Main circuit analysis
This soft switching power supply adopts a full-bridge converter structure and uses MOSFET as a switch tube with a parameter of 1000V/24A. It adopts phase-shifted ZVZCS PWM control, that is, the leading arm switch tube realizes ZVS and the lagging arm switch tube realizes ZCS. The circuit structure diagram is shown in Figure 1. VT1~VT4 are four MOSFET switch tubes of the full-bridge converter. VD1 and VD2 are the reverse-parallel ultra-fast recovery diodes of the leading arm switch tubes VT1 and VT2 respectively. C1 and C2 are high-frequency capacitors set to achieve ZVS of VTl and VT2 respectively. VD3 and VD4 are reverse current blocking diodes used to achieve ZCS of the lagging arm VT3 and VT4. Llk is the transformer leakage inductance, Cb is the blocking capacitor, T is the main transformer, and the secondary side is composed of a high-frequency rectifier circuit composed of VD5~VD8 and filter components such as Lf, C3, and C4.
Figure 1 1.2kw soft-switching DC power supply circuit diagram
Its basic working principle is as follows:
When the switch tubes VT1, VT4 or VT2, VT3 are turned on at the same time, the circuit works in the same way as the hard switch working mode of the full-bridge converter, and the primary side of the main transformer provides energy to the load. Through phase shift control, when VT1 is turned off, VT4 is not turned off immediately, but the phase shift angle is determined according to the output feedback signal, and VT4 is turned off after a certain period of time. Before turning off VT1, since VT1 is turned on, the voltage on its parallel capacitor C1 is equal to the conduction voltage drop of VT1, and its value is zero under ideal conditions. When VT1 is turned off, C1 starts to charge. Since the capacitor voltage cannot change suddenly, VT1 is turned off with zero voltage.
Due to the transformer leakage inductance L1k and the secondary rectifier filter inductor, after VT1 is turned off, the primary current cannot change suddenly and continues to charge Cb. At the same time, C2 also discharges through the primary side. When the voltage of C2 drops to zero, VD2 is naturally turned on. At this time, VT2 is turned on with zero voltage.
When C1 is fully charged and C2 is discharged, since VD2 is turned on, the voltage applied to the primary winding and leakage inductance of the transformer is the voltage across the blocking capacitor Cb, and the primary current begins to decrease, but Cb continues to be charged until the primary current is zero. At this time, due to the blocking effect of VD4, capacitor Cb cannot be discharged through VT2, VT4, and VD4, and the voltage across Cb remains unchanged. At this time, the current flowing through VT4 is zero, and turning off VT4 is zero current shutdown.
After VT4 is turned off, VT3 is turned on after a preset dead time. Due to the existence of the transformer leakage inductance, the primary current cannot change suddenly, so VT3 is turned on with zero current.
After VT2 and VT3 are turned on at the same time, the primary side provides energy to the load, and VT2 is turned off after a certain period of time. Due to the existence of C2, VT2 is turned off at zero voltage. As analyzed above, the primary current cannot change suddenly at this time. After C1 is discharged through VD3, VT3.Cb, VD1 is turned on naturally. At this time, turning on VT1 is zero voltage turning on. Due to the blocking of VD3, the primary current drops to zero, and VT3 is turned off. Then VT3 is turned off at zero current. After the pre-selected dead time delay, VT4 is turned on. Due to the leakage inductance of the transformer and the secondary filter inductance, the primary current cannot change suddenly, and VT4 is turned on at zero current.
The ideal working waveform of the ZVZCS PWM full-bridge converter topology is shown in Figure 2, where Uab represents the voltage between points a and b in the main circuit diagram 3, ip is the primary current of the transformer T, Ucb is the voltage on the blocking capacitor Ub, and Urect is the voltage after secondary rectification.
Figure 2 Ideal working waveform
Design of the main control loop of UC3875
In order to realize the ZVZCS soft switching of the main circuit switch tube, a PWM phase shift control circuit is designed for it using UC3875 , as shown in Figure 3. Considering that the selected MOSFET has a relatively large power, the four output drive signals of the chip are power amplified, then isolated by high-frequency pulse transformers T1 and T2, and finally driven by the drive circuit to drive the MOSFET switch tube.
Figure 3 PWM phase shift control circuit
The entire control system uses the same 15V DC power supply for all power supplies. The switching frequency is set to 70kHz in the experiment, and the dead time is set to 1.5μs. A simple voltage control mode is used. The DC voltage output by the power supply forms a control signal after passing through the sampling circuit and the optoelectronic isolation circuit, and is input to the EA of the UC3875 error amplifier to control the output of the UC3875 error amplifier, thereby controlling the phase shift angle between the four outputs of the chip, so that the power supply can work stably. In the figure, R6 and C5 are connected between EA and E/AOUT to form PI control. In this design, the CS+ terminal is used as a fault protection circuit. When faults such as output overvoltage, output overcurrent, high-frequency transformer primary overcurrent, and switch tube overheating occur, the fault signal is converted into a voltage higher than 2.5V through a certain conversion circuit and connected to the CS+ terminal, so that the four output drive signals of UC3875 are all low level, and the circuit is protected.
Figure 4 is the driving circuit of the switch tube. The isolation transformer is designed using the AP method, with a three-winding transformer with a transformation ratio of 1:1.3. The unipolar pulse output by UC3875 passes through the amplifier circuit, isolation circuit and drive circuit to form a +12V/-5V bipolar drive pulse to ensure the stable opening and closing of the switch tube.
Figure 4 Switching tube drive circuit
Simulation and Experimental Results Analysis
PSpice is a powerful circuit analysis software. The simulation of ZVZCS soft switching power supply with switching frequency of 70kHz is carried out on PSpice9.1 platform.
The main circuit structure of the experimental prototype adopts the circuit topology shown in Figure 1. The blocking diode adopts the ultra-fast recovery high-power diode RHRG30120, whose reverse recovery time is within 100ns, meeting the requirement of 70kHz switching frequency. The switch MOSFET adopts the IXFK24N100 switch tube of IXYS Company. This type of MOS tube has an ultra-fast recovery diode in reverse connection, and its reverse recovery time is about 250ns.
Figure 5 is a waveform diagram of the driving voltage and tube voltage drop of the leading bridge arm switch tube. (a) is the simulation waveform and (b) is the experimental waveform. It can be seen that the leading arm switch tube fully realizes ZVS turn-on. When VT1 and VT2 are turned off, they rely on their own very small junction capacitance to achieve it. It can be seen from the figure that ZVS turn-off is basically achieved when they are turned off.
Figure 5 Leading bridge arm switch tube drive voltage and tube voltage drop waveform
Figure 6 Lag bridge arm switch driving voltage and current waveform
Figure 6 is a diagram of the driving voltage and current waveforms of the lagging bridge arm switch tube, (a) is a simulation waveform, (b) is an experimental waveform;
FIG7 is a diagram showing the voltage drop and current waveform of the lagging bridge arm switch tube, where (a) is the simulation waveform and (b) is the experimental waveform.
Figure 7 Lagging bridge arm switches VT3 and VT4 achieve ZCS shutdown
From Figures 6 and 7, it can be seen that the lagging arm switch tubes VT3 and VT4 have achieved ZCS shutdown very well, and the switch tube current is already zero when shutting down. Before the lagging arm switch tube is fully turned on, the switch tube current is also almost zero, basically achieving ZCS turn-on. Moreover, the lagging bridge arm switch tubes VT3 and VT4 can achieve ZCS switching in a wide load range.
FIG8 is a waveform diagram of the voltage Uab between the midpoints of the two bridge arms, where (a) is a simulation waveform and (b) is an experimental waveform.
Figure 8 Uab waveform
FIG. 9 is a waveform of the voltage U on the blocking capacitor Cb, where (a) is a simulation waveform and (b) is an experimental waveform.
Figure 9 Ucb waveform
As can be seen from the figure above, due to the existence of Ucb, Uab is not a square wave. When Uab=0, the voltage Ucb on the blocking capacitor Cb gradually reduces the primary current ip to zero. Due to the blocking effect of the blocking diode, ip cannot flow in the reverse direction, thus realizing the ZCS switch of the lagging bridge arm.
In summary, we can find that the advantage of using UC3875 as the core control device is that the structure is simple and the performance is reliable. In addition, all the switches in the main circuit realize soft switching, and some common errors in ZVS and ZCS modes are avoided. It can significantly reduce the loss of the switch tube during the switching process, thereby increasing the switching frequency, reducing the size of the power supply and reducing the weight.
Previous article:A simple method to increase the hold-up time of AC-DC power supply
Next article:[Ultimate Secret] Detailed explanation of the "three major components" of mobile power
Recommended ReadingLatest update time:2024-11-16 14:38
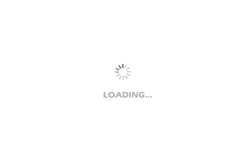
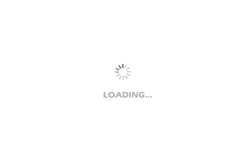
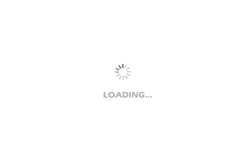
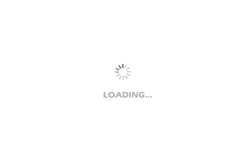
- Popular Resources
- Popular amplifiers
-
西门子S7-12001500 PLC SCL语言编程从入门到精通 (北岛李工)
-
Small AC Servo Motor Control Circuit Design (by Masaru Ishijima; translated by Xue Liang and Zhu Jianjun, by Masaru Ishijima, Xue Liang, and Zhu Jianjun)
-
Intelligent Control Technology of Permanent Magnet Synchronous Motor (Written by Wang Jun)
-
100 Examples of Microcontroller C Language Applications (with CD-ROM, 3rd Edition) (Wang Huiliang, Wang Dongfeng, Dong Guanqiang)
- MathWorks and NXP Collaborate to Launch Model-Based Design Toolbox for Battery Management Systems
- STMicroelectronics' advanced galvanically isolated gate driver STGAP3S provides flexible protection for IGBTs and SiC MOSFETs
- New diaphragm-free solid-state lithium battery technology is launched: the distance between the positive and negative electrodes is less than 0.000001 meters
- [“Source” Observe the Autumn Series] Application and testing of the next generation of semiconductor gallium oxide device photodetectors
- 采用自主设计封装,绝缘电阻显著提高!ROHM开发出更高电压xEV系统的SiC肖特基势垒二极管
- Will GaN replace SiC? PI's disruptive 1700V InnoMux2 is here to demonstrate
- From Isolation to the Third and a Half Generation: Understanding Naxinwei's Gate Driver IC in One Article
- The appeal of 48 V technology: importance, benefits and key factors in system-level applications
- Important breakthrough in recycling of used lithium-ion batteries
- Innolux's intelligent steer-by-wire solution makes cars smarter and safer
- 8051 MCU - Parity Check
- How to efficiently balance the sensitivity of tactile sensing interfaces
- What should I do if the servo motor shakes? What causes the servo motor to shake quickly?
- 【Brushless Motor】Analysis of three-phase BLDC motor and sharing of two popular development boards
- Midea Industrial Technology's subsidiaries Clou Electronics and Hekang New Energy jointly appeared at the Munich Battery Energy Storage Exhibition and Solar Energy Exhibition
- Guoxin Sichen | Application of ferroelectric memory PB85RS2MC in power battery management, with a capacity of 2M
- Analysis of common faults of frequency converter
- In a head-on competition with Qualcomm, what kind of cockpit products has Intel come up with?
- Dalian Rongke's all-vanadium liquid flow battery energy storage equipment industrialization project has entered the sprint stage before production
- Allegro MicroSystems Introduces Advanced Magnetic and Inductive Position Sensing Solutions at Electronica 2024
- Car key in the left hand, liveness detection radar in the right hand, UWB is imperative for cars!
- After a decade of rapid development, domestic CIS has entered the market
- Aegis Dagger Battery + Thor EM-i Super Hybrid, Geely New Energy has thrown out two "king bombs"
- A brief discussion on functional safety - fault, error, and failure
- In the smart car 2.0 cycle, these core industry chains are facing major opportunities!
- The United States and Japan are developing new batteries. CATL faces challenges? How should China's new energy battery industry respond?
- Murata launches high-precision 6-axis inertial sensor for automobiles
- Ford patents pre-charge alarm to help save costs and respond to emergencies
- New real-time microcontroller system from Texas Instruments enables smarter processing in automotive and industrial applications
- EEWORLD University Hall----TI Smart Speaker and Sound Bar- New Power Design Trend
- Share a STLINK V2_1 PCB project, which can be directly sampled and produced
- The input is 3.3V TTL high and low level. In theory, the output of Darlington should be the opposite level of TTL. I checked it...
- GPIO Programming and Example Code for MSP430 using C/C++
- Learning ARM-LINUX embedded system based on Beaglebone Black Part 2 - JTAG debugging
- EEWORLD University Hall ---- EDA Technology and Experiments Zhu Min from Harbin Institute of Technology
- Hot topic: The four most popular and profitable majors in the 5G era, which you definitely can’t miss in the 2019 college entrance examination!
- How to read constant array in flash using IAR FOR AVR?
- Technology Live: MEMS sensors usher in a new era of condition monitoring, ADI takes you into the kingdom of cold machines
- Analysis of the working principles of seven triode collector DC circuits 3