Although peak current mode controlled discontinuous buck-boost converters are a good choice for LED drivers when the output voltage may be higher or lower than the input voltage. However, when designing a driver using this buck-boost converter, changes in LED voltage will change the LED current, and an LED open circuit will cause excessive voltage at the output end, thus damaging the converter. This article will discuss this converter design for LEDs in detail and provide various methods to overcome its inherent shortcomings.
Light-emitting diodes (LEDs) have been used for many years, and with the advancement of the latest technology, they are gradually becoming strong competitors in the lighting market. The new high-brightness LEDs have a long life (approximately 100,000 hours) and high efficiency (approximately 30 lumens/watt). Over the past thirty years, the light output brightness of LEDs has doubled every 18 to 24 months, and this growth momentum will continue. This trend is called Haitz's Law, which is equivalent to Moore's Law of LEDs.
Electrically speaking, LEDs are similar to diodes in that they also conduct electricity in one direction (although their reverse blocking capabilities are not very good, high reverse voltages can easily damage (LEDs)), and have low dynamics similar to regular diodes. Impedance VI characteristics. In addition, LEDs generally have a rated current for safe conduction (the rated current of high-brightness LEDs is generally 350mA or 700mA). When passing the rated current, the difference in LED forward voltage drop may be relatively large, usually 350mA white light The voltage drop of LED is between 3~4V.
Driving LEDs requires a controlled DC current. In order to make the LED have a longer service life, the ripple in the LED current must be very low, because high ripple current will cause the LED to generate large resistive power consumption and reduce the LED service life. LED driving circuits require higher efficiency because the overall efficiency depends not only on the LED itself, but also on the driving circuit. Switching converters operating in current control mode are ideal driving solutions to meet the high power and high efficiency requirements of LED applications.
Driving multiple LEDs also requires careful consideration. Figure 1 is a series-parallel connection circuit of LEDs. Figure 1(a) shows the parallel connection circuit of LEDs. Figure 1(h) is a series connection circuit of LEDs. Since the dynamic impedance and forward voltage drop of each LED are different, it is impossible to ensure that the current flowing through the LED is the same without an external current sharing circuit (such as current mirror); in addition, a failure of one LED will cause the LED string to disconnect, causing all LED current to be divided among the remaining LED strings, which will cause the current on the LED strings to increase, potentially damaging the LEDs. Therefore, for the above two reasons, parallel LED circuits as shown in Figure 1(a) are generally not used during design.
Therefore, a better approach is to connect the LEDs in series. The disadvantage of this method is that if one LED fails, the entire LED string will stop working. A simple way to keep the remaining LED strings operating is to connect a Zener diode (with a rated voltage greater than the maximum voltage of the LED) in parallel with each LED (or group), as shown in Figure 1(b). In this way, if any LED fails, its current will flow to the corresponding Zener diode, and the rest of the LED string can still operate normally.
Basic single-stage switching converters can be divided into three categories: buck converters, boost converters, and buck-boost converters. When the voltage of the LED string is lower than the input voltage, the buck converter Figure 2(a) is an ideal choice; when the input voltage is always lower than the string output voltage, it is more appropriate to use a boost converter Figure 2(b) ; When the output voltage may be higher or lower than the input voltage (caused by output or input changes), it is more appropriate to use a buck-boost converter (Figure 2(c)). The disadvantage of a boost converter is that any transient in the input voltage that can raise the input voltage above the output voltage will cause a large current to flow through the LED (due to the low dynamic impedance of the load), thus damaging the LED. Buck-boost converters can also replace boost converters because transients in the input voltage do not affect the LED current.
How a buck-boost converter works
For LED drivers in low-voltage applications, buck-boost converters are a good choice. The reasons for this are that they can drive LED strings at voltages above and below the input voltage (boost and buck), are very efficient (easily over 85%), and have a discontinuous operating mode that suppresses input voltage changes (provided Excellent line voltage regulation), peak current control mode allows the converter to regulate LED current without complex compensation (simplifying design), linear and PWM LED brightness regulation is easy to achieve, switching transistor failure does not damage the LED, etc. Figure 2 shows the connection circuits of buck, boost and buck-boost converters to LED strings.
However, this method still has shortcomings: First, the problem of peak current control, because the buck-boost converter using discontinuous current mode is a constant power converter. Therefore, any change in the LED string voltage will cause a corresponding change in the LED current; another problem is that the LED open circuit state will generate high voltages in the circuit that damage the converter; in addition, additional circuitry is required to convert the constant power converter to a constant current converter and needs to protect the converter under no load conditions.
Figure 3 shows a specific application circuit of a buck-boost converter. The controller has a built-in oscillator for setting the switching frequency. At the beginning of the switching cycle, Q1 is on. Since the input voltage VIN is applied to the inductor, the inductor current (iL(t)) starts to rise from zero (initial steady state). When the induced current rises to the preset current value (ipk), Q1 turns off. The switch conduction time (ton) is determined by the following formula:
ton=ipkL/VIN
At this time, the total energy (J) stored in the inductor is:
J=Li2pk/2
In this way, although the switch will be closed at this time, the current flowing through the inductor will not be interrupted. This causes diode D1 to conduct and generate an output voltage (-Vo) across the inductor. This negative voltage causes the inductor current to drop rapidly. After a certain period of time tOFF, the inductor current tends to zero. This time can be calculated using the following formula:
tOFF=ipkL/VO
In order for the converter to operate in discontinuous conduction mode, the sum of the switch conduction time and the inductor current drop time must be less than or equal to the switching period TS to ensure that the inductor current can start from zero in the next switching period.
In fact, (tON+tOFF) can achieve the maximum value when the input voltage is the minimum and the output voltage is the maximum. Therefore, ensuring that the converter operates in discontinuous conduction mode at these voltages ensures that the conditions listed in the following equation are met under any circumstances: tON+tOFF≤Ts
The power the converter obtains from the input (Pin) is the product of the energy in the inductor and the switching frequency f: that is:
Pin=fsLi2pk/2
Assuming the voltage of the LED string (VO) is constant and the efficiency is 100%, then the current of the LED (iLED) is:
iLED=PIN/VLED=Li2pkfs/2V
In peak current control mode, ipk is usually a fixed value. Therefore, the LED current is completely independent (theoretically) of the input voltage. At a fixed ipk, a rise (fall) in the input voltage will cause the transistor's on-time to decrease (increase) in inverse proportion, which will provide good line voltage regulation. In a real application, the delay between the control IC detecting the current peak and the GATE pin actually turning off will cause input power changes. Shorter on-times will introduce more error due to delay time, since the delay time will account for a significant portion of the on-time.
In fact, the LED current is inversely proportional to the voltage of the LED string. A circuit with a nominal output of 20 V and 350 mA will produce 700 mA at an output voltage of 10 V, which is obviously not the desired result. However, the above formula provides a way to convert a constant power converter into a constant voltage converter by making the switching frequency proportional to the output voltage.
Assuming fs=KVO, where K is a constant, then there is:
iLED=kLi2pk/2
This way, the iLED will be independent of input and output voltages.
Another disadvantage of the flyback converter is that it is susceptible to an open-circuit condition at the output. When the LED is open circuit, the energy stored in the inductor is transferred to the output capacitor at the end of each switch on time. Thus, a load lacking capacitive discharge will cause the voltage across the capacitor to gradually rise, eventually exceeding the nominal value of the device and damaging the power stage. Therefore, additional circuitry can be added to provide output voltage feedback and overvoltage protection.
Output voltage feedback
Figure 4 is an additional circuit that implements overvoltage protection and LED open circuit protection. In fact, many peak current mode controller ICs have dedicated RT pins. The resistor connected to this pin can be used to set the internal current used to charge the oscillator capacitor (which can be internal or external). The ramp voltage across the oscillator capacitor controls the switching frequency such that the switching frequency is proportional to the output current from the RT pin. The smaller (larger) the resistance, the larger (smaller) the current, and the higher (lower) the switching frequency. Based on this principle, output voltage feedback can be used to adjust the switching frequency.
?
In the circuit shown in Figure 4, resistors R3 and R4 form a voltage divider. The voltage across R4 minus the voltage drop (Vbe) between the base and emitter of transistor Q2 is the voltage across R5. Therefore, the current flowing through R5 (IR5) is:
This current is obtained from pin RT of the control IC using a matched pair of transistors.
Resistor R2 in Figure 4 is used to start the converter. In the starting state, the output voltage is zero, so IR5 is also zero. Since there is no current from the RT pin of the controller, the converter cannot start. Adding resistor R2 can obtain a small amount of current in the startup state and make the size of R2 satisfy:
IR5>>V(RT)/R2
where V(RT) is the voltage on the controller's RT pin. Meeting this condition ensures start-up of the converter and minimizes the error introduced by R2. If R3=R4 is selected, then:
IR5>>VO/2R5
This assumes that the output voltage is much larger than the base-emitter voltage drop of Q2.
In this way, according to the above formulas, the output LED current can be obtained as:
iLED=KICLi2pk/(2×2R5)
In this way, the LED current will no longer depend on the input or output voltage. The overvoltage protection function can be added by using resistor R6, transistor Q3 and zener diode D2. In the LED open circuit state, when the switch is on, the inductor stores energy, and when the switch is off, this energy is transferred to the output capacitor. Because there is not enough load supply capacity to discharge, the output voltage will gradually increase with each cycle. When the voltage rises above the turn-on voltage of the Zener diode, the Zener diode branch circuit consisting of D2 and R6 begins to conduct. This also provides a path for current through the base of Q3, causing Q3 to conduct. At this time, resistor R4 is actually short-circuited. Therefore, the base-emitter PN junction of Q2 will close, causing zero current on R5. This stops the controller's internal oscillation until the output voltage drops below the Zener diode voltage, and the above process continues. This burst mode minimizes the average power in the open LED state. This overvoltage protection method will force the control IC into a low-frequency, low-power operating mode.
The current in the zener diode resistor branch must produce a large enough voltage across R6 to bias the PN junction between the base and emitter of the transistor.
Conclusion
In switching LED drivers with output current feedback, feedback compensation is generally required to stabilize the converter and regulate the current to achieve the desired current value. The transient response performance of these feedback schemes is limited and cannot meet the fast on/off transient response required for PWM brightness adjustment of LEDs. However, the converter described in this article does not require any feedback compensation. The only feedback information used in this control scheme is the peak current flowing through the MOSFET through the sensing resistor. Because the converter stores the required energy on each cycle, it can respond instantly to transients. Therefore it can easily work with PWM brightness adjustment schemes.
Buck-boost converters are an effective solution for low DC voltage input LED drivers, allowing them to drive LED strings regardless of whether the output voltage is higher or lower than the input voltage. Additionally, small and inexpensive additional circuitry can be added to the converter to overcome load regulation and no-load conditions. The converter is easy to implement and requires no feedback compensation when operating in peak current mode control. Its open-loop characteristics also make it ideal for applications requiring PWM brightness adjustment.
Previous article:Selection strategy and application introduction of backlight drive circuit
Next article:Applications of ultra-bright LEDs
Recommended ReadingLatest update time:2024-11-16 17:49
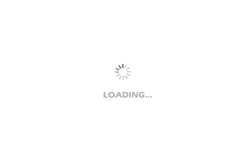
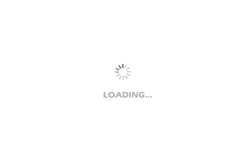
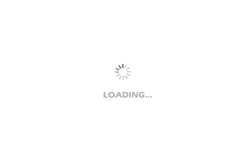
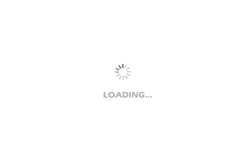
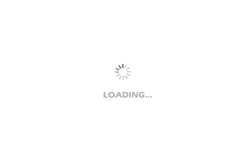
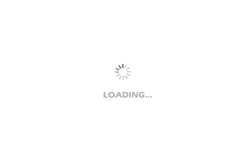
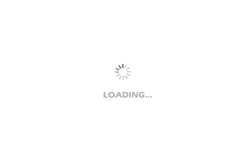
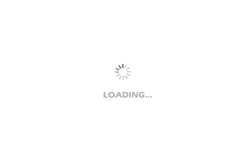
- Popular Resources
- Popular amplifiers
-
Microgrid Stability Analysis and Control Microgrid Modeling Stability Analysis and Control to Improve Power Distribution and Power Flow Control (
-
Modern Electronic Technology Training Course (Edited by Yao Youfeng)
-
New Energy Vehicle Control System Inspection and Maintenance (Edited by Bao Pili)
-
Intelligent Control Technology of Permanent Magnet Synchronous Motor (Written by Wang Jun)
- MathWorks and NXP Collaborate to Launch Model-Based Design Toolbox for Battery Management Systems
- STMicroelectronics' advanced galvanically isolated gate driver STGAP3S provides flexible protection for IGBTs and SiC MOSFETs
- New diaphragm-free solid-state lithium battery technology is launched: the distance between the positive and negative electrodes is less than 0.000001 meters
- [“Source” Observe the Autumn Series] Application and testing of the next generation of semiconductor gallium oxide device photodetectors
- 采用自主设计封装,绝缘电阻显著提高!ROHM开发出更高电压xEV系统的SiC肖特基势垒二极管
- Will GaN replace SiC? PI's disruptive 1700V InnoMux2 is here to demonstrate
- From Isolation to the Third and a Half Generation: Understanding Naxinwei's Gate Driver IC in One Article
- The appeal of 48 V technology: importance, benefits and key factors in system-level applications
- Important breakthrough in recycling of used lithium-ion batteries
- Innolux's intelligent steer-by-wire solution makes cars smarter and safer
- 8051 MCU - Parity Check
- How to efficiently balance the sensitivity of tactile sensing interfaces
- What should I do if the servo motor shakes? What causes the servo motor to shake quickly?
- 【Brushless Motor】Analysis of three-phase BLDC motor and sharing of two popular development boards
- Midea Industrial Technology's subsidiaries Clou Electronics and Hekang New Energy jointly appeared at the Munich Battery Energy Storage Exhibition and Solar Energy Exhibition
- Guoxin Sichen | Application of ferroelectric memory PB85RS2MC in power battery management, with a capacity of 2M
- Analysis of common faults of frequency converter
- In a head-on competition with Qualcomm, what kind of cockpit products has Intel come up with?
- Dalian Rongke's all-vanadium liquid flow battery energy storage equipment industrialization project has entered the sprint stage before production
- Allegro MicroSystems Introduces Advanced Magnetic and Inductive Position Sensing Solutions at Electronica 2024
- Car key in the left hand, liveness detection radar in the right hand, UWB is imperative for cars!
- After a decade of rapid development, domestic CIS has entered the market
- Aegis Dagger Battery + Thor EM-i Super Hybrid, Geely New Energy has thrown out two "king bombs"
- A brief discussion on functional safety - fault, error, and failure
- In the smart car 2.0 cycle, these core industry chains are facing major opportunities!
- The United States and Japan are developing new batteries. CATL faces challenges? How should China's new energy battery industry respond?
- Murata launches high-precision 6-axis inertial sensor for automobiles
- Ford patents pre-charge alarm to help save costs and respond to emergencies
- New real-time microcontroller system from Texas Instruments enables smarter processing in automotive and industrial applications