LED now occupies a large position in the power supply market. Its advantages such as high brightness, low power consumption, long life, fast startup, low power, no flicker, and low visual fatigue make it an important factor in consumers' praise. In the power supply industry, LED isolation and non-isolation are probably the two most commonly heard terms. So what are they? What is the difference between the two? The editor will use this article to help you understand the two.
Mainly from the following aspects:
safety
An isolated power supply uses a transformer to reduce the 220V voltage to a lower voltage, and then rectifies it into a DC output for power supply. Because the primary coil of the transformer bears the 220V voltage, the secondary coil only bears the output low AC voltage, and the primary and secondary coils are not directly connected, it is called an isolated power supply. The conversion process of the transformer is: electricity-magnetism-electricity, and it is not connected to the ground, so there is no danger of electric shock.
The non-isolated power supply is a 220V power supply that is directly input to the electronic circuit and then stepped down by electronic components. The input and output are directly connected through electronic components, so it is called a non-isolated power supply. The difference between the two is the presence or absence of a transformer. LED non-isolated design is limited to double-insulated products, such as bulb replacement products, where the LED and the entire product are integrated and sealed in non-conductive plastic, so the end user does not have any risk of electric shock. Secondary products are all isolated and relatively expensive. Non-isolated circuits are input power supplies that are directly added to the LED load after stepping up and down, which poses a risk of electric shock.
Therefore, if you want to pass safety certification, such as 3C, UL, CE, etc., non-isolation is troublesome. Generally, manufacturers do not have absolute design and technical strength, and it is generally difficult to pass. Because the insulation and creepage distance are not enough, you can only design from the physical structure of the lamp. The lamp tube is acceptable, and there are also full plastic ones. For example, the insulation between the LED and the aluminum heat sink
However, as a complete LED lighting product, the part of the product surface that users can touch must be isolated to prevent electric shock. From the perspective of the entire product system, isolation is inevitable, the only difference is the location of the isolation. As a product that can be used safely by end users, the reliability of insulation and isolation must be considered.
Note: It should be noted that in order to save costs, some manufacturers use the method of directly tapping the main coil to extract low voltage. This method seems to have a transformer, but actually there is no secondary coil, and it cannot be regarded as an isolated power supply!
Electrical properties
In terms of performance, the advantages of isolated power supply are: no threat to human body, good wide voltage performance, non-isolated is also very mature now, the voltage range is slightly worse than isolated, the voltage range is between 110V-300V; while isolated power supply can reach 60-300V. High and low currents are very uniform. Isolated drive is safe but less efficient, non-isolated drive is more efficient, and isolated or non-isolated drive should be selected according to actual use requirements.
In terms of constant current accuracy: the isolated type can achieve within ±5%, while the non-isolated type is difficult to achieve.
Non-isolated circuits are very sensitive to surges and have poor suppression capabilities. Lightning surges are instantaneous high voltages, up to several thousand volts, very short duration, and extremely strong. When this voltage enters the power supply, it will instantly transmit to the output for non-isolated buck circuits, damaging the constant current detection loop, or further damaging the chip, causing a 300v direct pass, and burning the entire lamp tube. In fact, it refers to non-isolated power supplies. When shipped in batches, the return rate is higher than that of isolated LED driver power supplies, mostly because of explosions. The probability of explosions of isolated power supplies is much smaller, and the probability of explosions of non-isolated power supplies is generally around 2% to 3%.
Many power grids have unstable voltages, and isolation will also occur. The phenomenon is that chips, MOS tubes , and constant current loops are all burned out, but isolation is relatively less.
Note: Therefore, non-isolated surge protection varistors are essential, and any warranty without varistor performance is just empty talk. Cost and efficiency
The cost of electronic products is not only the design and production cost, but also the maintenance cost for large-volume products. As for the circuit structure of LED power supply , the current isolation type solutions are mostly AC/DC flyback circuit solutions, so the circuit is relatively complex and the cost is relatively high. The non-isolated type basically adopts the DC/DC boost or buck circuit, which is relatively simple, so the cost is relatively low.
Since non-isolated power supplies do not have the energy loss of voltage transformation, their efficiency can generally reach over 90%, and they have a higher power factor. However, the energy efficiency of isolated power supplies is generally 88%, depending on the power, so the heat generated by isolated power supplies is also relatively large.
Non-isolated power supplies have advantages over isolated power supplies in terms of efficiency and cost. It is not easy to make isolated power supplies more efficient. If they are not handled properly, they will generate a lot of heat and be costly, especially for LED fluorescent lamps with built-in lamps. However, non-isolated power supplies have poor lightning surge voltage suppression capabilities, so they will be damaged a lot when shipped in large quantities.
Compared with isolated power supplies, non-isolated power supplies mainly reduce transformers and design the architecture with the least amount of materials to achieve the same product functions, so non-isolated power supplies have a greater cost advantage. This is probably why non-isolated power supplies are very popular in China.
Note: In low-voltage powered LED lamps, based on the principle of efficiency and cost priority, non-isolated solutions are actually the best choice.
Use occasions
Whether to use an isolated insulating transformer or an isolated protective lamp housing usually requires analysis from many aspects, such as cost and manufacturing process, efficiency and volume, insulation reliability and safety regulations. Both types of designs will continue to be used because each design meets different market needs.
In terms of load range, generally speaking, the output load range of isolated power supply is 30-42V, and the output load range of non-isolated power supply can be 30-84V. When selecting power supply, many LED manufacturers require the power supply to adapt to the full voltage 90-265V input for overall adaptability, and the load range is also required to be as high as 84V. Such a choice has certain risks and hidden dangers. When the input is 90V, the power supply may lose the constant current function, THD, etc. Non-isolated power supply is suitable for high voltage and low current, and the cost of large current is not cheaper than that of isolated power supply.
Non-isolated power supplies are suitable for the following occasions: First, indoor lamps. This kind of indoor power environment is better and the surge impact is small. For straw hats and SMD LEDs, the occasions of use are high voltage and small current. It is meaningless to use non-isolation for low voltage and large current, because the efficiency of low voltage and large current non-isolation is not higher than that of isolation, and the cost is not much lower. It is not suitable for centralized lighting. What is centralized lighting? It means that hundreds of lamps are lit on the same AC line. At this time, because there are too many lamps on one line, the voltage environment on this line is relatively dirty, so the probability of damaging the lamps becomes greater. Therefore, LED lamps made of non-isolated power supplies.
From the perspective of the entire product system, isolation is inevitable, the only difference is the location of the isolation. Some designers use an isolated transformer design so that they can simplify the design of heat dissipation and lampshade. If a non-isolated driver design is used, reliable insulation requirements must be considered in the lamp housing and other structures.
Note: As a power driver, isolated and non-isolated solutions always exist at the same time.
Due to the above points, these two types of power supplies have their own advantages. Non-isolated power supplies focus on higher power factor and efficiency, reducing energy loss; while isolated power supplies focus on life safety and the overall safety of fluorescent lamps, and are slightly inferior to non-isolated power supplies in terms of power factor and efficiency. There are no rigid regulations on different power supply types for different occasions and different usage environments.
Previous article:The requirements of the power-on pulse on the selection of LED lighting fuses
Next article:Selection of LED driver topology and example analysis
Recommended ReadingLatest update time:2024-11-16 14:48
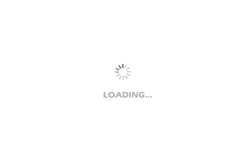
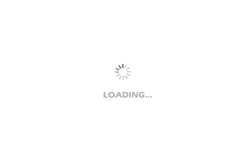
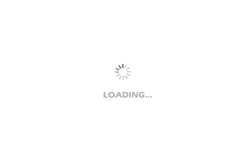
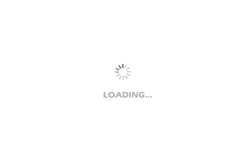
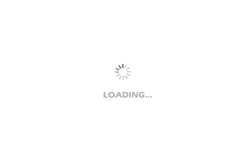
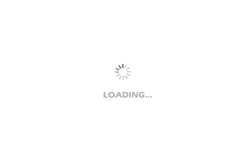
- Popular Resources
- Popular amplifiers
- MathWorks and NXP Collaborate to Launch Model-Based Design Toolbox for Battery Management Systems
- STMicroelectronics' advanced galvanically isolated gate driver STGAP3S provides flexible protection for IGBTs and SiC MOSFETs
- New diaphragm-free solid-state lithium battery technology is launched: the distance between the positive and negative electrodes is less than 0.000001 meters
- [“Source” Observe the Autumn Series] Application and testing of the next generation of semiconductor gallium oxide device photodetectors
- 采用自主设计封装,绝缘电阻显著提高!ROHM开发出更高电压xEV系统的SiC肖特基势垒二极管
- Will GaN replace SiC? PI's disruptive 1700V InnoMux2 is here to demonstrate
- From Isolation to the Third and a Half Generation: Understanding Naxinwei's Gate Driver IC in One Article
- The appeal of 48 V technology: importance, benefits and key factors in system-level applications
- Important breakthrough in recycling of used lithium-ion batteries
- Innolux's intelligent steer-by-wire solution makes cars smarter and safer
- 8051 MCU - Parity Check
- How to efficiently balance the sensitivity of tactile sensing interfaces
- What should I do if the servo motor shakes? What causes the servo motor to shake quickly?
- 【Brushless Motor】Analysis of three-phase BLDC motor and sharing of two popular development boards
- Midea Industrial Technology's subsidiaries Clou Electronics and Hekang New Energy jointly appeared at the Munich Battery Energy Storage Exhibition and Solar Energy Exhibition
- Guoxin Sichen | Application of ferroelectric memory PB85RS2MC in power battery management, with a capacity of 2M
- Analysis of common faults of frequency converter
- In a head-on competition with Qualcomm, what kind of cockpit products has Intel come up with?
- Dalian Rongke's all-vanadium liquid flow battery energy storage equipment industrialization project has entered the sprint stage before production
- Allegro MicroSystems Introduces Advanced Magnetic and Inductive Position Sensing Solutions at Electronica 2024
- Car key in the left hand, liveness detection radar in the right hand, UWB is imperative for cars!
- After a decade of rapid development, domestic CIS has entered the market
- Aegis Dagger Battery + Thor EM-i Super Hybrid, Geely New Energy has thrown out two "king bombs"
- A brief discussion on functional safety - fault, error, and failure
- In the smart car 2.0 cycle, these core industry chains are facing major opportunities!
- The United States and Japan are developing new batteries. CATL faces challenges? How should China's new energy battery industry respond?
- Murata launches high-precision 6-axis inertial sensor for automobiles
- Ford patents pre-charge alarm to help save costs and respond to emergencies
- New real-time microcontroller system from Texas Instruments enables smarter processing in automotive and industrial applications
- 【Showing goods】The second wave
- EEWORLD University ---- HVI Series: Mastering the Art and Fundamentals of High Voltage Gate Driver Design
- How to enable TMU of 28377d.
- "【TGF4042 Signal Generator】" Potential Compensation Test
- MCU Programming_Interrupt
- Using TI power timing controller in 5G MIMO application
- MCU development full-time/part-time and sales assistant
- G100 acoustic imager is used in many product development and fault diagnosis fields
- The moon rises over the sea, and the world is sharing this moment
- Treatment of cross-partition area and slot in EMC design of power board