With the rapid development of electronic technology, the types of electronic devices are increasing day by day. Any electronic device cannot do without a reliable power supply, and the requirements for the quality of power supply are getting higher and higher. The switching power supply has significant advantages over the traditional transistor linear power supply in terms of efficiency, weight, volume, etc. It is precisely because of these characteristics of the switching power supply that it has been widely used in emerging electronic devices and has gradually replaced the continuous control linear power supply.
Figure 1 Schematic diagram of the main power circuit
Power main circuit
This power module adopts a half-bridge power inverter circuit. As shown in Figure 1, the three-phase AC power is filtered by the EMI filter, which greatly reduces the electromagnetic interference of the AC power input and prevents the harmonics generated by the switching power supply from crosstalking to the input power supply. Then it passes through the bridge rectifier circuit and the filter circuit to become a DC voltage added between points P and N. A small-capacity, high-voltage-resistant non-inductive capacitor is connected between P and N to play a high-frequency filtering role. The half-bridge power conversion circuit is similar to the full-bridge power conversion circuit, except that the two power switching devices are replaced by two capacitors C1 and C2 with equal capacity. In practical applications, in order to increase the capacity and voltage resistance of the capacitor, C1 and C2 often use a capacitor group composed of multiple equal-value capacitors in parallel. The capacity of C1 and C2 should be as large as possible to reduce the ripple coefficient and low-frequency oscillation of the output voltage. Due to the restrictions on volume and weight, the values of C1 and C2 cannot be infinite. In order to make the ripple of the output voltage meet the specified requirements, there is a calculation formula for the capacitance value, namely:
Where IL is the output load current, VL is the output load voltage, VM is the input AC voltage amplitude, f is the input AC frequency, and VU is the output ripple voltage value.
This is a theoretical calculation formula. The calculated capacitance value that meets the requirements is relatively large. The actual capacitance should be as large as possible. Since the output voltage is small, the capacitance can also be increased during secondary rectification and filtering. In this way, the capacitance value converted to this formula is not small. C1 and C2 realize static voltage division here, making VA=Vin/2.
When VT1 is turned on and VT2 is turned off, the input current direction is the dotted line direction in the figure, charging C2, and C1 is discharged through VT1; when VT2 is turned on and VT1 is turned off, the input current direction is the solid line direction in the figure, charging C1, and C2 is discharged through VT2.
When VT1 is turned on and VT2 is turned off, the voltage across VT2 is the input DC voltage Vin. An RC absorption network is connected in parallel between the collector and emitter of the IGBT to reduce the switching stress of the switch tube and the peak voltage generated by the IGBT shutdown; the parallel diode realizes the function of freewheeling. The secondary rectification adopts a single-phase bridge rectifier circuit, and the subsequent LC filter circuit eliminates high-frequency ripple and reduces the low-frequency oscillation of the output DC voltage. The capacitor in the LC filter circuit is composed of multiple high-voltage and large-capacity capacitors in parallel to improve the reliability of the power supply and make the output DC voltage more stable.
Functional features of PWM integrated chip SG3525
SG3525 is a fully functional, highly versatile monolithic integrated PWM chip. It uses a constant frequency pulse width modulation control scheme and is suitable for the control of various switching power supplies and choppers. Its main functions include reference voltage generation circuit, oscillator, error amplifier, PWM comparator, undervoltage lockout circuit, soft start control circuit, and push-pull output form. The basic peripheral circuit wiring diagram of SG3525 is shown in Figure 2. Compared with other chips of the same type, this chip has many outstanding features.
Figure 2 Basic peripheral wiring diagram of SG3525
(1) The frequency is adjustable. Generally, the output frequency of the PWM wave is adjusted by changing the values of CT and RT (see Figure 2). The frequency calculation formula is:
(2) The dead time is adjustable. By adjusting RD, the size of the dead time can be changed to prevent the upper and lower arms of the inverter bridge from being directly connected.
(3) It has a PWM pulse signal blocking function. When the voltage at pin 10 is higher than 2.5V, the pulse output can be blocked in time to prevent damage to the circuit when overvoltage, overcurrent, or overheating occurs.
(4) The operating frequency of the oscillator in the chip is 100Hz~400kHz. Pin 3 is set as the synchronization terminal to facilitate the use of multiple SG3525s.
(5) It has a soft start circuit. The inverting input of the comparator, i.e., pin 8 of the soft start control chip, can be connected to an external soft start capacitor C. The reference voltage V ref inside the capacitor is powered by a constant current source. The time it takes to reach 2.5V is t = (2.5V/50uA) C, and the duty cycle changes from small to large (50%).
(6) The built-in PWM (Pulse Width Modulation) latch latches the set signal sent by the comparator and eliminates the noise, ringing and all the beating and oscillation signals on the error amplifier. It can only be reset in the next clock cycle, and the system reliability is high.
Application circuit and working principle of SG3525
The high-power DC switching power supply control circuit built using SG3525 is shown in Figure 3. The voltage regulation and current limiting modules are mainly introduced below.
Figure 3 SG3525 peripheral control circuit
As shown in Figure 3, the voltage feedback circuit achieves isolation between the strong current output part and the weak current control part through the photoelectric coupler. The photoelectric coupler uses HP4504. When the input current is between 0 and 4 mA, the current transfer ratio between input and output is linear. When designing, select a suitable current limiting resistor to control the input current to change between 0 and 3 mA. When the output voltage Uout increases, the emitter current Ie at the output of the photoelectric coupler increases linearly, which increases the emitter voltage Ve, and the V1 input to pin 1 after filtering and voltage stabilization by C2, C3, R4, and R5 also increases. When V1 increases, the voltage at pin 9 decreases after error amplification, the pulse width of the comparator output becomes wider, and the PWM pulse width of pins 11 and 14 becomes narrower, thereby reducing the output voltage Uout; conversely, when Uout decreases, the voltage at pin 1 decreases, the voltage at pin 9 increases, and the PWM pulse width of pins 11 and 14 becomes wider. In short, the increase and decrease of the voltage V1 at pin 1 reflects the rise and fall of the output voltage Uout, which is ultimately reflected in the width changes of the PWM pulses output at pins 11 and 14, so as to achieve automatic voltage regulation of the circuit.
By utilizing the linear segment of the optocoupler's current transfer ratio, linear changes in input and output can be achieved. When used in feedback circuits, it not only reduces costs but also isolates the input from the output. At the same time, its voltage regulation effect is comparable to that of a voltage sensor. In practical applications, it is a desirable method.
The current sampling signal Vi obtained by the output current sensor is compared with the given current limiting reference voltage Urefi. When the external load changes and the output current Uout changes, Vi will also change accordingly. When Iout increases and Vi is greater than Vrefi, the output terminal Vb of the operational amplifier L1A is low. At this time, the output terminal V2 of L2A will be directly pulled down to a low level, pin 2 is equivalent to grounding, and there is no pulse output at the output terminals 11 and 14. The switching power supply has a "hiccup" phenomenon, which plays a current limiting role. At the same time, the output current Iout decreases, causing V2 to be pulled up again, pins 11 and 14 resume pulse output, and the switching power supply works normally, thereby achieving a dynamic balance process of the output current.
Figure 4 SEMIKRON SKYPER32PRO driver module
IGBT drive circuit
The triggering and shutting down of IGBT requires the application of forward and reverse voltages between its gate and emitter, and a certain amount of dynamic drive power is required to ensure the timely triggering and shutting down of IGBT.
The IGBT driver of this power supply adopts Semikron SKYPER32PRO driver module. The control core is a half-bridge driver module that integrates drive, internal isolation and electrical protection. Compared with similar products, SKYPER32PRO has many features.
(1) A pulse transformer with bidirectional transmission function is used to transmit drive signals and status signals between the primary side and the secondary side, and transfer energy to the secondary side.
(2) The component is designed to be plug-and-play, easy to use, and has undergone comprehensive electrical and temperature tests.
(3) Use a single power supply mode to power both sides of the driving bridge arm at the same time.
(4) It has a short pulse suppression function, which can automatically repair the dual-channel PWM wave sent by SG3525 to make the waveform more stable.
(5) It has VCE monitoring, undervoltage monitoring, undervoltage reset and dead zone interlocking functions.
Prototype development
Main technical indicators:
Input voltage: three-phase AC380V±5%
Output voltage: DC220V±2%
Output current: 50A
Rated power: 11kW
The output waveform of the test prototype at rated load is shown in Figure 5 (a). From the actual reading in Figure 5 (a), it can be seen that the response time of the output voltage rising from 0V to 220V is about 1s, and the power supply system has a fast response speed. At the same time, from the partial enlarged diagram of the voltage waveform in Figure 5 (b), it can be seen that when the output voltage is 220V, the voltage fluctuation is about 2V, and its maximum voltage fluctuation is less than 1%.
Figure 5
in conclusion
Using the powerful functions of SG3525 and SKYPER32PRO, an 11kW, 220V DC switching power supply is designed. This power supply has a simple design, convenient debugging, fewer components, small size and low cost. When the load changes in the full range, this power supply can maintain good output performance. The test data shows that the indicators meet the design requirements, and the output ripple factor is controlled within the range of less than 1%.
Previous article:Double the laser driver protection with a 1V supply
Next article:Resonant coordinates method for analyzing switched-mode power supplies
Recommended ReadingLatest update time:2024-11-16 15:56
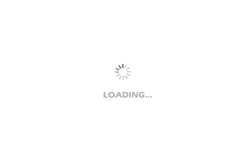
- Popular Resources
- Popular amplifiers
- MathWorks and NXP Collaborate to Launch Model-Based Design Toolbox for Battery Management Systems
- STMicroelectronics' advanced galvanically isolated gate driver STGAP3S provides flexible protection for IGBTs and SiC MOSFETs
- New diaphragm-free solid-state lithium battery technology is launched: the distance between the positive and negative electrodes is less than 0.000001 meters
- [“Source” Observe the Autumn Series] Application and testing of the next generation of semiconductor gallium oxide device photodetectors
- 采用自主设计封装,绝缘电阻显著提高!ROHM开发出更高电压xEV系统的SiC肖特基势垒二极管
- Will GaN replace SiC? PI's disruptive 1700V InnoMux2 is here to demonstrate
- From Isolation to the Third and a Half Generation: Understanding Naxinwei's Gate Driver IC in One Article
- The appeal of 48 V technology: importance, benefits and key factors in system-level applications
- Important breakthrough in recycling of used lithium-ion batteries
- Innolux's intelligent steer-by-wire solution makes cars smarter and safer
- 8051 MCU - Parity Check
- How to efficiently balance the sensitivity of tactile sensing interfaces
- What should I do if the servo motor shakes? What causes the servo motor to shake quickly?
- 【Brushless Motor】Analysis of three-phase BLDC motor and sharing of two popular development boards
- Midea Industrial Technology's subsidiaries Clou Electronics and Hekang New Energy jointly appeared at the Munich Battery Energy Storage Exhibition and Solar Energy Exhibition
- Guoxin Sichen | Application of ferroelectric memory PB85RS2MC in power battery management, with a capacity of 2M
- Analysis of common faults of frequency converter
- In a head-on competition with Qualcomm, what kind of cockpit products has Intel come up with?
- Dalian Rongke's all-vanadium liquid flow battery energy storage equipment industrialization project has entered the sprint stage before production
- Allegro MicroSystems Introduces Advanced Magnetic and Inductive Position Sensing Solutions at Electronica 2024
- Car key in the left hand, liveness detection radar in the right hand, UWB is imperative for cars!
- After a decade of rapid development, domestic CIS has entered the market
- Aegis Dagger Battery + Thor EM-i Super Hybrid, Geely New Energy has thrown out two "king bombs"
- A brief discussion on functional safety - fault, error, and failure
- In the smart car 2.0 cycle, these core industry chains are facing major opportunities!
- The United States and Japan are developing new batteries. CATL faces challenges? How should China's new energy battery industry respond?
- Murata launches high-precision 6-axis inertial sensor for automobiles
- Ford patents pre-charge alarm to help save costs and respond to emergencies
- New real-time microcontroller system from Texas Instruments enables smarter processing in automotive and industrial applications
- Problems with ADS1220
- Why do smart water meters use disposable 17450 (or other models) disposable lithium batteries? Why not use rechargeable batteries?
- 【Development and application based on NUCLEO-F746ZG motor】15. Mathematical model - voltage equation and electromagnetic torque equation
- Playing with Zynq Serial 42——[ex61] Image Laplacian Sharpening Processing of OV5640 Camera
- Snake moving in a twisting motion
- Qorvo's leading RF solutions
- Shanghai Hangxin ACM32F070 development board + serial port
- I'm a newbie and would like to ask for the code of an electronic combination lock!
- Purgatory Legend-Generate War.pdf
- In FPGA design, timing is everything