In response to the above problems, this paper designs a simulated picking robot based on ATmega32, which can realize manually operated mechanical picking. The infrared remote control controls the robotic arm to extend the end gripper to the location of the target fruit, perform grabbing work, and complete the picking task.
1 Overall design of the robot
The design of the robot integrates mechanical manufacturing technology, electronic circuit technology, automatic control and sensor detection technology, as well as software development and programming. In this paper, the signals of the robot's sensors and infrared remote controllers are input to the main control board, which processes and outputs the robot's three-degree-of-freedom mechanical arm and crawler chassis structure, and the infrared remote control mechanical arm to grasp the fruit. The robot structure block diagram is shown in Figure 1.
The control mode of the robot is wireless control. The robot adopts direct control mode. The operator sends control instructions to the remote end through the remote control. Control the forward movement of the robot body, left and right steering, movement of the three-degree-of-freedom mechanical arm, and rotation, opening and closing of the gripper. The robot designed in this paper has the characteristics of simple structure, rich functions, and strong scalability.
2 Mechanical device design
The mechanical device diagram of the remote control picking robot is shown in Figure 2, which mainly includes two parts: a two-degree-of-freedom mobile carrier and a three-degree-of-freedom mechanical arm with a gripper. The robot body is assembled into a robot body using mesh aluminum plate material and engineering plastics. The structure is light and convenient for adding modules to the body. The mobile carrier is a crawler chassis, which is equipped with a main control circuit board, a picking auxiliary device, a variety of sensors, a power module, etc. Each side of the crawler chassis adopts a double crawler structure and is driven by 4 FAULHABER motors. The robot arm is fixed on the crawler walking mechanism. The servo motor on the robot arm uses the MG995 metal gear servo with a torque of 10 kg/cm. The servo motor 1 on the robot arm controls the opening and merging of the gripper, so that the gripper can complete tasks such as picking and shearing. Servo motor 2 controls the left and right rotation of the gripper. Servo motor 3 controls the up and down movement of the small arm. Servo motor 4 drives the up and down movement of the large arm through the connecting rod and servo motor 5.
[page]
3 Hardware Circuit Design
Since the robot needs to process a lot of sensor input data and control a lot of motors at the same time, this places stringent requirements on the microcontroller. Based on openness, reliability, real-time and other considerations, this design uses a high-performance AVR processor--ATmega series, and selects the chip model ATmega32 16AU as the control core. ATmega32 16AU, with 44 pins, is an 8-bit high-performance, low-power microcontroller with 32KB system programmable Flash. ATmega32 is a low-power 8-bit CMOS microcontroller based on the enhanced AVR RISC structure.
The data throughput of ATmega32 is as high as 1 MIPS/MHz, which can alleviate the contradiction between power consumption and processing speed of the system. Its core has a rich instruction set and 32 general working registers. All registers are directly connected to the arithmetic logic unit (ALU), so that one instruction can access two independent registers simultaneously in one clock cycle. It has an advanced RISC structure, 131 instructions, most of which are executed in a single clock cycle, 32 8-bit general-purpose working registers, fully static operation, and performance up to 16 MIPS when operating at 16 MHz, requiring only 2 clock cycles of hardware multipliers.
3.1 Control motherboard design
The motherboard circuit based on ATmega32 consists of a power module, a crystal oscillator module, a communication module, a motor drive module, a remote control encoding module, and input and output parts. The motherboard circuit is designed with 8 input interfaces, 8 output interfaces, 4 DC motor output interfaces, ISP interface and program download interface, IR infrared remote control receiver access port and IR infrared remote control channel setting dip switch. Each module interface is plug-in, which is convenient for the use of various modules and function expansion. The input interface uses a variety of sensors to detect signal input into the MCU. Use AVR development software on the computer to write the program, and then download the program to ATmega32. The infrared transmitting module sends a control signal to the infrared receiving module, which processes the signal and transmits it to the MCU. The external sensor module processes the sensing signal and transmits it to the MCU, which processes and analyzes various input signals and sends a control signal to the actuator.
The control motherboard of this design has strong scalability. By adding modules and modifying programs, it can be used for various robot development and intelligent circuit production, and is widely used. The control circuit is shown in Figure 3.
3.2 USB to UART download circuit
The serial communication between AVR and PC is carried out. The mainboard download port adopts the serial communication mode of UART, and the computer cannot be directly connected to the UART port, so a USB to UART converter is needed. Considering the factors such as practicality and reliability, the conversion circuit chip is designed as a single-chip bridge CP2101. The integrated USB transceiver on CP2101 does not require external resistors, the integrated clock does not require an external oscillator, the integrated 512-byte EEPROM is used to store products, and the on-chip voltage regulator is 3.3 V output.
3.3 Infrared remote control design
The infrared remote control of this design adopts the BL35P12 chip of Shanghai Belling. BL35P12 is an OTP type low-power 8-bit general-purpose microcontroller (MCU), which completes the scanning of keys and the generation of infrared coding signals. It can be precisely controlled, so this chip is used as the main control chip of remote control. The robot can be controlled to move forward, backward, left, and right by operating the direction keys, and different actions can be achieved by operating the number keys and special keys.
[page]
4 Software ProgrammingThe software design of the harvesting robot control system mainly considers the control certainty and system openness. It adopts the programming environment of AVR Studio4. AVRStudio4 is a complete development tool, including editing and simulation functions. With this tool, you can edit the source code and run it on the AVR device. The control software of the harvesting robot system consists of the main program, servo motor drive subroutine, remote control receiving terminal program, sensor processing subroutine, DC motor control subroutine, etc.
The program mainly processes the AVR microcontroller I/O port, T/C (timer/counter), PWM speed regulation, interrupt processing, global variables, macro definitions, etc. The program adopts structured and modular writing ideas to achieve the best usability and readability of the program. By calling each subroutine, modifying the parameters such as the speed of the DC motor and the angle of the servo motor on the main program, the robot manipulator is debugged to the optimal angle, and the software design is carried out according to the control strategy. The main program flow chart is compiled as shown in Figure 4.
5 Debugging and testing of picking robots
The remote control simulation picking robot designed in this system is 1.2 m long and 0.38 m wide after extension. The maximum speed of the robot is 0.5 m/s and the maximum climbing angle is 45°. The longest remote control distance of the infrared remote control is 3 m. The robot arm movement is controlled by the servo. The servo of the robot arm is tested here. The angles of each servo are shown in Table 1. The test effect of the grabbing picture after the robot assembly test is completed is shown in Figure 5.
This robot adopts modular design, and each module has complementary functions, providing a variety of different picking modes. You can choose the appropriate mode for picking according to the working environment. At the same time, the functional module has good scalability and can be expanded through programming. At the same time, multiple tasks can work in parallel, which improves the picking efficiency.
6 Conclusion
This paper designs a picking robot based on ATmega32. The robot body uses strong and lightweight materials to ensure that the robot is light and stable. The robot is driven by a crawler chassis, and the double crawler bar structure is innovatively designed. The picking structure is designed with a two- and three-degree-of-freedom robotic arm, which can flexibly grab objects.
After entering the control program, the robot can achieve semi-autonomous control and infrared remote control through external sensors. The robot has two complementary picking modes: vibration shaking and one-by-one clamping. Actual tests show that this intelligent picking robot can complete the expected tasks well. The designed system is small in size and light in weight. Through experimental verification, the system has strong human-computer interaction capabilities, stable and reliable operation, flexible control and rapid response, and has achieved the expected design purpose. In particular, it has fast movement speed, agile movements, and can adapt to complex orchard environments. Its speed and stability have met the specified requirements. The robot has strong scalability, powerful functions, low cost, and has a certain reference value.
Of course, this is only an exploratory design for a picking robot, which is far from actual operation. In future research work, it is necessary to conduct in-depth research and improvement on the actual conditions such as the height of fruit trees, the size of fruits, and the fragility of fruits based on actual operations. If fully intelligent picking is used, machine vision must be added to feed the remote control robot platform with video monitoring modules based on the collected image information to guide the operation of the manipulator. The mechanical picking hand should also be designed with stress sensors to intelligently adjust the opening degree to avoid damaging the fruit.
Previous article:Design of pressure control system for deep sea environment simulation experimental device
Next article:Design of intelligent instrument based on ATmega162
Recommended ReadingLatest update time:2024-11-16 20:53
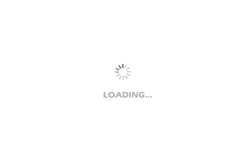
Professor at Beihang University, dedicated to promoting microcontrollers and embedded systems for over 20 years.
- Innolux's intelligent steer-by-wire solution makes cars smarter and safer
- 8051 MCU - Parity Check
- How to efficiently balance the sensitivity of tactile sensing interfaces
- What should I do if the servo motor shakes? What causes the servo motor to shake quickly?
- 【Brushless Motor】Analysis of three-phase BLDC motor and sharing of two popular development boards
- Midea Industrial Technology's subsidiaries Clou Electronics and Hekang New Energy jointly appeared at the Munich Battery Energy Storage Exhibition and Solar Energy Exhibition
- Guoxin Sichen | Application of ferroelectric memory PB85RS2MC in power battery management, with a capacity of 2M
- Analysis of common faults of frequency converter
- In a head-on competition with Qualcomm, what kind of cockpit products has Intel come up with?
- Dalian Rongke's all-vanadium liquid flow battery energy storage equipment industrialization project has entered the sprint stage before production
- Allegro MicroSystems Introduces Advanced Magnetic and Inductive Position Sensing Solutions at Electronica 2024
- Car key in the left hand, liveness detection radar in the right hand, UWB is imperative for cars!
- After a decade of rapid development, domestic CIS has entered the market
- Aegis Dagger Battery + Thor EM-i Super Hybrid, Geely New Energy has thrown out two "king bombs"
- A brief discussion on functional safety - fault, error, and failure
- In the smart car 2.0 cycle, these core industry chains are facing major opportunities!
- The United States and Japan are developing new batteries. CATL faces challenges? How should China's new energy battery industry respond?
- Murata launches high-precision 6-axis inertial sensor for automobiles
- Ford patents pre-charge alarm to help save costs and respond to emergencies
- New real-time microcontroller system from Texas Instruments enables smarter processing in automotive and industrial applications
- Pixel Pump, an open source vacuum pump using micropython
- Questions about PCF8583
- Answers to questions about programming the Lingdongwei MM32 MCU
- 16-bit MSP430G series microprocessor usage expansion
- [Reprint] STM32 drives VGA display to display IKS01A2 sensor data
- 555 timer frequency drift problem
- What should I pay attention to when making a boost circuit for a battery (without using a chip)?
- About the circuit components of TPS5405
- How to design RF circuits?
- Live broadcast entrance is now open: TI prize live broadcast | Application of precision ADC in transmitter