0 Introduction
With the rapid development of power electronics technology and microcontroller technology, the application of modern AC variable frequency speed regulation system technology in motor control systems is becoming more and more widespread. The fully digital controlled variable frequency speed regulator using the fully controlled device IGBT has been universalized, with the advantages of wide speed regulation range, high speed regulation accuracy, fast dynamic response, high operating efficiency, and convenient operation. The popularization and application of variable frequency speed regulators has improved the automation level of modern industry, improved product quality and labor efficiency, and saved energy to the maximum extent, thus conforming to the national policy of developing and building a harmonious and conservation-oriented society.
This paper selects the cost-effective microcontroller R5F21246 seties launched by Renesas, which is embedded with the R8C/Tiny series CPU core. All MCUs in the R8C/Tiny series integrate on-chip flash memory, which has high performance and good ease of use, 1 MB address space, and 2 KB on-chip data storage FLASH, which is very suitable for home appliances such as air conditioners, washing machines, refrigerators, and industrial control applications such as AC servo motors.
1 Basic structure of AC induction motor system
The principle structure of AC induction motor control system is shown in Figure 1, which includes main circuit, control unit, power drive unit, protection unit and signal feedback acquisition unit.
The AC induction motor control unit includes speed controller, torque and current controller, etc. Renesas single-chip microcomputer R5F21246 has become a trend of becoming the control core of AC induction motor control system with its advantages of low price, low power consumption, high performance and fast processing speed. The power drive unit adopts the driver chip IRS2136S, which not only integrates the drive circuit, but also has fault detection and protection circuits such as overvoltage, overcurrent, overheating and undervoltage. When the system has problems, it can protect itself in time, improving the reliability of the system. Each collected signal is transmitted to the R5F21246 through feedback, and is accurately and quickly processed and then output to realize real-time control of each component. A soft start circuit is also added to the main circuit to reduce the impact of the startup process on the driver.
2 Drive circuit design of AC induction motor system
The power drive module, as the strong power part of the AC induction motor control system, consists of two units: the power supply unit provides power for the digital and analog circuits of the entire system; the power drive unit IRS2136S is used to drive the motor (see Figure 2).
The design of the power board includes four hardware protection functions, namely overcurrent (forward and reverse current) protection, bus overvoltage protection, bus undervoltage protection and IGBT overheat protection. Each protection has an LED alarm display. In order to enhance reliability, after the protection action occurs, a shutdown signal will be sent to the MCU to protect the power device IRS2136S and prevent damage to the components. These signals must be canceled by a separate reset signal, otherwise the protection circuit will always be effective to prevent misoperation from damaging the equipment and affecting personal safety.
2.1 Power supply circuit
The main power supply circuit is shown in Figure 3. Input voltage range: AC 187~264 V, frequency range: 48~53 Hz. The DC bus voltage output is stable at a normal value of about 310 V. The Schottky diode D110 is connected in parallel at both ends of the bus voltage to prevent the bus from overvoltage. The filter capacitor C110 filters out interference signals. Resistors R104~R109, C107 and C106 are connected in parallel to stabilize the voltage at both ends of the capacitor. The DC bus voltage output uses a pre-charging circuit. At the moment of power-on, the current-limiting resistor R102 provides current to the rectifier bridge D101 and filter capacitors C107 and C108, reducing the impact on the rectifier bridge. When the filter capacitor is almost fully charged, the current-limiting resistor is bypassed through relay K101. The DC bus voltage generates 16 V and 5 V stable DC voltages through the VIPER12 (U101) and LM78L05 (U102) chips, which respectively power the drive circuit and other circuits, as shown in Figure 4.
2.2 Temperature detection circuit
Figure 5 is the temperature detection circuit of IGBT. R379 in the circuit is a negative temperature coefficient thermistor NTC. When the temperature is too high, the resistance of R379 becomes smaller. The voltage output fault signal of the detection circuit is fed back to the single-chip microcomputer. After the single-chip microcomputer analyzes and processes, the measures taken are used to protect the system, such as stopping the driver chip from working, and then releasing the protection when the temperature returns to normal. [page]
2.3 Current detection circuit
In order to reduce the system cost, the circuit adopts a single resistor sampling technology. Generally speaking, the vector control algorithm needs to collect at least two-phase current of the motor, but the single resistor sampling only needs to collect the current of the negative bus.
As shown in Figure 2, the single resistor R236 samples, and the sampled current ishunt. For each switch state of the lower bridge arm Q202, Q204, and Q206, the current state flowing through is shown in Table 1.
In Table 1, "0" indicates that the switch is off, and "1" indicates that it is on. Since the current is almost unchanged in one PWM cycle, it is only necessary to sample twice in one PWM cycle to obtain the state of the current of each phase of the motor at that moment, because the sum of the three-phase current is zero.
Single resistor sampling will encounter some challenges. The space vector pulse width modulator (SVPWM) will have two long and one short duty cycles and two short and one long duty cycles as well as three almost equal duty cycles at the sector boundary and low-speed modulation area of the space vector. In this way, if the effective vector lasts less than the current sampling time, an error will occur. The solution adopted in this solution is to insert an effective vector of a fixed time at the adjacent boundary, and in the low-speed modulation area, the effective vector is inserted in turn. Inserting an effective vector will cause distortion to the current waveform, which needs to be compensated by software in this case.
In addition to reducing the cost of the system, the advantage of single resistor sampling is that it detects the three-phase current based on the same gain and offset, and has good consistency. The disadvantages are also obvious. For MCU, the algorithm is complicated and its operation time is increased, and the code is longer than the three-resistance method; for current detection, its waveform distortion is slightly larger than the three-resistance method. The performance of single-resistance sampling is fully competent for the application of variable-frequency air conditioners, and the cost is low, which is why most home appliance manufacturers are willing to choose single-resistance sampling.
2.4 Speed detection circuit
The position sensor plays the role of determining the rotor position and speed in the AC induction motor. As a logic switch circuit, it provides correct position information, that is, converts the magnetic pole position signal of the rotor magnet into an electrical signal. Then control the stator winding commutation. This design uses FUS1881 (Hall sensor). The motor rotor rotates one circle to input 8 pulses to the single-chip microcomputer, thereby controlling the movement of the AC induction motor and making the control program simple. The Hall detection circuit is shown in Figure 6.
3 EMC measures
The electromagnetic compatibility (EMC) anti-interference design of this hardware system mainly includes the following aspects: lightning protection and filtering of power input, grounding technology, shielding technology, isolation technology, and printed circuit board design.
3.1 Filtering of power input
As shown in Figure 7, L101, C102 and C103 form a common mode choke. This is a power filter composed of a low-pass filter circuit. It implements the initial attenuation of the high-frequency components in the transient voltage waveform. It allows DC or 50 Hz current to pass through, and has a greater attenuation on the interference signal with a higher frequency. Since there are two types of interference signals, differential mode and common mode, the power filter must have an attenuation effect on both types of interference. Note that when the operating current exceeds the rated current, the inductor core in the filter will be saturated, which will reduce the actual inductance and reduce the high-frequency filtering performance of the filter. Therefore, when determining the rated operating current of the filter, take 1.5 times the actual current value. The varistor V101 plays the role of suppressing differential mode overvoltage and increasing the leakage current limiting voltage.
3.2 IGBT protection circuit
As shown in Figure 2, the power drive amplifier circuit, if the forward voltage rise rate dv/dt applied to the IGBT is too large, due to the existence of the junction capacitance, a large displacement current is generated, which may act as a trigger current, reducing the forward blocking ability of the IGBT, and causing misconduction in severe cases. In order to suppress the effect of dv/dt, a resistance absorption circuit is connected in parallel at both ends of the IGBT gate level and the gate, and a bidirectional freewheeling diode circuit is added to suppress the large displacement current, and this part of the energy is consumed by the resistor. Similarly, the protection circuit can also attenuate and suppress the high-frequency interference signal in the circuit.
3.3 Others
Due to the large amount of power supply in the system, the analog ground, digital ground, etc. are properly handled. In addition, attention is paid to the grounding of the shell, and a small capacitor is added to each input end of the driver chip IRS2136S to improve reliability. When designing the PCB board, attention is paid to the routing method, line width, via processing, etc.
4 Conclusion
The control circuit of the AC induction motor based on Renesas microcontroller designed in this paper, combined with the advanced three-phase power driver chip IRS2136S, adopts 6 single-tube IGBTs and single resistor sampling, which reduces the production cost; adds EMC measures to make the system work more stable and reliable. This paper makes full use of the advantages of the R8C/Tiny series CPU core - rich firmware library functions, shortening the development cycle. Practical application shows that the AC induction motor control circuit based on Renesas microcontroller has good dynamic performance, stable and reliable system operation, high efficiency, low cost, energy saving and low noise, etc., which can fully meet the actual use requirements of household appliances.
Previous article:Interference Analysis of Single Chip Microcomputer and Improvement of MCU
Next article:Generate PWM pulses using the PCA function of SST microcontroller
Recommended ReadingLatest update time:2024-11-16 19:55
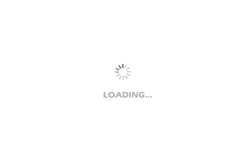
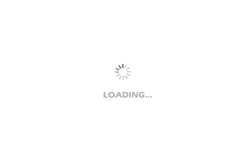
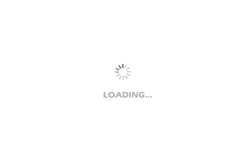
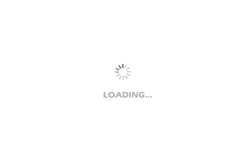
- Popular Resources
- Popular amplifiers
Professor at Beihang University, dedicated to promoting microcontrollers and embedded systems for over 20 years.
- Innolux's intelligent steer-by-wire solution makes cars smarter and safer
- 8051 MCU - Parity Check
- How to efficiently balance the sensitivity of tactile sensing interfaces
- What should I do if the servo motor shakes? What causes the servo motor to shake quickly?
- 【Brushless Motor】Analysis of three-phase BLDC motor and sharing of two popular development boards
- Midea Industrial Technology's subsidiaries Clou Electronics and Hekang New Energy jointly appeared at the Munich Battery Energy Storage Exhibition and Solar Energy Exhibition
- Guoxin Sichen | Application of ferroelectric memory PB85RS2MC in power battery management, with a capacity of 2M
- Analysis of common faults of frequency converter
- In a head-on competition with Qualcomm, what kind of cockpit products has Intel come up with?
- Dalian Rongke's all-vanadium liquid flow battery energy storage equipment industrialization project has entered the sprint stage before production
- Allegro MicroSystems Introduces Advanced Magnetic and Inductive Position Sensing Solutions at Electronica 2024
- Car key in the left hand, liveness detection radar in the right hand, UWB is imperative for cars!
- After a decade of rapid development, domestic CIS has entered the market
- Aegis Dagger Battery + Thor EM-i Super Hybrid, Geely New Energy has thrown out two "king bombs"
- A brief discussion on functional safety - fault, error, and failure
- In the smart car 2.0 cycle, these core industry chains are facing major opportunities!
- The United States and Japan are developing new batteries. CATL faces challenges? How should China's new energy battery industry respond?
- Murata launches high-precision 6-axis inertial sensor for automobiles
- Ford patents pre-charge alarm to help save costs and respond to emergencies
- New real-time microcontroller system from Texas Instruments enables smarter processing in automotive and industrial applications
- [Fudan Micro FM33LC046N] PACK package also limits the MDK version?
- Can stm32f407 be used as a USB host to receive serial port data?
- uLisp, a Lisp language for embedded systems
- SensorTile.box firmware upgrade first experience
- EPLAN P8 Advanced Tutorial (Chinese)
- [ESP32-Audio-Kit Audio Development Board Review] Part 3 play_mp3_control
- PCB manufacturing experience summary (2)
- [Telink B91 Universal Development Kit] Questions about the functions of TX and RX on the burning tool
- FPGA Design Process
- Power supply obstacles + power supply SBC selection and pitfalls