Taking the single-chip microcomputer AT89C51 as the control core, the semiconductor refrigeration technology is introduced into the LED heat dissipation research. The PID algorithm and PWM modulation technology are used to control the input voltage of the semiconductor refrigeration chip, and then the semiconductor refrigeration power is controlled. The feasibility of this method is verified through experiments.
With the rapid development of LED technology, LED has entered the general lighting market. However, the development of LED lighting systems is greatly affected by the heat dissipation problem. For high-power LEDs, the heat dissipation problem has become a bottleneck problem restricting its development. Semiconductor refrigeration technology has the advantages of small size, no need to add refrigerant, simple structure, no noise, stable and reliable. With the advancement of semiconductor material technology and the discovery of high thermoelectric conversion materials, using semiconductor refrigeration technology to solve the heat dissipation problem of LED lighting systems will have very practical significance.
1 Causes of LED heat generation and its impact on LED performance
When LED is under forward voltage, electrons obtain energy from the power supply. Driven by the electric field, they overcome the electric field of the PN junction and jump from the N region to the P region. These electrons recombine with the holes in the P region. Since the free electrons drifting to the P region have higher energy than the valence electrons in the P region, the electrons return to a low energy state during recombination, and the excess energy is released in the form of photons. However, only 30% to 40% of the released photons are converted into light energy, and the remaining 60% to 70% are converted into heat energy in the form of point vibration.
Since LED is a semiconductor light-emitting device, and semiconductor devices change with temperature, their inherent characteristics will change significantly. The increase in LED junction temperature will cause changes and attenuation in device performance. This change is mainly reflected in the following three aspects: ⑴ Reducing the external quantum efficiency of the LED; ⑵ Shortening the life of the LED; ⑶ Causing the main wavelength of the light emitted by the LED to shift, thereby causing the color of the light source to shift. High-power LEDs generally use more than 1W of electrical power input, and the heat they generate is very large. Solving their heat dissipation problem is a top priority.
2 Principle of semiconductor refrigeration
Semiconductor refrigeration, also known as electronic refrigeration or thermoelectric refrigeration, is a discipline developed in the 1950s that is at the edge of refrigeration technology and semiconductor technology. It is known as the world's three major refrigeration methods along with compression refrigeration and absorption refrigeration. The basic device of a semiconductor refrigerator is a thermocouple pair, that is, an N-type semiconductor and a P-type semiconductor are connected into a thermocouple (as shown in Figure 1). After direct current is applied, a temperature difference and heat transfer will occur at the interface. Several pairs of semiconductor thermocouples are connected in series in the circuit, while the heat transfer is in parallel, thus forming a common refrigeration thermopile. With the help of various heat transfer methods such as heat exchangers, the hot end of the thermopile continuously dissipates heat and maintains a certain temperature, while the cold end of the thermopile is placed in the working environment to absorb heat and cool down. This is the principle of semiconductor refrigeration.
This article uses semiconductor refrigeration because compared with other refrigeration systems, it has no mechanical rotating parts, no need for refrigerants, no pollution, high reliability, long life and easy control. The size and power can be made very small, which is very suitable for application in the limited working space of LED. 3 System overall design plan
The LED heat dissipation control system consists of a temperature setting module, a reset module, a display module, a temperature acquisition module, a control circuit module [2] and a cooling module. The overall block diagram of the system is shown in Figure 1. The system uses a microprocessor as the control core, communicates with the temperature acquisition module to acquire the real-time temperature of the controlled object, and communicates with the temperature setting module to set the cooling start temperature and the forced cooling temperature. The unprocessed programming can be realized using C language. When the acquired real-time temperature is lower than the cooling start temperature, no PWM modulation wave [1, 6] is output, and the cooling module is in an idle state; when the acquired real-time temperature is higher than the cooling start temperature but lower than the forced cooling temperature, a PWM modulation wave with a certain duty cycle is output, and the cooling module starts a low-power cooling mode; when the acquired real-time temperature is higher than the forced cooling temperature, a PWM modulation wave with a certain duty cycle is output, and the cooling module starts a high-power cooling mode.
4 Hardware circuit design and component selection
The system is mainly composed of temperature setting, temperature acquisition, PWM control circuit and auxiliary circuit (reset circuit and display circuit). This scheme adopts low-cost, high-performance AT89C51 as the main control chip to realize the logic control function of the whole system; adopts high-precision temperature sensor DS18B20 with single-line communication to realize the real-time temperature acquisition of the controlled object LED chip; at the same time, a 4×3 input keyboard is designed, and the refrigeration start temperature and forced cooling temperature are input by the keyboard; a PWM control circuit is designed to realize the control of the working voltage of the semiconductor refrigeration piece TEC[5], and then realize the control of the refrigeration power of the semiconductor refrigeration piece TEC, so as to achieve the effect of timely heat dissipation of the LED chip.
4.1 Main control chip AT89C51
The main control chip of the system is the single-chip microcomputer AT89C51. The single-chip microcomputer AT89C51 is a low-voltage, high-performance processor produced by ATMEL in the United States. It provides a flexible and low-cost solution for embedded control systems. The single-chip microcomputer AT89C51 contains 4KB Flash storage, which can be repeatedly erased and written 1000 times, 128 bytes of RAM, four parallel 8-bit bidirectional I/Os and two 16-bit programmable timers. In addition, the main control chip AT89C51 uses a crystal oscillator with a frequency of 12MHz, so that the system runs a machine cycle, which is conducive to program writing. The main functions of the single-chip microcomputer AT89C51 are: read the set refrigeration start power and forced power from the keyboard circuit, read the real-time collected LED chip working temperature from the temperature sensor DS18B20, compare the two through C language programming, output PWM modulation wave to the photoelectric coupler, and output the real-time collected temperature of DS18B20 to LCD display.
4.2 Keyboard Circuit
The system uses a 4×3 keyboard [4], which includes 10 numeric keys from 0 to 9, an "OK" key, and a "Clear" key. The operation process is as follows: enter the 2-digit set temperature, press "OK", and enter the set temperature into a storage unit in the user-defined area of AT89C51 as the start-up temperature of the semiconductor refrigerator. Then, enter the 2-digit temperature again in the same way as the forced cooling temperature of the semiconductor refrigerator. Keyboard working principle: I/O ports P1.0~P1.3 act as row select lines, and P1.5~P1.7 (externally connected to a pull-up resistor to a +5V power supply ) act as column select lines. During initialization, P1.0~P1.3 are set to a low potential, and P1.5~P1.7 are set to a high potential and wait for a key to be pressed. When a key is pressed, the corresponding column select line level is forced to be pulled low, and the corresponding row code and column code are read, and the key number can be determined.
4.3 Temperature acquisition circuit
The system uses the digital temperature sensor DS18B20 produced by DALLAS, USA. DS18B20 is a temperature measurement chip that uses only one signal line (1-Wire) to communicate with the microcontroller. It can measure the temperature between (meeting the temperature measurement requirements of the system). The program can be used to achieve 9-bit digital temperature output with a measurement accuracy of . Because the leakage current of DS18B20 is relatively large when the temperature is higher than , the communication with the microcontroller AT89C51 may collapse, so the external power supply mode is used for power supply. The biggest feature of DS18B20 is the single bus transmission mode, so it has strict timing requirements for reading and writing data bits. The timing includes: initialization timing, read timing, and write timing. Each transmission of commands and data starts from the start write timing of the microcontroller. If DS18B20 is required to send back data, after the write timing, the microcontroller needs to start the read timing to complete the data reception. The transmission of data and commands is the first priority.
4.4PWM Control Circuit
The PWM control circuit consists of a photocoupler and a Cuk circuit [3]. In this control circuit, the photocoupler can effectively suppress the noise of the ground loop, eliminate ground interference, and improve the anti-interference ability of the entire system; the photocoupler electrically isolates the input end (microcontroller AT89C51) and the output end (semiconductor cooling element TEC), avoiding accidental damage to the main control chip AT89C51 and effectively protecting the microcontroller AT89C51. In addition, this control circuit also uses a photocoupler to form a switching circuit, saving the use of switching devices. The function of the Cuk DC chopper circuit is to convert the +15V external power supply into a DC power with an adjustable voltage, that is, the voltage at the output end of the Cuk circuit (the working voltage of the semiconductor cooling element TEC) is adjustable. The adjustable voltage between the output ends OUT+ and OUT- is controlled by the turn-off frequency between the Q1 end and the Q2 end. The Cuk circuit is selected in this control circuit because the Cuk chopper circuit has an obvious advantage, that is, its input power supply current and output load current are continuous and have very small pulsation, which is conducive to ensuring that the semiconductor cooling element TEC is in a good working state.
Due to limited space, the following is only a brief introduction to this PWM control circuit: when the PWM control signal is low, the transistor T1 is in the cut-off state, the current of the light-emitting diode in the photocoupler is approximately zero, and the resistance between the output terminals Q1 and Q2 is large, which is equivalent to the switch "off"; when the PWM wave control signal is high, the transistor T1 is in the on state, the light-emitting diode in the photocoupler emits light, and the resistance between the output terminals Q1 and Q2 is very small, which is equivalent to the switch "on". From the above introduction, it can be seen that when the real-time temperature collected by DS18B20 is lower than the refrigeration start temperature, when there is no signal input to the PWM input terminal of the photocoupler, the photocoupler is in a non-working state, and there is no output voltage at the OUT+ and OUT- terminals in Figure 5, that is, the semiconductor refrigeration plate is in an idle state; when the real-time temperature collected by DS18B20 is higher than the refrigeration start temperature, there is a signal input to the PWM input terminal of the photocoupler, and there is an output voltage at the OUT+ and OUT- terminals in Figure 5. By controlling the on and off of Q1 and Q2 through PWM modulation wave, the working voltage of semiconductor refrigeration piece TEC can be controlled, and then the heat dissipation power of semiconductor refrigeration piece TEC can be controlled. The OUT+ and OUT- terminals in Figure 5 are respectively connected to the input terminal line of semiconductor refrigeration piece TEC. According to the relationship between the output voltage of CUK circuit and the power supply voltage, the relationship between PWM wave duty cycle and semiconductor refrigeration piece TEC input voltage can be obtained:
Where D is the duty cycle of the PWM wave, is the operating voltage of the semiconductor refrigeration piece TEC, and E is the voltage of the power supply (in this circuit, E=15V). From the above formula, we can know that controlling the duty cycle of the PWM wave can control the operating voltage of the semiconductor refrigeration piece TEC.
5 Conclusion
This article selects some low-cost and relatively high-performance components to perform different power cooling for different working temperatures of LED chips, saving power resources to a certain extent. Compared with traditional cooling solutions, this solution has the advantages of good controllability and good cooling effect, and has very practical significance for solving the heat dissipation problem of high-power LED lighting systems.
Previous article:Systematization and integration will become the development trend of LED power supply industry
Next article:Tips for selecting chips for LED driver power design
Recommended ReadingLatest update time:2024-11-17 01:35
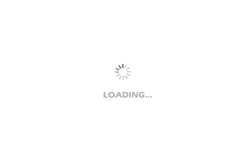
- MathWorks and NXP Collaborate to Launch Model-Based Design Toolbox for Battery Management Systems
- STMicroelectronics' advanced galvanically isolated gate driver STGAP3S provides flexible protection for IGBTs and SiC MOSFETs
- New diaphragm-free solid-state lithium battery technology is launched: the distance between the positive and negative electrodes is less than 0.000001 meters
- [“Source” Observe the Autumn Series] Application and testing of the next generation of semiconductor gallium oxide device photodetectors
- 采用自主设计封装,绝缘电阻显著提高!ROHM开发出更高电压xEV系统的SiC肖特基势垒二极管
- Will GaN replace SiC? PI's disruptive 1700V InnoMux2 is here to demonstrate
- From Isolation to the Third and a Half Generation: Understanding Naxinwei's Gate Driver IC in One Article
- The appeal of 48 V technology: importance, benefits and key factors in system-level applications
- Important breakthrough in recycling of used lithium-ion batteries
- Innolux's intelligent steer-by-wire solution makes cars smarter and safer
- 8051 MCU - Parity Check
- How to efficiently balance the sensitivity of tactile sensing interfaces
- What should I do if the servo motor shakes? What causes the servo motor to shake quickly?
- 【Brushless Motor】Analysis of three-phase BLDC motor and sharing of two popular development boards
- Midea Industrial Technology's subsidiaries Clou Electronics and Hekang New Energy jointly appeared at the Munich Battery Energy Storage Exhibition and Solar Energy Exhibition
- Guoxin Sichen | Application of ferroelectric memory PB85RS2MC in power battery management, with a capacity of 2M
- Analysis of common faults of frequency converter
- In a head-on competition with Qualcomm, what kind of cockpit products has Intel come up with?
- Dalian Rongke's all-vanadium liquid flow battery energy storage equipment industrialization project has entered the sprint stage before production
- Allegro MicroSystems Introduces Advanced Magnetic and Inductive Position Sensing Solutions at Electronica 2024
- Car key in the left hand, liveness detection radar in the right hand, UWB is imperative for cars!
- After a decade of rapid development, domestic CIS has entered the market
- Aegis Dagger Battery + Thor EM-i Super Hybrid, Geely New Energy has thrown out two "king bombs"
- A brief discussion on functional safety - fault, error, and failure
- In the smart car 2.0 cycle, these core industry chains are facing major opportunities!
- Rambus Launches Industry's First HBM 4 Controller IP: What Are the Technical Details Behind It?
- The United States and Japan are developing new batteries. CATL faces challenges? How should China's new energy battery industry respond?
- Murata launches high-precision 6-axis inertial sensor for automobiles
- Ford patents pre-charge alarm to help save costs and respond to emergencies
- About atmel studio 7 to generate .lib library files
- Basic knowledge of power supply that you must know
- AD PCB cannot be saved, showing file save failed
- In the EMC-related experiments of circuits, there are some voltage pulse experiments. How should the withstand voltage value of the capacitor be considered?
- Start with LoRa and learn more about the Internet of Things
- Bored at home? Learn about oscilloscopes. 200M Tektronix LCD oscilloscope for 1580 yuan including express delivery
- Ask about the udealy function of Liunx
- How to modify the AT32F4xx SRAM space size
- About software testing of commercial appliances
- EEWORLD University ---- Operating System Harbin Institute of Technology