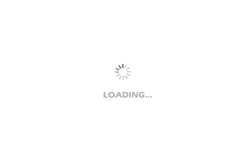
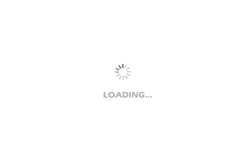
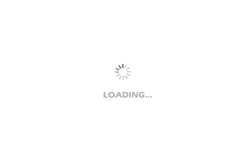
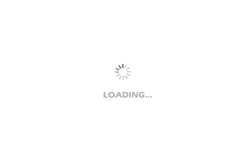
- Popular Resources
- Popular amplifiers
Professor at Beihang University, dedicated to promoting microcontrollers and embedded systems for over 20 years.
- Innolux's intelligent steer-by-wire solution makes cars smarter and safer
- 8051 MCU - Parity Check
- How to efficiently balance the sensitivity of tactile sensing interfaces
- What should I do if the servo motor shakes? What causes the servo motor to shake quickly?
- 【Brushless Motor】Analysis of three-phase BLDC motor and sharing of two popular development boards
- Midea Industrial Technology's subsidiaries Clou Electronics and Hekang New Energy jointly appeared at the Munich Battery Energy Storage Exhibition and Solar Energy Exhibition
- Guoxin Sichen | Application of ferroelectric memory PB85RS2MC in power battery management, with a capacity of 2M
- Analysis of common faults of frequency converter
- In a head-on competition with Qualcomm, what kind of cockpit products has Intel come up with?
- Dalian Rongke's all-vanadium liquid flow battery energy storage equipment industrialization project has entered the sprint stage before production
- Allegro MicroSystems Introduces Advanced Magnetic and Inductive Position Sensing Solutions at Electronica 2024
- Car key in the left hand, liveness detection radar in the right hand, UWB is imperative for cars!
- After a decade of rapid development, domestic CIS has entered the market
- Aegis Dagger Battery + Thor EM-i Super Hybrid, Geely New Energy has thrown out two "king bombs"
- A brief discussion on functional safety - fault, error, and failure
- In the smart car 2.0 cycle, these core industry chains are facing major opportunities!
- The United States and Japan are developing new batteries. CATL faces challenges? How should China's new energy battery industry respond?
- Murata launches high-precision 6-axis inertial sensor for automobiles
- Ford patents pre-charge alarm to help save costs and respond to emergencies
- New real-time microcontroller system from Texas Instruments enables smarter processing in automotive and industrial applications
- Overcurrent protection circuit with self-locking
- LCD5110 driver for MSP430f5529
- TI DSP C6657 Learning - Compiling static library .lib
- tree Command
- What are the categories of edge computing devices?
- A question about transformers
- Application skills of watchdog reset
- Anyone know what connector this is?
- [Evaluation of the popular N32G45XVL model of the National Technology M4 core] Part 6 Preparation for motor application development
- AR1021X uses hostapd to configure AP hotspots.