Lithium-ion batteries have completely replaced other batteries in the mobile phone and laptop computer markets due to their high energy density, small size, and light weight, and their market share has reached almost 100%. At present, lithium-ion batteries are rapidly extending to power tools and other applications, and their broad market prospects are increasingly recognized by the industry. However, compared with nickel-metal hydride, nickel-cadmium, and lead-acid batteries, to promote the application and development of lithium-ion batteries faster, its safety and service life must be continuously improved. This article will discuss a new charging solution from the perspective of chargers to improve the safety of lithium-ion batteries, extend the battery life, and reduce the cost of chargers.
In the process of using batteries, we often hear the following sentence from battery industry: "Batteries are rarely damaged during use, but are more damaged by charging". We can understand this sentence as incorrect charging conditions or methods will more easily damage the battery and reduce the battery life. Take 18650 cobalt acid lithium ion battery as an example. When charging overtemperature, at about 70℃: the electrolyte interface (SEI) module begins to decompose and generate heat; at about 120℃: the electrolyte and positive electrode begin to thermally decompose, causing gas evolution and rapid temperature rise; at about 260℃: the battery explodes. Or charging overvoltage, with an overvoltage of 5.5V, it is easy to cause lithium metal precipitation, solvent oxidation, temperature rise, a vicious cycle, and even battery fire and explosion. Therefore, let's discuss the following important issues together on how to charge.
Why is pre-charging required?
The battery operating voltage ranges from 2.5V (carbon negative battery: 3V, 0% charge) to 4.2V (100% charge). When the voltage is less than 2.5V, the battery discharge is terminated. At the same time, because the discharge circuit is closed, the current loss of the internal protection circuit is also minimized. Of course, in actual applications, due to different internal materials, the discharge termination voltage can be in the range of 2.5V-3.0V. When the voltage exceeds 4.2V, the charging circuit is terminated to protect the battery safety; and when the operating voltage of the single cell drops below 3.0V, we can consider it an over-discharge state, and the discharge circuit is terminated to protect the battery safety. Therefore, when the battery is not in use, it should be charged to 20% of the power and then stored in a moisture-proof manner.
Since lithium-ion batteries have a high energy density, overcharging and over-discharging should be strictly avoided during battery use. Over-discharging will make it difficult for active substances to recover. If you directly enter the fast charging mode (high current) at this time, it will damage the battery, affect the service life and may cause safety hazards. It is necessary to first charge with a small current (C/10) to 2.5V to 3.0V, and then switch to fast charging.
Although lithium-ion batteries are currently equipped with protection boards in applications, under normal circumstances, the probability of over-discharge is very small, but without the pre-charge function, there may still be hidden dangers of over-discharge in these two situations. One is the failure of the protection board, and the other is the self-discharge rate after long-term storage (5%-10%/month). Therefore, low-current pre-charging can effectively solve the charging problem of over-discharged batteries.
However, the higher the charging current, the better. Taking a single lithium-ion battery as an example, its charging method includes constant current and constant voltage charging processes. The constant voltage is usually 4.2V (taking LiCoO2 battery as an example), and the constant current setting value is 0.1C~1C. Although high current charging will shorten the charging time, it will also shorten the battery life cycle and reduce the capacity, so we need to choose an appropriate constant current value for charging.
The following is a curve of the relationship between different charging currents and battery capacity of a 4.2V/900mAH LiCoO2 battery cell (Figure 1). We can see that after about 500 charging and discharging cycles, the battery capacity charged with a small current is significantly greater than the battery capacity charged with a large current.
Voltage accuracy requirements during constant voltage charging
As a high energy density battery, overcharging can cause great harm to lithium-ion batteries, which may cause expansion, leakage, or even explosion. Moreover, overcharging can easily accelerate the reaction of electrolytes in the battery, shortening the battery life. Therefore, accurate constant voltage charging is of great significance to the service life of lithium-ion batteries.
In order to fully charge the battery, the accuracy of the constant voltage and the termination voltage should be within 1%. Taking cobalt-acid lithium-ion batteries as an example, it is best to be as close to 4.2V as possible, but not more than 4.2V. This high-precision voltage charging method can reduce the dissolution of cobalt, stabilize the layered structure of LiCoO2, prevent its coating from phase change, improve cycle performance, and maintain high capacity. In addition, even a slight overvoltage will bring about changes in two phenomena: a reduction in the initial capacity of the battery and a reduction in the battery cycle life.
When multiple lithium-ion batteries are connected in series, in order to ensure the maximum battery capacity and life, the accuracy is sometimes required to be within 0.5%. Therefore, the accuracy control of charging voltage is a key technology of lithium-ion battery chargers.
At present, people have a misunderstanding about the charging voltage of lithium batteries. They think that with a battery protection board, they don't need to worry about the voltage accuracy. This is not advisable. Because the purpose of the battery protection board is to provide timely protection against possible accidents, it considers more safety factors rather than performance factors. For example, taking a 4.2V battery cell as an example, the overvoltage protection parameter of the protection board is 4.30V (some may require 4.4V). If it is overcharged every time, with 4.30V as the charging cutoff point, the battery capacity will decay quickly.
Why do you need a charging timer?
A charger manufacturer once said that they often encountered charger users returning products, saying that the charger was broken because the battery was not fully charged after a day of charging, and the charger light did not turn on and was always red. However, when the manufacturer actually measured the charger, it was found to be normal and met the factory requirements. What is the problem? This is mainly because the charger does not take into account the increase in self-discharge of the battery after aging. If the cut-off current of charging is set too small, the aging battery will not reach the set point of charging completion, which will cause the user to misjudge and think that the charger is broken.
The function of the charging timer is to prevent damaged or over-cycled lithium batteries from self-discharging too much during the charging cutoff period, making it difficult for the battery to enter the EOC state (higher than the judgment current). On the one hand, it may cause the user to misjudge that the battery is not fully charged. On the other hand, it may also cause the battery to overheat and expand due to charging for too long, which may even be dangerous.
Considering these factors, the new multi-series lithium-ion battery charging chip OZ8981 launched by O2Micro is a complete solution. OZ8981 is a dedicated charging management integrated chip with precise voltage, current output and multiple protections, and provides a six-stage charging control mode, which is convenient for system design and low cost. It is mainly used for multi-cell lithium-ion battery packs in light electric vehicles, electric bicycles and power tools.
The cost-effective and highly reliable OZ8981 includes a single-chip integrated charge controller that can achieve efficient error amplifier output. It supports six-stage intelligent charging control: 0V pulse charging, pre-charging, constant current charging, constant voltage charging, cut-off charging, and automatic recharging. It supports flexible settings of the pre-charging start voltage, constant current charging value, constant voltage charging value, and cut-off charging current value.
In addition, OZ8981 has high-precision charging voltage (<1%) and current (<5%) outputs; the voltage output accuracy can be <0.5% by adjusting the external resistor. Supports dual charging timer protection: pre-charge timing, constant voltage charging timing (maximum 5 hours, or not used). Supports dual temperature protection: chip internal temperature protection (115°C), external over-temperature protection (default: 44°C) and under-temperature protection (default: 2°C). The external temperature protection point can be flexibly set externally. Supports charging overvoltage protection, over-current protection, and short-circuit protection. Supports automatic battery access detection and direct LED display of charging status. The device uses the general package SOP16.
Figure 4 is the charging curve of OZ8981 lithium-ion battery. By combining with the front-end PWM chip, OZ8981 will help users quickly realize safe, efficient and low-cost lithium-ion battery charger design.
Previous article:A low-power electronic energy meter power supply monitoring chip
Next article:Practical Power Management for Wireless Remote Sensor Networks
Recommended ReadingLatest update time:2024-11-16 21:50
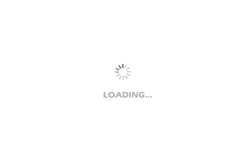
- MathWorks and NXP Collaborate to Launch Model-Based Design Toolbox for Battery Management Systems
- STMicroelectronics' advanced galvanically isolated gate driver STGAP3S provides flexible protection for IGBTs and SiC MOSFETs
- New diaphragm-free solid-state lithium battery technology is launched: the distance between the positive and negative electrodes is less than 0.000001 meters
- [“Source” Observe the Autumn Series] Application and testing of the next generation of semiconductor gallium oxide device photodetectors
- 采用自主设计封装,绝缘电阻显著提高!ROHM开发出更高电压xEV系统的SiC肖特基势垒二极管
- Will GaN replace SiC? PI's disruptive 1700V InnoMux2 is here to demonstrate
- From Isolation to the Third and a Half Generation: Understanding Naxinwei's Gate Driver IC in One Article
- The appeal of 48 V technology: importance, benefits and key factors in system-level applications
- Important breakthrough in recycling of used lithium-ion batteries
- Innolux's intelligent steer-by-wire solution makes cars smarter and safer
- 8051 MCU - Parity Check
- How to efficiently balance the sensitivity of tactile sensing interfaces
- What should I do if the servo motor shakes? What causes the servo motor to shake quickly?
- 【Brushless Motor】Analysis of three-phase BLDC motor and sharing of two popular development boards
- Midea Industrial Technology's subsidiaries Clou Electronics and Hekang New Energy jointly appeared at the Munich Battery Energy Storage Exhibition and Solar Energy Exhibition
- Guoxin Sichen | Application of ferroelectric memory PB85RS2MC in power battery management, with a capacity of 2M
- Analysis of common faults of frequency converter
- In a head-on competition with Qualcomm, what kind of cockpit products has Intel come up with?
- Dalian Rongke's all-vanadium liquid flow battery energy storage equipment industrialization project has entered the sprint stage before production
- Allegro MicroSystems Introduces Advanced Magnetic and Inductive Position Sensing Solutions at Electronica 2024
- Car key in the left hand, liveness detection radar in the right hand, UWB is imperative for cars!
- After a decade of rapid development, domestic CIS has entered the market
- Aegis Dagger Battery + Thor EM-i Super Hybrid, Geely New Energy has thrown out two "king bombs"
- A brief discussion on functional safety - fault, error, and failure
- In the smart car 2.0 cycle, these core industry chains are facing major opportunities!
- The United States and Japan are developing new batteries. CATL faces challenges? How should China's new energy battery industry respond?
- Murata launches high-precision 6-axis inertial sensor for automobiles
- Ford patents pre-charge alarm to help save costs and respond to emergencies
- New real-time microcontroller system from Texas Instruments enables smarter processing in automotive and industrial applications
- ADI's smoke detector integrated solution based on ADPD188BI has started the registration for the prize live broadcast~
- Prize-winning live broadcast: TI chip technology is helping motor development in progress!
- C2000 MCU DesignDRIVE Solutions for Industrial Motor Drives
- Bluetooth BLE - BlueNRG2 VTimer
- Celebrate National Day and wish our motherland a happy 70th birthday!
- [STM32F769Discovery development board trial] SD card file system application & hard-to-decode JPEG decoding code that makes people autistic
- The general form of C language function call
- R329 Development Board Application - Operation Image (1)
- Why are pull-up resistors necessary in microcontroller systems?
- Thonny version 4.0 released