LED (Light Emitting Diode) is the fourth generation of light source, with great development prospects due to its advantages of energy saving, environmental protection and long life. However, because LED is extremely sensitive to temperature, the increase of junction temperature will affect the life, light efficiency, light color (wavelength), color temperature, light shape (light distribution), forward voltage, maximum injection current, luminosity, chromaticity, electrical parameters and reliability of LED. This paper analyzes in detail the impact of temperature increase on the optoelectronic parameters and reliability of LED, so as to facilitate the design and development of LED chips and LED lighting products.
1. Excessive temperature will cause permanent damage to LED
(1) When the operating temperature of LED exceeds the load temperature of the chip, the luminous efficiency of LED will decrease rapidly, resulting in obvious light decay and damage;
(2) LED is mostly encapsulated with transparent epoxy resin. If the junction temperature exceeds the solid phase transition temperature (usually 125℃), the encapsulation material will change to rubber and the thermal expansion coefficient will rise sharply, causing the LED to open circuit and fail.
2. Temperature increase will shorten the life of LED
. The life of LED is manifested in its light decay, that is, the brightness will become lower and lower over time until it finally goes out. The life of an LED is usually defined as the time it takes for the luminous flux of an LED to decay by 30%.
The following are the common causes of LED light decay:
(1) Defects in the LED chip material will rapidly multiply and proliferate at high temperatures until they invade the light-emitting area, forming a large number of non-radiative recombination centers, which seriously reduce the luminous efficiency
of the LED. In addition, under high temperature conditions, micro-defects in the material and fast-expanding impurities from the interface and the board will also be introduced into the light-emitting area, forming a large number of deep energy levels, which will also accelerate the light decay of the LED device [1].
(2) At high temperatures, transparent epoxy resin will denature and turn yellow, affecting its light transmission performance. The higher the operating temperature, the faster this process will proceed. This is another major cause of LED light decay.
(3) The light decay of phosphors is also a major cause of LED light decay, because phosphors decay very severely at high temperatures.
Therefore, high temperature is the main cause of LED light decay and shortening of LED life.
The light decay of LEDs of different brands is different. Usually, LED manufacturers will provide a set of standard light decay curves. For example, the light decay curve of Philips Lumiled's Luxeon K2 is shown in Figure 1. When the junction temperature increases from 115°C to 135°C, its life span will be shortened from 50,000 hours to 20,000 hours.
Figure 1 Lumiled Luxeon K2 light decay curve
The LED luminous flux attenuation caused by high temperature is irreversible. The luminous flux of the LED before irreversible luminous attenuation occurs is called the "initial luminous flux" of the LED.
3. Temperature increase will reduce the luminous efficiency of the LED
The reasons why temperature affects the luminous efficiency of the LED include the following:
(1) As the temperature increases, the concentration of electrons and holes will increase, the band gap width will decrease, and the electron mobility will decrease.
(2) As the temperature increases, the probability of radiative recombination of electrons and holes in the potential well decreases, resulting in non-radiative recombination (generating heat), thereby reducing the internal quantum efficiency of the LED [2]. (3) As the temperature increases, the
blue light peak of the chip shifts toward the long-wave direction, causing the emission wavelength of the chip and the excitation wavelength of the phosphor to not match, which will also cause the external light extraction efficiency of the white light LED to decrease [3].
(4) As the temperature rises, the quantum efficiency of the phosphor decreases, the light output decreases, and the external light extraction efficiency of the LED decreases.
(5) The performance of silicone is greatly affected by the ambient temperature. As the temperature increases, the thermal stress inside the silicone increases, resulting in a decrease in the refractive index of the silicone, thereby affecting the luminous efficiency of the LED.
In general, the effect of the luminous flux decreasing with the increase of junction temperature is reversible. That is to say, when the temperature returns to the initial temperature, the light output flux will have a restorative growth. This is because some relevant parameters of the material will change with temperature, which will cause changes in the parameters of the LED device and affect the light output of the LED. When the temperature returns to the initial state, the changes in the parameters of the LED device disappear, and the LED light output will also return to the initial state value. In this regard, the luminous flux value of the LED is divided into "cold lumen" and "hot lumen", which respectively represent the light output of the LED when the LED node is at room temperature and a certain temperature.
In general, the relationship between the LED luminous flux and the junction temperature can be expressed by formula (1):
(1)
Among them,
represents
the luminous flux (lm) at a junction temperature of ;
represents
the luminous flux (lm) at a junction temperature of ;
is the temperature coefficient (1/℃);
is the difference in LED junction temperature, that is
.
In general, the value can be determined experimentally. For example, the relevant values for InGaAlP-based LEDs are shown in Table 1.
LED material category |
Temperature coefficient (1/℃) |
InGaAlP/GaAs orange-red |
9.52×10-3 |
InGaAlP/GaAs Yellow |
1.11×10-2 |
InGaAlP/GaP High Brightness Red |
9.52×10-3 |
InGaAlP/GaP Yellow |
9.52×10-2 |
Table 1 Temperature coefficients of LEDs of different material types
Figure 2: The relationship between the light output (percentage) of LEDs with different k values and the junction temperature
As can be seen from Figure 2: the temperature coefficient k of LED light efficiency is preferably below 2.0×10-3, so that the reduction of LED light output caused by temperature will not be very large. For example, the k value of InGaN LED is about 1.2×10-3, and the light output is about 11% lower when the junction temperature is 125℃ relative to the junction temperature of 25℃.
At present, the temperature coefficients of the most used GaN-based white light LEDs are mostly between 2.0×10-3 and 4.0×10-3, and some even reach 5.0×10-3. For LEDs with large k values, more attention should be paid to controlling the junction temperature.
4. The influence of temperature on the wavelength (light color) of LED light emission
The wavelength of LED light emission can generally be divided into peak wavelength and main wavelength. The peak wavelength is the wavelength with the highest light intensity, while the main wavelength can be determined by the X and Y chromaticity coordinates, reflecting the color perceived by the human eye. Obviously, the change in the wavelength of LED light emission caused by the junction temperature will directly cause the human eye to feel differently about the color of LED light emission. For an LED device, the bandgap width value of the material in the light-emitting area directly determines the wavelength or color of the device's light emission. As the temperature rises, the bandgap width of the material will decrease, causing the wavelength of the device to become longer and the color to red shift.
The change in wavelength with junction temperature can usually be expressed as formula (2):
Among them:
represents
the wavelength at junction temperature (nm);
represents
the wavelength at junction temperature (nm);
represents the coefficient of wavelength change with temperature, generally between 0.1 and 0.3nm/K;
.
5. The influence of temperature on LED forward voltage
Forward voltage is an important parameter for determining LED performance, and its magnitude depends on the characteristics of semiconductor materials, chip size, and device junction and electrode manufacturing processes. For a forward current of 20 mA, the forward voltage of InGaAlP LEDs is usually between 1.8 and 2.2 V, and the forward voltage of InGaN LEDs is between 3.0 and 3.5 V. Under the small current approximation, the forward voltage drop of LED devices can be expressed by formula (3):
(3)
In the formula,
is the forward voltage,
is the forward current,
is the reverse saturation current,
is the electron charge,
is the Boltzmann constant,
is the series resistance,
is a parameter that characterizes the perfection of the P/N junction, and is between 1 and 2. On the right side of formula (3), only the reverse saturation current
is closely related to temperature, and
its value increases with the increase of junction temperature, resulting in
a decrease in the forward voltage value. Experiments show that when the input current is constant, for a certain LED device, the relationship between the forward voltage drop at both ends and the temperature can be expressed by formula (4):
(4)
In formula (4),
and
respectively represent
the forward voltage drop when
the
junction temperature is and ,
which is the coefficient of voltage drop variation with temperature, generally between -1.5 and -2.5 mV/K;
.
When the current is fixed, the temperature rises and the LED forward voltage decreases. Since the relationship between forward voltage and temperature is close to linear, most LED thermal resistance test instruments use this characteristic of LED to measure its thermal resistance or junction temperature.
6. Excessive temperature will limit the maximum injection current of the LED
As the temperature increases, the bandgap of the material will decrease, resulting in a decrease in the maximum injected current.
Figure 3 Relationship between maximum injection current and junction temperature of Cree 3WXLampXP-E
In addition, temperature also affects the light distribution curve, color temperature and color rendering of LED.
Temperature affects the refractive index of the light-transmitting material, which will change the spatial distribution of the light emitted by the LED, that is, the light distribution curve.
When the temperature is too high, the blue light peak shifts, and the phosphor peak becomes flat and degrades, which will cause the LED color temperature to be high and the color rendering to deteriorate [4].
VII. Summary
Due to the high heat generation, high-power LEDs have high operating temperatures and their performance drops sharply. Only by deeply understanding the temperature characteristics of LEDs and developing low thermal resistance LED chips and LED application products can the superiority of LEDs be truly reflected.
Previous article:Design and analysis of heat sink based on LED lighting fixtures
Next article:LED lighting protection solutions based on Littelfuse
Recommended ReadingLatest update time:2024-11-17 00:29
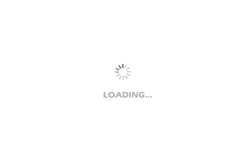
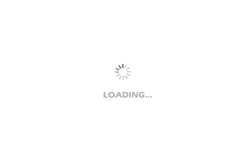
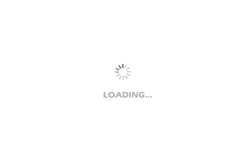
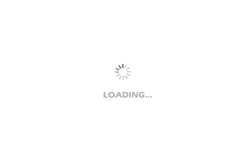
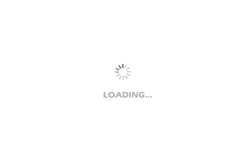
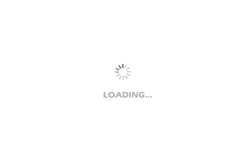
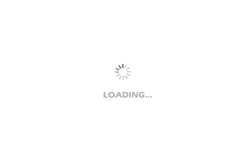
- Popular Resources
- Popular amplifiers
- MathWorks and NXP Collaborate to Launch Model-Based Design Toolbox for Battery Management Systems
- STMicroelectronics' advanced galvanically isolated gate driver STGAP3S provides flexible protection for IGBTs and SiC MOSFETs
- New diaphragm-free solid-state lithium battery technology is launched: the distance between the positive and negative electrodes is less than 0.000001 meters
- [“Source” Observe the Autumn Series] Application and testing of the next generation of semiconductor gallium oxide device photodetectors
- 采用自主设计封装,绝缘电阻显著提高!ROHM开发出更高电压xEV系统的SiC肖特基势垒二极管
- Will GaN replace SiC? PI's disruptive 1700V InnoMux2 is here to demonstrate
- From Isolation to the Third and a Half Generation: Understanding Naxinwei's Gate Driver IC in One Article
- The appeal of 48 V technology: importance, benefits and key factors in system-level applications
- Important breakthrough in recycling of used lithium-ion batteries
- Innolux's intelligent steer-by-wire solution makes cars smarter and safer
- 8051 MCU - Parity Check
- How to efficiently balance the sensitivity of tactile sensing interfaces
- What should I do if the servo motor shakes? What causes the servo motor to shake quickly?
- 【Brushless Motor】Analysis of three-phase BLDC motor and sharing of two popular development boards
- Midea Industrial Technology's subsidiaries Clou Electronics and Hekang New Energy jointly appeared at the Munich Battery Energy Storage Exhibition and Solar Energy Exhibition
- Guoxin Sichen | Application of ferroelectric memory PB85RS2MC in power battery management, with a capacity of 2M
- Analysis of common faults of frequency converter
- In a head-on competition with Qualcomm, what kind of cockpit products has Intel come up with?
- Dalian Rongke's all-vanadium liquid flow battery energy storage equipment industrialization project has entered the sprint stage before production
- Allegro MicroSystems Introduces Advanced Magnetic and Inductive Position Sensing Solutions at Electronica 2024
- Car key in the left hand, liveness detection radar in the right hand, UWB is imperative for cars!
- After a decade of rapid development, domestic CIS has entered the market
- Aegis Dagger Battery + Thor EM-i Super Hybrid, Geely New Energy has thrown out two "king bombs"
- A brief discussion on functional safety - fault, error, and failure
- In the smart car 2.0 cycle, these core industry chains are facing major opportunities!
- The United States and Japan are developing new batteries. CATL faces challenges? How should China's new energy battery industry respond?
- Murata launches high-precision 6-axis inertial sensor for automobiles
- Ford patents pre-charge alarm to help save costs and respond to emergencies
- New real-time microcontroller system from Texas Instruments enables smarter processing in automotive and industrial applications
- Comparison of technical indicators between N76E003AT20 and STM8S003F3P6
- 51 drives ST7920 to display custom size characters at any position. I don't know why it flashes when refreshing. Please guide me
- Guess the idiom
- Comparison of C55x DSP EMIF and C6000 DSP EMIF
- CCS variable observer problem
- Electromagnetic interference is no small matter, EMI prize survey is launched!
- Compile and run the button routine for the i.MX6ULL development board
- [GD32L233C-START Review] On-chip temperature detection and display
- [NXP Rapid IoT Review] Rapid IoT Studio Simple Programming Step 4 Add Bluetooth RGB Light Control
- [ESK32-360 Review] + LCD library function BUG review feedback