Many friends who are new to LED display are curious about why they are required to wear shoe covers, anti-static rings, anti-static clothing and other protective equipment when visiting many LED display workshops. To understand this issue, we need to talk about the knowledge related to anti-static protection in the production and transportation of LED display; many LED display screens have dead lights or are not lit, mostly due to static electricity.
The source of static electricity during the production of LED displays
1. Objects and materials
2. Floor, work desk and chair
3. Work clothes and packaging containers;
4. Painted or waxed surfaces, organic and fiberglass materials.
5. Cement floors, painted or waxed floors, plastic tiles or floor coverings.
6. Chemical fiber work clothes, non-conductive work shoes, and clean cotton work clothes.
7. Plastics, packaging boxes, boxes, bags, trays, foam plastic pads.
The harm of static electricity in the production process of LED display screens If anti-static is ignored in any link of production, it will cause electronic equipment to malfunction or even damage it. When semiconductor devices are placed alone or loaded into a circuit, even if there is no power, static electricity may cause permanent damage to these devices. As we all know, LEDs are semiconductor products. If the voltage between two or more pins of an LED exceeds the breakdown strength of the component medium, it will damage the component. The thinner the oxide layer, the more sensitive the LED and driver IC are to static electricity. For example, if the solder is not full, the quality of the solder itself is problematic, etc., serious leakage paths will be generated, causing devastating damage.
Another type of failure is caused when the temperature of the node exceeds the melting point of semiconductor silicon (1415°C). The pulse energy of static electricity can generate local heating, thus directly breaking down the lamp and IC. This failure can occur even if the voltage is lower than the breakdown voltage of the medium. A typical example is that LED is a diode composed of PN junctions, and the breakdown between the emitter and the base will cause a sharp decrease in current gain. After the LED itself or the various ICs in the drive circuit are affected by static electricity, functional damage may not occur immediately. These potentially damaged components usually only show up during use, so they are fatal to the life of LED products.
The production process of LED display is a very rigorous and meticulous process, and every link cannot be overlooked. The electrostatic protection of the display is also an important part of the production of LED display. At present, the industry's understanding of electrostatic protection is not deep enough, and it cannot meet the needs of professional LED display production. More professionals are needed to continue research and discuss together.
How to prevent static electricity in LED display production:
1) Provide electrostatic knowledge and related technology training to personnel using electrostatic sensitive circuits.
2) Establish an anti-static work area, use anti-static floors, anti-static workbenches, anti-static grounding leads and anti-static equipment in the area, and control the relative humidity above 40.
3) The harm caused by static electricity to electronic equipment may occur anywhere from the manufacturer to the field equipment. The harm is caused by insufficient and effective training and equipment operation failure. LED is a device sensitive to static electricity. INGAN chips are usually considered to be "first" susceptible to interference. And ALINGAPLEDSSHI "second" or better.
4) ESD damaged devices can show dim, fuzzy, off, short or low VF or VR. ESD damaged devices should not be confused with electronic overstress, such as: due to incorrect current design or drive, chip hanging, wire shield grounding or packaging, or general environmental induced stress.
5) ESD safety and control procedures: Most electronic and electro-optical companies have very similar ESD and have successfully implemented ESD control, manipulation and master procedures for all equipment. These procedures have been used to detect quality effects of ESD instruments since ancient times. ISO-9000 certification also includes it in normal control procedures.
Previous article:Combination of linear and switching LED power supply design
Next article:[Questions and Answers] Five major technical issues in the use of LED chips
Recommended ReadingLatest update time:2024-11-16 23:46
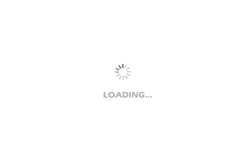
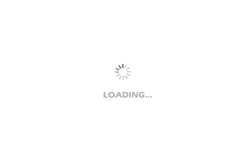
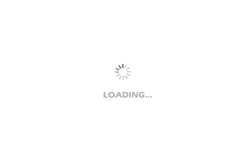
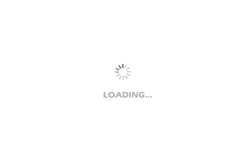
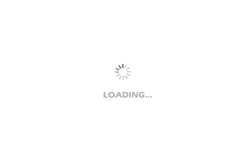
- Popular Resources
- Popular amplifiers
- MathWorks and NXP Collaborate to Launch Model-Based Design Toolbox for Battery Management Systems
- STMicroelectronics' advanced galvanically isolated gate driver STGAP3S provides flexible protection for IGBTs and SiC MOSFETs
- New diaphragm-free solid-state lithium battery technology is launched: the distance between the positive and negative electrodes is less than 0.000001 meters
- [“Source” Observe the Autumn Series] Application and testing of the next generation of semiconductor gallium oxide device photodetectors
- 采用自主设计封装,绝缘电阻显著提高!ROHM开发出更高电压xEV系统的SiC肖特基势垒二极管
- Will GaN replace SiC? PI's disruptive 1700V InnoMux2 is here to demonstrate
- From Isolation to the Third and a Half Generation: Understanding Naxinwei's Gate Driver IC in One Article
- The appeal of 48 V technology: importance, benefits and key factors in system-level applications
- Important breakthrough in recycling of used lithium-ion batteries
- Innolux's intelligent steer-by-wire solution makes cars smarter and safer
- 8051 MCU - Parity Check
- How to efficiently balance the sensitivity of tactile sensing interfaces
- What should I do if the servo motor shakes? What causes the servo motor to shake quickly?
- 【Brushless Motor】Analysis of three-phase BLDC motor and sharing of two popular development boards
- Midea Industrial Technology's subsidiaries Clou Electronics and Hekang New Energy jointly appeared at the Munich Battery Energy Storage Exhibition and Solar Energy Exhibition
- Guoxin Sichen | Application of ferroelectric memory PB85RS2MC in power battery management, with a capacity of 2M
- Analysis of common faults of frequency converter
- In a head-on competition with Qualcomm, what kind of cockpit products has Intel come up with?
- Dalian Rongke's all-vanadium liquid flow battery energy storage equipment industrialization project has entered the sprint stage before production
- Allegro MicroSystems Introduces Advanced Magnetic and Inductive Position Sensing Solutions at Electronica 2024
- Car key in the left hand, liveness detection radar in the right hand, UWB is imperative for cars!
- After a decade of rapid development, domestic CIS has entered the market
- Aegis Dagger Battery + Thor EM-i Super Hybrid, Geely New Energy has thrown out two "king bombs"
- A brief discussion on functional safety - fault, error, and failure
- In the smart car 2.0 cycle, these core industry chains are facing major opportunities!
- The United States and Japan are developing new batteries. CATL faces challenges? How should China's new energy battery industry respond?
- Murata launches high-precision 6-axis inertial sensor for automobiles
- Ford patents pre-charge alarm to help save costs and respond to emergencies
- New real-time microcontroller system from Texas Instruments enables smarter processing in automotive and industrial applications
- (Bonus 14) GD32L233 Review - Driving Segment Code LCD
- China's chip self-sufficiency rate was 30% last year, and the goal is to reach 70% by 2025 (attached with representative companies in 70 sub-sectors of domestic chips)
- 【New Year's Taste Competition】New Year's Eve Reunion Dinner and My Wedding
- Getting Started with the TI AWR1642BOOST-ODS EVM Development Board
- [STM32WB55 Review] A brief analysis of the execution process of the BLE demo program
- Positioning, positioning, positioning: the road to ultra-wideband
- 35-year-old programmer trades Luna and loses tens of millions of assets in three days
- Design of Pulse Oximeter Based on TI MSP430
- BMS solutions for electric bicycles and electric motorcycles under the new national standard for electric vehicles
- Bluetooth spoofing vulnerability affects billions of IoT devices