introduction
For some systems that require long-term uninterrupted operation and high reliability, such as base station communication equipment, monitoring equipment, servers, etc., a highly reliable power supply is often required. Redundant power supply design is a key part and plays an important role in high-availability systems. Redundant power supplies are generally configured with more than two power supplies. When one power supply fails, the other power supplies can be put into use immediately without interrupting the normal operation of the equipment. This is similar to the working principle of UPS power supply: when the city power is cut off, the battery replaces the power supply. The difference between redundant power supplies is mainly that they are powered by different power supplies.
Power redundancy has applications in AC 220 V and various DC voltages. This article mainly introduces the design of redundant power supply solutions for low-voltage DC (such as DC 5 V, DC 12 V, etc.).
1 Introduction to Redundant Power Supply
The solutions that can be generally adopted for power supply redundancy include capacity redundancy, redundant cold backup, parallel current-sharing N+1 backup, redundant hot backup, etc. Capacity redundancy means that the maximum load capacity of the power supply is greater than the actual load, which is of little significance to improving reliability.
Redundant cold backup means that the power supply is composed of multiple modules with the same functions. When it is normal, one of them supplies power. When it fails, the backup module starts working immediately. The disadvantage of this method is that there is a time interval between power switching, which is easy to cause voltage gaps.
The N+1 backup method of parallel current sharing means that the power supply is composed of multiple identical units, each unit is connected in parallel through an OR gate diode, and each unit supplies power to the device at the same time. This solution will not affect the load power supply when one power supply fails, but it is easy to affect all units when the load end is short-circuited. Redundant hot backup means that the power supply is composed of multiple units and works at the same time, but only one of them supplies power to the device, and the others are unloaded. When the main power supply fails, the backup power supply can be immediately put into use, and the output voltage fluctuation is very small. This article mainly introduces the design of the latter two solutions.
2 Traditional redundant power supply solution
The traditional redundant power supply design is to connect two or more power supplies to the power bus in parallel by connecting the anodes of diodes respectively, in the form of "OR gate". As shown in Figure 1. One power supply can work alone, or multiple power supplies can work at the same time. When one of the power supplies fails, the output of the power bus will not be affected due to the unidirectional conduction characteristics of the diode.
In actual redundant power supply systems, the current is generally large, up to tens of A. Considering the power consumption of the diode itself, Schottky diodes with low voltage drop and large current are generally selected, such as SR1620~SR1660 (rated current 16 A). Usually, heat sinks are also required on these diodes to facilitate heat dissipation.
3 Comparison of traditional solutions and alternative solutions
The traditional solution using diodes is simple in circuit, but has its inherent disadvantages: high power consumption, severe heat generation, need to install heat sink, and large volume. Since the circuit usually has high current, the diode is in forward conduction mode most of the time, and the power consumption caused by its voltage drop cannot be ignored. The Schottky diode with the smallest voltage drop is also 0.45 V. When the current is large, such as 12 A, there is a power consumption of 5 W, so the heat dissipation problem must be specially handled.
The new redundant power supply solution now uses high-power MOSFET tubes to replace the diodes in traditional circuits. The on-resistance of MOSFET can reach several mΩ, which greatly reduces the voltage drop loss. In high-power applications, not only a more efficient solution is achieved, but also a large amount of circuit board area is saved because no heat sink is required, and the heat source of the equipment is also reduced. The MOSFET in the application circuit needs to be controlled by a professional chip. At present, major companies such as TI and Linear have launched some mature chips of this type.
4 Special applications of MOSFET in the new solution
MOSFET is a key device in the new redundant power supply solution. Because it is different from the application in conventional circuits, many people have certain misunderstandings about MOSFET. In order to facilitate the introduction of the subsequent circuit, the following explains its special features.
First, the arrow in the MOSFET symbol does not represent the actual direction of current flow. In transistor applications, the current direction is the same as the arrow direction of the component symbol, so many people think that the same is true for MOSFET. In fact, MOSFET is different from transistors. The direction of its arrow only indicates that it points from the P plate to the N plate, and has nothing to do with the direction of current flow, as shown in Figure 2.
Secondly, attention should be paid to the presence of diodes in MOSFET. As shown in Figure 2, the source S in N-channel MOSFET is connected to the anode of the diode, and the drain D in P-channel MOS-FET is connected to the anode of the diode. Therefore, in most circuits that use MOSFET as a switch, for N-channel MOSFET, the current flows from the drain to the source, and the gate G is connected to a high voltage to turn on; for P-channel MOSFET, the current flows from the source to the drain, and the gate G is connected to a low voltage to turn on. Otherwise, due to the presence of the diode, the control of the gate cannot shut off the current path.
Finally, it should be noted that the current flow direction of MOSFET is bidirectional, which is different from the unidirectional conduction of triode. For the conductive characteristics of MOSFET, most materials, literature and device data sheets only give unidirectional conductive characteristic curves, and most applications only use its unidirectional conductive characteristics; as for its bidirectional conductive characteristics, there are few literature introductions. In fact, MOS-FET is a voltage-controlled device, which changes the thickness of the conductive channel generated by the induced electric field through the gate voltage, thereby controlling the size of the drain current. Taking N-channel MOSFET as an example, when the gate voltage is less than the turn-on voltage, no matter what the polarity of the source and drain is, one of the two back-to-back PN junctions inside is always reverse biased, forming a depletion layer, and the MOSFET is not turned on. When the gate voltage is greater than the turn-on voltage, an N-type channel is formed between the drain and the source. The N-type channel is just equivalent to a non-polar equivalent resistor with a very small resistance. At this time, if a forward voltage is applied between the drain and the source, the current will flow from the drain to the source. This is a commonly used method. If a reverse voltage is applied between the drain and the source, the current will flow from the source to the drain. This method is rarely used.
In the redundant power application circuit, the connection direction of MOSFET is different from the conventional one. Taking N-channel tube as an example, the connection circuit should be shown in Figure 3. If the power input voltage is higher than the load power voltage, that is, Vi>Vout, the current flows from Vi to Vout. Due to the redundant power application, the load power voltage Vout may be higher than the power input voltage Vi. At this time, the external circuit controls the MOSFET gate to shut off the source and drain paths. At the same time, due to the reverse blocking effect of the internal diode, the load power cannot flow back to the input power.
If you need to directly control the MOSFET path to be turned off by a control signal, the above single tube cannot be realized, because after the MOSFET channel is turned off, the internal diode still has a unidirectional path. In this case, two MOSFET circuits connected back to back in reverse are required as shown in Figure 4. Only in this way can the current path be actively turned off.
5 Several practical redundant power supply scheme designs
This article mainly discusses the design of low-voltage redundant power supplies such as DC 5 V and DC 12 V. Several design examples are given below to meet different functional and cost requirements.
5.1 Simple redundant power supply solution
Using Linear's LTC4416, a simple 2-way power supply redundancy solution can be designed, as shown in Figure 5. In the figure, an LTC4416 chip is connected to two external P-channel MOSFETs to control 2-way power inputs. It is a very simple solution. It uses two MOSFETs instead of two diodes to achieve the "OR" effect. The voltage drop of MOSFET is generally 20 to 30 mV, so the power loss is very small and does not generate too much heat.
The working principle of this circuit is that when the voltages of the two input power supplies of LTC4416 are the same (the difference is less than 100 mV), G1 and G2 are used to control the two MOSFETs to turn on at the same time, so that the two inputs can provide current to the load at the same time. When the input power supply voltages are different, the output power supply voltage may be higher than the voltage of one input power supply. At this time, LTC4416 can prevent the output from backflowing current to the input. This is because the chip always monitors the voltage difference between the input and output. When the output voltage is 25 mV higher than the input voltage, the chip controls G1 or G2 to immediately turn off the MOSFET to prevent current backflow. In terms of preventing backflow, other control chips also have similar principles.
LTC4416 also has two control terminals E1 and E2, which can actively control the on and off of the two power supplies with external signals, or monitor the input voltage through resistor voltage division to control the conduction of a certain power supply. For specific methods, please refer to the chip data sheet. This chip is also suitable for applications where one input power supply voltage is high and the other input power supply voltage is low, such as "power supply + battery" applications. It should be noted that in order for the chip to actively shut down one power supply, the external MOSFET must use a "back-to-back" solution, as shown in Figure 4.
In addition, using TI's TPS2412 can form a multi-input power supply solution. This solution requires a TPS2412 for each input power supply. As shown in Figure 6, each chip simulates the "OR input" of a diode by externally controlling a MOSFET. The A and C pins of the chip are the input and output power supply voltage detection pins, VDD is the chip power supply, and RSET adjusts the speed of MOS-FET conduction by configuring different external resistors, and can also be left floating. This chip can form a power supply redundancy solution for more than 2 channels.
5.2 Redundant power supply solution with overvoltage and undervoltage detection
Figure 7 shows a dual redundant power supply solution with overvoltage and undervoltage detection composed of two P12121 chips. P12121 is a power redundancy dedicated chip from Vicor. Since it integrates a 24 A, 1.5 mΩ MOSFET, the external circuit is very simple. The chip OV is the overvoltage detection pin, and the MOSFET is automatically cut off when it is higher than 0.5 V; UV is the undervoltage detection pin, and the MOSFET is cut off when it is lower than 0.5 V. FT is the status output pin, and VC is the chip working power pin. Using P12121 can also flexibly form a multi-input power supply solution.
5.3 Redundant power supply solution with hot-swap and over- and under-voltage protection
LTC4352 is a single redundant power chip that not only has overvoltage and undervoltage protection, but also has protection against hot-swap surge current. Figure 8 shows a single redundant power circuit composed of LTC4352. Multiple such circuits can be connected in parallel to form a multi-redundant power solution. In the figure, OV and UV are overvoltage and undervoltage detection, respectively. This circuit prevents the chip from quickly turning on and off the MOSFET by leaving CPO floating. It relies on undervoltage detection to delay turning on the MOSFET after the power is powered on by the GATE pin. The resistor-capacitor network composed of R1 and C slows down the voltage rise of the power supply output, and R2 effectively prevents the switch oscillation of Q, thereby achieving a certain hot-swap surge current protection function.
5.4 Redundant power supply solution with current sharing control
If different input power supplies are to bear the load current at the same time (i.e., current sharing control), an additional premise is required, that is, the voltage of each input power supply can be externally adjusted through a control signal to achieve the purpose of basically the same voltage of each power supply. By controlling this power supply through LTC4350, the function of current sharing can be achieved. Figure 9 is an application example diagram. In the figure, "SHARE BUS" is a distribution bus shared by all chips. This circuit mainly adjusts the voltage of the input power supply by detecting the current in the power supply path to achieve the purpose of balanced current supply for each module.
RSENSE is a current detection resistor. LTC4350 detects the voltage across the resistor, amplifies it internally, and compares it with the voltage of the GAIN pin. According to the comparison result, the analog output of the IOUT pin controls the voltage change of the input power supply to achieve the purpose of adjusting the output current of the power supply. In addition, the UV and OV pins are undervoltage and overvoltage detection pins respectively. LTC4350 can control the shutdown of MOSFET by detecting the voltage of these two pins to achieve the functions of undervoltage protection and overvoltage protection.
Previous article:Design of high power factor boost circuit based on L6562
Next article:Design of a new embedded system power monitoring module
Recommended ReadingLatest update time:2024-11-16 19:31
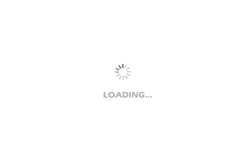
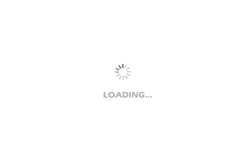
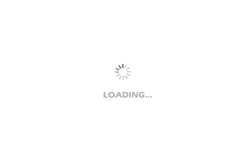
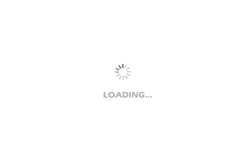
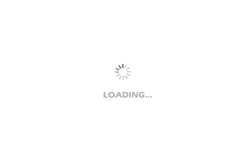
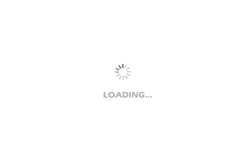
- Popular Resources
- Popular amplifiers
-
Microgrid Stability Analysis and Control Microgrid Modeling Stability Analysis and Control to Improve Power Distribution and Power Flow Control (
-
Modern Electronic Technology Training Course (Edited by Yao Youfeng)
-
New Energy Vehicle Control System Inspection and Maintenance (Edited by Bao Pili)
-
Intelligent Control Technology of Permanent Magnet Synchronous Motor (Written by Wang Jun)
- MathWorks and NXP Collaborate to Launch Model-Based Design Toolbox for Battery Management Systems
- STMicroelectronics' advanced galvanically isolated gate driver STGAP3S provides flexible protection for IGBTs and SiC MOSFETs
- New diaphragm-free solid-state lithium battery technology is launched: the distance between the positive and negative electrodes is less than 0.000001 meters
- [“Source” Observe the Autumn Series] Application and testing of the next generation of semiconductor gallium oxide device photodetectors
- 采用自主设计封装,绝缘电阻显著提高!ROHM开发出更高电压xEV系统的SiC肖特基势垒二极管
- Will GaN replace SiC? PI's disruptive 1700V InnoMux2 is here to demonstrate
- From Isolation to the Third and a Half Generation: Understanding Naxinwei's Gate Driver IC in One Article
- The appeal of 48 V technology: importance, benefits and key factors in system-level applications
- Important breakthrough in recycling of used lithium-ion batteries
- Innolux's intelligent steer-by-wire solution makes cars smarter and safer
- 8051 MCU - Parity Check
- How to efficiently balance the sensitivity of tactile sensing interfaces
- What should I do if the servo motor shakes? What causes the servo motor to shake quickly?
- 【Brushless Motor】Analysis of three-phase BLDC motor and sharing of two popular development boards
- Midea Industrial Technology's subsidiaries Clou Electronics and Hekang New Energy jointly appeared at the Munich Battery Energy Storage Exhibition and Solar Energy Exhibition
- Guoxin Sichen | Application of ferroelectric memory PB85RS2MC in power battery management, with a capacity of 2M
- Analysis of common faults of frequency converter
- In a head-on competition with Qualcomm, what kind of cockpit products has Intel come up with?
- Dalian Rongke's all-vanadium liquid flow battery energy storage equipment industrialization project has entered the sprint stage before production
- Allegro MicroSystems Introduces Advanced Magnetic and Inductive Position Sensing Solutions at Electronica 2024
- Car key in the left hand, liveness detection radar in the right hand, UWB is imperative for cars!
- After a decade of rapid development, domestic CIS has entered the market
- Aegis Dagger Battery + Thor EM-i Super Hybrid, Geely New Energy has thrown out two "king bombs"
- A brief discussion on functional safety - fault, error, and failure
- In the smart car 2.0 cycle, these core industry chains are facing major opportunities!
- The United States and Japan are developing new batteries. CATL faces challenges? How should China's new energy battery industry respond?
- Murata launches high-precision 6-axis inertial sensor for automobiles
- Ford patents pre-charge alarm to help save costs and respond to emergencies
- New real-time microcontroller system from Texas Instruments enables smarter processing in automotive and industrial applications
- 2. Hardware Introduction and Development Environment Installation
- 【New Year's Festival Competition】+ Watching Lanterns on the Lantern Festival (multiple photos)
- 5G small base stations are under the spotlight: now is the eve of the outbreak
- 【CH579M-R1】+ PWM breathing light
- [Experience] [Free trial of Letuo USB oscilloscope] Comparison test of Letuo USB oscilloscope
- Wi-Fi 6E scarcity causes enterprises to delay upgrades until Wi-Fi 7 devices ship
- [RISC-V MCU CH32V103 Evaluation] W25Q16 Reading, Writing and Application
- 【GD32E231 DIY Contest】1. USART0
- When a plane crashes, is there any technology that can completely guarantee the safety of passengers?
- STMicroelectronics launches the second generation multi-zone time-of-flight sensor VL53L8