According to information provided by the U.S. Department of Energy's Office of Energy Efficiency and Renewable Energy, heat dissipation is one of the most important factors in successfully designing an LED system. Light-emitting diodes can only convert 20% to 30% of electrical energy into visible light, and the rest is converted into heat, which must be directed from the LED chip to the circuit board and heat sink. Excess heat will reduce the light output of the LED and shorten its life. Therefore, improving heat dissipation efficiency is very important for optimizing the performance potential of LEDs.
Replace with heat sink
Currently, LED substrates or modules for high power/high brightness applications are soldered to a metal core printed circuit board (MCPCB), thermally enhanced printed circuit board, or ceramic substrate, which is then bonded to a heat sink. While this configuration is widely used in the LED industry, it is not the best method for heat dissipation and can be expensive to manufacture.
MCPCB and enhanced heat dissipation printed circuit boards have good heat dissipation performance, but the design flexibility is limited, and if the heat dissipation efficiency needs to be improved, the cost may be high because of the additional cost of heat dissipation hole processing and expensive thermal insulation materials. Ceramic substrates can be made of ceramics that are not very thermally conductive but cheap (such as alumina ceramics) or ceramics that are very thermally conductive but very expensive (such as aluminum nitride ceramics). In general, ceramic substrates cost more than MCPCB and enhanced heat dissipation printed circuit board substrates.
To replace the above substrates, LED manufacturers are testing methods to make circuits directly on aluminum substrates because this method can provide excellent thermal conductivity. Due to its advantages, the LED industry is interested in using aluminum, but making LED circuits on aluminum substrates requires an insulating layer. Now, advances in thick film technology allow the LED industry to reap the benefits of using aluminum substrates.
The Aluminum Substrate Material System (IAMS) developed by Heraeus Materials Technology, a supplier of thick film thermal pastes, is a low temperature sintering (less than 600°C) thick film insulation system that can be printed and sintered on aluminum substrates. The IAMS material system includes dielectric paste, silver conductive paste, glass protective layer and resistor paste. These materials are suitable for 3000, 4000, 5000 and 6000 series aluminum substrates.
Advantages of IAMS
“IAMS is an insulation system designed for aluminum substrates,” said Mitsuru Kondo, Global LED Project Manager at Heraeus Thick Film Materials. “Aluminum cannot withstand temperatures above 660 degrees Celsius, and standard thick film products are based on ceramics and must be sintered at high temperatures, up to 800 to 900 degrees Celsius.
Mr. Kondo explained: “Because IAMS paste can be sintered at temperatures below 600 degrees Celsius, the system is suitable for aluminum processing conditions. In addition, IAMS’ unique glass system reduces the deformation and warping of aluminum while providing a high breakdown voltage and excellent thermal conductivity.”
Most thick film pastes have a coefficient of thermal expansion (CTE) tuned for use on high temperature, low CTE ceramic substrates. However, if an aluminum substrate with a very high CTE is used with a paste designed for ceramic, the substrate will "warp" due to the difference in CTE. The CTE of IAMS is designed to match that of aluminum to minimize warping.
By using IAMS, it is easy to modify the design of the LED substrate. Mr. Kondo said: "Thick film technology allows the LED circuit pattern to be screen printed directly onto the aluminum substrate. The screen pattern can be easily modified according to changes in the circuit design, just by changing the screen and reprinting. "This flexibility is very helpful during the prototyping and design stage.
In addition, the printing process for printing IAMS paste is a selective printing area process, so the cost is lower. The insulating paste is only printed where the conductive circuit is located. With proper design, thermal vias can be easily connected directly to the highly thermally conductive aluminum. This method wastes very little material compared to etched MCPCB and enhanced thermal printed circuit boards (the former two types of boards are made by chemically etching copper plates to form circuits). With the IAMS system, the conductive paste is only printed where the circuit is needed.
In addition, with IAMS technology, customers only need to use one insulating paste. Other thick film technologies require two different types of glass paste for each insulating layer. In addition, all IAMS pastes are RoHS compliant.
Proven technology
Effective heat dissipation is critical to LED performance; keeping LEDs cool helps increase brightness and extend life. To prove that IAMS can provide the heat dissipation characteristics required by LED manufacturers, Heraeus invited third parties to conduct tests. Heraeus asked VTT Technical Research Center in Oulu, Finland to conduct a comparative study of MCPCB and IAMS.
Aila Sitomaniemi, a researcher at VTT, said: "We compared the thermal characteristics of LED substrates using MCPCB and IAMS. We tested 10 substrates, each with a high-power LED soldered on it. Each board was placed in a constant temperature chamber, keeping the contact temperature of the bottom of the board at 25 degrees Celsius to ensure that each board was efficiently and equally cooled."
Sitomaniemi pointed out: "Test results show that LEDs soldered with IAMS paste operate cooler than LEDs soldered on MCPCB. The average temperature of the junction is up to three degrees lower at 350 mA and up to six degrees lower at 700 mA."
Eveliina Juntunen, a researcher at VTT, said heat dissipation is a key factor that dominates the performance of LED devices. Juntunen said: "When using high-power LEDs, heat dissipation must be achieved to meet the increasingly stringent requirements in terms of efficiency, color, reliability and product lifetime."
“Measurements show that IAMS reduces the junction temperature of the LED. When using IAMS, the thermal resistance between the LED active junction and the bottom of the circuit board was measured to be up to 20% lower than when using MCPCB,” Juntunen said. Juntunen said she believes these results are meaningful and provide clear advantages in applying LEDs in the best way.
Heat sink printing
IAMS technology may allow the circuit to be printed directly on the heat sink in the future. Currently, in most LED assembly businesses, packaged LEDs are purchased and then the LEDs and heat sinks are bonded to the MCPCB using a low-temperature adhesive. Each additional layer will increase the thermal resistance, which will eventually compromise brightness and life.
Mr. Kondo said, “IAMS technology enables customers to print the insulating layer directly on the heat sink, solving the problem of additional heat dissipation substrates (MCPCB, enhanced heat dissipation circuit board, ceramic, etc.) increasing the thermal resistance value. The LED device can be directly connected to the heat sink, providing the best heat dissipation method.”
Reduce heat generation and extend service life
Heraeus' material system for aluminum substrates reduces thermal resistance by reducing the number of joints/layers in the LED package. By using this single-formulation, multi-functional system, LED manufacturers can make design changes at low cost and selectively print insulating layers. The ability to use lower-cost substrates (such as aluminum) can enhance conductivity and extend the life of the LED.
Mr. Kondo concluded: "Keeping the temperature of LED packages cooler is key to achieving optimal LED function. Lowering the temperature of LEDs by 10 degrees can more than double the life of the device and reduce overall costs, making LEDs more attractive to consumers."
Previous article:Application of LED light sources in garden landscape lighting
Next article:How to do a good job in quality control and daily maintenance of LED display screens
Recommended ReadingLatest update time:2024-11-17 01:41
![[In-depth analysis] The development and application of LED street lights](https://6.eewimg.cn/news/statics/images/loading.gif)
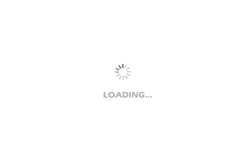
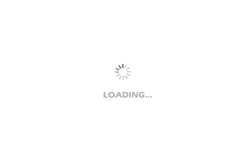
- Popular Resources
- Popular amplifiers
- MathWorks and NXP Collaborate to Launch Model-Based Design Toolbox for Battery Management Systems
- STMicroelectronics' advanced galvanically isolated gate driver STGAP3S provides flexible protection for IGBTs and SiC MOSFETs
- New diaphragm-free solid-state lithium battery technology is launched: the distance between the positive and negative electrodes is less than 0.000001 meters
- [“Source” Observe the Autumn Series] Application and testing of the next generation of semiconductor gallium oxide device photodetectors
- 采用自主设计封装,绝缘电阻显著提高!ROHM开发出更高电压xEV系统的SiC肖特基势垒二极管
- Will GaN replace SiC? PI's disruptive 1700V InnoMux2 is here to demonstrate
- From Isolation to the Third and a Half Generation: Understanding Naxinwei's Gate Driver IC in One Article
- The appeal of 48 V technology: importance, benefits and key factors in system-level applications
- Important breakthrough in recycling of used lithium-ion batteries
- Innolux's intelligent steer-by-wire solution makes cars smarter and safer
- 8051 MCU - Parity Check
- How to efficiently balance the sensitivity of tactile sensing interfaces
- What should I do if the servo motor shakes? What causes the servo motor to shake quickly?
- 【Brushless Motor】Analysis of three-phase BLDC motor and sharing of two popular development boards
- Midea Industrial Technology's subsidiaries Clou Electronics and Hekang New Energy jointly appeared at the Munich Battery Energy Storage Exhibition and Solar Energy Exhibition
- Guoxin Sichen | Application of ferroelectric memory PB85RS2MC in power battery management, with a capacity of 2M
- Analysis of common faults of frequency converter
- In a head-on competition with Qualcomm, what kind of cockpit products has Intel come up with?
- Dalian Rongke's all-vanadium liquid flow battery energy storage equipment industrialization project has entered the sprint stage before production
- Allegro MicroSystems Introduces Advanced Magnetic and Inductive Position Sensing Solutions at Electronica 2024
- Car key in the left hand, liveness detection radar in the right hand, UWB is imperative for cars!
- After a decade of rapid development, domestic CIS has entered the market
- Aegis Dagger Battery + Thor EM-i Super Hybrid, Geely New Energy has thrown out two "king bombs"
- A brief discussion on functional safety - fault, error, and failure
- In the smart car 2.0 cycle, these core industry chains are facing major opportunities!
- Rambus Launches Industry's First HBM 4 Controller IP: What Are the Technical Details Behind It?
- The United States and Japan are developing new batteries. CATL faces challenges? How should China's new energy battery industry respond?
- Murata launches high-precision 6-axis inertial sensor for automobiles
- Ford patents pre-charge alarm to help save costs and respond to emergencies
- [Xingkong Board Python Programming Learning Main Control Board] Python development environment experience - graphic code can be quickly started
- 【NXP Rapid IoT Review】+① NXP Rapid IoT unboxing test
- How to detect whether the switching power supply transformer is good or bad?
- How to enable TI 15.4-Stack to support 470M frequency band
- Xu Jinglei's blog ranks first in the world
- 【Development Kit for nRF52840】+ Review 5-thread trial
- How to determine whether the EN enable pin of the chip needs a series resistor?
- Thermal Design of Semiconductor Components: Heat Transfer and Heat Dissipation Paths
- 【Qinheng Trial】Implementation of USB HID
- matlab