The temperature controller consists of three parts: temperature monitoring, signal processing, and output control. The system block diagram is shown in Figure 1. It obtains the winding temperature value through three platinum resistance sensors embedded in the three-phase winding of the transformer, and directly sends it to the A/D conversion input of the controller after being processed by the signal conditioning circuit. The microcontroller performs calculations and processing according to the signal data and various control parameters set, and according to the embedded software control rules, automatically displays the temperature value of the transformer winding, outputs the corresponding control signal, controls the start and stop of the fan, and outputs normal, alarm and trip signals according to the current state. At the same time, various data are transmitted to the host computer through RS-485 for centralized monitoring.
The control core of the temperature controller adopts ATmegal6 microcontroller, which is a low-power CMOS 8-bit microcontroller based on AVR RISC. It can execute one instruction in one clock cycle and can achieve 1MIPS/MHz performance, so it has real-time performance. The chip has 16KB FLASH and 512B E2PROM, which can temporarily store faults and over-temperature upper limit temperature values.


A/D conversion accuracy in ATmega16 is 10 bits. Since the reference voltage is 5V, the analog signal must be converted into a voltage of 0 to 5V. Therefore, when designing this circuit, the parameters of each component are designed according to this requirement. At the same time, its linearization must also be considered. In order to make the calculation in the software design linear, when designing the hardware, the temperature must be linearly changed with the digital quantity converted to the single-chip microcomputer. From the circuit, it can be seen that: From the formula

it can be seen that the obtained A/D conversion voltage is not proportional to Rw and does not meet the linear requirements. If it meets the requirements,

1.2 Output circuit
The output circuit is the embodiment of the calculation and control results of the analog-to-digital conversion value by the single-chip microcomputer, as shown in Figure 3. The control quantity output by the single-chip microcomputer is input to the JK port. If this signal is low level, the optocoupler device is turned on, turning on the CMOS transistor, so that the relay is energized, the normally open contact is closed, and the 220V voltage is output; otherwise, the output voltage is 0V.

The software adopts a modular structure, including 1 main module and 5 submodules (button processing submodule, digital quantum module for setting upper limit temperature and collecting boundary points, communication submodule, fault output processing submodule and display submodule). The main module completes the initialization of each submodule and calls the fault output processing submodule and display submodule. The button processing submodule, digital quantum module for setting upper limit temperature and collecting boundary points and communication module work in interrupt mode, and the main module communicates with them through a shared RAM area. Since the analog input signal of the single-chip microcomputer application system contains various noises and interferences, this program uses digital filtering technology to filter. In addition, for the linearization problem mentioned above, we divide 0~200℃ into four areas and perform linearization calculations in each area. This is much more accurate than directly calculating in the 0~200℃ area and can achieve an accuracy of 0.1℃.
The functions of each submodule are as follows:
(1) The button processing submodule applies for an interrupt to ATmega16 when a key is pressed, and modifies the pre-set flag in the interrupt subroutine. (2) Setting the upper limit temperature and collecting boundary points The digital quantum module can enter the interface for modifying the upper limit temperature by entering a password when the key is pressed for a long time. The digital quantities corresponding to 0℃, 50℃, 100℃, 150℃, and 200℃ are collected through the buttons, and the results are stored in the E2PROM. This data is used as the boundary point to calculate any temperature between 0 and 200℃. (3) The communication submodule can connect to the remote controlled object through the LBC184 (converts RS232 signals to RS485 signals) chip and the single-chip microcomputer for RS485 communication. (4) The fault output submodule can determine whether an abnormal situation occurs on site by comparing the actual temperature with the upper limit temperature. At the same time, the flag bit is set to determine whether to perform A/D conversion and whether to display. (5) The display submodule converts the results of the linear calculation from binary to BCD code and sends them to the 5-digit LED display for display.

(4) Conduct electromagnetic interference tests at the dry-type transformer operation site, conduct probability statistical analysis on the test results, and minimize the electromagnetic interference generated by the interference source by carefully selecting components and using hardware anti-interference technology and software anti-interference technology.
The temperature controller has low power consumption, advanced technology, complete functions, simple operation, reliable performance, and can work stably for a long time in very harsh electromagnetic interference or high temperature environments. It is an ideal monitoring device for dry-type transformers.
Previous article:Design of dry-type transformer intelligent controller system using ATmega16
Next article:AVR MCU Hardware/Software Co-simulation Using VMLAB
Recommended ReadingLatest update time:2024-11-16 21:30
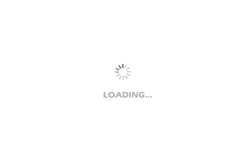
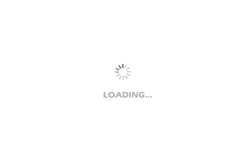
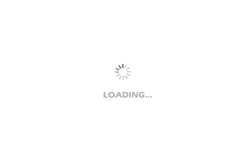
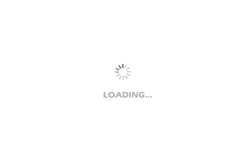
- Popular Resources
- Popular amplifiers
Professor at Beihang University, dedicated to promoting microcontrollers and embedded systems for over 20 years.
- Innolux's intelligent steer-by-wire solution makes cars smarter and safer
- 8051 MCU - Parity Check
- How to efficiently balance the sensitivity of tactile sensing interfaces
- What should I do if the servo motor shakes? What causes the servo motor to shake quickly?
- 【Brushless Motor】Analysis of three-phase BLDC motor and sharing of two popular development boards
- Midea Industrial Technology's subsidiaries Clou Electronics and Hekang New Energy jointly appeared at the Munich Battery Energy Storage Exhibition and Solar Energy Exhibition
- Guoxin Sichen | Application of ferroelectric memory PB85RS2MC in power battery management, with a capacity of 2M
- Analysis of common faults of frequency converter
- In a head-on competition with Qualcomm, what kind of cockpit products has Intel come up with?
- Dalian Rongke's all-vanadium liquid flow battery energy storage equipment industrialization project has entered the sprint stage before production
- Allegro MicroSystems Introduces Advanced Magnetic and Inductive Position Sensing Solutions at Electronica 2024
- Car key in the left hand, liveness detection radar in the right hand, UWB is imperative for cars!
- After a decade of rapid development, domestic CIS has entered the market
- Aegis Dagger Battery + Thor EM-i Super Hybrid, Geely New Energy has thrown out two "king bombs"
- A brief discussion on functional safety - fault, error, and failure
- In the smart car 2.0 cycle, these core industry chains are facing major opportunities!
- The United States and Japan are developing new batteries. CATL faces challenges? How should China's new energy battery industry respond?
- Murata launches high-precision 6-axis inertial sensor for automobiles
- Ford patents pre-charge alarm to help save costs and respond to emergencies
- New real-time microcontroller system from Texas Instruments enables smarter processing in automotive and industrial applications
- STM32F105RBT6
- Detailed explanation of ZigBee networking principle
- How to set up RTC and LPUART to work simultaneously when the HGI MCU is in deep sleep
- Some questions about starting xenon lamps
- FPGA design ideas finite state machine
- About high-end driver and low-end driver of MOS
- BlueNRG video tutorial: BlueNRG-1 Demo board introduction
- Problems with capacitors in snubber circuits
- [Topmicro Intelligent Display Module Review] 2. Power-on test
- Pingtouge Bluetooth Mesh Gateway Development Kit Trial Experience --- Mesh switch controls Mesh lights