As the cost of producing LEDs decreases, their use becomes more common, covering applications ranging from handheld devices to automotive to architectural lighting. The high reliability (lifetime of more than 50,000 hours), high efficiency (>120 lumens/watt), and near-instantaneous response of LEDs make them an extremely attractive light source. Compared with the 200mS response time of incandescent bulbs, LEDs emit light in just 5ns. As a result, they are now widely used in brake lights in the automotive industry.
China Lighting Network Technical Papers · LED TechnologyDriving LEDs
Driving LEDs is not without its challenges. Adjustable brightness requires driving the LED with a constant current, and that current must remain constant regardless of the input voltage. This is more challenging than simply connecting an incandescent bulb to a battery to power it.
LEDs have a forward VI characteristic similar to that of a diode. Below the LED turn-on threshold (about 3.5V for white LEDs), the current through the LED is very small. Above this threshold, the current increases exponentially as a function of the forward voltage. This allows the LED to be modeled as a voltage source with a series resistor, with a caveat: this model is only valid for a single operating DC current. If the DC current in the LED changes, the model's resistor should also change to reflect the new operating current. At large forward currents, the power dissipated in the LED causes the device to heat up, which changes the forward voltage drop and dynamic impedance. It is important to consider the thermal environment when determining the LED impedance. When
driving an LED through a buck regulator, the LED often conducts the inductor's AC ripple current and the DC current, depending on the output filter arrangement chosen. This not only increases the RMS amplitude of the current in the LED, but also increases its power dissipation. This can increase the junction temperature and have a significant impact on the LED's lifetime. If we set a 70% light output limit as the LED life, the LED life will be extended from 15,000 hours at 74 degrees Celsius to 40,000 hours at 63 degrees Celsius. The power loss of the LED is determined by the LED resistance times the square of the RMS current plus the average current times the forward voltage drop. Since the junction temperature is determined by the average power dissipation, even large ripple currents have little effect on the power dissipation. For example, in a buck converter, a peak-to-peak ripple current equal to the DC output current (Ipk-pk=Iout) will add no more than 10% to the total power loss. If the above loss levels are exceeded, the AC ripple current from the power supply needs to be reduced to keep the junction temperature and operating life the same. A very useful rule of thumb is that for every 10 degrees Celsius reduction in junction temperature, the semiconductor life will double. In practice, most designs tend to have lower ripple currents due to the damping effect of the inductor. In addition, the peak current in the LED should not exceed the manufacturer's maximum safe operating current rating.
Topology selection
The information shown in Table 1 helps you choose the best switching topology for your LED driver. In addition to these topologies, you can also use simple current limiting resistors or linear regulators to drive LEDs, but such methods usually waste too much power. All relevant design parameters include input voltage range, number of LEDs driven, LED current, isolation, EMI suppression, and efficiency. Most LED driver circuits belong to the following topology types: buck, boost, buck-boost, SEPIC, and flyback topologies.
Table 1 Alternative LED power supply topologies
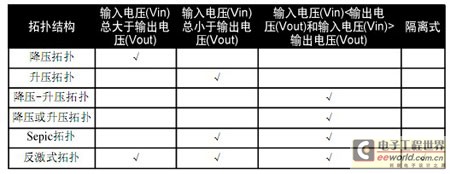
Figure 1 shows three basic examples of power supply topologies. The first schematic shows a buck regulator that is suitable for situations where the output voltage is always less than the input voltage. In Figure 1, the buck regulator controls the current into the LED by varying the on-time of the MOSFET. Current sensing can be achieved by measuring the voltage across a resistor that should be in series with the LED. The important design challenge for this approach is how to drive the MOSFET. From a cost-effective point of view, it is recommended to use an N-channel field effect transistor (FET) that requires a floating gate drive. This requires a drive transformer or a floating drive circuit that can be used to maintain an internal voltage higher than the input voltage.
Figure 1 also shows an alternative step-down regulator (buck #2). In this circuit, the MOSFET drives ground, greatly reducing the drive circuit requirements. The circuit has the option of sensing the LED current by monitoring the FET current or a current sense resistor in series with the LED. The latter requires a level shift circuit to obtain information about the power supply ground, but this can complicate a simple design. Alternatively, Figure 1 shows a boost converter that can be used when the output voltage is always greater than the input voltage. This topology is easy to design because the MOSFET drives ground and the current sense resistor is also ground referenced. One drawback of this circuit is that during a short circuit, the current through the inductor is unlimited. You can add fault protection in the form of fuses or electronic circuit breakers. In addition, some more complex topologies can also provide such protection.
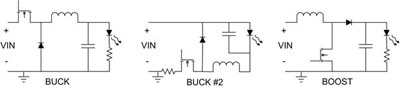
Figure 1 Simple buck and boost topologies for powering LEDs
Figure 2 shows two buck-boost circuits that can be used when the input voltage is higher or lower than the output voltage. Both have the same trade-off characteristics (the trade-offs are shown in the two buck topologies regarding the location of the current sense resistor and the gate drive). The buck-boost topology in Figure 2 shows a ground-referenced gate drive. It requires a level-shifted current sense signal, but the inverting buck-boost circuit has a ground-referenced current sense and a level-shifted gate drive. If the control IC is associated with the negative output, and the current sense resistor and LED are swappable, then the inverting buck-boost circuit can be configured in a very useful way. With the appropriate control IC, the output current can be measured directly, and the MOSFET can be driven directly.
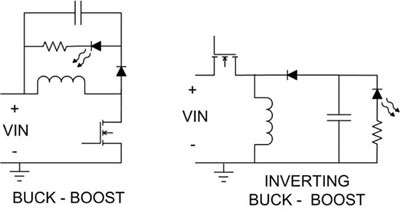
Figure 2 The buck-boost topology can regulate input voltages greater or less than Vout
One drawback of the buck-boost approach is that the currents are quite high. For example, when the input and output voltages are the same, the inductor and power switch currents are twice the output current. This can negatively impact efficiency and power consumption. In many cases, the “buck or boost” topology in Figure 3 will alleviate these issues. In this circuit, a buck power stage is followed by a boost. If the input voltage is higher than the output voltage, the buck stage regulates while the boost stage is just powered on. If the input voltage is less than the output voltage, the boost stage regulates while the buck stage is powered on. It is common to allow for some overlap between the boost and buck operation, so there is no deadband when going from one model to the other.
The benefit of this circuit is that the switch and inductor currents are nearly equal to the output current when the input and output voltages are nearly equal. The inductor ripple current also tends to be smaller. Even though there are four power switches in this circuit, efficiency is usually significantly improved, which is critical in battery applications. The SEPIC topology is also shown in Figure 3, which requires fewer FETs but more passive components. The benefit is a simple ground-referenced FET driver and control circuit. In addition, the dual inductors can be combined into a single coupled inductor, saving space and cost. But like the buck-boost topology, it has higher switch currents than the "buck or boost" and pulsating output currents, which requires capacitors that can carry larger RMS currents.
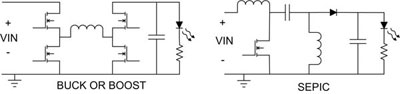
Figure 3 Buck or boost and SEPIC topologies offer higher efficiency
Safety considerations may dictate the use of isolation between the offline voltage and the output voltage. In this application, the most cost-effective solution is the flyback converter (see Figure 4). It requires the least number of components of all the isolation topologies. The transformer turns ratio can be designed for buck, boost, or buck-boost output voltages, which provides great design flexibility. However, the disadvantage is that the power transformer is usually a custom component. In addition, there is high component stress in the FETs and input and output capacitors. In steady-state lighting applications, the power factor correction (PFC) function can be implemented by using a "slow" feedback control loop that regulates the LED current in phase with the input voltage. A high power factor is achieved by regulating the desired average LED current and the input current in phase with the input voltage.
Figure 4 A flyback converter provides both isolation and power factor correction.
Dimming Technology
It is not uncommon to need to dim LEDs. For example, you may need to dim a display or adjust the brightness of an architectural light. There are two ways to do this: either reduce the LED current or turn the LED on and off quickly and then let the eye eventually balance. Because light output is not completely linear with current, reducing current is the least efficient method. In addition, the LED color spectrum will generally change at currents below the rated value. Remember that human perception of brightness is exponential, so dimming requires a larger percentage change in current. This has a significant impact on circuit design because a 3% regulation error at full current can magnify into a 30% or more error at 10% load due to circuit tolerances. Although there are response speed issues, regulating current through pulse width modulation (PWM) is still more accurate. When lighting and displaying, PWM above 100Hz is required to make the human eye not notice the flicker. The 10% pulse width is in the millisecond range and requires a power supply with a bandwidth of more than 10kHz.
in conclusion
As shown in Table 2, the use of LEDs in many applications is becoming increasingly common. It will use a variety of power supply topologies to support these applications. Generally, the input voltage, output voltage and isolation requirements will dictate the correct choice. When the input voltage is always higher or lower than the output voltage, using a buck or boost may be the obvious choice. However, when the relationship between the input and output voltages is not so constrained, the choice becomes more difficult and requires weighing many factors, including efficiency, cost and reliability.
Table 2 Many LED applications specify multiple power supply topologies
Previous article:Ultra-bright LED drive circuit design
Next article:Power, protection and networking solutions for LED area lighting applications
Recommended ReadingLatest update time:2024-11-16 18:09
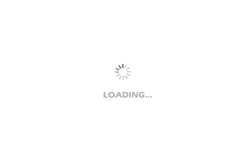
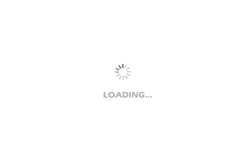
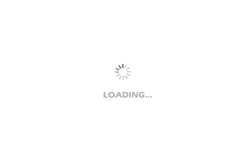
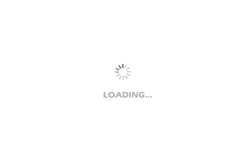
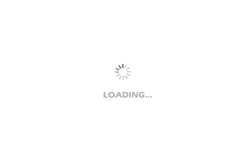
- Popular Resources
- Popular amplifiers
- MathWorks and NXP Collaborate to Launch Model-Based Design Toolbox for Battery Management Systems
- STMicroelectronics' advanced galvanically isolated gate driver STGAP3S provides flexible protection for IGBTs and SiC MOSFETs
- New diaphragm-free solid-state lithium battery technology is launched: the distance between the positive and negative electrodes is less than 0.000001 meters
- [“Source” Observe the Autumn Series] Application and testing of the next generation of semiconductor gallium oxide device photodetectors
- 采用自主设计封装,绝缘电阻显著提高!ROHM开发出更高电压xEV系统的SiC肖特基势垒二极管
- Will GaN replace SiC? PI's disruptive 1700V InnoMux2 is here to demonstrate
- From Isolation to the Third and a Half Generation: Understanding Naxinwei's Gate Driver IC in One Article
- The appeal of 48 V technology: importance, benefits and key factors in system-level applications
- Important breakthrough in recycling of used lithium-ion batteries
- Innolux's intelligent steer-by-wire solution makes cars smarter and safer
- 8051 MCU - Parity Check
- How to efficiently balance the sensitivity of tactile sensing interfaces
- What should I do if the servo motor shakes? What causes the servo motor to shake quickly?
- 【Brushless Motor】Analysis of three-phase BLDC motor and sharing of two popular development boards
- Midea Industrial Technology's subsidiaries Clou Electronics and Hekang New Energy jointly appeared at the Munich Battery Energy Storage Exhibition and Solar Energy Exhibition
- Guoxin Sichen | Application of ferroelectric memory PB85RS2MC in power battery management, with a capacity of 2M
- Analysis of common faults of frequency converter
- In a head-on competition with Qualcomm, what kind of cockpit products has Intel come up with?
- Dalian Rongke's all-vanadium liquid flow battery energy storage equipment industrialization project has entered the sprint stage before production
- Allegro MicroSystems Introduces Advanced Magnetic and Inductive Position Sensing Solutions at Electronica 2024
- Car key in the left hand, liveness detection radar in the right hand, UWB is imperative for cars!
- After a decade of rapid development, domestic CIS has entered the market
- Aegis Dagger Battery + Thor EM-i Super Hybrid, Geely New Energy has thrown out two "king bombs"
- A brief discussion on functional safety - fault, error, and failure
- In the smart car 2.0 cycle, these core industry chains are facing major opportunities!
- The United States and Japan are developing new batteries. CATL faces challenges? How should China's new energy battery industry respond?
- Murata launches high-precision 6-axis inertial sensor for automobiles
- Ford patents pre-charge alarm to help save costs and respond to emergencies
- New real-time microcontroller system from Texas Instruments enables smarter processing in automotive and industrial applications
- MSP430F149 serial RS485 interface
- Optocoupler replacement
- Working principle of photoelectric encoder
- FPGA controls TMS320C6678 power-on reset program
- Lee Kun-hee, chairman of South Korea's Samsung, has passed away. How do you evaluate his life?
- RTT & Renesas high performance CPK-RA6M4 development board review - SPI driven OLED
- 【TGF4042 signal generator】+6th issue pwm modulation
- Free benefits: One-click download of premium sensor data without points required!
- Building a GDB remote debugging environment under TMS320DM8168
- Microwave Engineering