In recent years, with the rapid development of LED production technology, the brightness of light has been improved and the life span has been extended. In addition, the production cost has been greatly reduced, which has rapidly expanded the LED application market, such as consumer products, signal systems and general lighting. As a result, the global market size has grown rapidly. In 2003, the global LED market was approximately US$4.48 billion (the high-brightness LED market was approximately US$2.7 billion), an increase of 17.3% over 2002 (the high-brightness LED market grew by 47%). Riding on the continued growth of the mobile phone market, it is predicted that there will still be a 14.0% growth rate in 2004.
At present, the white light LED used in the backlight of mobile phones, digital cameras, PDAs, etc. is made of a blue light single chip plus YAG fluorescence. With the increasing application of mobile phone flash, large and medium-sized (NB, LCD-TV, etc.) display screen light source modules and special-purpose lighting systems, it will be expanded to general lighting system equipment in the future. The high-power (HighPower) LED market using white light LED technology will gradually emerge. In terms of technology, the biggest challenge currently encountered is to improve and maintain brightness. If its heat dissipation capacity is further enhanced, the market development has great potential.
ASM has more than 20 years of experience in the development and production of automated optoelectronic component packaging equipment. There are many ways to improve LED brightness in the industry. From the chip and packaging design to the packaging process, the goal is to improve heat dissipation and increase luminous efficiency. In this article, the latest developments and achievements of LED packaging technology are summarized and discussed.
Chip Design
From the evolution of chips, it is found that major LED manufacturers have continuously improved their upstream epitaxial technology, such as using different electrode designs to control current density, using ITO thin film technology to evenly distribute the current passing through the LED, etc., so that the LED chip can generate as many photons as possible in terms of structure. Then various methods are used to extract each photon emitted by the LED, such as producing chips with different shapes; using the chip periphery to effectively control the light refraction to improve the light extraction efficiency of the LED, developing and expanding the surface size of a single chip (>2mm2) to increase the light-emitting area, and using rough surfaces to increase the light transmission, etc. On some high-brightness LED chips, the positions of the pn electrodes are closer, which improves the chip's luminous efficiency and heat dissipation capacity. Recently, the production of high-power LEDs has been carried out by using newly improved laser lift-off and metal bonding technology to remove the LED epitaxial wafer from the GaAs or GaN crystal growth substrate and bond it to another metal substrate or other materials with high reflectivity and high thermal conductivity, helping high-power LEDs improve their light extraction efficiency and heat dissipation capacity.
Package Design
After years of development, vertical LED lamps (φ3mm, φ5mm) and SMD lamps (surface mount LED) have evolved into a standard product model. However, with the development and needs of chips, high-power package product designs have been developed. In order to use automated assembly technology to reduce manufacturing costs, high-power SMD lamps have also come into being. Moreover, driven by the rapid development of the portable consumer product market, the volume design of high-power LED packages has become smaller and thinner to provide a wider product design space.
In order to maintain the brightness of the finished product after packaging, the newly improved high-power SMD device has a cup-shaped reflective surface inside, which helps to uniformly reflect all the light out of the package to increase the output lumen. The round optical lens covering the LED is changed to use silicone sealing glue instead of epoxy resin in the past, so that the package can maintain a certain durability.
Packaging technology and solutions
The main purpose of semiconductor packaging is to ensure the correct electrical and mechanical connection between the semiconductor chip and the underlying circuit, and to protect the chip from mechanical, thermal, humid and other external impacts. When selecting packaging methods, materials and machines, factors such as the shape of the LED epitaxial, electrical/mechanical characteristics and die bonding accuracy must be considered. Because LEDs have their own optical properties, packaging must also consider and ensure that their optical properties can be met.
Whether it is vertical LED or SMD packaging, a high-precision die bonder must be selected, because the accuracy of the position of the LED chip in the package directly affects the luminous efficiency of the entire package device. As shown in Figure 1, if the position of the chip in the reflector cup is deviated, the light cannot be fully reflected, affecting the brightness of the finished product. However, if a die bonder has an advanced pre-image recognition system (PRSystem), even if the quality of the lead frame is uneven, it can still be accurately welded to the predetermined position in the reflector cup.
Generally, low-power LED devices (such as indicator devices and mobile phone keyboard lighting) are mainly bonded with silver paste. However, since silver paste itself cannot withstand high temperatures, while increasing brightness, heat will also occur, thus affecting the product. To obtain high-quality and high-power LEDs, new bonding processes have been developed. One of them is to use eutectic welding technology, first welding the chip to a heat sink or heat sink, and then welding the entire chip to the heat sink and then to the package device. This can enhance the heat dissipation capacity of the device and increase the luminous power relatively. As for substrate materials, silicon, copper and ceramic are commonly used heat dissipation substrate materials.
Eutectic welding
The key to the technology is the selection of eutectic materials and the control of welding temperature. For the new generation of InGaN high-brightness LEDs, if eutectic welding is used, the bottom of the chip can be coated with pure tin (Sn) or gold-tin (Au-Sn) alloy as the contact surface, and the chip can be welded on a substrate plated with gold or silver. When the substrate is heated to a suitable eutectic temperature (Figure 5), gold or silver elements penetrate into the gold-tin alloy layer. The change in the composition of the alloy layer increases the melting point, causing the eutectic layer to solidify and the LED to be firmly welded to the heat sink or substrate (Figure 6). Selecting the eutectic temperature The degree depends on the heat resistance of the chip, substrate and device materials and the temperature requirements of the subsequent SMT reflow process. When considering the eutectic bonding machine, in addition to high position accuracy, another important condition is flexible and stable temperature control. The addition of nitrogen or mixed gas devices will help to provide anti-oxidation protection during the eutectic process. Of course, like silver paste bonding, to achieve high-precision bonding, it depends on rigorous mechanical design and high-precision motor movement, so that the welding head movement and welding force control can be just right without compromising the requirements of high production capacity and high yield rate.
Flux can also be added during the eutectic soldering process. The biggest feature of this technology is that no additional soldering force is required, so there will be no excessive eutectic alloy overflow due to excessive soldering force, reducing the chance of LED short circuit.
FlipChip welding
In recent years, flip chip welding has been actively used in the high-power LED process. The flip chip method reversely bonds the GaNLED chip to the heat sink substrate. Because there is no gold wire pad obstruction, it helps to improve the brightness. Because the distance of current flow is shortened and the resistance is reduced, the heat generation is relatively reduced. At the same time, such a connection can also effectively transfer the heat to the next layer of the heat sink substrate and then to the outside of the device. When this process is applied to SMDLED, it not only improves the light output, but also reduces the overall area of the product and expands the product's application market.
There are two main solutions for the development of flip-chip LED technology: one is solder bump reflow technology; the other is thermosonic welding technology. Solder bump reflow (Figure 10) has been used in IC packaging for a long time, and the process technology is mature, so it will not be described in detail here.
For the production of low-cost and low-line devices, the Thermosonic flip chip technology (Figure 11) is particularly suitable for high-power LED welding. Gold is used as the welding interface. Since the melting point of gold itself is higher than that of lead solder balls and silver paste, it is more flexible in the process design after solid crystal. In addition, it has the advantages of lead-free process, simple process, and reliable metal connection. After years of research and experience accumulation, the Thermosonic flip chip process has mastered the optimized process parameters and has been successfully put into mass production by several major LED manufacturers.
Except for the equipment that is sufficient for the production line, the rest of the automation equipment (such as chip bonding machines, lead welding machines, test machines, and taping machines) are all imported.
Specific suggestions for developing my country's LDD equipment industry
It is suggested that the country should support the development of LED technology and industry by taking materials and process equipment as the foundation and driving force of development. In the process of developing LED technology and industry, it is suggested that my country should follow the path of introduction, digestion, absorption, innovation and improvement. The specific plan is as follows: With the support of the state, a tripartite alliance among the state, LED production enterprises and equipment and material manufacturing industries will be established to establish a Chinese LED equipment, material, manufacturing and application consortium with incubator function.
In order to master and improve the level of equipment manufacturing in a short period of time and drive the development of my country's medium and high-end LED industry, it is recommended that the consortium jointly raise funds (50% from the state, 15% from equipment research units, 15% from chip manufacturing and packaging technology research units, and 20% from LED chip manufacturing and packaging companies) to build a complete LED chip manufacturing and packaging demonstration production line. The demonstration line is responsible for solving equipment development and process testing, LED product manufacturing process technology research and verification, and realizing the complete supply of process technology and process equipment. All units participating in the demonstration construction have the right to use the production line free of charge to conduct related product, technology and industrialization research and testing. In particular, LED product production units can obtain relevant research and industrialization results with priority and preferential treatment.
For this demonstration line, a three-step strategy will be implemented to eventually realize the commercialization and localization of LED production equipment (see Table 2 of the equipment localization plan for details). Step 1: Use about two years to localize some key equipment (the state will provide certain bonus support); for ordinary equipment that already has a certain foundation in China and has cost-effective advantages, the market competition principle will be used to adopt an access system to select the best equipment (through the formulation of standards); for some equipment that is difficult to localize in the short term, the state should arrange for research and development, and complete the development of production-type ɑ prototypes. Step 2: Starting from the third year of the implementation of this plan, the first two types of equipment involved in the first step will focus on solving problems such as adaptability of production processes, production efficiency, reliability, appearance and cost, and have domestic matching and batch supply capabilities. The research and development equipment will complete the commercialization of production prototypes (γ-type machines). Step 3: Starting from the fifth year of the implementation of this plan, all equipment involved in the first and second steps will have international competitiveness. In addition to meeting domestic demand, they must occupy a certain international market; the research and development equipment can meet the requirements of industrialized production and have batch supply capabilities.
Previous article:Discussion on LED Packaging Innovation for Lighting
Next article:Introduction to the Growth Process of LED Epitaxial Wafers
Recommended ReadingLatest update time:2024-11-16 17:36
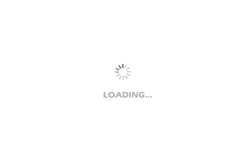
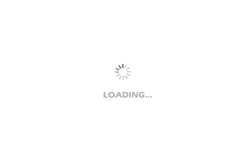
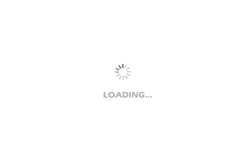
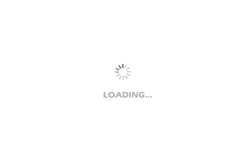
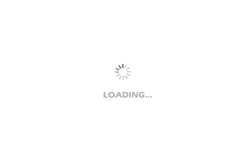
- Popular Resources
- Popular amplifiers
- MathWorks and NXP Collaborate to Launch Model-Based Design Toolbox for Battery Management Systems
- STMicroelectronics' advanced galvanically isolated gate driver STGAP3S provides flexible protection for IGBTs and SiC MOSFETs
- New diaphragm-free solid-state lithium battery technology is launched: the distance between the positive and negative electrodes is less than 0.000001 meters
- [“Source” Observe the Autumn Series] Application and testing of the next generation of semiconductor gallium oxide device photodetectors
- 采用自主设计封装,绝缘电阻显著提高!ROHM开发出更高电压xEV系统的SiC肖特基势垒二极管
- Will GaN replace SiC? PI's disruptive 1700V InnoMux2 is here to demonstrate
- From Isolation to the Third and a Half Generation: Understanding Naxinwei's Gate Driver IC in One Article
- The appeal of 48 V technology: importance, benefits and key factors in system-level applications
- Important breakthrough in recycling of used lithium-ion batteries
- Innolux's intelligent steer-by-wire solution makes cars smarter and safer
- 8051 MCU - Parity Check
- How to efficiently balance the sensitivity of tactile sensing interfaces
- What should I do if the servo motor shakes? What causes the servo motor to shake quickly?
- 【Brushless Motor】Analysis of three-phase BLDC motor and sharing of two popular development boards
- Midea Industrial Technology's subsidiaries Clou Electronics and Hekang New Energy jointly appeared at the Munich Battery Energy Storage Exhibition and Solar Energy Exhibition
- Guoxin Sichen | Application of ferroelectric memory PB85RS2MC in power battery management, with a capacity of 2M
- Analysis of common faults of frequency converter
- In a head-on competition with Qualcomm, what kind of cockpit products has Intel come up with?
- Dalian Rongke's all-vanadium liquid flow battery energy storage equipment industrialization project has entered the sprint stage before production
- Allegro MicroSystems Introduces Advanced Magnetic and Inductive Position Sensing Solutions at Electronica 2024
- Car key in the left hand, liveness detection radar in the right hand, UWB is imperative for cars!
- After a decade of rapid development, domestic CIS has entered the market
- Aegis Dagger Battery + Thor EM-i Super Hybrid, Geely New Energy has thrown out two "king bombs"
- A brief discussion on functional safety - fault, error, and failure
- In the smart car 2.0 cycle, these core industry chains are facing major opportunities!
- The United States and Japan are developing new batteries. CATL faces challenges? How should China's new energy battery industry respond?
- Murata launches high-precision 6-axis inertial sensor for automobiles
- Ford patents pre-charge alarm to help save costs and respond to emergencies
- New real-time microcontroller system from Texas Instruments enables smarter processing in automotive and industrial applications
- Inside the DLP NIRscan Nano Evaluation Module
- How to process the current transformer signal with a single chip microcomputer
- 【2022 Digi-Key Innovation Design Competition】Material Unboxing
- DCDC isolated voltage regulated power supply module supports electric vehicle transmission and conversion, and configures high power supply system!
- Programmable linear constant current source circuit leakage current type: based on PAC chip GP8102, GP8202
- 1.2 PB Raspberry Pi Disk Array
- TI's GaN high-efficiency 1MHz CrM totem-pole PFC converter reference design
- Popular Science | Power Management Knowledge
- TI Reference Voltage (VREF) Application Design Tips
- The difference between multilayer PCB and LTCC