This trend has a profound impact on the entire electronics supply chain and is a challenge faced by suppliers at every stage. To take full advantage of this development trend, engineering design teams need a design automation tool that is more flexible in conceiving and innovating PCBs. The design rules under the new standard are also challenging, so EDA tool suppliers are focusing on these issues to enable more OEMs to adopt this highly competitive and revolutionary technology.
element
There are two main ways to connect components to substrates: molded connections and embedded connections. The former effectively utilizes copper plating and resistive films to produce passive (resistive, capacitive, inductive) components in the embedded layer (or surface layer); the latter is a gradual process that can install discontinuous components, bare chips and even modules under the surface of the substrate material.
This approach has many advantages, the most important of which is its component density. It is worth mentioning that the increased demand for passive components (especially capacitors that can handle higher operating frequencies and signal frequencies) has also created a new trend, namely vertical stacking of components to minimize trace lengths. Texas Instruments recently launched a 500mA DC-DC step-down converter that is only 2.3mm long, 2.0mm wide, and 1.0mm high.
Component manufacturers must continue to meet people's demand for packaging changes when launching new products, as well as the widespread use of surface mount technology, especially in passive components, which can better embed components into PCB substrates. As SMT profiles become smaller and smaller, these components can be directly mounted or embedded in PCB substrates with chips. For example, the 01005 (0402) series is only 0.4mm long, 0.22mm wide, and 0.15mm high.
However, this connection method has further requirements, which are mainly divided into two types: using traditional soldering methods or using copper-plated holes. If soldering is used, then general tin-plated multilayer ceramic capacitors can be used, but there will be certain risks when embedding. Secondary heating (such as when performing surface mounting) will cause solder paste and embedded components to reflow and may eventually lead to operational failure.
In order to avoid solder reflow problems, the industry is replacing soldered components with copper-plated holes, but requires the electrodes of the components to be copper (not tin) for better connection. Therefore, the industry is now also starting to produce SMT devices with copper electrodes. For example, Japan's Murata Company's GRU series embedded capacitors are specially designed for embedded components.
manufacture
In the traditional workflow, the various stages of manufacturing are often discontinuous: the bare board is manufactured first, then sent to the assembly factory, and the PCB board is assembled by the component placement machine.
Embedded components will improve this phenomenon: the various stages are no longer separate, and the components must be connected to the PCB board during production and manufacturing. This is a severe challenge for the PCB industry and equipment manufacturers. Whether during or after the PCB substrate assembly process, the components are always embedded in the substrate grooves. If the components are embedded after the PCB assembly, the grooves will be exposed on the surface. If the components are to be fully embedded in the multilayer board, it can only be operated by the PCB manufacturer, which also creates new market opportunities for SMT component placement machine manufacturers.
Accordingly, SMT placement machine manufacturers also need to consider the placement of embedded components. Usually, the maximum production tolerance allowed for embedded grooves is only 20um, which requires SMT placement to have a higher accuracy. For example, the automatic proofreading function of solder paste can improve accuracy to a certain extent, but it is not applicable to embedded components.
In addition, the force used when placing components must be accurately controlled. Damage to surface mounted components during placement can be detected during appearance inspection; in contrast, damage to embedded components cannot be detected by the naked eye, and once a rupture is found, the entire substrate will fail. Sudden thermal events (such as reflow during surface mounted components) can also significantly reduce the integrity of embedded components.
Manufacturing equipment suppliers strive to achieve standards and operating specifications when embedding components in order to gain both functional and commercial benefits for the industry.
EDA Tools
The electronics industry has successfully introduced the concept of embedded active components and has made it a mainstream trend. Although large OEMs are targeting consumer devices where every inch of space is valuable, OEMs of all sizes are beginning to take advantage of the benefits of embedded components as smaller design teams have grown in recent years.
This support mainly comes from EDA suppliers. For example, the latest release of Altium Designer 14 uses the leading board-level design environment to create PCB boards with grooves to support embedded components.
More PCB board manufacturing processes can accommodate more embedded components through grooving and laser drilling, as shown in Figure 1.

Figure 1: PCB manufacturing process for embedded components. The circuit board is manufactured using a stacking technique, with the embedded components embedded or encased in it. Laser micro-drilling is used to connect the embedded components on the lower side.
To take advantage of this feature, Altium Designer 14 (AD14) supports a Region attribute called Cavity Definition, which can be associated with the Height attribute to allow components to be placed on any signal layer. In order to be fully embedded, the groove of the component must extend to the edge of the PCB board, so that it is open on the side, which is particularly important when embedding SMD LEDs. As shown in Figure 2, the groove for assembling SMD LEDs on a circular PCB board designed by Altium Designer 14.
Figure 2: A notch designed for an SMT LED in a round PCB.

By editing the component properties, the layer can be treated as an inner layer, and the orientation of the embedded component is also determined by the orientation of this layer (which can be overridden by checking the Fipped on Layer option).
If embedded in this way, Altium Designer 14 can automatically generate a Managed Stack that defines the substrate structure in the Z plane.
There are currently several ways for developers to embed active components: module board (IMB), embedded wafer level package (EWCP), embedded chip stack (ECBU) and polymer embedded chip (CIP). The last method can embed thin wafer packages directly into the stacked dielectric layer instead of using grooves connected to the core material through drilling or routing. This method also supports FR-4 multilayer circuit boards.
When designing embedded components, in order to ensure success, it is important to communicate fully with the PCB manufacturer. Table 1 lists the documents and design files recommended to be provided to the PCB manufacturer.

Summarize
Large OEMs have been using embedded components in a large number of consumer applications for more than a decade, and its availability and technical support are gradually increasing in the electronics supply chain, which in turn has created new opportunities for OEMs of all sizes to target vertical markets and better develop their own advantages. Design engineers are the interface to the supply chain, and EDA vendors provide tools to achieve seamless and efficient interface connections. By supporting embedded components in PCB design, Altium ensures that effective electronic product design can be performed at all levels.
Previous article:Low-cost isoSPI coupling circuit for high-voltage, high-capacity battery systems
Next article:Detailed explanation of the conceptual differences between ADC accuracy and resolution
Recommended ReadingLatest update time:2024-11-16 21:43
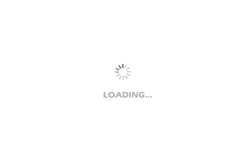
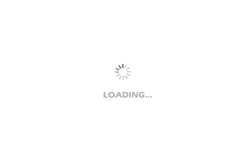
- Popular Resources
- Popular amplifiers
-
Semantic Segmentation for Autonomous Driving: Model Evaluation, Dataset Generation, Viewpoint Comparison, and Real-time Performance
-
Machine Learning and Embedded Computing in Advanced Driver Assistance Systems (ADAS)
-
Intelligent program synthesis framework and key scientific problems for embedded software
-
arm_embedded_machine_learning_design_dummies_guide
- MathWorks and NXP Collaborate to Launch Model-Based Design Toolbox for Battery Management Systems
- STMicroelectronics' advanced galvanically isolated gate driver STGAP3S provides flexible protection for IGBTs and SiC MOSFETs
- New diaphragm-free solid-state lithium battery technology is launched: the distance between the positive and negative electrodes is less than 0.000001 meters
- [“Source” Observe the Autumn Series] Application and testing of the next generation of semiconductor gallium oxide device photodetectors
- 采用自主设计封装,绝缘电阻显著提高!ROHM开发出更高电压xEV系统的SiC肖特基势垒二极管
- Will GaN replace SiC? PI's disruptive 1700V InnoMux2 is here to demonstrate
- From Isolation to the Third and a Half Generation: Understanding Naxinwei's Gate Driver IC in One Article
- The appeal of 48 V technology: importance, benefits and key factors in system-level applications
- Important breakthrough in recycling of used lithium-ion batteries
- Innolux's intelligent steer-by-wire solution makes cars smarter and safer
- 8051 MCU - Parity Check
- How to efficiently balance the sensitivity of tactile sensing interfaces
- What should I do if the servo motor shakes? What causes the servo motor to shake quickly?
- 【Brushless Motor】Analysis of three-phase BLDC motor and sharing of two popular development boards
- Midea Industrial Technology's subsidiaries Clou Electronics and Hekang New Energy jointly appeared at the Munich Battery Energy Storage Exhibition and Solar Energy Exhibition
- Guoxin Sichen | Application of ferroelectric memory PB85RS2MC in power battery management, with a capacity of 2M
- Analysis of common faults of frequency converter
- In a head-on competition with Qualcomm, what kind of cockpit products has Intel come up with?
- Dalian Rongke's all-vanadium liquid flow battery energy storage equipment industrialization project has entered the sprint stage before production
- Allegro MicroSystems Introduces Advanced Magnetic and Inductive Position Sensing Solutions at Electronica 2024
- Car key in the left hand, liveness detection radar in the right hand, UWB is imperative for cars!
- After a decade of rapid development, domestic CIS has entered the market
- Aegis Dagger Battery + Thor EM-i Super Hybrid, Geely New Energy has thrown out two "king bombs"
- A brief discussion on functional safety - fault, error, and failure
- In the smart car 2.0 cycle, these core industry chains are facing major opportunities!
- The United States and Japan are developing new batteries. CATL faces challenges? How should China's new energy battery industry respond?
- Murata launches high-precision 6-axis inertial sensor for automobiles
- Ford patents pre-charge alarm to help save costs and respond to emergencies
- New real-time microcontroller system from Texas Instruments enables smarter processing in automotive and industrial applications
- About the sending problem of single chip microcomputer serial port mode 3
- Week 1: Learn about the hardware information of the development board
- imx6ull transplant alsa
- Central media report: Beixing is becoming a potential unicorn company
- "Playing with the board" + Zhou Hangci's book Chapter 8, Example 4
- Experts who are familiar with 7135 are welcome to explain and discuss if interested.
- Recommend a fast source code style conversion tool AStyle
- Is there something wrong with the advanced search?
- 【Silicon Labs BG22-EK4108A Bluetooth Development Review】 + First Look at the W7230F1 Development Board
- (c = getchar()) Under what circumstances will it be equal to EOF?