The main component of the communication switching power supply is the high-frequency switching rectifier, which has gradually developed and matured with the development of power electronics theory and technology and power electronic devices. The rectifier using soft switching technology has lower power consumption, lower temperature, and significantly reduced volume and weight, and the overall quality and reliability are constantly improving. However, every time the ambient temperature rises by 10°C, the life of the main power components is reduced by 50%. The reason for such a rapid decline in life is due to temperature changes. Fatigue failure caused by various microscopic and macroscopic mechanical stress concentrations, ferromagnetic materials and other components will develop various types of microscopic internal defects under the continuous action of alternating stress during operation. Therefore, ensuring effective heat dissipation of the equipment is a necessary condition to ensure the reliability and life of the equipment.
Relationship between operating temperature and reliability and life of power electronic components
A power supply is an electric energy conversion device. During the conversion process, it consumes some electric energy, which is converted into heat and released. The working stability and aging speed of electronic components are closely related to the ambient temperature. Power electronic components are composed of a variety of semiconductor materials. Since the loss of power components during operation is dissipated by their own heat, the thermal cycle of multiple materials with different expansion coefficients will cause very significant stress, and may even cause instantaneous fracture and component failure. If power components work under abnormal temperature conditions for a long time, fatigue that will lead to fracture will be induced. Since semiconductors have a thermal fatigue life, this requires that they should work in a relatively stable and low temperature range.
At the same time, rapid changes in temperature will temporarily produce semiconductor temperature differences, which will generate thermal stress and thermal shock. The components will be subjected to thermal-mechanical stress. When the temperature difference is too large, stress cracks will be generated in different material parts of the components, causing the components to fail prematurely. This also requires that power components should work within a relatively stable operating temperature range, reduce rapid temperature changes, eliminate the impact of thermal stress shock, and ensure long-term reliable operation of the components.
The influence of operating temperature on the insulation capacity of transformer
After the primary winding of the transformer is energized, the magnetic flux generated by the coil flows in the iron core. Since the iron core itself is a conductor, an induced potential will be generated on the plane perpendicular to the magnetic lines of force, forming a closed loop on the cross section of the iron core and generating current, which is called "eddy current". This "eddy current" increases the loss of the transformer and causes the iron core of the transformer to heat up, increasing the temperature rise of the transformer. The loss generated by the "eddy current" is called "iron loss". In addition, the copper wire used to wind the transformer has resistance. When current flows through, this resistance will consume a certain amount of power. This part of the loss is converted into heat and consumed, which is called "copper loss". Therefore, iron loss and copper loss are the main reasons for the temperature rise of the transformer during operation.
As the transformer's operating temperature rises, the coil will inevitably age. When its insulation performance decreases, its ability to resist the impact of the mains power will weaken. At this time, if there is a lightning strike or a mains power surge, the high reverse voltage at the primary of the transformer will break down the transformer, causing the power supply to fail. At the same time, there is also the risk of high voltage entering the main communication equipment, causing damage to the main equipment.
Effect of Cooling Method on Power Supply Operating Temperature
The heat dissipation of power supply generally adopts two methods: direct conduction and convection conduction. Direct heat conduction is the transfer of heat energy from the high temperature end to the low temperature end along the object, and its heat conduction capacity is stable. Convection conduction is the process of making the temperature of liquid or gas uniform through rotation. Since convection conduction involves the power process, the temperature drop is relatively smooth.
The heat transfer element is installed on the metal radiator, and the energy is transferred by high and low energy bodies by squeezing the heat surface. The energy that can be radiated by the large area of the heat sink is not much. This heat conduction method is called natural cooling, which has a long delay time for heat loss. The heat transfer amount Q=KA△t (K heat transfer coefficient, A heat transfer area, △t temperature difference). If the indoor ambient temperature is high, the absolute value of △t is small, and the heat dissipation performance of this heat transfer method will be greatly reduced.
Adding a fan to the power supply can quickly discharge the heat accumulated in the energy conversion out of the power supply. The continuous air supply from the fan to the heat sink can be regarded as the convection transfer of energy. It is called fan cooling. The delay time of this heat dissipation method is short and long. The heat dissipation Q = Km△t (K heat transfer coefficient, m heat transfer air mass, △t temperature difference). Once the fan speed decreases or stops, the m value will decrease rapidly, and the heat accumulated in the power supply will be difficult to dissipate, which will greatly increase the aging speed of the capacitors, transformers and other electronic components in the power supply and affect the stability of its output quality, eventually leading to the burning of components and equipment failure.
The main methods and advantages and disadvantages of communication power supply heat dissipation
The design of the cooling technology for communication switch power supply must first meet the various technical performance requirements of the industry. In order to better adapt to the special environment of the communication room, its cooling method is required to be highly adaptable to changes in ambient temperature. At present, the commonly used cooling methods for rectifiers are natural cooling, pure fan cooling, and a combination of natural cooling and fan cooling. Natural cooling has the characteristics of no mechanical failure, high reliability; no air flow, less dust, and conducive to heat dissipation; no noise. Pure fan cooling has the characteristics of light equipment weight and low cost. The technology combining fans and natural cooling has the characteristics of effectively reducing the size and weight of the equipment, long fan service life, and strong fan fault adaptive ability.
Natural cooling
Natural cooling is the traditional cooling method of the early switching power supply. This method mainly relies on a large metal heat sink for direct heat conduction heat dissipation. Heat transfer Q = KA△t (K heat transfer coefficient, A heat transfer area, △t temperature difference). When the output power of the rectifier increases, the temperature of its power components will rise, and the △t temperature difference will also increase. Therefore, when the heat transfer area of the rectifier A is sufficient, its heat dissipation has no time lag, the temperature difference of the power components is small, and its thermal stress and thermal shock are small. However, the main disadvantage of this method is that the heat sink is large in size and weight. The winding of the transformer is to reduce the temperature rise as much as possible to prevent the temperature rise from affecting its working performance, so the margin of its material selection is large, and the volume and weight of the transformer are also large. The material cost of the rectifier is high, and maintenance and replacement are inconvenient. Because it does not require high environmental cleanliness, it is currently used in some small professional communication networks for small-capacity communication power supplies, such as electricity, petroleum, radio and television, military, water conservancy, national security, public security, etc.
Fan Cooling
With the development of fan manufacturing technology, the working stability and service life of fans have been greatly improved, and the average trouble-free time is 50,000 hours. The use of fans for heat dissipation can eliminate the bulky radiator, greatly improving the size and weight of the rectifier and greatly reducing the cost of raw materials. With the intensification of market competition and the decline in market prices, this technology has become the main trend at present.
The main disadvantage of this method is that the fan's MTBF is shorter than the rectifier's 100,000 hours. If the fan fails, the failure rate of the power supply will be greatly affected. Therefore, in order to ensure the service life of the fan, the fan speed changes with the temperature change in the equipment. Its heat dissipation Q = Km△t (K heat transfer coefficient, m heat exchange air quality, △t temperature difference). m heat exchange air quality is related to the fan speed. When the rectifier output power increases, the temperature of its power components will rise. There is a large time lag from the change in the temperature of the power components to the rectifier being able to detect this change, and then to increasing the fan speed to enhance heat dissipation. If the load often changes suddenly, or the mains input fluctuates greatly, it will cause the power components to change rapidly from hot to cold. The thermal stress and thermal shock generated by this sudden semiconductor temperature difference will cause stress cracks in different material parts of the components. Make it fail prematurely.
Combination of fans and natural cooling
Due to changes in ambient temperature and load, the power supply consumes heat when it is working. The combination of fan and natural cooling can dissipate the heat faster. This method can reduce the radiator area while increasing the fan heat dissipation, so that the power components work under relatively stable temperature field conditions, and the service life will not be affected by changes in external conditions. This not only overcomes the shortcomings of pure fan cooling for the lagging heat dissipation regulation of power components, but also avoids the impact of low fan service life on the overall reliability of the rectifier. Especially when the ambient temperature of the computer room is very unstable, the cooling technology that combines air cooling and self-cooling has better cooling performance. The material cost of the rectifier in this way is between pure fan cooling and natural cooling, with low weight and easy maintenance.
Especially when using intelligent air cooling and self-cooling technology, the rectifier can keep the module temperature rise small under low load working conditions, and the module fan is in a low-speed operation state. Under high load working conditions, the module heats up. The module temperature rises by more than 55°C. The fan speed increases linearly with the temperature change. Fan fault detection is in place. After the fan fails, the fan fault current limiting output is output, and the fault alarm is also issued. Since the number of fan operation is related to the load size, the service life of the fan is longer than that of pure air cooling, and its reliability is greatly improved.
The communication switching power supply adopts a cooling method that combines fans and natural cooling. It can effectively reduce the internal working temperature of the rectifier and extend the service life of the device when the ambient temperature is high. It can also reduce the speed of the rectifier fan when the ambient temperature is low and the load is low, thereby extending the service life of the fan. The heat sink is used for heat dissipation, and the device spacing and creepage distance can be relatively far. In the case of high humidity, the safety performance is high. The rectifier is small in size and light in weight, making maintenance work easy.
To ensure the reliable and stable operation of the rectifier of the communication switching power supply , reducing its operating temperature rise is a key technology. It adopts a combination of intelligent air cooling and self-cooling technology. It has technical advantages such as stronger environmental adaptability, long service life, reliability and stability.
Previous article:Research on SVPWM Active Power Filter Based on Current Loop Compound Control
Next article:LDO linear regulator topology and classification
Recommended ReadingLatest update time:2024-11-16 14:49
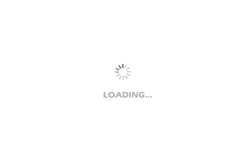
- Popular Resources
- Popular amplifiers
-
Mission-oriented wireless communications for cooperative sensing in intelligent unmanned systems
-
Follow me Season 2 Episode 1 All Codes
-
CVPR 2023 Paper Summary: Embodied Vision: Active Agents, Simulation
-
ICCV2023 Paper Summary: Fairness, Privacy, Ethics, Social-good, Transparency, Accountability in Vision
- MathWorks and NXP Collaborate to Launch Model-Based Design Toolbox for Battery Management Systems
- STMicroelectronics' advanced galvanically isolated gate driver STGAP3S provides flexible protection for IGBTs and SiC MOSFETs
- New diaphragm-free solid-state lithium battery technology is launched: the distance between the positive and negative electrodes is less than 0.000001 meters
- [“Source” Observe the Autumn Series] Application and testing of the next generation of semiconductor gallium oxide device photodetectors
- 采用自主设计封装,绝缘电阻显著提高!ROHM开发出更高电压xEV系统的SiC肖特基势垒二极管
- Will GaN replace SiC? PI's disruptive 1700V InnoMux2 is here to demonstrate
- From Isolation to the Third and a Half Generation: Understanding Naxinwei's Gate Driver IC in One Article
- The appeal of 48 V technology: importance, benefits and key factors in system-level applications
- Important breakthrough in recycling of used lithium-ion batteries
- Innolux's intelligent steer-by-wire solution makes cars smarter and safer
- 8051 MCU - Parity Check
- How to efficiently balance the sensitivity of tactile sensing interfaces
- What should I do if the servo motor shakes? What causes the servo motor to shake quickly?
- 【Brushless Motor】Analysis of three-phase BLDC motor and sharing of two popular development boards
- Midea Industrial Technology's subsidiaries Clou Electronics and Hekang New Energy jointly appeared at the Munich Battery Energy Storage Exhibition and Solar Energy Exhibition
- Guoxin Sichen | Application of ferroelectric memory PB85RS2MC in power battery management, with a capacity of 2M
- Analysis of common faults of frequency converter
- In a head-on competition with Qualcomm, what kind of cockpit products has Intel come up with?
- Dalian Rongke's all-vanadium liquid flow battery energy storage equipment industrialization project has entered the sprint stage before production
- Allegro MicroSystems Introduces Advanced Magnetic and Inductive Position Sensing Solutions at Electronica 2024
- Car key in the left hand, liveness detection radar in the right hand, UWB is imperative for cars!
- After a decade of rapid development, domestic CIS has entered the market
- Aegis Dagger Battery + Thor EM-i Super Hybrid, Geely New Energy has thrown out two "king bombs"
- A brief discussion on functional safety - fault, error, and failure
- In the smart car 2.0 cycle, these core industry chains are facing major opportunities!
- The United States and Japan are developing new batteries. CATL faces challenges? How should China's new energy battery industry respond?
- Murata launches high-precision 6-axis inertial sensor for automobiles
- Ford patents pre-charge alarm to help save costs and respond to emergencies
- New real-time microcontroller system from Texas Instruments enables smarter processing in automotive and industrial applications
- 【LoRa】LoRa development common problems 2
- EEWORLD University Hall----Teacher Tang talks about operational amplifiers
- Why do positrons and electrons "annihilate"?
- CCS tools and the functions of different files
- One of the 17 most used software by electronic engineers
- How to draw a circular PCB lamp bead board and arrange the lamp beads equidistantly
- Could you please tell me the bootstrap principle of IR2104 in the following circuit diagram (please write in detail, thank you)
- Today at 14:00, live broadcast with prizes: [In-depth and easy-to-understand wearable health monitoring]
- MSP430 capture device is simple and practical
- I want to learn stm32, please recommend a tutorial