Central topics:
- Design of hysteresis control circuit based on buck-type LED constant current drive
- Hysteresis control circuit design and principle analysis
Solution:
-
Design of hysteresis comparison voltage generation circuit
-
Circuit design with op amp
-
Average drive current setting
This paper designs a hysteresis control circuit for a buck-type LED constant current driver chip. The chip adopts a high-side current detection scheme and uses a hysteresis current control method to perform hysteresis control on the drive current, thereby obtaining a constant average drive current. The design adopts a simple design concept to achieve constant current drive, does not require complex circuit analysis, can achieve precise current control, and has its own stability. The chip is developed using a 0.5μm 5V/18V/40V CDMOS process, with a power supply voltage range of 4.5V~28V and an operating temperature of -40℃~125℃. It can provide a constant 350mA drive current for the LED. By adjusting the external detection resistor, the constant LED drive current can be adjusted. The DIM signal is provided externally, and the brightness of the LED is adjusted by the duty cycle of the DIM. The Hspice simulation results show that the LED drive current is a triangular wave with hysteresis changes, and the constant current accuracy is less than 6.2%.
1 Introduction
At present, there are two driving modes for LEDs: constant voltage drive and constant current drive, among which constant current drive is a common method. Constant current drive eliminates the current change caused by the change of forward voltage due to factors such as temperature and process, ensuring constant LED brightness. In the LED constant current drive control mode, the hysteresis current control mode has many advantages: simple structure, self-stabilization, not easy to cause unstable oscillation due to noise, etc., and is increasingly widely used. MAXIM16819 of MAXIM is an LED constant current drive chip.
This paper implements a simple hysteresis control module, which controls the on and off of the power switch tube by the self-built hysteresis comparison voltage inside the module and the PWM signal of the DIM control end to achieve constant current control of the LED.
2 Circuit design and principle analysis
2. 1 Hysteresis control principle
The application of the hysteresis control module is shown in Figure 1. The change of the LED drive current is reflected in the change of the voltage difference across the detection resistor RSENSE. In this design, the detection resistor is set to 0.5Ω. A smaller detection resistor is conducive to reducing power consumption and maintaining a higher conversion efficiency. The hysteresis current control module has two built-in voltage thresholds. The detection voltage Vcs is compared with the threshold voltage, and the comparison result is ANDed with the DIM dimming signal to control the on and off of the power switch tube.
Figure 1 Application diagram of hysteresis control module
Use PWM dimming to provide full current to the LED during the current duty cycle. For example, to reduce the brightness by half, only the full current needs to be provided during the 50% duty cycle. Usually, the frequency of the PWM dimming signal will exceed 100Hz to ensure that the pulse current will not be detected by the human eye.
The internal circuit of the hysteresis control module is shown in Figure 2. When the DIM signal is at a high level, when Vcs is greater than the upper voltage threshold, the control circuit outputs a low level and turns off the power switch tube. The loop composed of LED, inductor L, freewheeling diode D and RSENSE allows the inductor to continue to provide current to the LED, and the inductor current gradually decreases, causing the detection voltage Vcs to decrease accordingly; when Vcs is less than the lower threshold voltage, the control circuit outputs a high level and turns on the power switch tube. At this time, D is cut off, forming a loop from the power supply through RSENSE, LED, L and the power switch tube to the ground. The power supply charges the inductor L, the inductor current rises, and the detection voltage Vcs rises accordingly. When Vcs is greater than the upper voltage threshold, the control circuit turns off the switch tube and repeats the action of the previous cycle, thus completing the hysteresis current control of the LED drive current, so that the drive current flowing through the LED, that is, the average value of the inductor current, is constant.
Figure 2 Internal modules of the hysteresis control module
4. The input voltage of 5V~28V is adjusted and converted into a constant voltage Vcc of 5V to power the subsequent circuits. As shown in Figure 3, the potential at point A is clamped by the operational amplifier and will be equal to the reference voltage 1.2V. Assuming that the output V out is at a high level, M2 is turned on, and the current flowing through M1 is IM1 = V ref / R2, and the voltage at point B is V BL = Vin - IM1 R1; when V out is at a low level, M2 is turned off, and the current flowing through M1 becomes I′M1 = V ref / (R2 + R3), and the voltage at point B increases to V BH = Vin -I′M1 R1, so the voltage change at point B is ΔV B = V BH - V BL = V ref R1 R3/ R2 (R2 + R3), which means that when V out changes from a high level to a low level, a hysteresis voltage is generated at point B. It can be seen that the hysteresis voltage has nothing to do with the input voltage, but is only determined by the reference voltage V ref and the size of the resistor. The size of the hysteresis voltage can be set by selecting the resistance value of each resistor.
Figure 3 Hysteresis comparison voltage generation circuit
2.3 Operational amplifier circuit
The above analysis shows that the operational amplifier plays an important role. It must have a high gain to make the voltage at point A accurately follow the reference voltage, so as to accurately set the level at point B and the hysteresis voltage. In addition, since the change frequency of V out is the same as the system switching frequency (the maximum switching frequency of the system is about 2MHz), the current flowing through M1 also switches quickly between IM1 and I′M1 at the same frequency, so the unit gain bandwidth of the operational amplifier must be greater than the maximum switching frequency of the system. The designed operational amplifier structure is shown in Figure 4. The folded input structure can obtain a larger common-mode input voltage range.
From the frequency characteristic simulation diagram of the operational amplifier 5, it can be seen that the gain reaches 84.266dB, the phase margin is 108°, and the unit gain bandwidth is about 12MHz, which meets the circuit requirements.
Figure 4 Op amp implementation circuit
Figure 5 Op amp frequency characteristic simulation
2. 4 Average drive current setting
The op amp clamps the potential of point A on the bandgap voltage reference. The cascade current mirror composed of M7 - M8, M6 - M9 mirrors the bias current I1 to the branch where M8 - M9 - R5 is located, so the voltage Vn of one input terminal of the Compara2tor module remains constant, and the voltage Vp of the other input terminal will change with the detection voltage Vcs. When the comparator output Vout is high (the switch tube is turned on), the voltage at point B is VBL, that is, the lower threshold detection voltage VCSMIN. When Vcs drops to this threshold, the symmetrical circuit structure composed of M6~M11 makes the current flowing through R5 and R6 equal, and Vn = Vp. If Vcs < VCSMIN, that is, Vp < Vn, the comparator flips and the output Vout is low. When V out changes to a low level, M2 is turned off, and the voltage at point B becomes V BH , which is the upper threshold voltage V CSMAX . The average driving current flowing through the LED is set by the average voltage at point B:
Hysteresis current range:
The above formula determines the ripple size of the driving current.
3 Simulation result analysis
The circuit in this paper adopts 0.5μm 5V/18V/40V CDMOS process and is simulated by Hspice Z - 2007.03. Under the joint action of DIM signal with a pulse width of 200μs and a period of 300μs and Vin = 12V (typical value), the simulation results are shown in Figure 6.
Figure 6 Circuit simulation when Vin = 12V
The LED driving current was simulated again under the conditions of Vin = 2.5V and Vin = 28V respectively. The three simulation data results are shown in Table 1 respectively.
Table 1 Driving current under three input voltage conditions
When Vin = 12V, the temperature characteristic of the LED driving current is simulated, and the three simulation waveform results are shown in Table 2. It can be seen that the temperature characteristic of the chip is good.
Table 2 Driving current at three ambient temperatures when Vin = 12V
Since the fixed delay τ of the system has an impact on the current ripple, the actual driving current peak is IMAX + τoff di/ dt, and the current valley is IMIN - τON di/ dt, τoff is the system delay from the driving current being greater than the set value to the power switch being turned off, τon is the system delay from the driving current being less than the set value to the power switch being turned on, and di/ dt is the rate of change of the inductor current. If the inductance takes a larger value, it will have little effect on the average driving current, but it can reduce the current ripple. On the contrary, this is at the expense of increasing the volume of the external inductor.
The circuit can achieve very high efficiency. On the one hand, the power consumption in the detection resistor
will cause the power dissipation of the power supply, but in this design RSENSE = 0.5Ω, then PRSENSE is quite small. On the other hand, the system efficiency is defined as the ratio of the power consumed by the LED to the power provided by the power supply, that is, η = PLED/PPOWER. Among them, PPOWER =V in3 Ivin, PLED = V LED*
. From the simulation, it can be seen that the average value of Ivin is much smaller than
, so the efficiency of the system can be very high.
4 Conclusion
This paper designs a hysteresis control circuit suitable for buck-type LED constant current driver chip. The high-side current detection scheme is adopted, and the hysteresis current control method is used to perform hysteresis control on the drive current, so as to obtain a constant average drive current. By adjusting the external detection resistor, the constant LED drive current can be adjusted. The chip adopts 0.15μm 5V/18V/40V CDMOS process, with a power supply voltage range of 4.5V~28V, which can provide a constant 350mA drive current for LEDs, with a temperature characteristic of -40℃~125℃, and can achieve a fairly high efficiency. When Vin changes from 4.5V to 28V, the average drive current changes by 22mA, and the maximum constant current accuracy is 6.2%.
Previous article:Analysis: LED color-changing light circuit
Next article:Passive OLED power supply solution for portable applications
Recommended ReadingLatest update time:2024-11-16 19:33
![[High-power car lighting driver solution] Input 8-100V step-down LED constant current driver chip FP7125](https://6.eewimg.cn/news/statics/images/loading.gif)
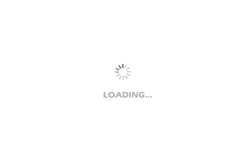
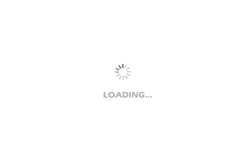
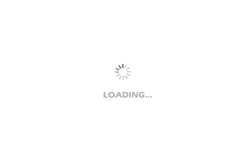
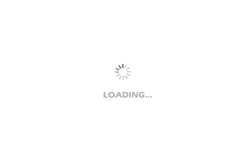
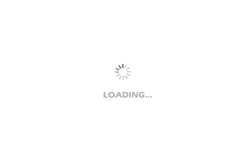
- Popular Resources
- Popular amplifiers
-
MCU C language programming and Proteus simulation technology (Xu Aijun)
-
100 Examples of Microcontroller C Language Applications (with CD-ROM, 3rd Edition) (Wang Huiliang, Wang Dongfeng, Dong Guanqiang)
-
Research on three-phase all-solid-state high-efficiency LED tunnel lighting system based on chip drive_Li Jian
-
Follow me Season 2 Episode 1 All Code + Library
- MathWorks and NXP Collaborate to Launch Model-Based Design Toolbox for Battery Management Systems
- STMicroelectronics' advanced galvanically isolated gate driver STGAP3S provides flexible protection for IGBTs and SiC MOSFETs
- New diaphragm-free solid-state lithium battery technology is launched: the distance between the positive and negative electrodes is less than 0.000001 meters
- [“Source” Observe the Autumn Series] Application and testing of the next generation of semiconductor gallium oxide device photodetectors
- 采用自主设计封装,绝缘电阻显著提高!ROHM开发出更高电压xEV系统的SiC肖特基势垒二极管
- Will GaN replace SiC? PI's disruptive 1700V InnoMux2 is here to demonstrate
- From Isolation to the Third and a Half Generation: Understanding Naxinwei's Gate Driver IC in One Article
- The appeal of 48 V technology: importance, benefits and key factors in system-level applications
- Important breakthrough in recycling of used lithium-ion batteries
- Innolux's intelligent steer-by-wire solution makes cars smarter and safer
- 8051 MCU - Parity Check
- How to efficiently balance the sensitivity of tactile sensing interfaces
- What should I do if the servo motor shakes? What causes the servo motor to shake quickly?
- 【Brushless Motor】Analysis of three-phase BLDC motor and sharing of two popular development boards
- Midea Industrial Technology's subsidiaries Clou Electronics and Hekang New Energy jointly appeared at the Munich Battery Energy Storage Exhibition and Solar Energy Exhibition
- Guoxin Sichen | Application of ferroelectric memory PB85RS2MC in power battery management, with a capacity of 2M
- Analysis of common faults of frequency converter
- In a head-on competition with Qualcomm, what kind of cockpit products has Intel come up with?
- Dalian Rongke's all-vanadium liquid flow battery energy storage equipment industrialization project has entered the sprint stage before production
- Allegro MicroSystems Introduces Advanced Magnetic and Inductive Position Sensing Solutions at Electronica 2024
- Car key in the left hand, liveness detection radar in the right hand, UWB is imperative for cars!
- After a decade of rapid development, domestic CIS has entered the market
- Aegis Dagger Battery + Thor EM-i Super Hybrid, Geely New Energy has thrown out two "king bombs"
- A brief discussion on functional safety - fault, error, and failure
- In the smart car 2.0 cycle, these core industry chains are facing major opportunities!
- The United States and Japan are developing new batteries. CATL faces challenges? How should China's new energy battery industry respond?
- Murata launches high-precision 6-axis inertial sensor for automobiles
- Ford patents pre-charge alarm to help save costs and respond to emergencies
- New real-time microcontroller system from Texas Instruments enables smarter processing in automotive and industrial applications
- Huawei employee detained for 251 days for extortion over severance pay
- LOTO oscilloscope measured open-loop gain frequency response curve/power supply loop response stability
- Can different DRAMs be mixed and matched?
- How many kilometers does it take to change tires? [I recently rented a car and wanted to know more]
- TMS320C6748 development board EDMA routine
- Watch Shui Ge's video to win a JD card | PICE 3.0 related tests
- Paradox between power control accuracy and time delay accuracy of zero-crossing switch
- How to Make LED Bulbs Dimmable
- (All delivered, order number can be checked) The shortlist is here - 2020 ST MEMS Sensor Creative Design Competition
- [Content synchronization] A quick review of RVB2601 article synchronization specifications to avoid repeated returns and modifications