1 Overview
Traditional car tachometers have two functions: one is to indicate the instantaneous speed of the car with a pointer, and the other is to record the accumulated mileage of the car with a mechanical counter. Modern cars are developing in the direction of high speed. As the speed of the car increases, the traditional speedometer driven by a flexible shaft is facing unprecedented challenges. This is because the flexible shaft is prone to breakage when rotating at high speed due to the limitation of the alternating stress limit of the steel wire. At the same time, if the flexible shaft is arranged too long, it will cause excessive deformation or motion hysteresis. Moreover, for different car models, the installation position of the tachometer will also be limited by the length and curvature of the flexible shaft. All these factors have led to the rapid development of electronic tachometers based on non-contact speed sensors.
2 Principle of mileage accumulation
The speed ratio of the speedometer indicates the number of revolutions of the speedometer shaft (flexible shaft) when the car travels one kilometer. The speedometer based on the single-chip microcomputer adopts a Hall-type non-contact speed sensor. For each revolution of the speedometer shaft, the Hall sensor will sense and send out 8 pulses. Now take the car with a speed ratio of 1:624 as an example? The car travels one kilometer? Then the number of pulses sent by the Hall sensor is 8×624=4992, or in other words, each pulse represents 1/4992 kilometers of mileage. These pulse signals are input to the single-chip microcomputer as external interrupt sources, so that each pulse generates an interrupt, and each pulse is counted through the interrupt service program. In this way, when the count reaches 4992, it means that the car has traveled 1 kilometer, and then the cumulative unit is added by one and stored in the EEPROM unit. Finally, the mileage counting function can be realized by refreshing the LCD display.
However
, it should be noted during programming that the external interrupt of the MCS-51 series microcontroller has two triggering modes, namely level triggering and edge triggering. This design uses the edge triggering mode, that is, the negative jump is used to cause the interrupt.
The speed indicator can use a double-coil automobile tachometer head, which consists of an air-shaft core and a drive circuit. The air-shaft core usually consists of three parts: a magnet, a pointer connected to the shaft, and two coils at 90 degrees to each other. The shaft is the only movable part of the core. The rotation angle of the magnet always tends to the synthetic direction of the magnetic field strength vector of the two coils. The magnetic field strength is proportional to the voltage applied to the coil. Therefore, by changing the polarity and amplitude of the voltage, the shaft assembly can theoretically rotate within the range of 0 to 360 degrees. Obviously, as long as the two coils can be driven according to a certain rule, the pointer deflection position can be linearly related to the input quantity, that is, the following formula is satisfied:
θ=KVinn
Where θ is the pointer deflection angle, in degrees; K is the angle constant, in degrees/V; Vin is the input voltage, in V.
The sum of the magnetic field strength vectors of each coil must follow the deflection angle θ. Considering that the shaft assembly always points to the direction of the sum of the two orthogonal vectors Hsine and Hcosine, its direction can be obtained by the following formula:
θ=arctan Hsine/Hcosine
And from this we can conclude:
θ=arctan sinθ/cosθ
It can be seen from the above formula that when Hsine changes according to the sine function of θ and Hcosine changes according to the cosine function of θ, the direction of the total magnetic field intensity obtained is the same as the direction of the angle θ. Since the direction of the shaft assembly is the same as the direction of the sum of the magnetic field intensity vectors, the pointer will always point to the direction of the angle θ.
Figure 1 shows the internal block diagram of the LM1819 driver, which consists of a charge pump, a shaper, a function generator, etc. The input speed signal is buffered by the internal triode and then input to the charge pump for F/V frequency voltage conversion. The two output terminals change according to the sine and cosine functions of the input quantity. The minimum driving capacity of pins 2 and 12 is ±20mA (±4V). The common end of the coil is connected to pin 1 to provide feedback signals for the internal function generator and provide reference voltage for the 5.1V Zener diode. In this circuit, K = 54°/V, and the input Vin is actually the potential difference between pins 4 and 8. Pin 8 is both the output of the Norton amplifier and the input of the function generator. Generally, the voltage of pin 4 is 2.1V, so:
θ=K(V8-Vref)=54(V8-2.1)
Since V8 varies in the range of 2.1V to 7.1V, LM1819 can drive the crosshead to rotate in the range of 0° to 270°
.
Figure 2 shows a circuit schematic diagram of a car tachometer. This is a typical single-chip microcomputer minimum application system. The single-chip microcomputer AT89C2051 is famous for its low price, low power consumption, high reliability and easy programming. X25045 is an auxiliary chip of the MCS-51 series single-chip microcomputer circuit, which mainly performs reset, voltage detection, watchdog and EEPROM functions. The use of this chip greatly improves the reliability of the system, reduces the number of peripheral chips, and can realize the power-off storage of mileage accumulation. LCM1010 is a ten-digit eight-segment LCD display module with backlight, using a three-wire serial interface. It has the characteristics of low power consumption and easy programming. The display is divided into two lines. The first line of 6 digits displays the accumulated mileage, and the second line of 4 digits (1 decimal place) is used to display the subtotal mileage. In the figure, K1 is the subtotal mileage reset key, and R4 is used to adjust the viewing angle contrast of the LCD display. The chip X25045 is a CMOS serial EEPROM with a programmable μP monitor launched by Xicor. It has 4096 bits and is organized as 512×8. It has a 4-byte page write mode and 100,000 use cycles, and the data can be stored for 100 years. In order to ensure the reliable refresh of the units of the cumulative mileage unit or the decimal places of the subtotal unit, when these units are close to the limit of the use cycle, the page change method can be adopted to move these data to the new unit to continue counting.
The pulse signal emitted by the Hall sensor can be divided into two paths after shaping. One path is sent to the INT1 end of the microcontroller for cumulative mileage counting, and the other path is sent to the speed signal input end (pin 10) of the LM1819 driver. Then the drive circuit outputs the corresponding sine and cosine drive signals at pins 2 and 12 according to the frequency of the input signal. The magnetic field generated by the cross coil acts on the magnet to deflect the shaft assembly to a corresponding angle. However, it should be noted that the size of capacitor C3 will change the smoothness of the needle deflection. The larger the C3, the better the smoothness, but at the same time the time delay will also increase. If C3 is too small, the needle will shake. C4 can be used to adjust the linearity and hysteresis error of the circuit. The value of R4 can change the indication scale point of the needle.
5 Conclusion
This design uses the single-chip microcomputer AT89C2051 to realize mileage accumulation, subtotal, clearing and storage, and uses the LM1819 integrated circuit to drive the cross coil meter head, thereby realizing the indication of vehicle speed. This design scheme has low cost, good pointer stability, fast response speed, strong shock resistance, high reliability and cost performance. It has been proved by actual use that this odometer can completely replace the traditional speedometer driven by a flexible shaft. Of course, this is only one implementation scheme. The cross coil meter head can also be driven by the single-chip microcomputer through software, that is, the single-chip microcomputer controls the sine coil and cosine coil of the meter head respectively, and the LM1819 integrated circuit is omitted. This will not be repeated here.
Previous article:51 single-chip computer password lock that can prevent multiple password attempts
Next article:Application of Information Button DS1991 in 51 Single Chip Microcomputer System
Recommended ReadingLatest update time:2024-11-16 22:23
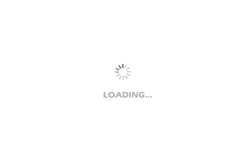
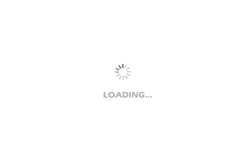
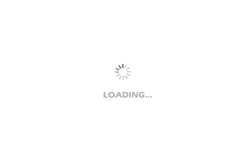
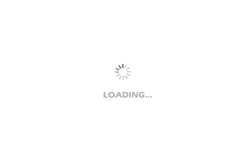
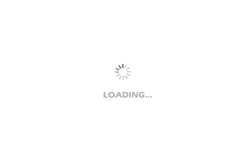
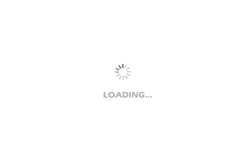
- Popular Resources
- Popular amplifiers
-
Siemens Motion Control Technology and Engineering Applications (Tongxue, edited by Wu Xiaojun)
-
Modern Product Design Guide
-
Modern arc welding power supply and its control
-
Small AC Servo Motor Control Circuit Design (by Masaru Ishijima; translated by Xue Liang and Zhu Jianjun, by Masaru Ishijima, Xue Liang, and Zhu Jianjun)
Professor at Beihang University, dedicated to promoting microcontrollers and embedded systems for over 20 years.
- Innolux's intelligent steer-by-wire solution makes cars smarter and safer
- 8051 MCU - Parity Check
- How to efficiently balance the sensitivity of tactile sensing interfaces
- What should I do if the servo motor shakes? What causes the servo motor to shake quickly?
- 【Brushless Motor】Analysis of three-phase BLDC motor and sharing of two popular development boards
- Midea Industrial Technology's subsidiaries Clou Electronics and Hekang New Energy jointly appeared at the Munich Battery Energy Storage Exhibition and Solar Energy Exhibition
- Guoxin Sichen | Application of ferroelectric memory PB85RS2MC in power battery management, with a capacity of 2M
- Analysis of common faults of frequency converter
- In a head-on competition with Qualcomm, what kind of cockpit products has Intel come up with?
- Dalian Rongke's all-vanadium liquid flow battery energy storage equipment industrialization project has entered the sprint stage before production
- Allegro MicroSystems Introduces Advanced Magnetic and Inductive Position Sensing Solutions at Electronica 2024
- Car key in the left hand, liveness detection radar in the right hand, UWB is imperative for cars!
- After a decade of rapid development, domestic CIS has entered the market
- Aegis Dagger Battery + Thor EM-i Super Hybrid, Geely New Energy has thrown out two "king bombs"
- A brief discussion on functional safety - fault, error, and failure
- In the smart car 2.0 cycle, these core industry chains are facing major opportunities!
- The United States and Japan are developing new batteries. CATL faces challenges? How should China's new energy battery industry respond?
- Murata launches high-precision 6-axis inertial sensor for automobiles
- Ford patents pre-charge alarm to help save costs and respond to emergencies
- New real-time microcontroller system from Texas Instruments enables smarter processing in automotive and industrial applications
- MSP430 upgrade boot program writing and upgrade firmware production
- Using FPGA to scan LED large screen.pdf
- I would like to ask about the random way, that is, writing the last 64 bytes of 24C256 by byte and writing its last 64 bytes by page.
- Leading with technology, sensing a new future. Download ams Semiconductor's "High-precision Short-distance Measurement Solution" and answer the questions to win prizes!
- Problems with thermistor constant temperature circuit built with op amp
- I really want to give up GoLang
- Digital tube driver advice
- [TI recommended course] #Boost and buck-boost DCDC converters help wireless charging design#
- How does the MCU in a drone work?
- About the cyclone soc network port printing link donw linkup problem