LED lighting will replace mainstream incandescent lighting and other lighting technologies and occupy a dominant position in the market. However, the transition from old technology to new technology will take many years. During this period, the challenge facing LED lamp designers is how to ensure that the new design is compatible and reliable with the existing controller and wiring architecture originally developed for incandescent lighting. This article introduces a solution that can be applied to both low-power and high-power LED lighting systems. It is a proven and mature solution.
The structure of LED bulb
An LED lamp contains from one to a dozen or more LED chips, which are usually connected in series. The brightness of each chip is determined by the amount of current passing through it. Because of the series connection, each LED chip in the bulb automatically passes the same current, but the voltage on each chip is different. The forward voltage drop of an LED is usually 3.4V, but it can vary from 2.8V to 4.2V. LEDs can be sorted to limit the voltage variation, but this increases cost, and the forward voltage drop will still change with temperature and time of use. To provide consistent light output, LED lamps must be driven by a strictly regulated, efficient, constant-current power supply. As an alternative to incandescent lamps, LED lamps must be integrated into the lamp housing.
A typical integrated LED lamp includes a driver circuit, an LED cluster, and a housing that provides mechanical protection and heat dissipation for the driver and LED chips.
The requirements for LED drivers are very stringent. They must be energy efficient, meet strict EMI and power factor specifications, and safely withstand a wide range of fault conditions. One of the most difficult requirements is dimming. Poor performance can easily occur due to the mismatch between the characteristics of LED lamps and dimming controllers designed for incandescent lamps. Problems can manifest as slow startup, flickering, uneven lighting, or flickering when adjusting the light intensity. There are also problems such as inconsistent performance from unit to unit and audible noise from the LED lamp. These negative conditions are usually caused by a combination of factors such as false triggering or premature shutdown of the controller and improper LED current control.
Dimming controller
Lighting controllers work with either line dimming or PWM dimming. The simplest form of line dimming is a leading edge thyristor controller. This is the most common lighting control method, but unfortunately, there are a lot of problems when using thyristor controllers to dim LED lights. More advanced line dimmers are electronic leading or trailing edge dimmers. PWM dimmers are used in professional lighting systems.
When using a leading-edge thyristor dimmer, dimming control is achieved by changing the phase angle of each half-cycle of the thyristor conduction. The input power to the bulb is a function of the phase angle of the dimming signal, which can range from nearly 0° to 180°.
One of the important parameters of a thyristor is the holding current (IH). This is the minimum load that the thyristor must maintain to remain on without gate drive. To maintain stable operation of the thyristor, this current cannot be zero, and typical values of IH are between 8mA and 40mA. Therefore, phase angle dimmers for incandescent lamps usually have a specified minimum load, usually 40W at a rated 230V AC voltage. This is to ensure that the current flowing through the internal thyristor is always above the specified holding current threshold. Since the power consumption of LED lighting is very low, the holding current will become a problem.
Another potential problem is inrush current. When the thyristor turns on, a high inrush current will flow into the LED lamp. The worst case is when the phase angle reaches 90°, when the AC input voltage reaches its peak. For incandescent lamps, inrush current is not a problem. But in LED lamps , the input stage impedance of the driver and the line capacitance will cause ringing. When ringing occurs, the thyristor current will immediately drop below the holding current, causing the thyristor to stop conducting.
To solve these problems, the specifications and design of the LED driver must be modified .
Non-isolated dimmable LED driver
The basic application circuit diagram of a non-isolated, dimmable LED driver for an LED lamp that can be used to replace an incandescent lamp is shown in Figure 1. The driver functionality is described below to illustrate the issues that arise when the driver becomes the load for a thyristor dimmer.
The controller is a Link Switch-PL device from Power Integrations (PI). It integrates a high-voltage power MOSFET switch and a power controller on a monolithic IC. The device provides single-stage power factor correction (PFC) and LED current control. The circuit can be used as a discontinuous mode, variable frequency, variable on-time flyback converter. The rectified AC power input is switched by an integrated 725V power MOSFET through a high-frequency transformer. The voltage generated on the secondary winding is rectified and smoothed before it becomes the LED load. The LED load current also flows through the sense resistor RSENSE. The voltage generated on RSENSE (typically 290mV) appears at the feedback (FB) pin through RF, providing precise constant current feedback control. DES and RES power the Link Switch-PL, and DZOV and ROV provide overvoltage protection when the LED is open.
The output current in this design is independent of the characteristics of the power transformer. Inductance changes have no effect on the constant current characteristic. Therefore, this enables the constant current characteristic to have a very tight tolerance, which is very prominent in a single-stage converter.
When performing dimming control, the LinkSwitch-PL device detects both the input voltage zero crossing and the conduction angle of the thyristor dimmer. The input voltage zero crossing is detected internally at the drain node. The control circuit processes this data and sets the required feedback voltage, thereby setting the LED load current.
Inrush Current
As shown in Figure 1, the driver presents a high impedance, high capacitance load to the thyristor controller. In addition, there will be input EMI filtering circuits formed by capacitors and inductors. In each half cycle, an inrush current will be generated, causing ringing (as described above).
For trouble-free dimming operation, the driver must be able to limit the oscillations and prevent the thyristor current from falling below the holding current value. Figure 2 shows a complete circuit diagram of a driver with this capability.
Figure 2: Circuit diagram of a 5W, 15V thyristor-dimmable LED driver for the A19 incandescent replacement lamp .
The circuit in Figure 2 provides a single constant current output of 350mA and a 15V LED string voltage. Using a standard AC mains thyristor dimmer, the output current can be reduced by 1% (3mA) without causing instability or flicker in the LED load. The driver is compatible with both low-cost thyristor dimmers and more complex electronic leading and trailing edge dimmers.
The driver's functionality adds input EMI filtering and three TRIAC dimming-specific components: a passive damper, an active damper, and a bleeder.
Input EMI filtering ensures compliance with IEC ring wave and EN55015 conducted EMI regulations. However, the key point is that the LinkSwitch-PL controller integrates a built-in frequency jitter feature. This feature spreads the switching frequency and reduces EMI peaks, making the size of the EMI filtering circuit much smaller than normal requirements. This helps to significantly reduce the inductive load on the thyristor, thereby reducing the possibility of oscillation.
Resistor R20 forms a passive damping circuit. The active damping circuit connects the series resistors (R7 and R8) through the input rectifier during each AC half cycle and bypasses the resistors through the parallel thyristor rectifier (Q3) during the remaining AC cycle. Resistors R3, R4, and C3 determine the delay time before Q3 turns on and then shorts out damping resistors R7 and R8. The passive damping circuit and active damping circuit work together to limit the peak surge current when the thyristor turns on during each half cycle.
Resistors R10, R11 and C6 form a bleeder circuit to ensure that the initial input current can meet the maintenance current requirement of the thyristor, especially when the conduction angle is small. For non-dimming applications, the passive attenuation circuit, active attenuation circuit and bleeder circuit can be omitted.
Isolated LED Driver
The driver in Figure 2 is optimized for low-power, electrically non-isolated integrated LED replacement lamps. PI has introduced the LinkSwitch-PH controller for higher-power LED lighting systems that require electrical isolation. Figure 3 (see our website for details) shows the circuit diagram of an isolated LED driver using LinkSwitch-PH.
Figure 3: Circuit diagram of a 14W thyristor-dimmable high power factor LED driver.
Capable of delivering 0.5A drive current to a nominal 28V LED string voltage over an input voltage range of 90VAC to 265VAC, the circuit features an ultra-wide dimming range, flicker-free operation (even with low-cost AC input TRIAC dimmers), and fast, smooth turn-on.
The topology used is an isolated flyback structure operating in continuous conduction mode. The output current regulation is completely sensed from the primary side, so no secondary feedback components are required. The single-stage internal controller adjusts the duty cycle of the high-voltage power MOSFET to keep the input current sinusoidal AC, ensuring high power factor and low harmonic currents.
The circuit functions similarly to the circuit in Figure 2, with the most notable difference being that this circuit is electrically isolated and does not use a sense resistor in series with the load. Feedback control is provided through the bias winding on the transformer. The feedback control has two functions: powering the LinkSwitch-PH via the bypass (BP) input and providing current feedback via the feedback (FB) input. Another important input provided by the LinkSwitch-PH is the voltage monitor (V). This pin interfaces with the external input voltage peak detector, which is formed by D1, C3, R1, R2, and R3. The impressed current is used to control the shutdown logic for input undervoltage (UV) and overvoltage (OV) and to provide a feed-forward signal to control the output current and remote on/off functions. The circuit integrates a damping circuit and a bleeder circuit to ensure the operation of the thyristor (see Figure 6).
In any LED lighting installation, the performance of the driver determines the lighting experience of the end user, including startup time, dimming, flicker-free operation and consistency between units. The 14W driver is compatible with various dimmers and the widest possible dimming range at both 115VAC and 230VAC. Therefore, the attenuation circuit and the bleeder circuit will play a relatively positive role, but this will reduce the efficiency. Even so, the efficiency of the circuit can still be ≥85% at 115VAC and ≥87% at 230VAC. If the dimming function is not required, the attenuation circuit and the bleeder circuit can be omitted to achieve higher efficiency.
As the potential of the LED lighting market continues to expand, the above design trade-offs highlight a series of philosophical questions. Since the new technology consumes only one-tenth of the power of the old technology, is it really necessary to achieve compatibility with all old thyristor controllers at the expense of efficiency (i.e., increased power consumption)? Can we make a 5W LED lamp work correctly when driven by a 1000W thyristor controller with a minimum load specification of 40W? Yes, it can be done, and perhaps it should be done soon. But we must remember that the ultimate goal of a complete lighting solution is to achieve maximum efficiency and lowest life cycle cost.
Previous article:"Electron overflow" is the root cause of LED light decay
Next article:[Technical Analysis] Non-isolated LED bulbs reduce size and cost
Recommended ReadingLatest update time:2024-11-16 14:34
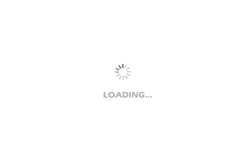
- MathWorks and NXP Collaborate to Launch Model-Based Design Toolbox for Battery Management Systems
- STMicroelectronics' advanced galvanically isolated gate driver STGAP3S provides flexible protection for IGBTs and SiC MOSFETs
- New diaphragm-free solid-state lithium battery technology is launched: the distance between the positive and negative electrodes is less than 0.000001 meters
- [“Source” Observe the Autumn Series] Application and testing of the next generation of semiconductor gallium oxide device photodetectors
- 采用自主设计封装,绝缘电阻显著提高!ROHM开发出更高电压xEV系统的SiC肖特基势垒二极管
- Will GaN replace SiC? PI's disruptive 1700V InnoMux2 is here to demonstrate
- From Isolation to the Third and a Half Generation: Understanding Naxinwei's Gate Driver IC in One Article
- The appeal of 48 V technology: importance, benefits and key factors in system-level applications
- Important breakthrough in recycling of used lithium-ion batteries
- Innolux's intelligent steer-by-wire solution makes cars smarter and safer
- 8051 MCU - Parity Check
- How to efficiently balance the sensitivity of tactile sensing interfaces
- What should I do if the servo motor shakes? What causes the servo motor to shake quickly?
- 【Brushless Motor】Analysis of three-phase BLDC motor and sharing of two popular development boards
- Midea Industrial Technology's subsidiaries Clou Electronics and Hekang New Energy jointly appeared at the Munich Battery Energy Storage Exhibition and Solar Energy Exhibition
- Guoxin Sichen | Application of ferroelectric memory PB85RS2MC in power battery management, with a capacity of 2M
- Analysis of common faults of frequency converter
- In a head-on competition with Qualcomm, what kind of cockpit products has Intel come up with?
- Dalian Rongke's all-vanadium liquid flow battery energy storage equipment industrialization project has entered the sprint stage before production
- Allegro MicroSystems Introduces Advanced Magnetic and Inductive Position Sensing Solutions at Electronica 2024
- Car key in the left hand, liveness detection radar in the right hand, UWB is imperative for cars!
- After a decade of rapid development, domestic CIS has entered the market
- Aegis Dagger Battery + Thor EM-i Super Hybrid, Geely New Energy has thrown out two "king bombs"
- A brief discussion on functional safety - fault, error, and failure
- In the smart car 2.0 cycle, these core industry chains are facing major opportunities!
- The United States and Japan are developing new batteries. CATL faces challenges? How should China's new energy battery industry respond?
- Murata launches high-precision 6-axis inertial sensor for automobiles
- Ford patents pre-charge alarm to help save costs and respond to emergencies
- New real-time microcontroller system from Texas Instruments enables smarter processing in automotive and industrial applications
- 4G RTU supports Ethernet communication and dual RS485 serial port communication functions
- EEWORLD University ----TI Precision Labs - CAN
- 【Qinheng Trial】Program downloaded successfully
- Collection of 20 RC application circuits
- Design of reversing radar based on MSP430
- Atmel Studio has stopped working?
- XMC4800 Review (VI) Making a Simple Web Browser
- [GD32E231 DIY Contest]——04. Build an IoT cloud server based on MQTT communication
- EEWORLD University Hall----Introduction to UCD3138 digital power controller architecture and power peripherals
- 【McQueen Trial】The third post is delayed——Simple wireless control car