With the rise and continuous improvement of the solid-state lighting industry, light-emitting diodes (LEDs) have become an alternative lighting technology and are gradually being used in lighting because of their high efficiency, energy saving, long life, and environmental protection. A key factor that has prompted people to pay attention to LED lighting technology is that it greatly reduces energy consumption and can achieve long-term and reliable operation. There is reason to believe that this new type of solid-state lighting will bring about the third revolution in the field of human lighting.
Of course, when using LED lighting, the first thing to consider is its brightness, cost and life. Since the main reasons that affect the life of LEDs are the frequent current shocks at the moment of startup, various external surge pulses, and current limits during normal operation, this circuit combines these factors, and tries to avoid the impact of large currents on LED lighting fixtures from the circuit design, and stabilizes its operating current within a certain range, solving the current brightness attenuation problem of LED lighting fixtures and effectively extending their service life.
1. Driving power supply
LEDs are all driven by direct current, so a power adapter, i.e., LED driver power supply, is required between the mains and the LED. Its function is to convert the AC mains into direct current suitable for LEDs.
LED driver power supplies can be divided into constant current type and voltage stabilization type according to their driving mode. The output current of the constant current driver circuit is constant, and the output DC voltage varies within a certain range with the size of the load resistance. The smaller the load resistance, the lower the output voltage, and the larger the load resistance, the higher the output voltage. For the voltage stabilization power supply circuit, its output voltage is fixed, but the output current changes with the increase or decrease of the load.
Since LED is a device whose current changes significantly with voltage, when the LED is forward-conducting, a slight change in its forward voltage can cause a huge change in the LED current. For a voltage-stabilized LED driver, when the load changes, the current fluctuates greatly, and the LED will be damaged if it works for a long time under a large current. Experiments show that when the actual current flowing through the LED is 70% of its maximum allowable current, the LED's luminous efficacy is optimal. At the same time, since the voltage temperature coefficient of the PN junction of the light-emitting diode is about -2 mVP℃, when the temperature rises due to poor heat dissipation of the LED, its operating current will also change significantly compared to the initial stage, which is also the main reason for the rapid aging of various LED products on the market. Obviously, ensuring the stability of the LED drive current is particularly important for the anti-aging of the LED. Therefore, a constant current driver is a more ideal LED drive method.
Usually, LEDs are driven by dedicated constant current sources or driver chips. When limited by factors such as volume and cost, the most economical and practical method is to use a capacitor step-down power supply. Using it to drive low-power LEDs has the advantages of not being afraid of load short circuits and simple circuits, and one circuit can drive 1 to 70 low-power LEDs. However, the current impact of this power supply circuit when it is started, especially frequent startup, will cause damage to the LED. Of course, taking appropriate protection can avoid this impact.
The typical circuit of capacitor step-down power supply is shown in Figure 1. C1 is a step-down capacitor (metallized polypropylene capacitor), and R1 provides a discharge circuit for C1. Capacitor C1 provides a constant working current for the entire circuit. Capacitor C2 is an electrolytic capacitor, and its withstand voltage value depends on the number of LEDs connected in series (about 1.5 times or more of its total voltage). Its main function is to suppress the voltage mutation caused by the power-on moment, thereby reducing the impact of voltage shock on the life of the LED. R4 is the leakage resistor of capacitor C2, and its resistance value should be appropriately increased with the increase of the number of LEDs.
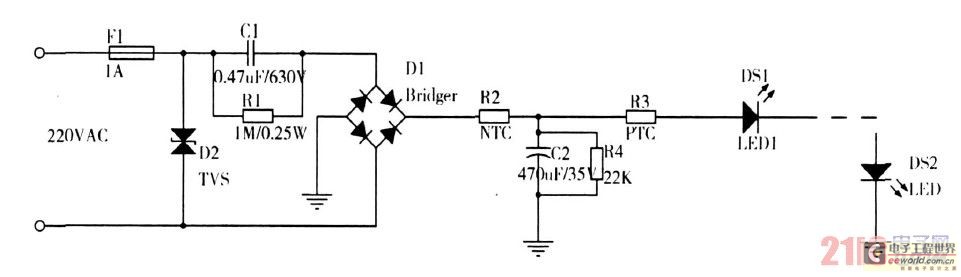
Figure 1 Typical circuit of capacitor step-down power supply
It should be noted that the appropriate capacitor must be selected based on the current size of the load, rather than the voltage and power of the load. Usually, the relationship between the capacitance C of the step-down capacitor C1 and the load current Io can be approximately considered as: C = 14.5 I, where the capacitance unit of C is μF and the unit of Io is A. The current limiting capacitor must be a non-polar capacitor, and the withstand voltage of the capacitor must be above 630 V.
2 Protection circuit
Since the capacitor step-down power supply is a non-isolated power supply, a large current will be generated at the moment of power-on, which is the so-called surge current.
In addition, due to the influence of the external environment such as the induction of lightning strikes, various surge signals will invade from the power grid system, and some surges will cause damage to the LED. However, the LED's ability to resist surge current and reverse voltage is relatively poor, so it is also very important to strengthen protection in this regard, especially when some LED lights are installed outdoors, such as LED street lights. Therefore, the LED driver power supply must have the ability to suppress the intrusion of surges and protect the LED from being damaged. This circuit uses NTC (negative temperature coefficient thermistor) to limit the sudden change of current, and uses PTC (positive temperature coefficient thermistor) to automatically adjust the current size so that it tends to a certain range of variation. At the same time, there is a TVS (transient voltage suppressor) at the power input to avoid voltage overload.
2.1 NTC protection
NTC is the abbreviation of Negative Temperature Coefficient, which means negative temperature coefficient. It generally refers to semiconductor materials or components with large negative temperature coefficient. The so-called NTC thermistor is a negative temperature coefficient thermistor. The simplest and most effective way to limit the inrush current is to connect an NTC thermistor in series at the line input end, such as R2 in Figure 1. Since the NTC thermistor exhibits high impedance during cold start, the inrush current is limited. When the thermal effect of the current causes the temperature of the NTC thermistor to rise and the NTC resistance value drops sharply, the current limiting effect on the system will be smaller. Since the impedance of the NTC thermistor in the hot state is not zero, power loss will occur, of course, this loss is very small.
2.2 PTC protection
PTC (Positive Temperature CoefflCient) refers to the phenomenon or material of thermistor with positive temperature coefficient whose resistance increases sharply at a certain temperature. In order to make the current in the circuit tend to be stable under normal operation, this circuit also uses PTC thermistor, such as R3 in Figure 1. When the current passes through the PTC thermistor, it causes the temperature to rise, that is, the temperature of the heating element rises. When the temperature exceeds the Curie point, the resistance increases, thereby limiting the increase of current. Therefore, the decrease of current causes the temperature of the component to decrease, and the decrease of resistance value causes the circuit current to increase, and the temperature of the component to rise, and this cycle repeats. Therefore, it has the function of keeping the temperature within a specific range.
The PTC element is connected in series in the circuit. Under normal circumstances, it is in a low-resistance state to ensure the normal operation of the circuit. When a short circuit occurs in the circuit or an abnormally large current flows into the circuit, the self-heating of the PTC element increases its impedance and limits the current to a sufficiently small level, thus playing an overcurrent protection role. When the fault that causes the overcurrent is eliminated, the PTC element automatically returns to a low-resistance state.
This avoids maintenance and replacement, as well as the continuous cycle of on and off that may cause circuit damage.
2.3 TVS protection
Transient Voltage Suppressor (TVS) is a highly efficient protection device developed on the basis of Zener diode, which is mainly used for rapid overvoltage protection of circuit components.
When the two poles of the TVS tube are subjected to a reverse transient high-energy impact, it can change the high impedance between the two poles to a very low impedance at a speed of 10 to 12 seconds, absorb high-energy surges, and clamp the voltage between the two poles to a predetermined value, protecting the components in the electronic circuit from damage caused by various surge pulses.
For overvoltage protection, this circuit connects a TVS in parallel to the power input, as shown in D2 in Figure 1. This maintains the voltage within the maximum tolerance range of the TVS. When an overvoltage occurs, the voltage is higher than the TVS breakdown point, allowing current to flow through the TVS to protect the LED lighting fixture.
3 Conclusion
The experiment shows that after the pointer multimeter is connected in series to the circuit, the phenomenon of the pointer suddenly deflecting at a large angle at the moment the circuit is powered on is significantly improved, effectively preventing the impact of surge current on the LED. At the same time, after a period of startup, the current decreases and gradually stabilizes. Using a 1W metal film resistor or a winding resistor instead of NTC can also meet the requirements, and TVS or varistor can be used for overvoltage protection. In terms of circuit board design, it should be noted that the high-voltage input part (that is, the power input end to the rectifier bridge part) should be as far away from the load circuit behind as possible, and if allowed, the distance between the wires of the high-voltage input part should be guaranteed to be more than 1 mm. Based on these considerations, the LED lighting fixture shown in Figure 2 was designed. This lighting module has been working continuously for about 4 years, and the brightness has not been reduced, and it has not been maintained. This circuit is easy to promote and popularize, and can be widely used in public lighting, corridors, warehouses, etc., with great commercial prospects.
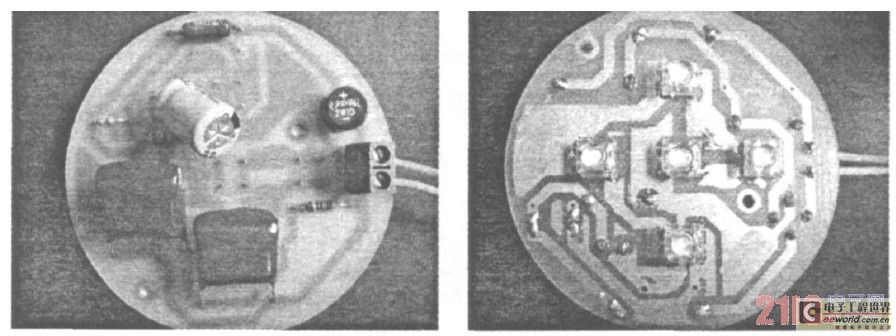
Figure 2 LED lighting fixtures
Previous article:Application of digital power technology in LED lighting
Next article:Low-power LED general lighting applications below 30 W
Recommended ReadingLatest update time:2024-11-17 00:36
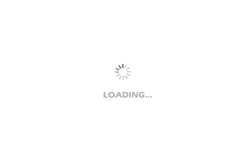
- MathWorks and NXP Collaborate to Launch Model-Based Design Toolbox for Battery Management Systems
- STMicroelectronics' advanced galvanically isolated gate driver STGAP3S provides flexible protection for IGBTs and SiC MOSFETs
- New diaphragm-free solid-state lithium battery technology is launched: the distance between the positive and negative electrodes is less than 0.000001 meters
- [“Source” Observe the Autumn Series] Application and testing of the next generation of semiconductor gallium oxide device photodetectors
- 采用自主设计封装,绝缘电阻显著提高!ROHM开发出更高电压xEV系统的SiC肖特基势垒二极管
- Will GaN replace SiC? PI's disruptive 1700V InnoMux2 is here to demonstrate
- From Isolation to the Third and a Half Generation: Understanding Naxinwei's Gate Driver IC in One Article
- The appeal of 48 V technology: importance, benefits and key factors in system-level applications
- Important breakthrough in recycling of used lithium-ion batteries
- Innolux's intelligent steer-by-wire solution makes cars smarter and safer
- 8051 MCU - Parity Check
- How to efficiently balance the sensitivity of tactile sensing interfaces
- What should I do if the servo motor shakes? What causes the servo motor to shake quickly?
- 【Brushless Motor】Analysis of three-phase BLDC motor and sharing of two popular development boards
- Midea Industrial Technology's subsidiaries Clou Electronics and Hekang New Energy jointly appeared at the Munich Battery Energy Storage Exhibition and Solar Energy Exhibition
- Guoxin Sichen | Application of ferroelectric memory PB85RS2MC in power battery management, with a capacity of 2M
- Analysis of common faults of frequency converter
- In a head-on competition with Qualcomm, what kind of cockpit products has Intel come up with?
- Dalian Rongke's all-vanadium liquid flow battery energy storage equipment industrialization project has entered the sprint stage before production
- Allegro MicroSystems Introduces Advanced Magnetic and Inductive Position Sensing Solutions at Electronica 2024
- Car key in the left hand, liveness detection radar in the right hand, UWB is imperative for cars!
- After a decade of rapid development, domestic CIS has entered the market
- Aegis Dagger Battery + Thor EM-i Super Hybrid, Geely New Energy has thrown out two "king bombs"
- A brief discussion on functional safety - fault, error, and failure
- In the smart car 2.0 cycle, these core industry chains are facing major opportunities!
- The United States and Japan are developing new batteries. CATL faces challenges? How should China's new energy battery industry respond?
- Murata launches high-precision 6-axis inertial sensor for automobiles
- Ford patents pre-charge alarm to help save costs and respond to emergencies
- New real-time microcontroller system from Texas Instruments enables smarter processing in automotive and industrial applications
- What TI DSP Power Knows
- Xilinx FPGA Development Tools
- The universal tool for impedance measurement
- Common data structures in RT-Thread system
- Advice for beginners of DLP4500 light modulation.
- RC parallel circuit bandwidth problem - 3db bandwidth position problem, please help
- When I posted a message just now, as soon as I selected the invitees and clicked the Save button, an error message appeared: Discuz!
- EEWORLD University - In-depth technical training on battery management
- Ask about the selection of bidirectional thyristor
- 2-way ADC0808 measurement digital tube display assembly program