The LED industry's call for unified standards for LED lighting has been a topic of discussion in the industry for a long time. Although various regions have been formulating and testing their own local standards, the confusion of standards and the lack of an authoritative testing platform have caused the entire industry to become a mess.
The government is in a dilemma, businesses are shaking their heads and sighing, and the people are in the dark, not knowing who is right or wrong, who is good or bad.
Due to the lack of unified standards and testing methods, the wide variety of LED application products on the market currently have different performances and uneven quality, which has brought severe challenges to the development of the entire industry.
From the perspective of current LED product structure and technology development, the quality evaluation criteria of lighting LED products mainly consider parameters such as optical performance, electrical performance, thermal performance, radiation safety and lifespan, among which the optical performance of LED mainly involves luminous flux, radiant flux, luminous efficiency, chromaticity coordinates, correlated color temperature, color rendering index, etc. At present, photoelectric detection, photometric detection, light energy detection, attenuation test and collision resistance test are conventional detection items for LED lamps.
The sampling results are not optimistic
Recently, the Guangdong Quality Supervision Bureau released the results of the provincial special supervision and random inspection of self-ballasted LED lamps in Guangdong Province. The inspection results show that among the 23 batches of self-ballasted LEDs inspected, 17 batches failed the inspection, with a failure rate of 73.9%. It is understood that the unqualified items involved protection against accidental contact with live parts, insulation resistance and dielectric strength after moisture treatment, mechanical strength, fault status, color tolerance, general color rendering index, interference voltage, lamp power, heat resistance, interchangeability, power factor, initial luminous efficacy/luminous flux, fire prevention and combustion prevention, etc.
There have been many reports of LED lighting products failing to meet quality standards. Why do LEDs frequently have quality problems? The key is the lack of LED lighting standards and the incomplete construction of a testing system. From power supply to finished products, LED lighting does not yet have a national or industry standard system, let alone mandatory testing and certification requirements.
"Although routine performance tests are conducted on lamps before they leave the factory, not all companies strictly follow the regulations. This is due to the fact that companies do not have complete testing equipment and the consideration of reducing costs." The relevant person in charge of Dongguan Qinshang Optoelectronics Co., Ltd. pointed out that currently large companies have nationally recognized laboratories for lamp testing, and the testing equipment is relatively complete. However, small and medium-sized enterprises often only need to test for a few hours to pass the test, and they are also relatively lacking in testing equipment. This has caused a large number of unqualified quality problems when some government agencies conducted random inspections on LED lamps, which has had a great negative impact on the market popularity of LED products.
Usually in the test results of LED lamps, problems such as luminous flux and CRI not meeting the standards, color temperature and power deviation are common. Li Sheng, Operation Director of Lice Testing, pointed out that the reasons for failing quality inspection are mainly concentrated in the following four aspects: 1. The electrical insulation requirements cannot be met, which is mainly manifested in the insufficient electrical clearance and creepage distance inside the product, and the conductors that can be touched by the human body are not safe isolation low voltage. In particular, some small-volume lamps often ignore the requirements of electrical insulation distance due to their compact structure. 2. The driver used does not meet the corresponding LED driver safety requirements, or a simple step-down circuit is used to drive the LED. 3. The electromagnetic interference voltage of the product exceeds the standard. Most LEDs use cheap driving circuits, and no electromagnetic interference suppression measures are taken in the circuit, resulting in excessive conduction voltage and radiation. 4. The light color performance requirements of the lamp cannot be met. The light-emitting principle of LED lamps is quite different from that of traditional light sources. Designers only care about whether the lamps emit light, and ignore the requirements of light and color quality, resulting in large deviations in color temperature and low color rendering index.
"The color rendering index cannot be lower than 80 according to regulations, otherwise the initial luminous efficacy cannot meet the energy efficiency requirements and the energy-saving effect cannot be achieved." An insider in the testing industry said that some current products unilaterally pursue high luminous efficacy and ignore lumen maintenance life, resulting in the actual service life of the lamps being low and causing the products to fail to meet energy-saving indicators.
There are errors in the test results
During the lamp testing process, the company often encounters the problem of inconsistent parameter results for the same lamp twice. In this regard, Zhu Jungao, technical support manager of Zhejiang University Sanse Instrument Co., Ltd., said that the reasons for the above errors are mainly in the following three aspects: First, the system error, which is within the allowable range. Each detection system may be inconsistent and have a certain error. Traditional lamps are qualified if the error is within 1.5%, but the standards for LED lamps have not yet been standardized, and the industry's allowable error range for LED lamps is also vague, generally between 3% and 5%.
The second is the error of the environment. The environment in which the lamp is located and the pollution on the surface will have a great impact on the test results. The error level can reach 7%-8%, especially for some products whose light-emitting surface also serves as the secondary optical lens surface. Since these products have concave-convex structures, they are easy to harbor dirt and are difficult to clean, which seriously affects the luminous flux and further affects the light distribution.
The third is the error of equipment and standards. The equipment needed for conventional lamp testing is mainly integrating spheres, goniophotometers and optical radiation detection equipment, which are used to measure the luminous flux, photometric performance and photobiological safety of lamps. Among them, optical radiation detection is for ultraviolet content detection for export to the European Union and blue light and infrared energy detection required by the US Energy Star. Due to the lack of national standards and testing specifications, the test methods, testing equipment and testing standards used by testing centers in various places are different, resulting in different test results for the same product of the company when tested by different testing agencies.
Specifically, when it comes to testing the luminous flux with an integrating sphere, although the method is relatively simple, only a light intensity meter or spectrometer can be used with the integrating sphere to complete the test, and no other parameters need to be measured. However, Li Sheng emphasized that since the internal screen, seams, openings on the sphere wall, and spraying effects of the integrating sphere will affect the test accuracy of the integrating sphere, high technical requirements are also placed on the integrating sphere manufacturers.
"The integrating sphere is a set of precision measuring equipment. You need to buy a brand of a big manufacturer with quality assurance. Otherwise, the integrating sphere may look the same, but the measurement result will deviate greatly from the true value, and the stability is poor," said Li Sheng. At the same time, the integrating sphere test also has certain requirements for the environment, usually requiring the ambient temperature to be 25±1℃. There are no strict regulations on the size of the integrating sphere, which is only related to the size of the lamp being tested. Generally speaking, the total surface area of the product being tested must be less than 2% of the total area of the inner wall of the sphere, and the longest physical dimension of the linear product must be less than 2/3 of the diameter of the sphere. For example, for LED lamps, the longest dimension that can be tested by an integrating sphere does not exceed 2/3 of the diameter of the sphere. These are all issues that manufacturers need to pay attention to when conducting tests.
Previous article:LED will enter the mature stage of the market in 2016
Next article:Handheld devices and LED lighting drive the LED industry in 2013
Recommended ReadingLatest update time:2024-11-16 16:55
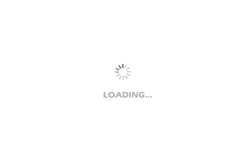
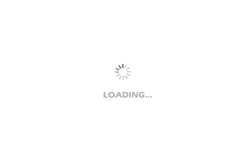
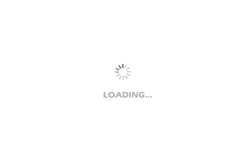
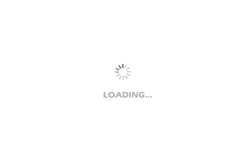
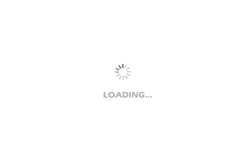
- Popular Resources
- Popular amplifiers
- MathWorks and NXP Collaborate to Launch Model-Based Design Toolbox for Battery Management Systems
- STMicroelectronics' advanced galvanically isolated gate driver STGAP3S provides flexible protection for IGBTs and SiC MOSFETs
- New diaphragm-free solid-state lithium battery technology is launched: the distance between the positive and negative electrodes is less than 0.000001 meters
- [“Source” Observe the Autumn Series] Application and testing of the next generation of semiconductor gallium oxide device photodetectors
- 采用自主设计封装,绝缘电阻显著提高!ROHM开发出更高电压xEV系统的SiC肖特基势垒二极管
- Will GaN replace SiC? PI's disruptive 1700V InnoMux2 is here to demonstrate
- From Isolation to the Third and a Half Generation: Understanding Naxinwei's Gate Driver IC in One Article
- The appeal of 48 V technology: importance, benefits and key factors in system-level applications
- Important breakthrough in recycling of used lithium-ion batteries
- Innolux's intelligent steer-by-wire solution makes cars smarter and safer
- 8051 MCU - Parity Check
- How to efficiently balance the sensitivity of tactile sensing interfaces
- What should I do if the servo motor shakes? What causes the servo motor to shake quickly?
- 【Brushless Motor】Analysis of three-phase BLDC motor and sharing of two popular development boards
- Midea Industrial Technology's subsidiaries Clou Electronics and Hekang New Energy jointly appeared at the Munich Battery Energy Storage Exhibition and Solar Energy Exhibition
- Guoxin Sichen | Application of ferroelectric memory PB85RS2MC in power battery management, with a capacity of 2M
- Analysis of common faults of frequency converter
- In a head-on competition with Qualcomm, what kind of cockpit products has Intel come up with?
- Dalian Rongke's all-vanadium liquid flow battery energy storage equipment industrialization project has entered the sprint stage before production
- Allegro MicroSystems Introduces Advanced Magnetic and Inductive Position Sensing Solutions at Electronica 2024
- Car key in the left hand, liveness detection radar in the right hand, UWB is imperative for cars!
- After a decade of rapid development, domestic CIS has entered the market
- Aegis Dagger Battery + Thor EM-i Super Hybrid, Geely New Energy has thrown out two "king bombs"
- A brief discussion on functional safety - fault, error, and failure
- In the smart car 2.0 cycle, these core industry chains are facing major opportunities!
- The United States and Japan are developing new batteries. CATL faces challenges? How should China's new energy battery industry respond?
- Murata launches high-precision 6-axis inertial sensor for automobiles
- Ford patents pre-charge alarm to help save costs and respond to emergencies
- New real-time microcontroller system from Texas Instruments enables smarter processing in automotive and industrial applications
- Is there any teacher who can teach me how to learn microcontrollers?
- 【AT-START-F425 Review】Thermohygrometer (Hardware I2C) AHT10
- Challenges and future development trends of power module design
- Why has the shared power bank become a “disliked bag”?
- About DSP data calibration
- How to consider and design ESD of RF modules?
- 【NUCLEO-L552ZE Review】+ Bluetooth communication experiment (2)
- 【XMC4800 Relax EtherCAT Kit Review】+ Webserver based on XMC4800
- Help with an electrometer data acquisition circuit
- Adafruit Circuit Playground Express Schematic