Trying to reduce the supply voltage of the core processor is one of the new technology trends in handheld devices. While reducing the voltage, it is also necessary to take into account the need to extend battery life with higher efficiency. Currently, there are many new functions in these devices that require step-down conversion, such as application processors, memory, and radio frequency (RF) design. From the perspective of load and space parameters, the most popular solutions for such applications are switching regulators and low dropout (LDO) regulators.
If efficiency is the only consideration, a switching regulator is the best choice. However, when the height of electronic components and the size of the solution exceed the use range of inductors, the converter may be replaced by an LDO or switched capacitor (SC) regulator. The power solution usually cannot provide more circuit board space, but the switching regulator can provide a larger solution size than LDO and switched capacitor regulators.
We use DC/DC switched capacitor regulators to improve the efficiency of power supplies, so what are the advantages of switched capacitors?
Switched capacitors maintain efficiency for a given load
As VIN increases, the energy generated by the converter between VIN and VOUT increases, causing power loss and reduced efficiency. The solution to this problem is to shift to a higher efficiency gain, just like changing gears in a car. The switched capacitor analog has an analog gain control and changes to keep the efficiency constant for a given load. The switched capacitor has discrete gain steps, and the efficiency is given by VOUT/(gain×VIN), and these efficiencies depend on the discrete gain. An LDO has only one gain and the lowest efficiency of the three. The switched capacitor regulator has three different voltage gains, namely 2/3, 1/2 and 1/3.
As VIN increases, the voltage gain of the SC regulator changes from 2/3 to 1/2 and 1/2 to 1/3, thus maximizing efficiency over the entire load range, delivering 80% of the power over the 3.4 to 3.8 volt range of the lithium-ion battery. In the same application, an LDO achieves only 50% efficiency. A typical switching regulator should have 88 to 90% efficiency, depending on the type of inductor.
Traditionally, regulators are compared based on effective quantity, but due to the characteristics of lithium-ion batteries, they are judged based on time efficiency or the time required for a lithium-ion battery to be fully discharged. As a rule of thumb, using a load current of 200 mA, using a typical switching regulator can last 6 to 8% longer than using a switched capacitor regulator. Assuming that the maximum load is the same as in a microprocessor, it only lasts 20 to 30% of the time, then the difference in operating time between the inductive switch and switched capacitor regulators is negligible. A trade-off must be made between efficiency and cost
More gain in a switched capacitor regulator may increase efficiency slightly, but requires more external capacitors and internal field effect transistors (FETs), which increases cost and solution size. The above gain can be achieved through two external capacitors or flying capacitors (CFLY). These capacitors are used to store charge and transfer charge from VIN to VOUT. In addition to the flying capacitors, an input capacitor (CIN) and an output capacitor (COUT) are required. The input capacitor indicates the voltage ripple, while the output capacitor controls the output voltage ripple. According to the acceptable ripple standard values of VIN and VOUT, the general range of CIN and COUT values is from 1 to 10 microfarads, and the number of CFLY is usually less than COUT. The external capacitors are connected to the chip through the internal power FETs in different configurations.
To use a switched capacitor regulator to regulate the output voltage, consider using pulse frequency modulation (PFM) or pulse width modulation (PWM). The output impedance of a switched capacitor regulator is proportional to the switching frequency and the resistance of the internal power FET. By modulating the output impedance, the converter can then step down the voltage for a given load. Using feedback, the frequency or internal FET impedance can be controlled to regulate the output voltage, and the PFM solution is a more traditional method.
In a PFM system, if the output voltage is higher than a specified value, the regulator will shut down and restart when the output voltage drops below the required value. The advantage of using the PFM control mode is that the operating voltage depends on VIN and ILOAD, and both can be adjusted. The higher the load, the closer the operating frequency is to the specified frequency, but the frequency variation within this operating range may not be suitable for some portable applications. The input voltage ripple also depends on VIN and ILOAD. The output ripple of a 10 microfarad COUT will be 50 millivolts. It can be seen that the ripple frequency of a 250 milliampere load is higher than the ripple frequency of a 10 milliampere load.
Voltage deviation leads to reduced LDO efficiency
LDOs are most efficient when the required voltage is close to the battery voltage, but if the voltage deviates far from the value, the LDO efficiency will drop very low. For example, when charging a microprocessor lithium-ion battery that only requires 1.5 volts at 3.6 volts, connecting the battery voltage to the 1.5 volt LDO can generate a complete, stable and small amount of power for the microprocessor , but the power consumption is very obvious.
The power consumption (PD) of LDO is equal to the load current (ILOAD) multiplied by the difference between the input and output voltages, that is, PD = ILOAD × (3.6 ~ 1.5) = ILOAD × 2.3 V. In other words, in this example, if LDO is used as a buck converter, only 42% efficiency is generated, which means that LDO consumes excess power and greatly increases the chip (Die) temperature, and this temperature rise will cause device reliability-related issues.
Switched capacitor regulators are more efficient solutions than linear regulators due to their voltage gain capability. This voltage gain is achieved by stacking capacitors and parallel capacitors in both phases, i.e., the charging phase and the transmission phase, to achieve an input voltage to output voltage ratio. For example, 1/2 of a switched capacitor converter in a gain configuration will convert a 3.6 volt input voltage (VIN) to a 1.8 volt output voltage (VOUT); if the required output voltage is 1.5 volts, the power consumption is only 300 millivolts times the load current, equivalent to 83% efficiency. PWM mode can be fixed operating frequency/duty cycle
When dealing with various frequencies and high output ripples in the PFM architecture, most switched capacitor regulators use PWM modulation mode. The power FET resistance is controlled according to VOUT and ILOAD to control the amount of charge provided by the flying capacitor. This is called pre-modulation. In this mode, the operating frequency and duty cycle are fixed.
Switched capacitor regulator is an emerging technology that combines the advantages of switched capacitors and LDOs, that is, integrating the efficiency and small size solutions of the lithium-ion battery range into portable applications. Recently, topology technology also uses smaller values of passive components to achieve lower noise. Many functions in portable devices require buck regulators to have smaller size and higher efficiency, and switched capacitor solutions are ideal.
Previous article:Switching Power Supply Design—Transformer Process
Next article:Power supply design tips: how to meet electromagnetic interference requirements
Recommended ReadingLatest update time:2024-11-17 01:41
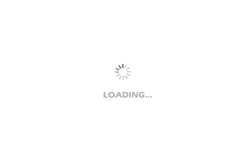
- Popular Resources
- Popular amplifiers
-
Research on design technology of high-efficiency step-up DC-DC converter with wide load range
-
Design and implementation of current-fed DC-DC converter based on digital control
-
Switching power supply design based on charge pump DC-DC converter
-
Design and simulation of Buck DC-DC power supply based on LM3150
- MathWorks and NXP Collaborate to Launch Model-Based Design Toolbox for Battery Management Systems
- STMicroelectronics' advanced galvanically isolated gate driver STGAP3S provides flexible protection for IGBTs and SiC MOSFETs
- New diaphragm-free solid-state lithium battery technology is launched: the distance between the positive and negative electrodes is less than 0.000001 meters
- [“Source” Observe the Autumn Series] Application and testing of the next generation of semiconductor gallium oxide device photodetectors
- 采用自主设计封装,绝缘电阻显著提高!ROHM开发出更高电压xEV系统的SiC肖特基势垒二极管
- Will GaN replace SiC? PI's disruptive 1700V InnoMux2 is here to demonstrate
- From Isolation to the Third and a Half Generation: Understanding Naxinwei's Gate Driver IC in One Article
- The appeal of 48 V technology: importance, benefits and key factors in system-level applications
- Important breakthrough in recycling of used lithium-ion batteries
- Innolux's intelligent steer-by-wire solution makes cars smarter and safer
- 8051 MCU - Parity Check
- How to efficiently balance the sensitivity of tactile sensing interfaces
- What should I do if the servo motor shakes? What causes the servo motor to shake quickly?
- 【Brushless Motor】Analysis of three-phase BLDC motor and sharing of two popular development boards
- Midea Industrial Technology's subsidiaries Clou Electronics and Hekang New Energy jointly appeared at the Munich Battery Energy Storage Exhibition and Solar Energy Exhibition
- Guoxin Sichen | Application of ferroelectric memory PB85RS2MC in power battery management, with a capacity of 2M
- Analysis of common faults of frequency converter
- In a head-on competition with Qualcomm, what kind of cockpit products has Intel come up with?
- Dalian Rongke's all-vanadium liquid flow battery energy storage equipment industrialization project has entered the sprint stage before production
- Allegro MicroSystems Introduces Advanced Magnetic and Inductive Position Sensing Solutions at Electronica 2024
- Car key in the left hand, liveness detection radar in the right hand, UWB is imperative for cars!
- After a decade of rapid development, domestic CIS has entered the market
- Aegis Dagger Battery + Thor EM-i Super Hybrid, Geely New Energy has thrown out two "king bombs"
- A brief discussion on functional safety - fault, error, and failure
- In the smart car 2.0 cycle, these core industry chains are facing major opportunities!
- Rambus Launches Industry's First HBM 4 Controller IP: What Are the Technical Details Behind It?
- The United States and Japan are developing new batteries. CATL faces challenges? How should China's new energy battery industry respond?
- Murata launches high-precision 6-axis inertial sensor for automobiles
- Ford patents pre-charge alarm to help save costs and respond to emergencies
- First look at TMS320C5410
- [Mill MYB-YT507 development board trial experience] + build QT development environment and test, the most detailed steps to solve all troubles
- [Repost] Advantages and process of dry etching
- Microphone noise problem
- How to ensure IoT security
- LTC2323-12 chip does not work
- A brief analysis of the power amplifier in RF chips
- 【ST NUCLEO-G071RB Review】_04_UART Experiment
- ELT8629 chip
- MicroPython driver for non-volatile memory