In the process of electronic circuit design, how to continuously improve the power factor has always been a problem that many developers have been studying. PWM rectifier circuit is a rectifier circuit that uses PWM control, which can effectively improve the power factor of the circuit. This article will explain the working principle of the single-phase full-bridge PWM rectifier circuit, hoping to provide convenience for power supply novices.
figure 1
As shown in Figure 1, the comparison method of triangular wave and sine signal is used to perform SPWM control on V1~V4 in the circuit. In this way, an SPWM wave uAB can be generated at the AC input terminal AB of the bridge. uAB contains the fundamental component with the same frequency and proportional amplitude as the sine signal wave, as well as high-frequency harmonics related to the triangular wave carrier, and does not contain low-order harmonics.
Due to the filtering effect of Ls , the harmonic voltage only causes a small pulsation in is. When the frequency of the sine signal wave is the same as the power supply frequency, is is also a sine wave with the same power supply frequency. When us is constant, the amplitude and phase of is are only determined by the amplitude of the fundamental wave uABf in uAB and its phase difference with us. By changing the amplitude and phase of uABf, is and us can be made in phase or out of phase, is can be ahead of us by 90°, or the phase difference between is and us can be made to be the required angle.
Working principle of PWM rectifier circuit
Figure 3 Further explanation of the working principle of the single-phase full-bridge PWM rectifier circuit
In rectification state:
When us > 0, (V2, VD4, VD1, Ls) and (V3, VD1, VD4, Ls) respectively form two boost chopper circuits, taking (V2, VD4, VD1, Ls) as an example.
When V2 is on, us stores energy to Ls through V2 and VD4.
When V2 is turned off, the energy stored in Ls charges C through VD1 and VD4.
When us < 0, (V1, VD3, VD2, Ls) and (V4, VD2, VD3, Ls) respectively form two boost chopper circuits.
This article explains the working principle of the single-phase half-bridge PWM rectifier circuit and determines multiple values under the rectifier state. I hope that after reading this article, power supply novices can fully understand the working principle of the single-phase half-bridge PWM rectifier circuit.
Previous article:What is the appropriate output ripple noise of a power supply?
Next article:Configuration and characteristics of half-bridge LLC resonant converter
Recommended ReadingLatest update time:2024-11-16 13:47
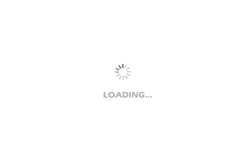
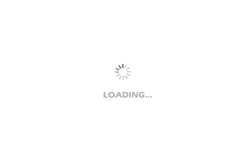
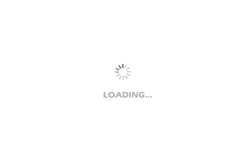
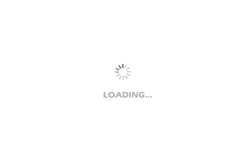
- Popular Resources
- Popular amplifiers
-
西门子S7-12001500 PLC SCL语言编程从入门到精通 (北岛李工)
-
Small AC Servo Motor Control Circuit Design (by Masaru Ishijima; translated by Xue Liang and Zhu Jianjun, by Masaru Ishijima, Xue Liang, and Zhu Jianjun)
-
Intelligent Control Technology of Permanent Magnet Synchronous Motor (Written by Wang Jun)
-
100 Examples of Microcontroller C Language Applications (with CD-ROM, 3rd Edition) (Wang Huiliang, Wang Dongfeng, Dong Guanqiang)
- MathWorks and NXP Collaborate to Launch Model-Based Design Toolbox for Battery Management Systems
- STMicroelectronics' advanced galvanically isolated gate driver STGAP3S provides flexible protection for IGBTs and SiC MOSFETs
- New diaphragm-free solid-state lithium battery technology is launched: the distance between the positive and negative electrodes is less than 0.000001 meters
- [“Source” Observe the Autumn Series] Application and testing of the next generation of semiconductor gallium oxide device photodetectors
- 采用自主设计封装,绝缘电阻显著提高!ROHM开发出更高电压xEV系统的SiC肖特基势垒二极管
- Will GaN replace SiC? PI's disruptive 1700V InnoMux2 is here to demonstrate
- From Isolation to the Third and a Half Generation: Understanding Naxinwei's Gate Driver IC in One Article
- The appeal of 48 V technology: importance, benefits and key factors in system-level applications
- Important breakthrough in recycling of used lithium-ion batteries
- Innolux's intelligent steer-by-wire solution makes cars smarter and safer
- 8051 MCU - Parity Check
- How to efficiently balance the sensitivity of tactile sensing interfaces
- What should I do if the servo motor shakes? What causes the servo motor to shake quickly?
- 【Brushless Motor】Analysis of three-phase BLDC motor and sharing of two popular development boards
- Midea Industrial Technology's subsidiaries Clou Electronics and Hekang New Energy jointly appeared at the Munich Battery Energy Storage Exhibition and Solar Energy Exhibition
- Guoxin Sichen | Application of ferroelectric memory PB85RS2MC in power battery management, with a capacity of 2M
- Analysis of common faults of frequency converter
- In a head-on competition with Qualcomm, what kind of cockpit products has Intel come up with?
- Dalian Rongke's all-vanadium liquid flow battery energy storage equipment industrialization project has entered the sprint stage before production
- Allegro MicroSystems Introduces Advanced Magnetic and Inductive Position Sensing Solutions at Electronica 2024
- Car key in the left hand, liveness detection radar in the right hand, UWB is imperative for cars!
- After a decade of rapid development, domestic CIS has entered the market
- Aegis Dagger Battery + Thor EM-i Super Hybrid, Geely New Energy has thrown out two "king bombs"
- A brief discussion on functional safety - fault, error, and failure
- In the smart car 2.0 cycle, these core industry chains are facing major opportunities!
- The United States and Japan are developing new batteries. CATL faces challenges? How should China's new energy battery industry respond?
- Murata launches high-precision 6-axis inertial sensor for automobiles
- Ford patents pre-charge alarm to help save costs and respond to emergencies
- New real-time microcontroller system from Texas Instruments enables smarter processing in automotive and industrial applications
- CY8CKIT-149 PSoC 4100S PLUS PROTOTYPING KIT Unboxing and Power-On Run Example
- B-U585I-IOT02A Bluetooth communication problem
- Super detailed teaching you how to use HFSS to design and simulate inverted F antenna 2
- How does an intelligent fully automatic multimeter measure capacitance?
- PCB current and signal integrity design
- micropython update: 2020.6
- 【DSP】TMS320F28035 SCI routine (self-transmission and self-reception + query)
- The reverse withstand voltage peak of the secondary winding rectifier tube D10 reaches -142V. How can I adjust the RCD parameter value to reduce it?
- C6678 multi-core application cache test
- Simulation AWR Learning Website