This kind of controller was made in 2007. At that time, it was made on street lamps and used an 8-pin single-chip microcomputer . In fact, this PWM controller is very mature and the market price is very low. Since this control method is actually similar to a switch, it basically does not generate any heat when working.
All PWM is the simplest way, because this is used for 48V 96V. The open circuit voltage of the solar panel may exceed 200V DC. In order to improve reliability, it is necessary to design an independent auxiliary power supply to provide to the CPU and drive circuit. The charging current is 50-100A. Because it is a PWM control method, the loss on the MOSFET is very small, and only a small heat sink is needed to fix the MOSFET.
The following are the actual photos:
In fact, the current PWM control method is simply a set of MOSFET switches. Just think of this MOS as a relay . At night, a set of MOSFETs are turned off to prevent the battery from discharging reversely to the battery board. I used TLP250 as the driver. And this does not require a fan, because the radiator is used for conducting electricity, and there is no air cooling requirement.
The switching frequency on the MOSFET is very low, less than 1KHZ. A set of PWM pulses is generated by the single-chip microcomputer, and then a battery voltage sampling is performed and a PI adjustment is performed, and it is OK. In fact, the duty cycle can reach 100%, because my driver is an optocoupler and a separate isolated power supply is used. When the duty cycle reaches 100%, the MOSFET is equivalent to directly passing through the solar panel and battery voltage.
Previous article:LT3840 Power Supply Design Application Circuit Diagram Collection
Next article:Detailed explanation of the design of barrier-free boost circuit for notebook power supply
Recommended ReadingLatest update time:2024-11-16 17:50
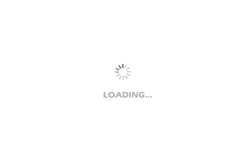
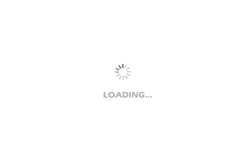
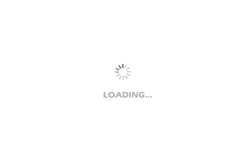
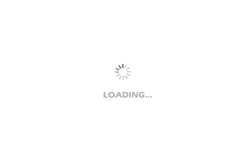
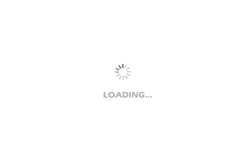
- Popular Resources
- Popular amplifiers
-
西门子S7-12001500 PLC SCL语言编程从入门到精通 (北岛李工)
-
Small AC Servo Motor Control Circuit Design (by Masaru Ishijima; translated by Xue Liang and Zhu Jianjun, by Masaru Ishijima, Xue Liang, and Zhu Jianjun)
-
Intelligent Control Technology of Permanent Magnet Synchronous Motor (Written by Wang Jun)
-
100 Examples of Microcontroller C Language Applications (with CD-ROM, 3rd Edition) (Wang Huiliang, Wang Dongfeng, Dong Guanqiang)
- MathWorks and NXP Collaborate to Launch Model-Based Design Toolbox for Battery Management Systems
- STMicroelectronics' advanced galvanically isolated gate driver STGAP3S provides flexible protection for IGBTs and SiC MOSFETs
- New diaphragm-free solid-state lithium battery technology is launched: the distance between the positive and negative electrodes is less than 0.000001 meters
- [“Source” Observe the Autumn Series] Application and testing of the next generation of semiconductor gallium oxide device photodetectors
- 采用自主设计封装,绝缘电阻显著提高!ROHM开发出更高电压xEV系统的SiC肖特基势垒二极管
- Will GaN replace SiC? PI's disruptive 1700V InnoMux2 is here to demonstrate
- From Isolation to the Third and a Half Generation: Understanding Naxinwei's Gate Driver IC in One Article
- The appeal of 48 V technology: importance, benefits and key factors in system-level applications
- Important breakthrough in recycling of used lithium-ion batteries
- Innolux's intelligent steer-by-wire solution makes cars smarter and safer
- 8051 MCU - Parity Check
- How to efficiently balance the sensitivity of tactile sensing interfaces
- What should I do if the servo motor shakes? What causes the servo motor to shake quickly?
- 【Brushless Motor】Analysis of three-phase BLDC motor and sharing of two popular development boards
- Midea Industrial Technology's subsidiaries Clou Electronics and Hekang New Energy jointly appeared at the Munich Battery Energy Storage Exhibition and Solar Energy Exhibition
- Guoxin Sichen | Application of ferroelectric memory PB85RS2MC in power battery management, with a capacity of 2M
- Analysis of common faults of frequency converter
- In a head-on competition with Qualcomm, what kind of cockpit products has Intel come up with?
- Dalian Rongke's all-vanadium liquid flow battery energy storage equipment industrialization project has entered the sprint stage before production
- Allegro MicroSystems Introduces Advanced Magnetic and Inductive Position Sensing Solutions at Electronica 2024
- Car key in the left hand, liveness detection radar in the right hand, UWB is imperative for cars!
- After a decade of rapid development, domestic CIS has entered the market
- Aegis Dagger Battery + Thor EM-i Super Hybrid, Geely New Energy has thrown out two "king bombs"
- A brief discussion on functional safety - fault, error, and failure
- In the smart car 2.0 cycle, these core industry chains are facing major opportunities!
- The United States and Japan are developing new batteries. CATL faces challenges? How should China's new energy battery industry respond?
- Murata launches high-precision 6-axis inertial sensor for automobiles
- Ford patents pre-charge alarm to help save costs and respond to emergencies
- New real-time microcontroller system from Texas Instruments enables smarter processing in automotive and industrial applications
- 5 important attributes of EMC analysis
- Bandwidth Management System (BWM) for TI C64x+ DSPs
- C++Primer Plus (Sixth Edition) Chinese Edition
- Xunwei RK3399 development board supports installing Docker in Ubuntu system
- Looking for a KICAD engineer
- MATLAB simulation model for parameter identification of three-phase asynchronous motor at static state
- 【CC1352P Review】What is a Sensor controller?
- The shell of the pycom development board
- Common switching power supply transformer design core size and AE area
- Thank you + my family, girlfriend, and friends